Abstract
This paper presents a comprehensive analysis of the evolution of meshing parameters of a hypoid gear drive under varying loads. Using loaded tooth contact analysis (LTCA), parameters such as equivalent meshing force, loaded transmission error, comprehensive elastic deformation, time-varying meshing stiffness, and actual contact ratio were obtained. The results provide insights into the dynamic meshing characteristics and behavior of hypoid gear systems under different operating conditions.
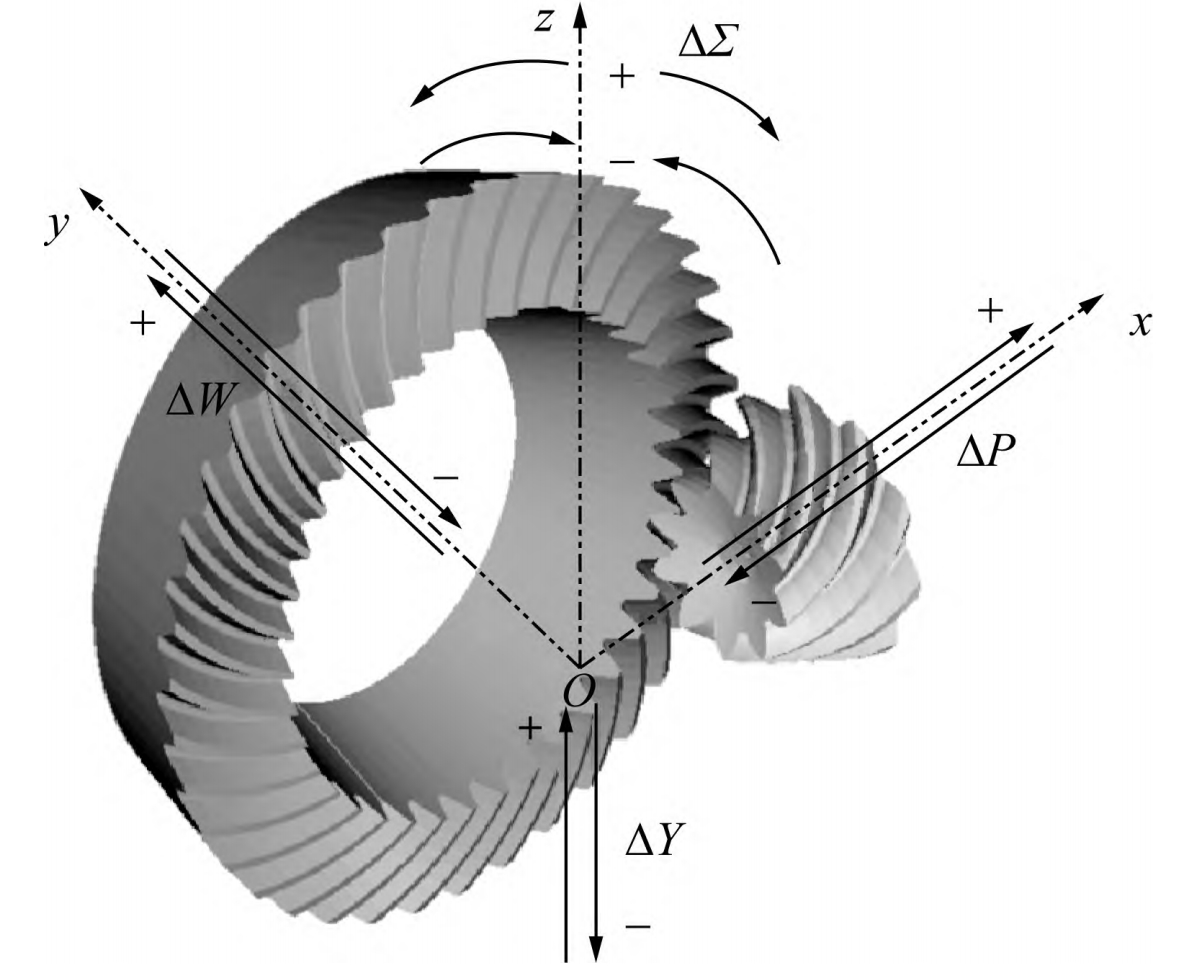
1. Introduction
Hypoid gears are characterized by their complex tooth surface geometry, which makes it difficult to calculate tooth stress and strain using analytical methods such as the Ishikawa formula or Weber’s energy method. Experimental measurements using methods like photoelasticity also face challenges. Finite element analysis (FEA) is currently the primary technique for calculating load-bearing meshing parameters.
2. Mathematical Description of Time-Varying Meshing Parameters
Table 1. Mathematical Representation of Key Meshing Parameters
Parameter | Description | Mathematical Expression |
---|---|---|
Equivalent Meshing Force (F→Q) | Resultant force vector of instantaneous equivalent meshing forces on all contact tooth surfaces | F→Q = (Fx, Fy, Fz) = ∑q i=1 (fix, fiy, fiz) |
Equivalent Meshing Point (R→Q) | Position of the resultant force based on force balance | xQ, yQ, zQ calculated using force and torque balance equations |
Transmission Error (δ(φ1)) | Difference between actual and theoretical angle of rotation of the large gear | δ(φ1) = (φ2 – φ02) – (z1/z2)(φ1 – φ01) |
Comprehensive Elastic Deformation (un(t)) | Sum of contact, bending, and shear deformations | un(t) = ∑ deformations |
Time-Varying Meshing Stiffness (kn(t)) | Ratio of equivalent meshing force to comprehensive elastic deformation | kn(t) = F→Q(t) / un(t) |
3. LTCA Analysis
Table 2. Gear Pair Design and Manufacturing Parameters
Parameter | Value |
---|---|
Geometry Parameters (example) | See text for details |
Machining Parameters (example) | See text for details |
Table 3. FEA Preferences
Parameter | Value |
---|---|
Elastic Modulus (MPa) | 2.09 × 10^5 |
Density (kg/m³) | 7.85 × 10^3 |
Poisson’s Ratio | 0.3 |
Friction Coefficient | 0.1 |
Contact Property | Hard Contact |
Element Type | C3D8R |
Analysis Type | Implicit, Static |
Load Steps for Convergence | See text for details |
4. Results and Analysis
4.1 Contact Patterns Comparison
4.2 Equivalent Meshing Points
4.3 Time-Varying Meshing Parameters
Table 4. Evolution of Meshing Parameters Under Different Loads
Load (N·m) | Contact Pattern Evolution | Equivalent Meshing Force Variation | Transmission Error Trend | Actual Contact Ratio Change | Comprehensive Elastic Deformation | Time-Varying Meshing Stiffness |
---|---|---|---|---|---|---|
100-6000 | Expands from middle to full tooth surface | Proportional to load increase | Decreases then increases | Increases then flattens | Increases with load | Varies non-symmetrically with load |
4.4 Evolution Analysis of Meshing Parameters
- Contact Patterns: Contact areas gradually expand across the tooth surface as load increases.
- Equivalent Meshing Force: Increases proportionally with load torque.
- Transmission Error: Shows a trend of “decreasing then increasing” due to the shift of contact areas relative to ideal contact zones.
- Contact Force and Actual Contact Ratio: Single tooth contact force rises with load; actual contact ratio increases significantly at lower loads then flattens.
- Comprehensive Elastic Deformation and Time-Varying Meshing Stiffness: Both increase with load, with stiffness exhibiting non-symmetrical characteristics.
5. Conclusion
The analysis provides a detailed understanding of how meshing parameters evolve under changing loads in hypoid gear drives. The obtained time-varying meshing parameters accurately reflect the meshing features of the hypoid gear drive under different loads, supporting the analysis of dynamic meshing characteristics and behavior of hypoid gear systems.