This article focuses on the thermal characteristics of dry gear hobbing machines. It proposes a multi-source information fusion testing method and constructs a data processing and analysis method based on the IPO model. Through experimental verification, the effectiveness and reliability of the method are demonstrated, providing technical support for the thermal balance design of dry gear hobbing machines.
1. Introduction
Dry gear hobbing machines are advanced green gear manufacturing equipment. Their thermal behavior is unique and complex due to significant changes in spatial structure layout, drive transmission mode, and heat generation and dissipation laws. Thermal errors, which account for 40% – 70% of the total errors, have a major impact on machining accuracy. Therefore, it is crucial to develop a multi-source information fusion-based thermal testing and analysis method to understand the thermal characteristics of dry gear hobbing machines and improve gear machining accuracy stability.
1.1 Research Status
Previous studies have mainly focused on building machine tool thermal error models and compensation methods. Experimental tests have been mainly conducted on the temperature and thermal deformation measurements of conventional machine tools such as lathes, grinders, and milling machines. However, there are relatively few studies on the thermal testing of dry gear hobbing machines, especially on online thermal characteristic testing and analysis methods.
1.2 Research Significance
This research is of great significance for understanding the thermal behavior of dry gear hobbing machines, improving machining accuracy, and providing technical support for thermal balance design.
2. Testing and Analysis Technical Scheme
The dry gear hobbing machine is usually designed with multi-axis linkage and a vertical layout. The structural and operational characteristics result in unique and complex thermal behavior. The heat sources include power motor heat generation, friction heat of moving pairs, cutting heat, and environmental temperature changes. The heat transfer behavior is affected by various factors, and the temperature distribution is uneven.
2.1 Testing Function Design
The testing function mainly focuses on the temperature and thermal deformation measurement of the dry gear hobbing machine, including the measurement of multi-source thermal signals such as columns, worktables, spindles, and beds. It also reserves interfaces for force, vibration, and noise measurement to meet the in-depth research needs of machine tool performance.
2.2 Data Processing and Analysis
Based on the LabVIEW data testing software, Python data processing tools are seamlessly embedded through secondary development to construct a data sequential processing method based on the IPO model. This method enables accurate analysis of the multi-source information fusion test data of the dry gear hobbing machine’s thermal characteristics.
3. Multi-Source Information Fusion Testing Method
3.1 Testing Hardware Function Realization
The hardware selection for the lower computer is crucial. The NI9214 C series temperature input module with 16 channels is used for temperature collection, and its accuracy is enhanced by various means. The NI-9202 C series voltage input module with 16 synchronous sampling differential input channels is used for thermal deformation collection. The Compact DAQ portable chassis cDAQ – 9174 is used for module installation and operation, and appropriate sensors are selected according to the characteristics of temperature and thermal deformation measurement.
3.2 Upper Computer Software Function Development
The upper computer software is developed based on LabVIEW to realize real-time data acquisition and processing analysis. The functions include temperature and thermal deformation signal acquisition, pre-processing and post-processing digital display modules. The software also enables synchronous acquisition of temperature and thermal deformation data and provides data visualization and analysis functions.
3.3 Test Platform Integration
The test platform integrates functions such as data storage, platform management, and platform maintenance. Dynamic storage of the entire machining process data and single workpiece thermal data is set up. The platform management ensures data security, and the platform maintenance provides reserved collection ports for other signals and realizes online measurement of multiple signals.
4. Multi-Source Thermal Data Processing and Analysis Method
4.1 Processing Flow
The experimental data of the dry gear hobbing machine is large and may be affected by interference. Therefore, a data processing method based on the IPO model is constructed. The method includes inputting data in TDMS format, processing it with Python tools, and outputting the processed data in visual and file formats.
4.2 Analysis Method
The data is processed sequentially through outlier replacement, moving average filtering, wavelet filtering, and data resampling. Outlier replacement uses methods such as standard deviation and upper and lower limit settings. Moving average filtering calculates the average value within a window. Wavelet filtering uses threshold processing to remove noise, and data resampling adjusts the data density.
5. Application and Analysis
5.1 Application Verification Experiment
An experiment is conducted on a YE3115CNC dry gear hobbing machine to test the temperature and thermal deformation data. The experimental parameters are set, and the temperature sensors and thermal deformation sensors are arranged according to certain principles.
5.2 Results Discussion and Analysis
The temperature measurement results show that the proposed testing method has high accuracy. The temperature curves of different positions on the machine tool are analyzed, and the reasons for the temperature changes are explained. The thermal deformation curve of the worktable spindle is also analyzed, and the influence of environmental temperature on thermal deformation is discussed.
6. Conclusion and Future Work
6.1 Research Achievements
- A multi-source information fusion testing method for the thermal characteristics of dry gear hobbing machines is proposed, which improves the technicality, objectivity, and accuracy of online temperature and thermal deformation measurement.
- A multi-source thermal data processing and analysis method based on the IPO model is constructed, which enhances the scientific nature of thermal characteristic analysis.
- The effectiveness of the proposed testing and analysis method is verified through experiments, realizing the online measurement and accurate analysis of the thermal behavior of dry gear hobbing machines.
6.2 Future Research Directions
Future work will focus on improving the function of the acquisition system and optimizing the thermal balance design of the machine tool to provide theoretical and technical support for improving the thermal stability of dry gear hobbing machines.
In the following, some possible figures are presented to illustrate the key points of the article:
Schematic Diagram of Dry Gear Hobbing Machine Structure
This figure shows the structure of the dry gear hobbing machine, including the spindle, worktable, column, and bed, to help readers understand the machine’s layout and components.
Temperature Sensor Layout on the Machine Tool
The layout of temperature sensors at different positions on the machine tool is illustrated, such as the motor, bearing, and guide rail, to show the distribution of temperature measurement points.
Thermal Deformation Sensor Layout on the Machine Tool
The layout of thermal deformation sensors on the spindle and worktable is presented to demonstrate how to measure the thermal deformation of key components.
Flowchart of the Multi-Source Information Fusion Testing Method
This flowchart details the process of the multi-source information fusion testing method, from hardware selection to software development and data processing.
Temperature and Thermal Deformation Curves of the Machine Tool
The temperature and thermal deformation curves of the machine tool during the machining process are shown to analyze the thermal characteristics and trends.
By presenting these figures and detailed text, readers can have a more comprehensive understanding of the research on the thermal characteristics of dry gear hobbing machines.
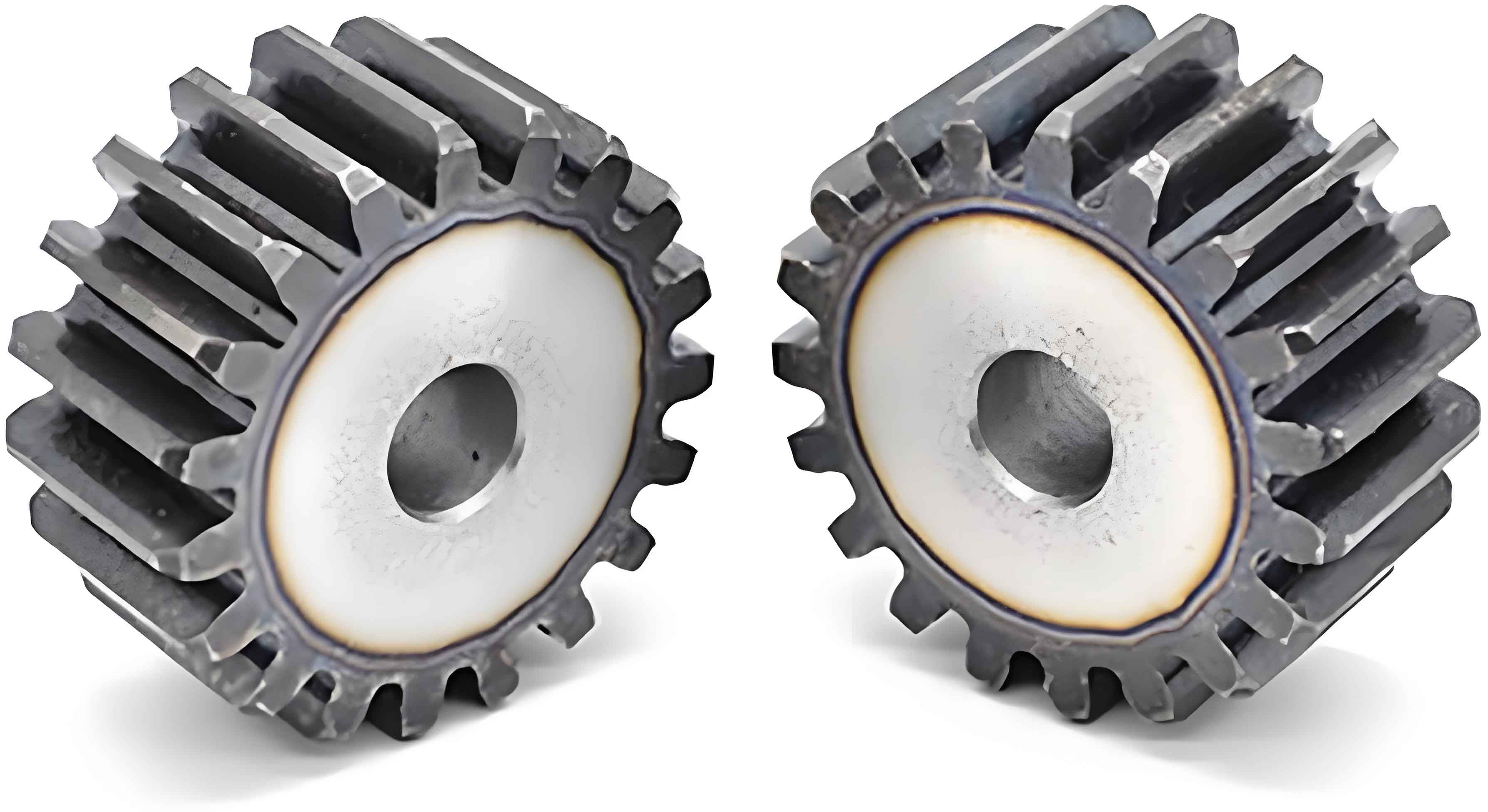