Spiral bevel gears have high coincidence, strong load-carrying capacity, high transmission ratio, and high transmission efficiency, and are widely used in the fields of automobiles, aviation, and mining machinery. The manufacturing accuracy of spiral bevel gears is directly related to the errors of CNC machine tools. Machine tool errors include geometric errors, thermal errors, and servo control errors. Among them, machine tool geometric errors are repetitive and stable, and can be accurately compensated through the CNC system. Therefore, studying the characteristics of machine tool geometric errors and determining the key geometric error items is important for tooth surface deviation compensation and the allocation and maintenance of machine tool motion accuracy.
1. Introduction
Spiral bevel gears are widely used in various fields due to their excellent performance. However, the tooth surface of spiral bevel gears is complex, and the manufacturing accuracy is easily affected by the geometric errors of the machine tool. Therefore, it is crucial to study the relationship between machine tool geometric errors and tooth surface deviations.
Sensitivity analysis is an important method to study this relationship. It can determine the key input factors that have a significant impact on the output results. By identifying these key factors, we can focus on optimizing and controlling them to improve the manufacturing accuracy of spiral bevel gears.
Currently, there are many sensitivity analysis methods, but the selection of an appropriate method is essential due to the complexity of the tooth surface of spiral bevel gears and the numerous factors affecting the machining accuracy.
2. Sensitivity Analysis Methods
2.1 Local Sensitivity Analysis Method
Local sensitivity analysis is a single-factor analysis method. It involves making a small change to a single input factor at a time while keeping all other factors constant. The sensitivity coefficient is determined based on the differential of the output result with respect to the input parameter or the change in the output result caused by the change in a single input factor. This method is conceptually clear and computationally simple, mainly suitable for linear models and models with weak nonlinearity. The analysis process is as follows:
- Start by inputting the change amount of the first parameter.
- Calculate the theoretical output result and the actual output result.
- Calculate the deviation value.
- Increment the parameter index (i = i + 1).
- Repeat the above steps until all parameters are processed.
- Output all deviation values.
- End the analysis.
2.2 Sobol Global Sensitivity Analysis
The global sensitivity analysis method takes into account the range and distribution law of each parameter. During the analysis and calculation, all parameters are substituted into the model for analysis, considering the influence of the coupling between input parameters on the results. However, this method usually requires a certain scale of sampling to obtain the input parameters of the model and then perform the sensitivity analysis. Especially for models with many parameters, the computational cost can be relatively large.
Taking the Sobol method as an example, it is a global sensitivity method based on variance. This method mainly calculates the sensitivity coefficient of the input parameters by decomposing the variance of the model into sub-items.
Suppose n represents the number of input parameters of the model, and xi represents the ith input parameter (i = 1, 2,…, n). Let K = f(X) represent the multivariate function corresponding to the model, where X = (x1, x2,…, xn). Then, f(X) can be decomposed as follows:
f(X) = f0 + ∑i=1n fi(xi) + ∑i<jn fi,j(xi, xj) +… + f1,…,n(x1, x2,…, xn)
Here, f0 is the expected value of the output result f(X) calculated from the input parameters, which is a constant. fi(xi) represents the output result when the input parameter xi acts alone, fi,j(xi, xj) represents the output result when the input parameters xi and xj act together, and f1,…,n(x1, x2,…, xn) represents the output result when all input parameters act together. The same applies to other orders.
The total variance D can be expressed as:
D = ∫01…∫01 f2(X)dX – f02
The variance components can be obtained as follows:
Di1,…,is = ∫01…∫01 fi1,…,is2(xi1,…, xis)dxi1…dxis (where 1 ≤ s ≤ n)
By squaring and integrating both sides of equation (1) using the Sobol method, we get:
D = ∑i=1n Di + ∑i<jn Di,j +… + D1,2,…,n
The sensitivity coefficient can be calculated using the following formula:
Si1,…,is = Di1,…,is / D
Since the variance is non-negative, Si1,…,is is also non-negative. According to equations (4) and (5), we have:
∑i=1n Si + ∑i<jn Si,j +… + S1,2,…,n = 1
Here, Si is the first-order sensitivity coefficient corresponding to the variable xi, and Si,j (i < j) is the second-order sensitivity coefficient corresponding to the mutual coupling effect of the variables xi and xj. Similarly, the sensitivity coefficient of each order can be obtained. The global sensitivity coefficient Stoti corresponding to the variable xi can be obtained by summing the sensitivity coefficients related to the variable xi, and the calculation method is as follows:
Stoti = Si + ∑i=kn Si,k +… + S1,2,…,n (where the positive integer k takes values in the range 1 ≤ k ≤ n, and k ≠ i)
2.3 Monte Carlo Estimation
In the process of solving the sensitivity coefficient using the Sobol method, it often involves the solution of multiple integrals, which is usually very difficult for complex models. Therefore, the Monte Carlo method is often used to approximately simulate the solution of multiple integrals. The general calculation method is as follows:
Perform two independent samplings on the input parameters to obtain two independent sampling matrices E and F, as follows:
E = [x11 x12… x1n
x21 x22… x2n
…
xk1 xk2… xkn]
F = [x11′ x12’… x1n’
x21′ x22’… x2n’
…
xk1′ xk2’… xkn’]
Here, k is the number of samples for each sampling.
To solve the first-order sensitivity coefficient and the global sensitivity coefficient, based on the matrices E and F, the matrix Er’ is constructed (where i = 1, 2,…, n). The matrix Er is obtained by replacing the ith column of the matrix E with the ith column of the matrix F, and the rest is exactly the same as the matrix E. The matrix Er can be expressed as follows:
Er = [x11 x12… x1i’… x1n
x21 x22… x2i’… x2n
…
xk1 xk2… xki’… xkn]
Therefore, each row of input parameters can separately solve for one model output result. The first-order sensitivity coefficient S and the global sensitivity coefficient Si− can be approximately calculated using the following formulas:
Si = (1/k) ∑h=1k f(F)h (f(Er)k – f(E)k) / D
Si− ≈ (1/2k) ∑h=1k (f(E)h – f(Er)h)2 / D
Here, f(E)h is the output result obtained by substituting the hth row of the matrix E into the model, f(F)h is the output result obtained by substituting the hth row of the matrix F into the model, and f(Er)h is the output result obtained by substituting the hth row of the matrix Er into the model. D is the total variance of the calculation model.
3. Spiral Bevel Gear Machine Tool Processing Model
3.1 Classification of Machine Tool Geometric Errors
The structure of the spiral bevel gear CNC machine tool is shown in Figure 2. According to the set CNC program, the axes A, B, X, Y, and Z move in a coordinated manner to machine the spiral bevel gear in the Gleason system. The c-axis drives the cutter head to rotate and does not affect the tooth surface generation process. The coordinate transformation relationship of the machine tool is shown in Figure 3.
For the five motion axes related to the generation of the tooth surface, each axis has geometric errors due to manufacturing, assembly, and other factors, which directly lead to the generation of tooth surface deviations. Each axis has 6 geometric errors, including 3 linear errors and 3 angular errors. For the entire machine tool, 30 geometric errors need to be considered [13].
To facilitate analysis, the geometric error sequences are numbered as shown in Table 1. Here, ε represents the angular error, δ represents the linear error, and the error variables are distinguished by two subscripts: the first subscript represents the direction of the error, and the second subscript indicates the axis where the error is located. For example, εay represents the angular error in the α direction of the Y-axis, and εyx represents the linear error in the y direction of the X-axis.
Axis | Geometric Error | Number | ||
---|---|---|---|---|
X | δxx | δxy | δxz | 1 – 3 |
Y | δyx | δyy | δyz | 4 – 6 |
Z | δzx | δzy | δzz | 7 – 9 |
A | εax | εay | εaz | 10 – 12 |
BXYZ | εbx | εby | εbz | 13 – 15 |
εax | εgx | εyx | 16 – 18 | |
εaY | εgy | εyY | 19 – 21 | |
εaZ | εgz | εyz | 22 – 24 | |
εa | εg | εy | 25 – 27 | |
B | εaB | εgB | εyB | 28 – 30 |
3.2 Tooth Surface Machining Process
The generating motion of the workpiece gear is determined by the five axes X, Y, Z, A, and B. Therefore, the homogeneous transformation matrix from the A-axis to the Y-axis combined with the tool equation can obtain the tooth surface equation rB under ideal conditions [14].
rB = MA · MB · MZ · MX · MY · rt(u, θ)
Here, M(q = X, Y, Z, A, B) is the motion transformation matrix corresponding to each axis, rt is the expression obtained from the tool equation, and u and θ are the parameters of the cutter head. Due to space limitations, the specific process can be referred to in literature [15].
If the machine tool geometric errors are considered, the actual tooth surface equation is as follows:
rg = MA · MAe · MB · MBe · MZ · MZe · MX · MXe · MY · MYe · rt(u, θ)
Here, Mq (q = X, Y, Z, A, B) is the geometric error matrix corresponding to each axis.
4. Sensitivity Analysis Example
4.1 Sampling Calculation
Taking the gear shown in Table 2 as an example, the theoretical tooth surface of the spiral bevel gear can be obtained according to equation (13). Considering the influence of the machine tool geometric errors in actual processing, the actual tooth surface of the spiral bevel gear can be calculated according to equation (14).
Parameter | Value |
---|---|
Number of Teeth Z1 | 18 |
Large End Module m/mm | 4.29 |
Tooth Face Width/mm | 45 |
Hand of Helix | Left-handed |
Midpoint Helix Angle/(°) | 35 |
Addendum h/mm | 8.78 |
Dedendum h/mm | 5.03 |
Pitch Cone Angle y/(°) | 27.21 |
Face Cone Angle/(°) | 31.65 |
Root Cone Angle/(°) | 25.36 |
Outer Cone Distance L/mm | 140.9 |
To facilitate analysis and calculation, a discrete 15×9 lattice is used to represent the tooth surface. Combining equations (13) and (14), the theoretical tooth surface lattice and the actual tooth surface lattice can be obtained. By the coordinate values of the corresponding points in the lattice, the deviation value Kf of the corresponding tooth surface point can be solved. Here, f represents the number of the point in the lattice, and K represents the tooth surface deviation, which is the output result of the calculation model and is used to measure the magnitude of the tooth surface deviation. It can be obtained by the following formula:
K = ∑j=113 |Kj|
Given that the change amount of each linear parameter is +0.01 mm and the change amount of each angular parameter is +27″, taking the tooth surface deviation K as the model output result, the local sensitivity analysis result is shown in Figure 4.
[Insert Figure 4 here]
Referring to the change amount of the input parameters in the local sensitivity analysis, the range of the linear error is given as 0 – 10 μm, the range of the angular error is 0″ – 27″, and the geometric error parameters follow a uniform distribution. Write a sampling program to randomly sample within the given range of the geometric errors to generate the machine tool geometric error parameters. Combining equations (13) and (14), the corresponding theoretical tooth surface and actual tooth surface can be calculated. According to the two types of tooth surface lattices, the corresponding tooth surface deviation K can be solved.
Through the Sobol global sensitivity analysis method, the global sensitivity coefficients of the 30 machine tool geometric errors can be solved. Arranging them in descending order according to the magnitude of the global sensitivity coefficients, as shown in Figure 5.
[Insert Figure 5 here]
4.2 Discussion on Input Parameter Situation
When using the local sensitivity analysis method for sensitivity analysis, it is necessary to ensure that the change amount of the input parameters of the same type is the same, so that the output results are comparable. The selection standard is independent of the actual range and distribution law of the input parameters, so changes in the actual input parameter value range will not affect the local sensitivity analysis results.
In the previous text, the selection of the input parameter range for the global sensitivity analysis method referred to the characteristics of the local sensitivity analysis method to ensure that the range and distribution law of the same type of parameters are the same. However, in real situations, the value range of the input parameters is generally not the same, and the change law is often different. Therefore, considering the possible actual situations, taking the geometric error with the number as an example, let the value interval of this geometric error change from 0 – 10 μm to 0 – 20 μm, while keeping other conditions unchanged. The sensitivity analysis result can be obtained as shown in Figure 6.
[Insert Figure 6 here]
It can be found that for the global sensitivity analysis method, after changing the value range of the input parameters, the sensitivity analysis results change significantly. Among them, the global sensitivity coefficient of the geometric error item with the number, that is, δs1, changes significantly, from the original 0.023 to 0.154. The global sensitivity coefficients of other items only have minor changes, and the relevant proportions do not change significantly.
4.3 Result Analysis
By comparing the calculation results of the two sensitivity analysis methods before and after the change in the value range, the following characteristics of the two sensitivity analysis methods for the tooth surface machining deviation calculation model of the spiral bevel gear can be found:
- Under the ideal situation where the value range and distribution law of the input parameters are completely the same, the sensitivity coefficient distribution law of the linear errors obtained by the two sensitivity analysis methods for the tooth surface deviation of the spiral bevel gear is the same. The sensitivity coefficients of the linear error items of each axis all show the trend of y direction (the geometric errors with numbers 2, 5, 8, 11, 14) > x direction (the geometric errors with numbers 1, 4, 7, 10, 13) > z direction (the geometric errors with numbers 3, 6, 9, 12, 15).
- Under the ideal situation where the value range and distribution law of the input parameters are completely the same, the sensitivity coefficient distribution law of the angular errors of each axis obtained by the two sensitivity analysis methods for the tooth surface deviation of the spiral bevel gear, due to the use of different probability calculation formulas and sampling sample limitations, there are small differences, but the overall trend is the same. The key angular errors of each axis are the same (the geometric errors with numbers 17, 18, 19, 20, 23, 26, 29).
- When the value range of the input parameters changes, through the global sensitivity analysis, it can be found that the input parameters of the original non-key geometric errors may change to key geometric errors. However, for the local sensitivity analysis method, its analysis results are independent of the distribution range of the input parameters. When the distribution range of the input parameters is quite different, the accuracy of the analysis results of this method will significantly decrease and may no longer be suitable for the sensitivity analysis of this model.
5. Conclusions
Through applying the two sensitivity analysis methods to the sensitivity analysis of the tooth surface machining deviation model of the spiral bevel gear, the following conclusions can be drawn:
- Under the ideal situation where the value range and distribution law of the input parameters are completely the same, the local sensitivity analysis method has a smaller computational cost and can obtain preliminary analysis results more quickly. At the same time, the distribution law of the analysis results is the same as that of the global sensitivity analysis results, which has certain reference value.
- The Sobol global sensitivity analysis method considers the influence of the value range and distribution law of the input parameters on the analysis results, which is more scientific, and the conclusions obtained are more reliable, and the applicable range is wider. In addition, most global sensitivity analyses
- The Sobol global sensitivity analysis method considers the influence of the value range and distribution law of the input parameters on the analysis results, which is more scientific, and the conclusions obtained are more reliable, and the applicable range is wider. In addition, most global sensitivity analyses can be used to study the quantitative relationship between input parameters and output results and the influence of the interaction between parameters on the output results. However, compared with the local sensitivity analysis method, the computational cost is significantly increased, and more time is required.
- For models with unclear distribution ranges of input parameters, limited available time, and similar or identical distribution situations, whether linear or not strongly nonlinear, the local sensitivity analysis can be considered. For nonlinear models with complex distribution ranges of input parameters and high accuracy requirements, the global sensitivity analysis method can be considered.
- This research provides theoretical guidance for the use of sensitivity analysis methods in the machining of spiral bevel gear tooth surfaces and offers a reference for the selection of sensitivity analysis methods.
- In the future, further studies can be conducted in the following aspects:
- Explore more advanced sensitivity analysis methods and their applications in spiral bevel gear machining to improve the accuracy and reliability of the analysis results.
- Investigate the influence of other factors, such as cutting parameters and tool wear, on the tooth surface deviation of spiral bevel gears and incorporate them into the sensitivity analysis.
- Develop optimization algorithms based on the sensitivity analysis results to effectively reduce the tooth surface deviation and improve the manufacturing quality of spiral bevel gears.
- In conclusion, the sensitivity analysis of the machining deviation of spiral bevel gears is an important research topic. By selecting the appropriate sensitivity analysis method and conducting in-depth studies, we can better understand the relationship between machine tool geometric errors and tooth surface deviations, and provide valuable guidance for improving the manufacturing accuracy of spiral bevel gears.
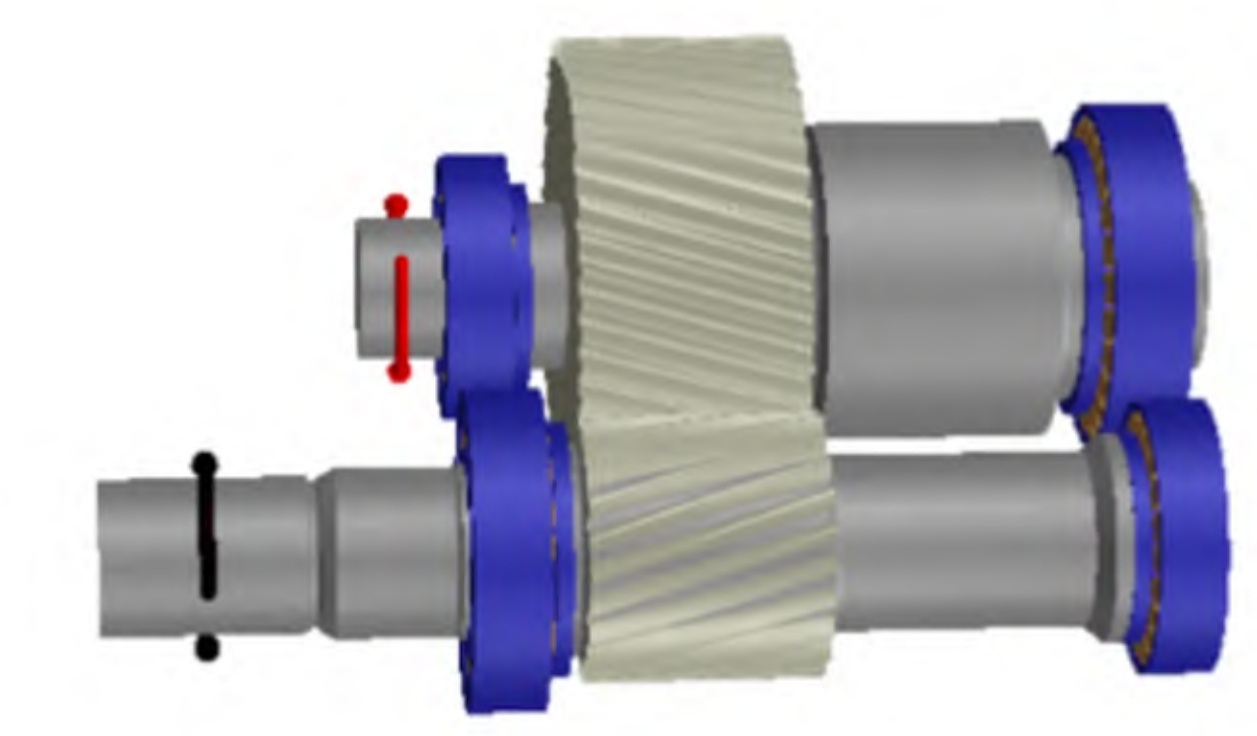