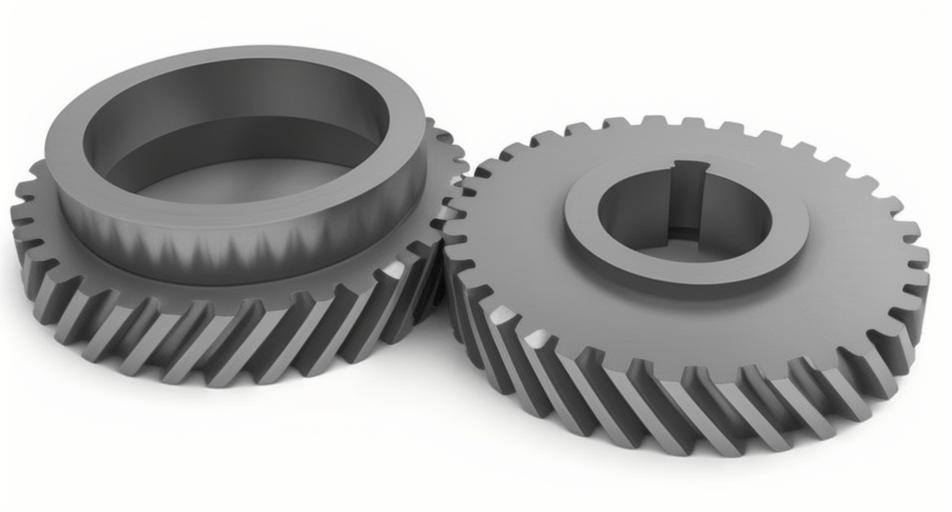
Helical gear is widely used in various industrial applications due to their ability to transmit power efficiently and smoothly. Recent advancements in helical gear design have focused on enhancing performance, particularly in high-load applications. These advancements have been driven by the need for higher durability, reduced noise, and improved efficiency. This article explores the latest developments in helical gear design, materials, and manufacturing processes that contribute to their enhanced performance in demanding conditions.
Key Advancements in Helical Gear Design
- Optimized Gear Geometry:
- Tooth Profile Optimization: Advanced computational tools and software allow for precise modeling of the tooth profile, resulting in reduced stress concentrations and improved load distribution.
- Helix Angle Adjustment: Adjusting the helix angle can optimize the balance between load capacity and smoothness of operation. Higher helix angles typically offer better load distribution but may increase axial thrust.
- Asymmetric Tooth Design: Asymmetric tooth profiles are designed to handle higher loads in one direction, making them suitable for applications with unidirectional loading.
- Material Innovations:
- High-Strength Alloys: The use of high-strength steel alloys and other advanced materials can significantly enhance the load-bearing capacity of helical gear.
- Composite Materials: Composite materials offer a combination of high strength and low weight, which can improve performance and reduce energy consumption.
- Surface Treatments and Coatings: Advanced surface treatments, such as nitriding and carburizing, as well as coatings like DLC (Diamond-Like Carbon), can enhance wear resistance and reduce friction.
- Manufacturing Technologies:
- Additive Manufacturing: 3D printing technologies enable the production of complex gear geometries that are difficult to achieve with traditional manufacturing methods.
- Precision Machining: Advances in CNC machining and grinding technologies allow for higher precision in helical gear manufacturing, leading to better performance and longer life.
- Automated Quality Control: Integration of automated inspection systems ensures high-quality standards in helical gear production, reducing the risk of defects.
Benefits of Advanced Helical Gear Design
- Increased Load Capacity: Optimized gear geometry and advanced materials result in higher load-bearing capacity, making helical gears suitable for heavy-duty applications.
- Enhanced Durability: Improved materials and surface treatments extend the lifespan of helical gear, reducing maintenance costs and downtime.
- Reduced Noise and Vibration: Precision manufacturing and optimized tooth profiles contribute to quieter and smoother operation, which is critical in many industrial settings.
- Improved Efficiency: Better load distribution and reduced friction lead to higher efficiency, which can translate to energy savings and lower operational costs.
Case Study: High-Load Industrial Application
Application: Heavy-duty conveyor system in a mining operation.
Challenges: The conveyor system operates under extreme loads and harsh environmental conditions, requiring gears with high durability and load capacity.
Solution:
- Gear Design: Utilized helical gear with optimized tooth profiles and a higher helix angle to distribute loads more evenly.
- Material Selection: Implemented high-strength steel alloys with nitriding surface treatment to enhance wear resistance.
- Manufacturing Process: Employed precision CNC machining and automated quality control to ensure high accuracy and consistency in helical gear production.
Results:
- Load Capacity: Increased by 20% compared to traditional gear designs.
- Durability: Lifespan of helical gear extended by 30%, reducing maintenance frequency and costs.
- Noise Reduction: Noise levels reduced by 15%, improving the working environment.
Table: Comparison of Traditional and Advanced Helical Gear
Feature | Traditional Helical Gear | Advanced Helical Gear |
---|---|---|
Material | Standard steel alloys | High-strength alloys |
Surface Treatment | Basic hardening | Nitriding, DLC coating |
Manufacturing Precision | Standard CNC machining | Precision CNC machining |
Load Capacity | Moderate | High |
Durability | Moderate | High |
Noise and Vibration | Moderate | Low |
Efficiency | Standard | High |
List: Key Considerations for Implementing Advanced Helical Gear
- Application Requirements: Assess the specific load and environmental conditions of the application to select the appropriate helical gear design and materials.
- Cost-Benefit Analysis: Consider the initial investment in advanced gears versus the long-term benefits of improved performance and reduced maintenance.
- Supplier Capabilities: Choose a supplier with expertise in advanced gear manufacturing and a track record of delivering high-quality products.
- Maintenance Practices: Implement regular maintenance and inspection routines to ensure the longevity and optimal performance of helical gear.
Conclusion
The advancements in helical gear design have significantly enhanced their performance in high-load applications. Through optimized geometry, innovative materials, and advanced manufacturing techniques, modern helical gear offer increased load capacity, enhanced durability, reduced noise, and improved efficiency. These improvements make them an ideal choice for demanding industrial applications, leading to cost savings and improved operational reliability.
By staying abreast of these advancements and carefully considering the specific needs of their applications, industries can leverage the benefits of advanced helical gear technology to achieve superior performance and longevity in their machinery and equipment.