1. Introduction
In the field of industrial automation, industrial robots play a crucial role. The RV gearbox, as a vital component in the power transmission system of industrial robots, is prone to failure. Therefore, effective fault diagnosis methods for RV gearboxes are of great significance for ensuring the stable operation of industrial robots and improving production efficiency.
1.1 Importance of RV Gearbox in Industrial Robots
The RV gearbox is widely used in the power transmission systems of industrial robots due to its high reduction ratio, high torque capacity, and compact structure. It enables the robot to perform precise and powerful movements, which is essential for various industrial applications such as welding, assembly, and material handling.
1.2 Common Faults in RV Gearboxes
Some common faults in RV gearboxes include gear wear, bearing damage, and shaft misalignment. These faults can lead to increased vibration, noise, and reduced transmission efficiency, ultimately affecting the performance and lifespan of the industrial robot.
1.3 Challenges in Fault Diagnosis
The early fault symptoms of RV gearboxes are often subtle and masked by noise and other interfering factors. Traditional fault diagnosis methods may have difficulty accurately detecting and identifying these early faults, highlighting the need for more advanced and reliable diagnostic techniques.
2. Related Work
Over the years, numerous research efforts have been dedicated to improving the fault diagnosis capabilities of RV gearboxes.
2.1 Traditional Fault Diagnosis Methods
Methods such as vibration analysis, temperature monitoring, and oil analysis have been commonly used. Vibration analysis, in particular, is widely employed as it can provide valuable information about the mechanical condition of the gearbox. However, these traditional methods often face challenges in dealing with complex fault patterns and early fault detection.
2.2 Advanced Signal Processing Techniques
With the development of signal processing technology, advanced techniques such as wavelet transform, empirical mode decomposition (EMD), and spectral kurtosis have been proposed. These techniques aim to enhance the fault feature extraction capabilities by decomposing the vibration signals into different frequency components and analyzing their characteristics. For example, the wavelet transform can effectively handle non-stationary signals, while spectral kurtosis is sensitive to impulsive components associated with faults.
2.3 Existing Research on RV Gearbox Fault Diagnosis
Previous studies have focused on various aspects, including the development of new fault diagnosis algorithms, the optimization of sensor placement, and the establishment of fault databases. Some researchers have proposed using machine learning algorithms, such as neural networks and support vector machines, for fault classification and prediction. Others have explored the combination of multiple diagnostic methods to improve the accuracy and reliability of fault diagnosis.
3. The Improved OSF Method
This section presents the details of the proposed improved OSF method for RV gearbox fault identification.
3.1 Autogram Kurtosis Principle
The Autogram is an effective algorithm for determining the optimal demodulation band. It is based on the unbiased autocorrelation detection principle. By dividing the frequency band using the maximum overlap discrete wavelet packet transform (MODWPT) and calculating the kurtosis value of each frequency band, the Autogram kurtosis curve can be obtained. This curve provides valuable information for detecting fault features in the presence of noise.
3.2 OSF Method for Signal Processing
The OSF method is used to process the Fourier spectrum of the vibration signal. It involves several steps:
- Fourier Transform: The vibration signal is first transformed into the Fourier domain to obtain the Fourier spectrum data.
- Envelope Calculation: The OSF is applied to the Fourier spectrum to calculate the envelope, which helps to highlight the fault-related components.
- Smoothing and Optimization: The envelope spectrum is smoothed using a moving average method to remove the first-order non-differentiable data and obtain a more accurate envelope array. This process improves the quality of the envelope spectrum and reduces the influence of noise.
- Boundary Determination: The number of divisions (K) and the maximum and minimum value points in the smoothed envelope spectrum are determined. K maximum values are selected, and the boundaries are set at the minimum value positions adjacent to the maximum values. This ensures that the frequency bands with significant impact components are properly selected.
- Normalization and EWT Reconstruction: The boundaries are normalized, and the Meyer wavelet is used to establish the basis function. The Empirical Wavelet Transform (EWT) is then applied to reconstruct the boundary signal, achieving the adaptive segmentation of the spectrum.
3.3 Comparison with Other Methods
Compared with traditional methods and some existing advanced techniques, the proposed improved OSF method offers several advantages. For example, compared to the adaptive Autogram method, it can better detect the fault characteristic frequencies and is less affected by interference components. In contrast to the filter fast spectral kurtosis method, it shows superior performance in identifying the optimal demodulation band.
4. Experimental Setup and Data Acquisition
To evaluate the effectiveness of the proposed method, an experimental setup was designed, and vibration data was collected from an RV gearbox with a fault.
4.1 Experimental Platform
A self-made RV gearbox test platform was used, as shown in Figure 1. The RV gearbox selected was of the 6206 – 2RS1SKF type, with 9 rollers, an inner diameter of 30 mm, and an outer diameter of 62 mm. The gearbox was machined using wire cutting technology.
4.2 Fault Simulation and Data Collection
A fault with a depth of 0.4 mm was simulated on the inner ring of the RV gearbox. During the test, a load of 5 kN was applied, and the rotational speed was maintained at 300 r/min. The vibration signal was sampled at a frequency of 8150 Hz. The time-domain waveform of the measured signal is shown in Figure 2.
5. Results and Analysis
The collected vibration data was analyzed using the proposed improved OSF method, and the results were compared with those of other methods.
5.1 Filtered and Unfiltered Signal Analysis
Figure 3 shows the envelope spectrum of the measured signal before filtering. It can be observed that a significant fault feature is present at the fundamental frequency (fi), while the other harmonic frequencies are submerged in the surrounding components, making accurate diagnosis difficult. In contrast, after applying the improved OSF filtering, the envelope spectrum in Figure 4 clearly shows the fault feature at the fundamental frequency, and the interference components are significantly reduced.
5.2 Comparison with Adaptive Autogram Method
When compared with the adaptive Autogram method, the proposed method shows better performance in detecting the fault characteristic frequencies. The adaptive Autogram method fails to form distinct characteristic frequencies at the double and triple frequencies, and is affected by more interference components.
5.3 Comparison with Filter Fast Spectral Kurtosis Method
The proposed method also outperforms the filter fast spectral kurtosis method. The filter fast spectral kurtosis method generates a large amount of interference signal at the double frequency (2fi), while the proposed method can effectively identify the optimal demodulation band and provide more accurate fault diagnosis results.
6. Discussion
The results obtained from the experiments demonstrate the effectiveness and superiority of the proposed improved OSF method for RV gearbox early fault identification.
6.1 Advantages of the Proposed Method
The method can accurately detect the fault characteristic frequencies, even in the presence of noise and interference. It provides a more reliable and efficient way to identify the early faults of RV gearboxes, which is crucial for timely maintenance and preventing further damage to the industrial robot.
6.2 Limitations and Future Research Directions
Although the proposed method shows good performance, it still has some limitations. For example, in the case of heavy loads, the calculation process may become time-consuming. Future research can focus on further optimizing the algorithm to reduce the computational complexity. Additionally, the integration of deep learning algorithms can be explored to improve the fault diagnosis accuracy and generalization ability.
6.3 Impact on Industrial Robot Maintenance and Operation
The accurate and early fault identification of RV gearboxes using the proposed method can significantly improve the maintenance efficiency of industrial robots. By detecting and addressing faults in a timely manner, the downtime of the robot can be reduced, and the production efficiency and product quality can be enhanced.
7. Conclusion
In this study, an improved OSF method based on adaptive Autogram was proposed for the early fault identification of RV gearboxes in industrial robots.
7.1 Summary of the Research Findings
The experimental results showed that the proposed method can effectively detect the fault characteristic frequencies and outperform the adaptive Autogram and filter fast spectral kurtosis methods. It provides a valuable tool for improving the fault diagnosis capabilities of RV gearboxes.
7.2 Significance of the Research
This research contributes to the improvement of the reliability and performance of industrial robots. By accurately identifying the early faults of RV gearboxes, it helps to reduce maintenance costs, increase production efficiency, and enhance the competitiveness of industrial manufacturing.
7.3 Future Prospects
Future research can focus on further enhancing the proposed method and exploring its application in other mechanical transmission systems. The combination of different diagnostic techniques and the use of advanced machine learning algorithms hold great potential for improving the fault diagnosis accuracy and efficiency.
In conclusion, the proposed improved OSF method has shown great promise in the field of RV gearbox fault diagnosis, and further research and development in this area will have a significant impact on the future of industrial automation.
Method | Advantage | Disadvantage |
---|---|---|
Traditional Methods | Widely used, some basic fault detection ability | Limited in handling complex faults and early detection |
Advanced Signal Processing Techniques (e.g., wavelet transform) | Good at handling non-stationary signals | May require complex parameter tuning |
Adaptive Autogram | Can detect fault bands to some extent | Affected by interference, not very accurate in some cases |
Filter Fast Spectral Kurtosis | Sensitive to impulsive components | Produces interference at certain frequencies |
Proposed Improved OSF Method | Accurate fault frequency detection, better performance | May be computationally intensive under heavy loads |
7.3.1 Optimization of the Proposed Method
- Algorithm Efficiency Improvement: Focus on reducing the computational complexity of the improved OSF method, especially when dealing with heavy loads. This could involve exploring more efficient data processing techniques and algorithms, such as parallel computing or optimized search algorithms for boundary determination.
- Adaptive Parameter Tuning: Develop strategies for automatically tuning the parameters of the method based on the characteristics of the vibration signals. This would enhance the adaptability of the method to different operating conditions and fault types, further improving its accuracy and reliability.
7.3.2 Integration of Deep Learning
- Deep Neural Network for Fault Classification: Incorporate deep learning algorithms, such as convolutional neural networks (CNNs) or recurrent neural networks (RNNs), to classify different fault patterns. The deep neural network can learn complex relationships between the vibration signal features and fault types, potentially improving the accuracy of fault diagnosis.
- Hybrid Models: Combine the improved OSF method with deep learning models to leverage the strengths of both. For example, the OSF method can be used for preprocessing the vibration signals to extract key features, and then these features can be fed into a deep learning model for final fault classification and prediction.
7.3.3 Multi-Sensor Fusion
- Data Fusion Strategies: Integrate data from multiple sensors, such as vibration sensors, temperature sensors, and acoustic emission sensors. Develop effective data fusion strategies to combine the information from different sensors and provide a more comprehensive view of the gearbox’s health status.
- Feature Level Fusion: Explore feature level fusion techniques where the features extracted from different sensors are combined before the fault diagnosis process. This can help to capture complementary information and improve the diagnostic performance.
7.3.4 Online Monitoring and Predictive Maintenance
- Real-Time Monitoring System: Implement an online monitoring system that continuously collects and analyzes the vibration data of the RV gearbox. The proposed improved OSF method can be integrated into this system to provide real-time fault diagnosis and alerts.
- Predictive Maintenance Models: Develop predictive maintenance models based on the historical vibration data and fault patterns. These models can predict the remaining useful life of the gearbox and schedule maintenance activities in advance, reducing unplanned downtime and improving the overall productivity of the industrial robot.
7.3.5 Application to Other Mechanical Systems
- Generalization to Different Gearboxes: Adapt and validate the proposed method for other types of gearboxes used in various industrial applications. This would involve studying the differences in the vibration characteristics and fault mechanisms of different gearboxes and modifying the method accordingly.
- Extension to Other Mechanical Components: Explore the possibility of extending the fault diagnosis approach to other critical mechanical components in industrial robots and machinery, such as bearings, shafts, and couplings. This could lead to the development of a comprehensive condition monitoring and fault diagnosis system for the entire mechanical system.
In summary, the future of RV gearbox fault diagnosis holds great potential for further advancements. By continuously improving the proposed method, integrating advanced technologies, and expanding its application scope, we can enhance the reliability and performance of industrial robots and other mechanical systems, leading to more efficient and sustainable industrial operations.
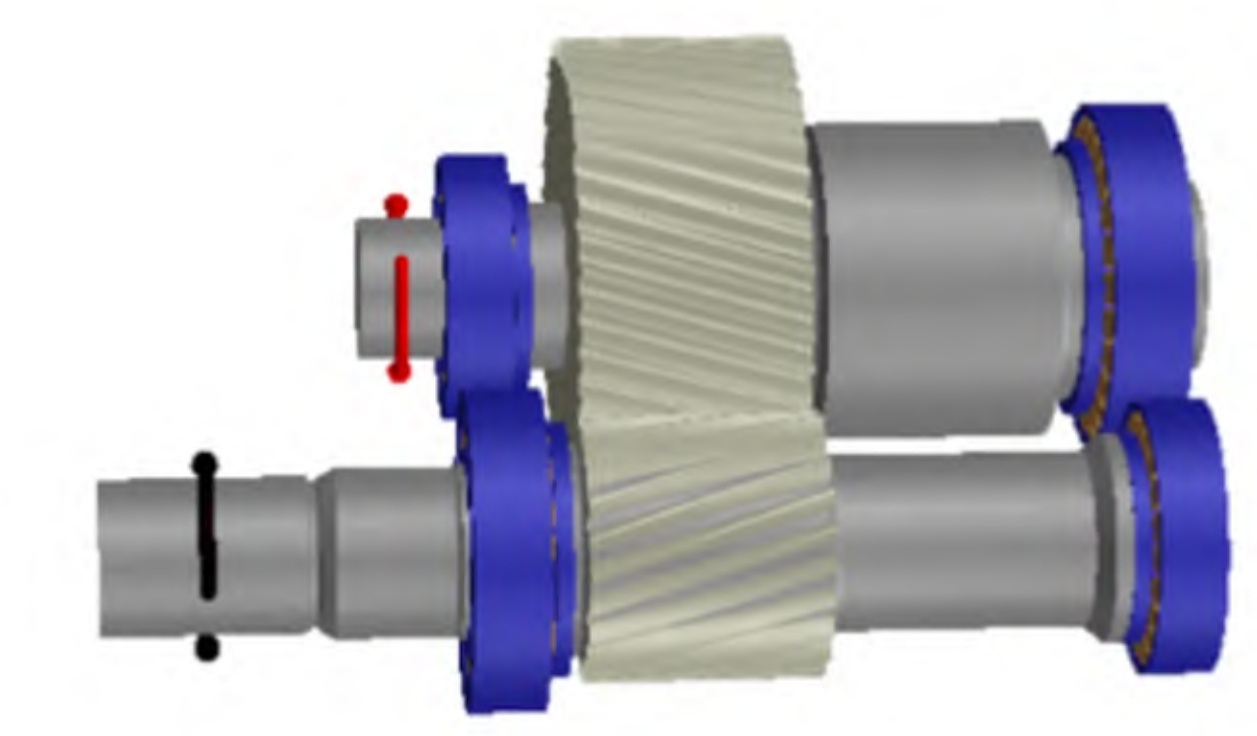