Hypoid gear is critical components in automotive, aerospace, and industrial applications due to their unique geometry and ability to handle high torque loads. Ensuring the quality and precision of hypoid gear is paramount to their performance and longevity. State-of-the-art inspection methods play a crucial role in maintaining high standards of gear manufacturing. This article explores various advanced inspection techniques used for quality control of hypoid gear, emphasizing their importance in the manufacturing process.
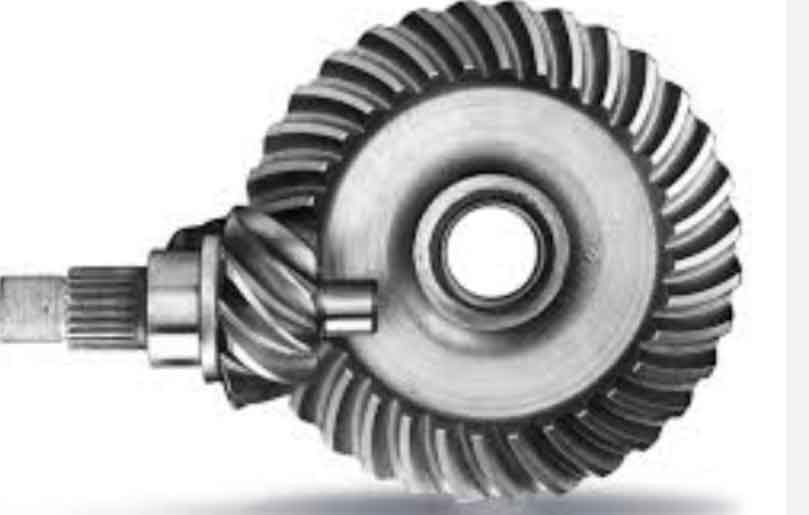
Introduction
Quality control in hypoid gear manufacturing involves rigorous inspection methods to detect defects, ensure dimensional accuracy, and maintain surface integrity. Traditional inspection methods, while effective, may not always meet the precision and efficiency required by modern manufacturing standards. Advanced inspection techniques provide enhanced accuracy, speed, and reliability, thereby improving the overall quality of hypoid gear.
Advanced Inspection Techniques
1. Coordinate Measuring Machines (CMM)
Coordinate Measuring Machines (CMM) are widely used for precision measurement of hypoid gear. CMMs use a probe to measure the coordinates of points on the hypoid gear surface, providing detailed dimensional data.
- Advantages:
- High precision and accuracy
- Ability to measure complex geometries
- Automated and repeatable measurements
- Disadvantages:
- High cost
- Requires skilled operators
- Time-consuming for large batch inspections
2. Gear Measuring Machines (GMM)
Gear Measuring Machines (GMM) are specialized devices designed specifically for measuring gears. They provide detailed analysis of hypoid gear parameters such as pitch, profile, helix, and lead.
- Advantages:
- Highly accurate gear-specific measurements
- Fast and efficient for hypoid gear inspection
- Capable of measuring a wide range of hypoid gear types
- Disadvantages:
- Expensive equipment
- Limited to hypoid gear measurements
3. Surface Roughness Measurement
Surface roughness measurement is critical for assessing the surface finish of hypoid gear, which directly impacts their performance and fatigue life. Techniques such as contact profilometry and non-contact optical methods are commonly used.
- Advantages:
- Accurate assessment of surface finish
- Non-contact methods reduce risk of damage
- Disadvantages:
- Contact methods may wear out over time
- Optical methods can be sensitive to surface conditions
4. Non-Destructive Testing (NDT)
Non-Destructive Testing (NDT) methods, such as ultrasonic testing, magnetic particle inspection, and X-ray radiography, are used to detect internal and surface defects without damaging hypoid gear.
- Advantages:
- Detects subsurface and internal defects
- Maintains gear integrity
- Provides detailed defect characterization
- Disadvantages:
- Requires specialized equipment and expertise
- Some methods may be time-consuming
5. 3D Scanning
3D scanning technologies, such as laser scanning and structured light scanning, create detailed 3D models of hypoid gear for comprehensive inspection and reverse engineering.
- Advantages:
- Rapid and detailed measurements
- Non-contact and non-invasive
- Capable of capturing complex geometries
- Disadvantages:
- High initial investment
- Data processing can be complex
Comparative Analysis of Inspection Techniques
Inspection Technique | Advantages | Disadvantages |
---|---|---|
CMM | High precision, complex geometries | High cost, skilled operators needed |
GMM | Accurate gear-specific measurements | Expensive, limited to gear measurements |
Surface Roughness Measurement | Accurate surface finish assessment | Contact methods wear out, optical methods sensitive to conditions |
Non-Destructive Testing (NDT) | Detects subsurface and internal defects | Specialized equipment and expertise required |
3D Scanning | Rapid, detailed, non-contact | High initial investment, complex data processing |
Key Factors in Inspection Method Selection
- Precision Requirements: The required level of precision and accuracy determines the choice of inspection method.
- Gear Complexity: Complex geometries may necessitate advanced techniques like 3D scanning or CMM.
- Production Volume: High-volume production may benefit from faster methods like GMM and non-contact surface roughness measurement.
- Defect Detection Needs: The need to detect internal or subsurface defects influences the use of NDT methods.
- Cost Considerations: Budget constraints may affect the feasibility of expensive techniques like CMM and 3D scanning.
Future Directions in Hypoid Gear Inspection
- Integration of AI and Machine Learning:
- AI and machine learning can enhance inspection processes by automating defect detection and improving measurement accuracy.
- Predictive analytics can be used to anticipate potential defects and maintenance needs.
- Real-Time Inspection Systems:
- Real-time inspection systems integrated into production lines can provide immediate feedback, reducing the occurrence of defects and improving overall quality control.
- Advanced Sensor Technologies:
- The development of advanced sensors, including high-resolution cameras and multi-spectral imaging, will enhance the capability of inspection systems to detect minute defects and irregularities.
- Sustainable Inspection Practices:
- Eco-friendly inspection technologies that minimize waste and energy consumption are becoming increasingly important in sustainable manufacturing practices.
Conclusion
State-of-the-art inspection methods are essential for ensuring the quality and reliability of hypoid gear. Advanced techniques such as CMM, GMM, surface roughness measurement, NDT, and 3D scanning provide the precision and efficiency required to meet modern manufacturing standards. As technology continues to evolve, the integration of AI, real-time inspection systems, and advanced sensors will further enhance the effectiveness of quality control processes in hypoid gear manufacturing.