1. Introduction
1.1 Significance of Cylindrical Spur Gears
Cylindrical spur gears are fundamental transmission components widely utilized in aerospace, aviation, automotive, and mechanical fields. The level of gear processing technology serves as a crucial criterion for evaluating a nation’s mechanical manufacturing capabilities. In aerospace applications, high-quality gears are essential for ensuring the reliable operation of various systems, such as aircraft engines and landing gear mechanisms.
1.2 Traditional Manufacturing Methods and Their Limitations
Conventionally, cylindrical spur gears are predominantly fabricated through cutting processes. Despite the maturity and stability of this technology, it suffers from several drawbacks when compared to plastic forming methods. The production efficiency of cutting is relatively low, resulting in longer manufacturing cycles. Moreover, the material utilization rate is not high, leading to significant material waste. This not only increases production costs but also has a negative impact on environmental sustainability, which is contrary to the principles of green manufacturing. Additionally, the cutting process disrupts the continuous fiber structure on the gear tooth surface, thereby deteriorating the mechanical properties of the gears and shortening their service life. In aerospace applications, where reliability and durability are of utmost importance, these limitations become even more critical.
1.3 Advantages of Gear Precision Forging
Gear precision forging, as a green plastic forming manufacturing technique with minimal or no cutting, offers several notable advantages. The continuous distribution of metal fibers along the tooth surface enhances the mechanical properties of the gears, making them more capable of withstanding heavy loads and high stresses. This results in improved gear performance, including higher strength, better wear resistance, and enhanced fatigue life. By reducing material waste and minimizing the need for subsequent machining operations, precision forging also contributes to cost savings and increased production efficiency. In the aerospace industry, where weight reduction and performance optimization are key considerations, gear precision forging presents a promising solution for manufacturing high-quality gears.
1.4 Overview of Orbital Forging Technology
Orbital forging is a local plastic forming process that has gained significant attention in recent years. It offers distinct advantages over traditional forging methods, particularly in terms of reduced forming forces. When compared to conventional forging equipment, the forming force required in the orbital forging process is only about 10% to 20% of that needed for traditional methods. This not only lowers the energy consumption during the manufacturing process but also reduces the load on the equipment, thereby extending its service life. Additionally, orbital forging exhibits lower impact vibrations and noise levels, creating a more favorable working environment. The fine-grained microstructure obtained through orbital forging further contributes to improved mechanical properties of the formed parts, making it an attractive option for gear manufacturing.
1.5 Research Status of Orbital Forging for Gears
Extensive research has been conducted on the orbital forging process, with scholars focusing on various aspects such as process parameters, metal flow behavior, and microstructure evolution. For example, HUA L et al. established three-dimensional finite element models to investigate the influence of key parameters on metal flow, workpiece deformation uniformity, and force-energy parameters in cold orbital forging. Their studies have provided valuable insights into the deformation mechanism of workpieces during the orbital forging process. In the case of bevel gears, significant progress has been made in both research and industrial applications. ZHUANG W H et al. proposed a novel finite element analysis strategy for predicting tooth shape changes in hot forging of straight bevel gears based on the transfer relationships of stress, strain, and temperature. DENG X B et al. developed a three-dimensional rigid-plastic finite element model for cold orbital forging of 20CrMnTi straight bevel gears using the DEFORM-3D platform. HAN X H et al. studied the evolution laws of microstructure and texture during the cold orbital forging process of 20CrMnTi straight bevel gears. However, despite these achievements, research on the hot orbital forging process for cylindrical spur gears remains relatively limited.
1.6 Objectives and Significance of This Study
The primary objective of this study is to investigate the metal deformation behavior and tooth filling characteristics during the hot orbital forging process of aerospace cylindrical spur gears. By employing the DEFORM-3D software, a three-dimensional rigid-plastic finite element model of the cylindrical spur gear hot orbital forging process will be developed. Through simulation and experimental analysis, a comprehensive understanding of the forming laws and mechanisms will be achieved. The results of this study will provide theoretical guidance and practical support for the development and optimization of the hot orbital forging process for cylindrical spur gears, contributing to the advancement of gear manufacturing technology in the aerospace industry.
2. Finite Element Model Establishment
2.1 Gear Three-Dimensional Model Construction
The research focuses on a specific aerospace cylindrical spur gear. The geometric parameters of the gear, as presented in Table 1, are used to create a detailed three-dimensional model. These parameters include the number of teeth, module, pressure angle, addendum coefficient, clearance coefficient, addendum modification coefficient, and tooth width. The three-dimensional model, as shown in Figure 1, provides a visual representation of the gear’s geometry and serves as the foundation for subsequent analysis.
Parameters | Value |
---|---|
Number of teeth | 16 |
Module/mm | 4.5 |
Pressure angle/(°) | 20 |
Addendum coefficient | 1 |
Clearance coefficient | 0.25 |
Addendum modification coefficient | 0.1917 |
Tooth width/mm | 11 |
2.2 Blank Design
Considering the structural characteristics of the cylindrical spur gear with convex platforms at both ends, the blank is designed in a cylindrical shape. The diameter of the blank is slightly smaller than that of the gear convex platform. Based on the principle of equal volume, the shape and dimensions of the blank are determined.
2.3 Orbital Die and Gear Cavity Design
The working principle of the cylindrical spur gear orbital forging process. The orbital die rotates around the machine spindle at a certain angle (orbital angle γ) while also rotating around its own axis. Simultaneously, the gear cavity moves upward at a specific feed rate. Under the coordinated action of the orbital die’s movement and the gear cavity’s feed, the blank undergoes plastic deformation and fills the die cavity.
2.4 Finite Element Model Setup
The.stl format files of the orbital die, gear cavity, and blank are imported into the preprocessor of DEFORM-3D for positioning and assembly. To accurately capture the material flow behavior in the tooth region, the mesh of the blank is refined in the tooth area. A mesh size of 100,000 elements with a refinement ratio of 0.01 is used. In the simulation, the orbital die and gear cavity are considered rigid bodies due to their minimal elastic deformation, while the blank is modeled as a plastic body. The material of the blank is selected as 20CrMnTi. Shear friction models with a friction coefficient of 0.25 are defined between the orbital die and blank, and between the gear cavity and blank. The simulation parameters, including feed rate, rotational speed, orbital angle, feed time, finishing time, blank temperature, die temperature, and interfacial thermal conductivity, are set as shown in Table 2. The resulting finite element model, enables the simulation of the hot orbital forging process.
Parameters | Value |
---|---|
Feed rate of tooth cavity/(mm·s) | 11.5 |
Rotational speed of orbital die/(r·s) | 4 |
Orbital angle/(°) | 2 |
Feed time/s | 2 |
Finishing time/s | 0.5 |
Blank temperature/°C | 1000 |
Die temperature/°C | 300 |
Interfacial thermal conductivity/(N·s’·mm’.°C) | 11 |
3. Forming Law Analysis
3.1 Gear Forming Process
The gear forming process during hot orbital forging is analyzed by observing the shape changes at different times. As shown in Figure 6, in the initial stage of forming (Figure 6a and 6b), the upper surface of the blank comes into contact with the orbital die first, and the material in the contact area begins to deform, forming the convex platforms. As the deformation progresses, the convex platforms at both ends are completed, and the central part of the blank undergoes upsetting deformation with a decrease in height and an increase in diameter. The diameter of the upper end of the blank is larger than that of the lower end, resulting in an overall inverted mushroom shape. In the middle stage of forming (Figure 6c and 6d), due to the local contact between the orbital die and the upper surface of the blank, the friction force is small, and the material at the upper end of the tooth profile flows faster, leading to the formation of the upper tooth profile first. The metal fills the tooth root before filling the tooth tip. In the later stage of forming and the finishing stage (Figure 6e and 6f), the plastic deformation gradually penetrates the entire tooth profile from top to bottom, and the tooth profile is gradually filled and formed, with the formation of petal-shaped flash.
The shape change of the gear during a single cycle of the orbital die’s rotation (0.25s) is shown in Figure 7. It can be observed that the deformation amount of the upper tooth profile of the gear gradually increases within one cycle.
The filling and forming process of a single tooth during the hot orbital forging of the cylindrical spur gear is illustrated in Figure 8. The left figure shows the axial cross-section, and the right figure shows the cross-section perpendicular to the tooth width. It can be seen that with the periodic movement of the orbital die and the feed of the gear cavity, the material of the blank fills the tooth profile along the axial direction, and the filling speed at the upper end of the tooth profile is faster than that at the lower end. Additionally, the material fills the tooth root first and then flows to the tooth tip until the tooth profile is fully filled. During the orbital forging process, the flash gradually becomes thinner and larger in diameter to ensure the complete filling of the tooth profile.
3.2 Metal Flow Velocity Field
In the hot orbital forging process, the deformation zone of the workpiece can be divided into an active deformation zone and a passive deformation zone, as shown in Figure 10. The area where the tooth profile surface directly contacts the orbital die is the active deformation zone, while the area where the tooth profile surface does not directly contact the orbital die is the passive deformation zone.
The distribution of the metal flow velocity field during the hot orbital forging of the cylindrical spur gear is shown in Figure 11. It can be seen that the flow velocity in the active deformation zone is much larger than that in the passive deformation zone. This is because under the combined action of the orbital die’s continuous swinging and the gear cavity’s continuous feed, the active deformation zone is subjected to local loads, resulting in a large degree of plastic deformation and intense metal flow. In contrast, the metal flow in the passive deformation zone is slower. Therefore, in the early stage of orbital forging (Figure 11a and 11b), the metal flow direction of the blank is mainly axial, and the metal in the active deformation zone flows radially outward at a relatively large velocity with the swinging direction of the orbital die to fill the die cavity. In the middle stage of orbital forging (Figure 11c and 11d), after the convex platforms are filled, the metal in the central part of the blank fills the gear cavity at different velocities. The tooth root is filled at a relatively small velocity and then hardly flows, while the tooth tip flows into the cavity at a relatively large velocity, with a faster flow velocity at the upper end. In the later stage of orbital forging (Figure 11e), the tooth profile of the blank is gradually filled, the height decreases slowly, the diameter increases slowly, and the flash is formed at a relatively large velocity. In the finishing stage (Figure 11f), part of the metal in the active deformation zone still fills the tooth profile axially downward at a relatively large velocity.
The distribution of the velocity field within a single cycle in the later stage of the cylindrical spur gear orbital forging is shown in Figure 12. It can be observed that the direction of the velocity field also changes periodically with the orbital forging direction, and the maximum metal flow velocity is located in the middle of the active deformation zone and decreases along both sides.
3.3 Equivalent Stress Field
The distribution characteristics of the equivalent stress of a single tooth during the hot orbital forging process are shown in Figure 13. In the middle stage of orbital forging (Figure 13a), as the tooth root is the area directly in contact with the gear cavity, it is subjected to a relatively large stress. At this time, the metal at the tooth tip has not completely flowed into the gear cavity, and the stress value is relatively small. In the later stage of orbital forging until the end of the feed movement (Figure 13b and 13c), the tooth root on the lower end face is filled first and is subjected to the maximum stress among all parts. During the process of plastic deformation 传递 from bottom to top, the stresses at the tooth root and tooth tip continue to increase compared to before, but the stress decreases from bottom to top. In the finishing stage (Figure 13d), the tooth tip on the lower end face is basically filled, and the stress decreases sharply, while the tooth tip on the upper end face is subjected to a relatively large stress.
3.4 Equivalent Strain Field
The distribution characteristics of the equivalent strain during the hot orbital forging process are shown in Figure 14. In the middle stage of forming, when the tooth profile begins to form (Figure 14a), the equivalent strain is distributed at the edges of the convex platforms, the center of the blank, and the tooth root. Among them, the tooth root has a relatively large equivalent strain value, while the equivalent strain values at the convex platforms and tooth tip are very small. In the later stage of forming, when the flash begins to form (Figure 14b), a relatively small equivalent strain value appears in the flash, and the equivalent strain value at the tooth root is relatively large and decreases from top to bottom. At the end of the feed movement (Figure 14c), the equivalent strain value on the tooth profile decreases along the tooth root, tooth profile, and tooth tip. In the finishing stage (Figure 14d), the equivalent strains at the tooth root, tooth center, and flash continue to increase, while the equivalent strain at the tooth tip hardly changes.
3.5 Temperature Field
The distribution of the temperature field during the hot orbital forging of the cylindrical spur gear at different times is shown in Figure 15. It can be seen that the parts in contact with the die and with relatively small plastic deformation (such as the upper and lower convex platforms) experience a large temperature drop due to heat conduction and small deformation during the deformation process. In contrast, the tooth profile part, which undergoes relatively large plastic deformation, has a slow temperature drop. There is a significant difference in temperature distribution between the tooth root and tooth tip, with the tooth tip temperature being higher than the tooth root temperature, while the temperature of the material in the center of the blank hardly changes.
3.6 Forming Load Variation
The variation curves of the axial and radial forming loads during the hot orbital forging of the cylindrical spur gear are shown in Figure 16. The axial forming load can be divided into four stages according to the tooth forming state. In the initial stage of forming, the orbital die contacts the workpiece locally, and the metal in the contact area undergoes plastic deformation, and the forming load increases slowly. In the middle stage of forming, as the tooth profile begins to form, the axial load increases at an accelerated rate. In the later stage of forming, due to the significant increase in the resistance to metal filling in the die cavity, the axial load also increases sharply and reaches a maximum value of approximately 2500 kN. In the finishing stage, the axial load shows a decreasing trend with a relatively fast decrease rate and fluctuations.
From Figure 16b, it can be seen that during the gear orbital forging process, the radial load changes periodically. In the finishing stage, when the lower die stops feeding and the orbital die only performs a swinging motion, mainly the flash is deformed, and the radial load increases steeply. Subsequently, the forming load decreases and changes periodically. It can also be observed that during the hot orbital forging of the cylindrical spur gear, the radial load is much smaller than the axial load.
4. Experiment
Based on the results of the finite element simulation, the orbital forging die and blank were designed and manufactured. Hot orbital forging experiments were conducted on 20CrMnTi samples using a T630 hot orbital forging machine. The experimental samples and the cylindrically spur gears formed by finite element simulation are shown in Figure 17. It can be seen that the tooth profiles of the experimentally formed gear samples are fully filled, and the tooth forming effect and flash shape are consistent with the finite element simulation results, validating the reliability of the established finite element model.
5. Conclusion
5.1 Summary of Key Findings
- In the hot orbital forging process of the cylindrical spur gear, the blank deformation zone consists of the active deformation zone and the passive deformation zone. The tooth profile is gradually formed from the upper end to the lower end, and the blank takes on a mushroom shape. In the early and middle stages of forming, the metal in the active deformation zone fills the die cavity radially. In the later stage of orbital forging, the metal in the active deformation zone mainly fills the entire die cavity through axial flow.
- During the forming process, the equivalent strain and equivalent stress in the tooth root region are the largest. The tooth root temperature is lower than that of the tooth tip, and the metal material in the center region of the blank hardly deforms, and the temperature field hardly changes. The axial load gradually increases with the progress of plastic deformation, and the increase rate gradually becomes faster, with a maximum value of approximately 2500 kN. The radial load changes periodically during the feed stage, and the radial load is much smaller than the axial load.
- The experimental results of the cylindrical gear hot orbital forging process are in good agreement with the finite element simulation results, validating the accuracy and reliability of the established finite element model.
5.2 Implications for Aerospace Gear Manufacturing
The findings of this study have significant implications for the manufacturing of aerospace gears. The understanding of the metal deformation behavior and tooth filling characteristics in the hot orbital forging process allows for more precise control of the manufacturing process. By optimizing the process parameters based on the research results, it is possible to improve the quality and performance of aerospace gears. For example, the knowledge of the distribution of equivalent stress and strain can help in designing gears with enhanced mechanical properties, ensuring their reliability and durability in aerospace applications. The ability to predict and control the temperature field during forging can contribute to reducing thermal damage and improving the microstructure of the gears.
5.3 Future Research Directions
- Process Optimization: Further research can focus on optimizing the hot orbital forging process parameters to achieve better gear quality and performance. This may include exploring different combinations of feed rates, rotational speeds, and orbital angles to minimize defects and improve dimensional accuracy.
- Microstructure and Property Relationship: Investigating the relationship between the microstructure evolution and mechanical properties of the gears after hot orbital forging. Understanding how the forging process affects the microstructure and subsequently the mechanical properties will enable the development of more advanced heat treatment and post-processing techniques.
- Multi-Physics Coupling Analysis: Incorporating more physical phenomena such as heat transfer, microstructure evolution, and mechanical deformation in a coupled manner to provide a more comprehensive understanding of the hot orbital forging process. This will help in predicting and controlling the process more accurately.
- Application to Other Gear Types: Extending the research to other types of gears with more complex geometries or different materials to evaluate the applicability and limitations of the hot orbital forging process. This will expand the range of gear manufacturing techniques available for aerospace and other industries.
In conclusion, this study has provided valuable insights into the hot orbital forging process for aerospace cylindrical spur gears. The results contribute to the advancement of gear manufacturing technology and offer a foundation for future research and development in this area. By continuing to explore and innovate in this field, the aerospace industry can expect to benefit from improved gear performance, reduced manufacturing costs, and enhanced overall system reliability.
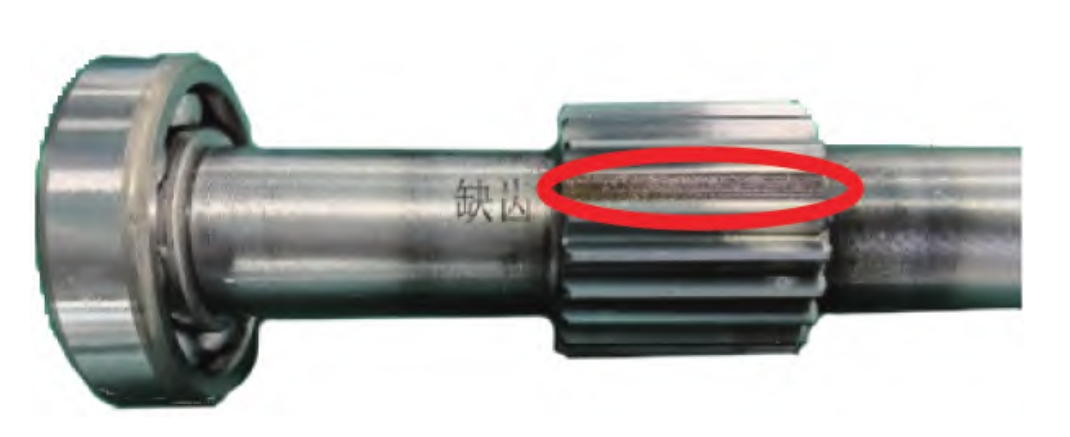