The cylindrical gear flowmeter is a volumetric flow meter with advantages such as small size, high accuracy, good stability, and wide measurement range. It is widely used in various fields such as aviation, aerospace, and chemical industry. However, the internal leakage phenomenon of the cylindrical gear flowmeter has always been a problem that cannot be ignored. Due to the mechanical structure components having a certain gap during assembly, the leakage caused by the assembly gap will make the measured actual flow rate less than the theoretical flow rate. This measurement error will inevitably affect the measurement performance of the cylindrical gear flowmeter. When the assembly gap changes, the flow state of the leakage flow is different, and the impact on the performance of the cylindrical gear flowmeter is also different. Therefore, studying the law of measurement performance of the cylindrical gear flowmeter with changes in assembly gap and reducing its impact on assembly gap has very important theoretical significance and application value for the cylindrical gear flowmeter.
To broaden the application fields of gear flowmeters, reduce their sensitivity to environmental and assembly conditions, and improve measurement accuracy, researchers have conducted extensive research through theoretical calculations, numerical simulations, or real-flow testing. Through experiments, the effects of different viscosity conditions on the performance of elliptical gears
The law of flowmeter performance change. The research results show that the meter factor of the elliptical gear flowmeter tends to increase with the increase of medium viscosity. The cylindrical gear flowmeter was tested under high pressure conditions, and the experimental results showed that the meter performance changes with pressure. However, no further analysis was made on how pressure affects the performance of the cylindrical gear flowmeter. The trend of meter factor change with temperature of the cylindrical gear flowmeter was studied, and the functional relationship between meter factor and temperature of the cylindrical gear flowmeter was obtained through function fitting. However, the mechanism of temperature change causing meter factor change was not analyzed. A mathematical model for clearance leakage of cylindrical gear flowmeter was established, and the model was used to predict the influence of measured oil viscosity change on end clearance leakage and radial clearance leakage. The results showed that when the measured fluid viscosity is high, the prediction results are close to the experimental results; when the measured fluid viscosity is low, the prediction results have large errors.
The research on gear flowmeters in the literature mainly focuses on the impact of changing operating conditions on the macro parameters of the measurement performance of cylindrical gear flowmeters, while there is little analysis of the mechanism of the impact of assembly conditions on the performance of cylindrical gear flowmeters. This article proposes a simulation method based on a 6-DOF model, using
This method conducts CFD simulations on DN16 cylindrical gear flowmeters with different assembly clearances, obtains the law of the influence of assembly clearance changes on the measurement performance of cylindrical gear flowmeters, and analyzes its mechanism using fluid mechanics principles. On this basis, it explores the law of the influence of medium viscosity changes on the measurement performance of cylindrical gear flowmeters, providing guidance for the design, assembly, and application of cylindrical gear flowmeters.
Working principle of cylindrical gear flowmeter
There is a pair of circular cross-section cylindrical gears meshing with each other inside the cylindrical gear flowmeter. When the fluid enters from the inlet, the gears start to rotate under the action of the pressure difference between the fluid inlet and outlet. The gear teeth continuously divide the flowing liquid into multiple independent volume units and send them to the outlet. The volume of each volume unit is v, and the total amount of fluid discharged by the gear rotating once is V. The existence of leakage flow makes the measured flow smaller, which is the main reason affecting the measurement performance of volumetric flowmeter. There are three types of leakage flow inside the cylindrical gear flowmeter as shown in Figure 1. Since the leakage flow at the gear meshing point only accounts for This article mainly analyzes end leakage flow and radial leakage flow.
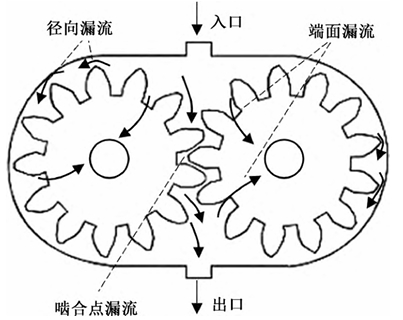
When the force condition changes, the gear adjusts its motion state based on the equation of motion. The gear only rotates around the center under the action of torque, independent of the other five directions. During the simulation process, the degree of freedom of the inner gear of the cylindrical gear flowmeter can be restricted by programming, and the rotational inertia in the direction of gear rotation can be assigned. Under the condition of setting the inlet flow rate, the gear adjusts its speed in real time based on the force condition. This study is based on this method to simulate the motion state of the cylindrical gear flowmeter gear and predict its measurement performance.
Simulation model establishment
The research object is DN16 cylindrical gear flowmeter, and the experimental prototype is shown in the figure. The key dimensions of the experimental prototype are measured and the results are shown in the table As shown in the figure, the flow channel was extracted using the 3D modeling software SolidWorks with reference to the experimental prototype, and a 3D model of the internal flow field of the flowmeter was drawn.
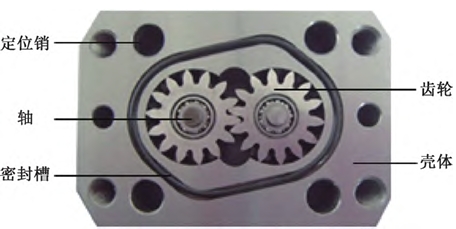
In order to limit the total number of grids without affecting the flow field analysis of key parts, the entire flow field is divided into five parts before grid division: inlet, upper end clearance, lower end clearance, gear and surrounding area, and outlet. Each flow field region and wall surface are named to facilitate the setting of boundary conditions and monitoring of process parameters during the simulation process. The three-dimensional simulation model of the cylindrical gear flowmeter is imported into PumpLinx software, and different grid generation modules are used to generate grids for each region. In order to ensure the accuracy of the solution at the clearance, the grid division at the gear top clearance and gear mesh clearance reaches 18 layers, and the total number of grids in each region is 66w. The grid division result of the three-dimensional simulation flow field of the cylindrical gear flowmeter is shown in the figure.
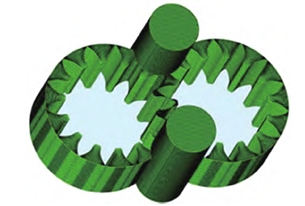
When the clearance of the cylindrical gear flowmeter decreases within a certain range, the leakage flow decreases accordingly. However, as the clearance continues to decrease, the leakage flow increases, with the minimum leakage flow being achieved in model 2. Further estimation of the measurement error caused by leakage in each model shows that the measurement error varies with flow rate. As the clearance of the gear changes, the measurement error also varies with the change in leakage flow, with model 2 having the smallest measurement error, with an average absolute percentage error of 0.32%. To explain the effect of assembly clearance on the measurement performance of cylindrical gear flowmeters, pressure losses at the inlet and outlet of the simulated flow field were extracted. The variation trend of pressure losses is basically consistent with that of leakage flow. When the clearance of the cylindrical gear flowmeter decreases within a certain range, the pressure losses decrease accordingly, resulting in a decrease in leakage flow, that is, an increase in average meter factor. As the clearance continues to decrease, the flow area decreases and the viscous shear force increases. The gear rotation needs to overcome greater resistance, resulting in greater pressure losses. The smaller the clearance, the greater the pressure loss, causing an increase in leakage flow, that is, an increase in average
The instrument factor decreases. Therefore, it can be concluded that the change in pressure loss in the flow field leads to a change in the average instrument factor. Due to the small clearance between the tooth tip circle and the end face, the fluid in the clearance flows in a laminar flow state. In complex flow field environments, due to the viscosity of the fluid, some fluid adheres to the gear surface and rotates with the gear, resulting in a certain deviation between the actual leakage flow and the theoretical leakage flow. This phenomenon causes changes in the linearity error of various models.
Influence of medium viscosity on the performance of cylindrical gear flowmeter
When the cylindrical gear flowmeter is actually applied, it will work at different temperatures, and different temperatures will change the basic properties of the medium, which will affect the accuracy of the cylindrical gear flowmeter.
The biggest factor affecting the leakage flow rate is the viscosity of the medium, which is the kinematic viscosity of YH-15 aviation hydraulic oil under different temperature conditions. The meter factor of the cylindrical gear flowmeter gradually increases with the increase of flow rate. When the viscosity is 22.5 and 7.1 mm2/s, the meter factor first increases and then decreases. This is because when the fluid gradually increases from small flow rate, there is a transition process from laminar flow to turbulence, and at this time, the performance of the flowmeter changes. As the viscosity of the fluid gradually increases, the average meter factor of the cylindrical gear flowmeter shows an upward trend, and the linearity error shows a downward trend. When the viscosity is 42.7 mm2/s, the linearity error of the cylindrical gear flowmeter is the smallest, indicating that the measurement performance of the cylindrical gear flowmeter is less affected by high viscosity fluids. The reason for the change in meter factor of the cylindrical gear flowmeter is mainly due to the different flow states of the fluid under different viscosity conditions, resulting in different leakage flows. Estimating the leakage flow rate of the cylindrical gear flowmeter under different viscosity conditions, the leakage flow rate varies with flow rate under different viscosity conditions.
Conclusion
In order to improve the measurement accuracy of cylindrical gear flowmeters and reduce the impact of assembly clearance on the performance of cylindrical gear flowmeters, this study obtained the rule of variation of the performance of DN16 cylindrical gear flowmeters with assembly clearance through CFD simulation, analyzed the mechanism of the impact of assembly clearance on the measurement performance of cylindrical gear flowmeters, and explored the rule of variation of the performance of cylindrical gear flowmeters with changes in medium viscosity. The following conclusions were drawn:
The trend of the simulation instrument coefficient of the cylindrical gear flowmeter with varying flow rates is consistent with experimental results, verifying the effectiveness of the simulation method based on the six-degree-of-freedom model.
2) The simulation results of different tooth tip clearance and gear end clearance show that as the clearance gradually decreases, the average meter factor and linearity error of the cylindrical gear flowmeter both have a decreasing trend. When the tooth tip clearance is 140 μm and the gear end clearance is 100 μm, the linearity error reaches an optimal value of 0.13%.
3) As the assembly clearance changes, the leakage flow gradually changes, and the measurement error caused by leakage flow also changes. When the tooth tip clearance is 170 μm and the gear end clearance is 130 μm, the measurement error caused by leakage flow is minimal, better than 0.32%;
4) The measurement performance of cylindrical gear flowmeters is affected by changes in medium viscosity. As the viscosity of the fluid gradually increases, the linearity error tends to decrease. When the viscosity is 42.7 mm2/s, the linearity error is minimal, only 0.03%.