Abstract:
The miter gear noise issue in miter saws with a triple geared drive structure. The root causes of the noise are analyzed from aspects such as gear backlash, gear installation, and critical support components. Corresponding improvement measures are proposed.
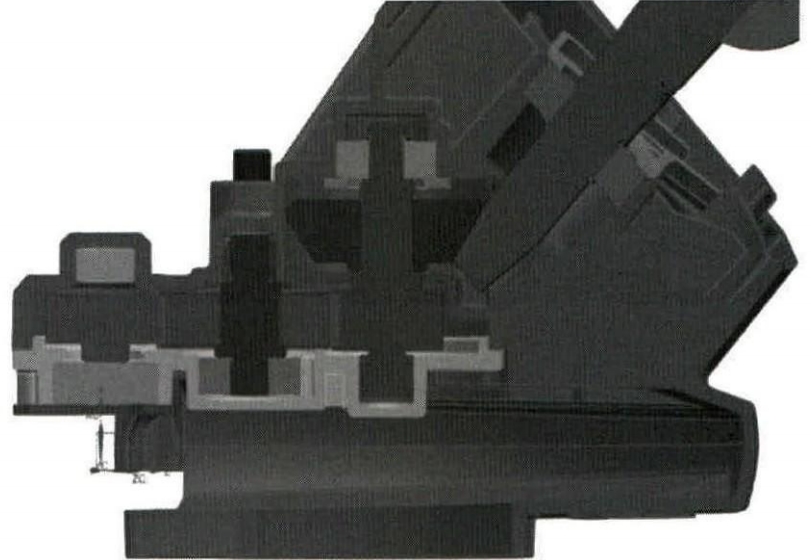
1. Introduction
Miter saws are portable electric tools relying on rotating toothed blades (with diameters ≤ 350mm) to cut materials like aluminum, wood, or similar composites. They are widely used in daily operations in the architectural decoration field due to their high cutting capacity and precision. However, miter gear noise issues, especially from bevel gears, can occur during production and assembly. This paper analyzes the multiple factors leading to miter gear noise in miter saws with a triple geared drive structure and proposes corresponding solutions based on practical cases encountered in tool manufacturing enterprises.
2. Structural Characteristics
The triple geared structure used in miter saws. Employing three pairs of gears, especially spiral bevel gears, can effectively enhance cutting capabilities and add functionalities, such as enabling three-dimensional tilt cuts.
3. Cause Analysis
Fifteen tools with significant noise were selected for comparison tests of motor gears and large bevel gears. The results are summarized in Table 1.
Table 1: Relationship Between Gear Noise and Backlash
Serial No. | Sample No. | Gear Noise | Backlash (mm) | Remarks |
---|---|---|---|---|
1 | A1-A5 | NG | 0.30~0.55 | |
2 | B1-B5 | NG/AC | 0.00~0.10 | |
3 | C1-C5 | AC | 0.15~0.30 |
Figure 2: Critical Dimensions Affecting Gear Installation
<img src=”https://example.com/critical_dimensions.png” />
(Note: This is a placeholder image link. Replace it with an actual image URL.)
Table 2: Adjusted Tolerance Ranges for Critical Dimensions
Item | Adjusted Tolerance |
---|---|
A1-A2 | 0/-0.15 |
B1-B2 | 0/-0.11, +0.1/0 |
B3 | 0/-0.05 |
C1-C2 | 0/-0.11, 0/-0.1 |
D1 | +0.1/0, 0/-0.12 |
4. Improvement Measures
4.1 Gear Backlash
The miter gear backlash is a critical factor affecting gear noise. Through extensive investigations, it is found that a backlash range of 0.15mm to 0.30mm between the motor gear and the large bevel gear is reasonable. Therefore, the following improvements are proposed:
- Adjust the required backlash between the motor gear and the large bevel gear to 0.15mm~0.25mm.
- Request the gear processing department to effectively control gear quality based on the meshing method.
4.2 Gear Installation
The size accuracy of miter gear installation is crucial, in addition to the precision of miter gear themselves. The critical dimensions affecting gear installation are shown in Figure 2. The tolerance ranges should be narrowed as much as possible, considering processing capabilities and processes.
Improvement measures include:
- Set appropriate tolerances and thoroughly investigate equipment capabilities. Purchase new equipment if the current equipment’s process capabilities are insufficient.
- Include the listed sizes as critical dimensions in daily management and regularly analyze Cpk.
4.3 Critical Support Components
During the investigation of defects, various factors were found to affect the accuracy of the critical dimensions. The gearbox cover, as shown in Figure 3, is particularly prone to deformation during aluminum die-casting and subsequent processing, leading to processing defects and potential gear noise issues in the assembly line.
Improvement measures include:
- Add arc corner designs at the step differences.
- Increase the arrangement of reinforcing ribs as much as possible between the three connecting holes.
- Strengthen the positional tolerance requirements for holes 1 and 3.
5. Additional Considerations
5.1 Gear Bruising
Gear bruising, especially with protruding surface injuries or burr residues, can cause miter gear noise to varying degrees. Most of these injuries occur before the heat treatment process. Effective management of the processing process is the best way to eliminate or reduce such phenomena.
5.2 Gear Precision
Gear processing accuracy directly affects miter gear noise, especially in multi-stage gear transmission structures. The thin-walled gearbox cover is more prone to deformation during aluminum die-casting and subsequent processing steps, often causing various defects and influencing gear noise. Therefore, strict control is necessary during design and production.
6. Conclusion
The noise issue of bevel gear in the triple geared drive structure of miter saws significantly affects the user experience and product lifespan. It is imperative to eliminate and reduce such defects in the quality management process of electric tool manufacturing enterprises. By adopting the above improvement measures, miter gear noise issue can be effectively mitigated.