Introduction
Helical gears, due to their structural compactness and high transmission efficiency, are widely used in various industrial applications such as aerospace, automotive, and marine industries. However, misalignment errors, including angular misalignment, are common installation issues in gearboxes that can significantly impact the performance and reliability of gear transmission systems. These errors can lead to excessive local stresses, increased vibration and noise, and accelerated wear of gear teeth. Therefore, accurately predicting and analyzing the effects of angular misalignment on helical gear meshing stiffness is crucial for the design and maintenance of gear systems.
In this article, an iterative model of helical gear meshing stiffness considering angular misalignment error is proposed. The model incorporates the axial bending stiffness and torsional stiffness induced by the misalignment, providing a more comprehensive understanding of the meshing behavior under misalignment conditions. Through this model, the effects of different misalignment parameters and loads on the meshing stiffness are studied, offering valuable insights into the dynamic characteristics of helical gear with angular misalignment.
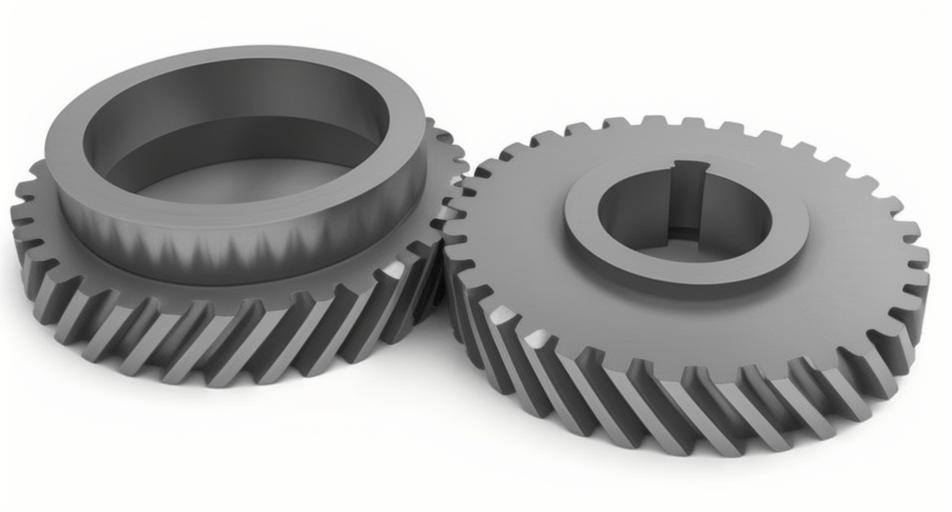
1. Overview of Angular Misalignment Error
Angular misalignment error in gear systems can be classified into two main types: misalignment along the meshing line direction and misalignment perpendicular to the meshing line direction. This error causes the gear axes to deviate from their ideal alignment, resulting in changes in the contact pattern and load distribution between the teeth.
1.1 Angular Misalignment Definitions
- Misalignment along the Meshing Plane (θPOA): This type of misalignment results in a deviation of the gear axis in the plane formed by the gear teeth and the rotation axis. The angle of deviation (θPOA) can be expressed as:thetaPOA=arctan(tan(θy)sinαn+tan(θx)cosαn)where αn is the normal pressure angle, θx and θy are the deviations around the x-axis and y-axis, respectively.
- Misalignment Perpendicular to the Meshing Plane (θOPOA): This type of misalignment causes the gear axis to deviate perpendicularly to the plane formed by the gear teeth and the rotation axis. The angle of deviation (θOPOA) can be defined as:thetaOPOA=arctan(tan(θy)cosαn+tan(θx)sinαn)
1.2 Effects of Angular Misalignment on Contact Pattern
Angular misalignment significantly affects the contact pattern between the gear teeth. For misalignment along the meshing plane, the contact trajectory changes from line contact to point contact, with evident edge contacts during meshing-in and meshing-out phases. For misalignment perpendicular to the meshing plane, the contact region may tilt, although slight tilts have minimal impact on the contact area.
2. Proposed Iterative Model for Meshing Stiffness
The proposed model for calculating the meshing stiffness of helical gear under angular misalignment error is based on the slicing method, which divides the helical gear into thin slices along the tooth width. The model considers both the transverse meshing stiffness caused by the transverse meshing force and the axial meshing stiffness caused by the axial meshing force.
2.1 Transverse Meshing Stiffness
The transverse meshing force (( F_t )) can be calculated using the slicing method, where each slice is modeled as a cantilever beam. The transverse meshing stiffness (( k_t )) comprises five components: Hertzian contact stiffness (( k_h )), bending stiffness (( k_b )), shear stiffness (( k_s )), axial compression stiffness (( k_a )), and foundation stiffness (( k_f )).
The transverse meshing force can be expressed as:
Ft=Fcosβb′
where βb′ is the helix angle adjusted for misalignment.
The individual stiffness components are calculated using equations derived from beam theory and Hertzian contact theory, as summarized in Table 1.
Component | Formula |
---|---|
Hertzian Contact Stiffness (( k_h )) | kh=4(1−ν2)πEL(LF)0.1 |
Bending Stiffness (( k_b )) | kb=∑i=1N∫−α1′α212Ebh3(sinα+(α2−α)cosα)3dα |
Shear Stiffness (( k_s )) | ks=∑i=1N∫−α1′α22(1+ν)1.2Eb(α2−α)hdα |
Axial Compression Stiffness (( k_a )) | ka=∑i=1N∫−α1′α2Ebh(α2−α)cos2αdα |
Foundation Stiffness (( k_f )) | kf1=EWL∗(ufSf)2+M∗ufSf+P∗(1+Q∗tan2α1′)cos2βb′cos2α1′ |
Table 1: Formulas for transverse meshing stiffness components.
2.2 Axial Meshing Stiffness
The axial meshing force (( F_a )) induced by angular misalignment causes additional bending and torsional stiffness. The axial meshing stiffness (( k_a )) is derived based on the cantilever beam model, considering both bending and torsion:
Fa=Fsinβb′
The bending stiffness (( k_{ab} )) and torsional stiffness (( k_{at} )) components are:
kab=12lEbh3andkat=lGJ
where E is the Young’s modulus, G is the shear modulus, b is the slice width, h is the slice thickness, l is the slice length, and J is the polar moment of inertia.
2.3 Coupling Effect between Slices
The angular misalignment leads to uneven load distribution along the tooth width, resulting in coupling effects between slices. The coupling stiffness (k_{ci} \)) between slices \( i and i+1 is given by:
kci=Cc⋅ktikt(i+1)⋅Δl
where Cc is the coupling coefficient and Δl is the slice thickness.
3. Model Validation
To validate the proposed model, a finite element analysis (FEA) was conducted using a helical gear model with defined misalignment parameters. The gear parameters used for simulation are summarized in Table 2.
Parameter | Value |
---|---|
Number of teeth (active) | 18 |
Number of teeth (passive) | 81 |
Module (mm) | 3.5 |
Face width (mm) | 65 |
Pressure angle (°) | 20 |
Helix angle (°) | 15 |
Addendum coefficient | 1.0 |
Dedendum coefficient | 0.25 |
Young’s modulus (Pa) | 2.06 × 10^11 |
Poisson’s ratio | 0.3 |
Table 2: Gear parameters for FEA validation.
The FEA model, was subjected to a torque of 50 Nm applied to the active gear while fixing the passive gear. The resulting meshing stiffness was compared with the results from the proposed model and a traditional model.
The meshing stiffness obtained from the proposed model, traditional model, and FEA. The proposed model shows better agreement with the FEA results, with a maximum error of 2.2% compared to 3.7% for the traditional model.
4. Results and Discussion
4.1 Effects of Angular Misalignment Direction
The effects of angular misalignment in the x-direction, y-direction, and a combined direction (θPOA and θOPOA) on meshing stiffness were studied.The variation in meshing stiffness with increasing misalignment angles from 0.01° to 0.05°.
As misalignment increases, the meshing stiffness decreases significantly due to the reduction in contact area. Table 3 summarizes the average reduction in meshing stiffness for different misalignment angles and directions.
Angle (°) | x-direction Reduction (%) | y-direction Reduction (%) | Combined Direction Reduction (%) |
---|---|---|---|
0.01 | 75.80 | 60.09 | 79.38 |
0.02 | 82.95 | 71.88 | 85.45 |
0.03 | 86.07 | 77.14 | 88.13 |
0.04 | 87.95 | 80.27 | 89.73 |
0.05 | 89.20 | 82.32 | 90.80 |
Table 3: Average reduction in meshing stiffness with angular misalignment.
4.2 Effects of Load
The influence of load on meshing stiffness under angular misalignment was also investigated. the variation in meshing stiffness with increasing loads from 50 Nm to 250 Nm for a 0.05° misalignment in different directions.
As the load increases, the meshing stiffness gradually improves due to the increase in contact area between the teeth. However, the improvement rate decreases with further increases in load. Table 4 summarizes the average reduction in meshing stiffness under different loads and misalignment directions.
Load (Nm) | x-direction Reduction (%) | y-direction Reduction (%) | Combined Direction Reduction (%) |
---|---|---|---|
50 | 89.20 | 82.32 | 90.80 |
100 | 84.73 | 75.09 | 87.05 |
150 | 81.34 | 69.46 | 84.11 |
200 | 78.48 | 64.82 | 81.69 |
250 | 75.98 | 60.63 | 79.55 |
Table 4: Average reduction in meshing stiffness with varying loads under angular misalignment.
5. Conclusion
In this study, an iterative model for calculating the meshing stiffness of helical gear considering angular misalignment error was proposed. The model integrates both transverse and axial meshing stiffness components, accounting for the effects of misalignment-induced axial bending and torsional stiffness. Validation through finite element analysis demonstrated the model’s accuracy, outperforming traditional methods.
The analysis revealed that angular misalignment significantly decreases meshing stiffness, with a more pronounced effect in the x-direction compared to the y-direction. Additionally, increasing the load partially mitigates the negative effects of misalignment on meshing stiffness, though the improvement tapers off at higher loads.
The findings of this study provide valuable insights into the dynamic behavior of helical gear under angular misalignment conditions. The proposed model can serve as a reliable tool for predicting and analyzing gear system performance, aiding in the design and maintenance of more robust and efficient gear transmissions.