1. Introduction
Gears are fundamental components in mechanical systems, widely used in machinery, automobiles, aerospace equipment, and other fields. They play a crucial role in transmitting motion and power, and their performance directly impacts the operation, service life, safety, and reliability of high-end equipment. Gears can be classified into circular gears and non-circular gears based on the structure of their pitch surfaces. Circular gears, including bevel spur gears, cylindrical spur gears, cylindrical helical / bevel gears, and spiral bevel gears, have a rotational pitch surface. Non-circular gears, such as non-cylindrical spur gears, non-bevel spur gears, and non-spiral bevel gears, have a non-rotational pitch surface. Currently, gear manufacturing methods mainly include cutting and precision plastic forming.
Cutting processes, such as hobbing, milling, shaping, and grinding, are traditional methods for gear manufacturing. However, these methods have several drawbacks. They result in low material utilization and long production cycles. Moreover, the cutting process severs the metal fibers in the gear tooth profile, which impairs the mechanical properties of the gear and significantly reduces its service life. Additionally, cutting gears is associated with high manufacturing costs and low production efficiency.
Gear precision plastic forming is an advanced manufacturing technology that offers significant advantages over traditional cutting methods. This process involves shaping a gear blank using a die with a tooth profile. Under the action of a press, the material undergoes plastic deformation to fill the tooth cavity, resulting in a gear that requires little or no further machining. Precision plastic forming not only saves materials and energy but also improves production efficiency. It enables the formation of a dense and uniform material structure within the gear, with the metal flow lines continuously and rationally distributed along the tooth profile. This, in turn, enhances the gear’s wear resistance, corrosion resistance, and bending strength at the root, substantially improving its fatigue performance. As a result, precision plastic forming is considered the future direction for high-performance gear manufacturing.
The research and development of gear precision plastic forming in China has a long history. Since the 1970s, significant progress has been made in this field. For example, in the 1970s, Wuhan University of Technology and Wuhan Iron and Steel Powder Metallurgy Company 合作 used powder metallurgy precision hot forging to manufacture the world’s largest 25 kg roll table bevel spur gear for a rolling mill. In the 1980s, Shandong University of Technology and Qingdao Precision Forging Gear Factory 合作 developed a hot precision forging process for bevel gears. In the 1990s, with the development of the automotive industry, the demand for high-strength and lightweight automotive gears increased. Wuhan University of Technology developed a cold rotary forging precision forming technology for bevel spur gears, which was used in the production of passenger car planetary gears, half-shaft gears, and combined gears. This technology achieved a tooth profile accuracy of 6 – 7 grades, eliminating the need for subsequent grinding and realizing the first gear tooth profile forming without cutting in China. The production efficiency reached 6 – 10 pieces per minute, significantly improving the fatigue life and production efficiency of the gears.
In recent years, with the development of China’s aerospace and defense weaponry, higher requirements have been imposed on gear transmission performance. Therefore, there is an urgent need to develop high-performance and long-life gear precision forming manufacturing technologies. This article summarizes the theory, technology, equipment, and applications of gear precision plastic forming, providing a reference for the research and development of high-performance gear precision plastic forming manufacturing.
2. Gear Precision Plastic Forming Theory
2.1 Gear Forming Plastic Mechanics Analytical Method
The forming load is a crucial mechanical parameter in gear plastic forming as it determines the die material and equipment tonnage. Scholars worldwide have developed methods to predict the forming load of cylindrical gear precision forging using plastic mechanics analytical methods, such as the upper bound method, slip line method, and principal stress method, based on simplified involute gear shapes. illustrates the use of the upper bound method to divide the plastic deformation zone for calculating the forming load in cylindrical helical gear closed-die forging. Although theoretically possible, the complex nature of the gear plastic forming process and the intricate theoretical calculations make this method less practical for industrial applications.
2.2 Gear Forming Finite Element Method
With the development of computer technology in the past 30 years, scholars have widely adopted the rigid-plastic / rigid-viscoplastic and elastic-plastic finite element methods to simulate the gear precision plastic forming process. These methods help reveal the macro and micro deformation laws, forming mechanisms, temperature field distributions, and mechanical parameter changes.
In gear precision plastic forming technologies like forging, rolling, extrusion, and rotary forging, the plastic deformation of the metal material is significant, while the elastic deformation is negligible. Therefore, the deformation material can be regarded as rigid-plastic or rigid-viscoplastic. The rigid-plastic finite element method is suitable for simulating the precision plastic forming process of rigid-plastic hardening materials, such as analyzing the deformation characteristics and laws of gear cold forging. The rigid-viscoplastic finite element method is used to simulate the precision plastic forming process of rigid-viscoplastic materials and conduct thermo-mechanical coupling analysis of deformation and heat transfer.
The elastic-plastic finite element theory considers both the elastic and plastic deformations of the deformed part. To accurately predict the elastic deformation of the die and the elastic recovery process of the formed gear and improve the forming accuracy, the elastic-plastic theory is essential. In the simulation of the gear plastic forming process, the blank is defined as an elastic-plastic body, and the die is defined as an elastic body for numerical simulation analysis.
2.2.1 Material Constitutive Relationship Determination
The true stress – true strain curves of the material are obtained through uniaxial tensile and high-temperature compression tests. Then, the gear constitutive equation is derived by fitting the curves. Fig. 2 shows the room temperature and high-temperature true stress – true strain curves of 20CrMnTi gear steel obtained using a Zwick Z100 universal testing machine and a Gleeble-3500 thermal compression simulator.
2.2.2 Finite Element Mesh Model Establishment
Mesh generation is a crucial step in the finite element preprocessing. Reasonable mesh division ensures the accuracy of the calculation results. Due to the complex shape of gears, increasing the number of mesh elements can better describe the gear surface and improve the simulation accuracy. However, an excessive number of mesh elements increases the simulation time. On the other hand, too few mesh elements can lead to poor final part shapes and calculation failures due to mesh distortion. Therefore, a reasonable mesh division strategy is required. Uniform mesh division shows that as the number of meshes increases, the quality of the simulated tooth profile improves. However, in gear precision plastic forming, the tooth profile is the area of significant plastic deformation and the focus of the study, while the deformation in the middle part of the blank is relatively small and approximates rigid movement. Therefore, a local refinement method can be adopted, with a denser mesh for the tooth profile and a sparser mesh for the less deformed middle part of the blank.
2.2.3 Boundary Condition Treatment
In gear plastic forming, friction between the blank and the die cavity affects the metal flow and thus the forming quality, load, and die life. The most commonly used friction models in engineering are the shear friction model and the Coulomb friction model. The Coulomb friction model is suitable for describing the friction conditions in sheet forming, while the shear friction model is more appropriate for volume forming. In gear precision forming, the shear friction model is often used, and the friction coefficient varies depending on the lubricant. The contact interface between the blank and the die is set as a rigid – flexible contact type, with the die defined as a rigid body and the blank as a flexible body. The friction coefficients for cold, warm, and hot forming are typically 0.12, 0.25, and 0.30, respectively.
In gear hot and warm deformation processes, heat transfer occurs between the die and the blank due to the temperature gradient. The blank transfers heat to the die through convection and conduction at the contact surface and exchanges heat with the surrounding environment through radiation. Additionally, friction heat is generated at the contact surface due to relative sliding. To accurately analyze the temperature field changes during gear warm forming using the finite element method, it is necessary to define the initial temperatures of the blank and the die, as well as the surface heat transfer coefficients and radiation heat transfer coefficients of various materials.
2.2.4 Gear Forming Finite Element Model Establishment
After determining the gear material model and boundary condition model, a plastic forming simulation software (such as DEFORM-3D, Abaqus, or Simufact) is selected to establish the gear forming finite element model. For cold forming processes, a room temperature material hardening model is required, or the corresponding material model can be selected from the software material library. The blank and die geometries are imported, the blank mesh is divided, and the blank is defined as a deformable body, while the die is defined as a rigid body. The initial velocity field and friction boundary conditions of the die are defined to establish the rigid-plastic finite element model. For warm or hot forming analyses, a high-temperature material viscoplastic model is imported or selected from the library, and the heat transfer boundary conditions are defined to establish the rigid-viscoplastic finite element model or the deformation – heat transfer coupling finite element model. To study the forming accuracy of the gear, an elastic-plastic finite element model is established to analyze the elastic deformation behavior of the formed gear or the die during the forming process.
Wuhan University of Technology’s Professor Hua Lin’s team proposed using the tooth surface comprehensive deviation to evaluate the tooth profile accuracy of cold rotary forged bevel spur gears. By establishing an elastic-plastic finite element model of the cold rotary forging deformation of bevel spur gears, the elastic deformation of the tooth profile concave die and the springback deformation distribution of the formed gear during the cold rotary forging process were analyzed. Based on the factors affecting the tooth profile accuracy during the cold rotary forging process of bevel gears and the elastic-plastic finite element theory, the transfer law between the die machining accuracy, die elastic deformation, and gear forming accuracy was revealed. Thus, a prediction model for the cold rotary forging forming accuracy of bevel spur gears was established. A new method for controlling the forming accuracy of straight bevel gears by cold rotary forging based on the 协同调控 of die machining, die preloading, and cold rotary forging process parameters was also proposed.
3. Gear Precision Plastic Forming Technology
Gear precision plastic forming technologies can be classified into hot precision forging, cold precision forging, warm precision forging, and composite precision forging based on the forming temperature. According to the different tooth profile structures of various gears, scholars worldwide have conducted extensive research on die structure design and developed multiple precision plastic forming technologies for different types of gears. These include closed-die forging, divided-flow forging, floating die forging, extrusion forming, rotary forging, rolling forming, and composite forming technologies that combine different forming techniques.
3.1 Gear Hot Precision Forging Technology
Hot precision forging involves heating the blank above the recrystallization temperature and deforming it plastically under the action of a die to fill the cavity and form the part. This technology has the advantages of low deformation resistance and good plasticity of the material, making it suitable for forming complex workpieces. The hot precision forging technology for gears originated in the 1950s when Germans first used the closed-die hot forging method to form bevel spur gears. Bevel spur gears, with their efficient, stable, and low-noise characteristics, are widely used in automobiles, machine tools, and other fields. Due to their relatively simple tooth profile formation compared to other types of gears, bevel spur gears were the first to be studied and developed for plastic forming.
In China, research on gear hot precision forging began in the 1970s, focusing on process optimization, die design, and parameter optimization for hot forging bevel spur gears. To ensure complete filling of the tooth profile, the hot precision forging process typically requires pre-forging, final forging, and trimming of the flash. The accuracy of hot precision forged straight bevel gears is generally 9 – 10 grades and is widely used in the mass production of planetary bevel gears, half-shaft bevel gears for commercial vehicles, tractors, agricultural machinery, and construction machinery.
However, for cylindrical spur gears and cylindrical helical / bevel gears, the tooth profile is on the cylindrical surface, and the plastic flow direction of the metal material is perpendicular to the force direction during forging. This makes it more difficult to form the tooth profile compared to bevel gears. Additionally, the closed-die forging process for these gears suffers from issues such as a sharp increase in forming load, difficulty in filling the corners, and low die life, especially for cylindrical helical / bevel gears with a helical tooth profile, where the material flow is more complex. To address these problems, scholars have combined the divided-flow pressure reduction process with the closed-die forging process to develop the divided-flow forging technology for forming cylindrical spur gears and cylindrical helical / bevel gears. This technology involves opening divided-flow holes in the blank or punch, allowing part of the blank to flow into the divided-flow holes during forging, thereby improving the material flow and reducing the forming load.
Despite its advantages, hot precision forging has some limitations. The strong oxidation of the blank surface during the process leads to lower surface quality and dimensional accuracy of the formed gear. Therefore, it is mainly used for the production of planetary bevel gears and half-shaft bevel gears for commercial vehicles, tractors, and some electric tool spiral bevel gears with relatively low tooth profile accuracy requirements. It is not suitable for the forming of high-precision passenger car gears.
3.2 Gear Cold Precision Forging Technology
Cold precision forging is a precision forging process in which the blank undergoes plastic deformation at room temperature to fill the cavity and form the part. This process avoids geometric errors caused by high-temperature oxidation and thermal expansion and contraction, resulting in high geometric accuracy and good surface quality of the formed part. It is the main forming technology for high-performance and high-precision passenger car gears,especially for bevel spur gears. Passenger car bevel gear cold precision forging technologies mainly include closed-die cold precision forging and cold rotary forging precision forming.
3.2.1 Gear Closed-Die Cold Precision Forging Technology
Gear closed-die cold precision forging involves the plastic deformation of the blank within a closed die cavity at room temperature to fill the cavity. This technology typically consists of two steps: preforming and final forming. It offers the advantages of a short process flow and high forming accuracy, with the metal flow lines continuously distributed along the tooth profile, resulting in good mechanical properties of the gear. However, the process has some drawbacks, such as high deformation resistance, requiring large-tonnage equipment, and poor tooth profile filling effect.
Many scholars have conducted extensive research on the tooth profile filling process, die failure modes, and forming defects in the cold forging of bevel spur gears, cylindrical spur gears, and cylindrical helical / bevel gears. The gear floating die forging technology, a type of closed-die cold precision forging, addresses some of these issues. By incorporating elastic elements below the die, the die can move downward with the punch during forming. This converts the friction between the die and the blank into a positive driving force for metal flow, reducing the friction resistance and effectively improving the tooth profile filling effect and reducing the forming load. The floating die principle allows for the adjustment of the friction force between the die and the blank by controlling the relative speed of the punch and the die, thereby regulating the metal flow process, forming load, and tooth profile filling effect.
To further improve the tooth profile filling effect and reduce the forming load in gear closed-die cold precision forging, some scholars have adopted the divided-flow forging technology for forming cylindrical spur gears and cylindrical helical / bevel gears. For example, Choi J C et al. proposed an internal cavity divided-flow forming method for cylindrical spur gears to enhance the tooth profile filling. Kou Shuqing and Wang G C et al. developed two-step forming processes such as closed-die upsetting – constrained hole divided-flow and closed-die forging – inward divided-flow for straight cylindrical gears, which significantly reduced the forming force and improved the tooth profile filling effect. Feng W et al. achieved the cold precision forging of cylindrical helical / bevel gears by designing blanks with different divided-flow hole diameters.
Due to the high forming load in gear cold precision forging, it is mainly used for the forming of small-module automotive bevel spur gears.
3.2.2 Gear Cold Rotary Forging Precision Forming Technology
Gear cold rotary forging precision forming is an advanced technology that utilizes the combined rotary and swinging motion of a conical rotary head and the linear feeding motion of the die to gradually deform the workpiece and form the gear. This process offers several advantages, including low forming load, good filling effect, and high production efficiency. It is capable of forming large-module and large-diameter gears that cannot be produced by closed-die cold precision forging.
Since the 1990s, the research team led by Professor Hua Lin at Wuhan University of Technology has conducted systematic and in-depth research on the cold rotary forging mechanism, forming laws, product testing and quality control, blank pretreatment, and long-life die design and manufacturing for bevel spur gears. They have elucidated the macro and microstructural evolution laws of bevel spur gear rotary forging – carburizing and quenching, determined the forming limits of gear rotary forging, established the theory of gear cold rotary forging, and invented a high-performance gear tooth profile non-cutting cold rotary forging method. They have also overcome key technologies in die – electrode – prestressed ring design and manufacturing, as well as rotary forging – carburizing and quenching measurement and control. The cold rotary forged gears have refined grain structures, continuous flow lines, and an accuracy of 6 – 7 grades, eliminating the need for tooth profile grinding and increasing the fatigue life by 1 – 2 times and the production efficiency by 10 – 20 times. This achievement realized the non-cutting cold rotary forging precision forming and large-scale production of high-precision passenger car gears in China for the first time and won the second prize of the National Science and Technology Progress Award in 2005, marking a significant milestone in China’s gear precision plastic forming technology.
Based on the structural characteristics of bevel spur gears and the motion mode of the rotary forging equipment, the cold rotary forging process of bevel spur gears involves the design of a conical rotary head and a tooth profile cavity in the lower die. During the forging process, the plastic deformation of the blank fills the tooth profile cavity under the coordinated reciprocating action of the rotary head’s swinging and the die’s feeding motion, gradually forming the gear. To ensure the stable forming of bevel spur gears, the research team proposed the following forming conditions based on the geometric, kinematic, and plastic mechanics studies, combined with finite element modeling and simulation analysis:
3.2.2.1 Stable Rotary Forging Conditions
To achieve continuous and stable rotary forging of bevel spur gears, the blank must remain relatively stationary with respect to the lower die during the forming process. This requires that the horizontal dragging force acting on the local deformation zone of the blank is less than the static friction force of the blank, and the force on the blank in the feeding direction of the lower die is balanced. Based on the stable rotary forging mechanical model, Coulomb friction conditions, and geometric motion relationships, the stable rotary forging condition for bevel spur gears can be expressed.
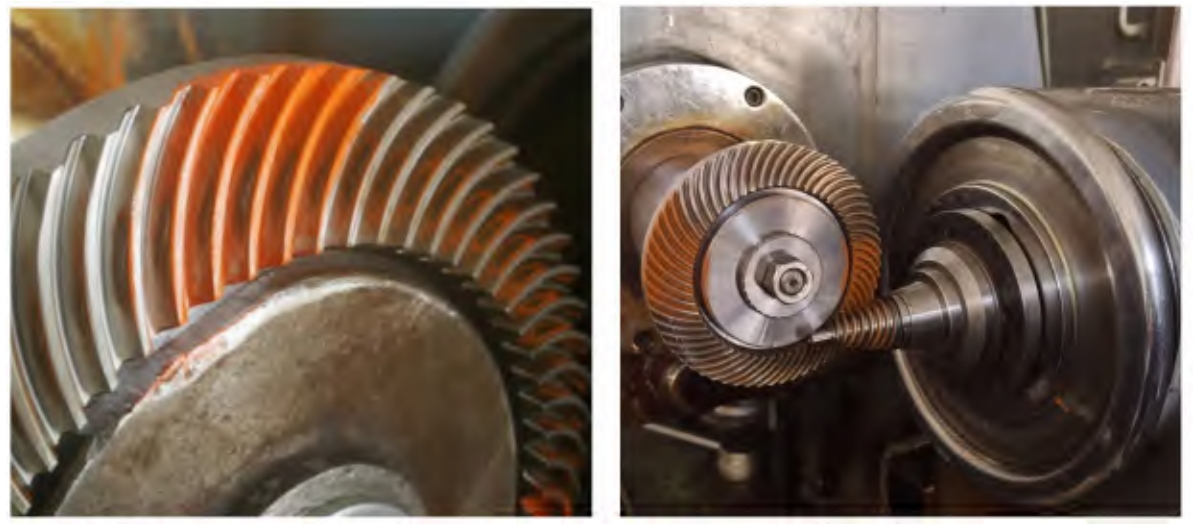