Spiral bevel gears are widely used in marine power systems, helicopters, aero engines, and automotive transmission systems due to their advantages of smooth operation, high transmission ratio, high transmission torque, reliable operation, and compact structure. Under long-term heavy-load and variable-load operating conditions, once spiral bevel gears Tooth surface damage can cause equipment vibration and reduce transmission performance at the most basic level, and can lead to equipment damage and even casualties at the most severe level. Therefore, accurately identifying the degree of failure damage of spiral bevel gears, timely grasping the development status of damage failures, and providing effective support for condition-based maintenance are crucial to ensuring the safe and stable operation of spiral bevel gears.
The meshing process of spiral bevel gears is complex and changeable, and the working environment is also relatively complex. Due to the strong background noise and strong nonlinearity of the fault vibration signal, it is difficult to accurately detect and analyze the fault characteristics.
The characteristics of non-stationarity and non-linearity make it difficult to identify the fault characteristics of rotating machinery. The modulation signal bispectrum (MSB) has powerful demodulation capabilities, which can effectively process nonlinear data, suppress Gaussian noise and non-Gaussian noise, and obtain the fault characteristics of rotating machinery in strong noise environments. A gear crack fault diagnosis method based on spectrum editing and MSB is proposed. This method can effectively suppress the interference of harmonic signals and white noise. The weighted average ensemble empirical mode decomposition (WAEEMD) and MSB are combined to extract the fault characteristics of rolling bearings. The second-order total variation denoising method is combined with MSB to diagnose the bearing. The MSB is improved to make it more stable, and the improved MSB is suitable for the classification of bearing faults.
The current research on fault diagnosis of spiral bevel gears is basically based on extracting features from vibration signals to analyze faults, such as the use of BP (Backpropagation) neural network by FOBIBO to identify the wear state of spiral bevel gears, and the use of Bayesian classifier by BUZZONI et al. to identify the wear and pitting state of straight bevel gears. However, traditional fault pattern recognition methods are difficult to effectively construct the complex mapping relationship between faults and signals. With the development of convolutional neural network (CNN), the accuracy of pattern recognition is getting higher and higher, and the data mining ability is also getting stronger. In recent years, CNN has been preliminarily studied and applied in rotating machinery fault diagnosis. CNN can improve the shortcomings of traditional fault pattern recognition algorithms, but how to construct spiral bevel gear fault samples based on vibration signals is the key to training damage degree recognition CNN model. Traditional time-domain and frequency-domain feature sample construction methods are difficult to extract weak fault features. However, MSB is a high-order spectrum that can effectively reflect the weak features of signals, and has been proven to be suitable for rotating machinery fault diagnosis. This paper combines MSB with CNN, using the modulation signal bispectrum of spiral bevel gear vibration signals to construct the input samples of CNN, and proposes a method for identifying the damage degree of spiral bevel gears based on modulation signal bispectrum and convolutional neural network. The effectiveness of the method is verified through experiments.
Damage degree identification of spiral bevel gears based on modulation signal bispectrum and CNN
The process of identifying the degree of damage of spiral bevel gears based on the modulation signal bispectrum and CNN is as follows:
Step 1: Conduct vibration testing of the spiral bevel gear failure, collect vibration signals from the spiral bevel gear using acceleration sensors, set theSelect a suitable sampling frequency and collect sufficient vibration signal segments.
Step 2: Split the collected vibration signal segments into several equal-length data segments, perform pre-processing and normalization, and perform The bispectrum analysis of the modulated signal is performed to extract the top-view image features of the modulated signal bispectrum, construct a feature map sample set, and divide it into a training set and a testing set.
Step 3: Initialize the learning rate k, pooling layer sampling size s, minimum training amount n, convolution kernel size o, and iteration number of the convolutional neural network
m and other parameters, and construct these parameters as a parameter set P. Set the learning rate, iteration number, minimum training amount, and convolution kernel size respectively, set the iteration threshold for the sampling size of the pooling layer to x1-x5, and adjust the step size to y1-y5.
Step 4: Input the training set into the CNN model for model training, optimize the key parameters such as the number of iterations and learning rate, and input the model error The model parameter set P with the minimum error rate is constructed to complete the CNN model training.
Step 5: Input the test sample set into the trained CNN model for identification to verify the effectiveness of the model, thus achieving the Damage degree identification.
Arc tooth bevel gear damage fault test
To verify the effectiveness of the method proposed in this paper, vibration simulation tests of spiral bevel gear damage faults were conducted on a spiral bevel gear system fault simulation bench. The spiral bevel gear reducer is shown in the figure. Depending on the degree of damage, normal gears and two different levels of damage faults were set up The three states of the spiral bevel gear are shown in the figure. Since the fault gear is located on the input shaft, the acceleration sensor is installed on the input shaft. The Bk test system is used to collect vibration signals from the spiral bevel gear under normal and different damage conditions. The vibration signals are collected under normal gear state, mildly damaged gear state, and moderately damaged gear state. The sampling frequency is 3.2kHz and the rotation speed is 900r/min.
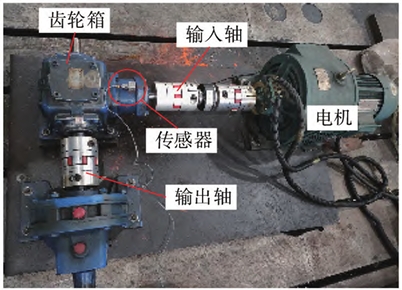
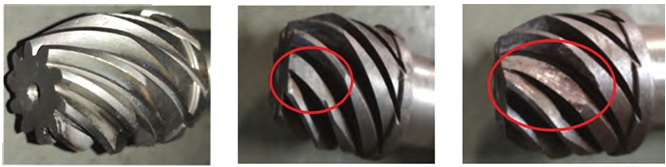
CNN model construction and parameter selection
The convolutional neural network structure used includes 1 input layer, 3 convolutional layers, 2 max pooling layers, 1 flattening layer, and 2 fully connected layers The process of convolutional neural network is as follows: (1) replace the activation function with ReLU; (2) adjust the feature image size of the model input to 128×128×1; (3) use maximum pooling to accelerate the network training speed; (4) add Batch Normalization operation after convolutional layer to accelerate the network convergence speed and stability; (5) add Dropout operation to the fully connected layer to effectively prevent overfitting.
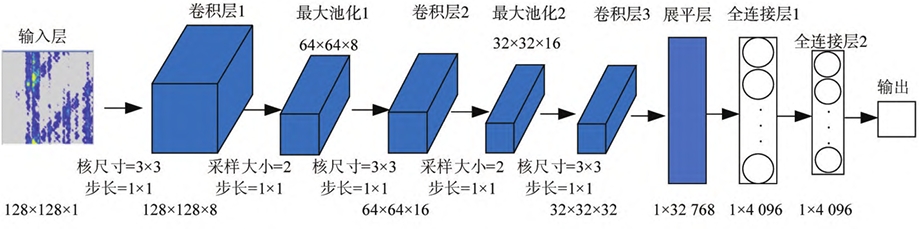
Identification results and analysis of spiral bevel gear failure
To verify the advantages and effectiveness of the bispectrum of modulated signals, the experiment selected the method of vibration signal + CNNS and modulated signal bispectrum + CNNS
The classification confusion matrix of different input samples is shown in Figure 7, where 0, 1, and 2 represent normal gears, slightly damaged gears, and moderately damaged gears, respectively. In order to eliminate the problem of differences in single-time diagnosis, each group of experiments was repeated 100 times, and the fault state recognition results were taken as the average of the repeated experiments. The recognition results and model training time of the two methods are shown in Table 2. From Table 2, it can be seen that the average recognition accuracy of the modulation signal bispectrum + CNN method is 99.91%, while the average recognition accuracy of the vibration signal + CNN method is lower than that of this method. As an input sample, the vibration signal is one-dimensional data, which contains a large amount of noise. Therefore, the average recognition accuracy decreases. The MSB method can not only effectively process nonlinear components of the signal, but also suppress various noises. Using MSB as a sample input to CNN, the extracted features are more accurate, so the average recognition accuracy is higher. In order to further verify the advantages and effectiveness of this method compared to other intelligent fault recognition methods, the identification results of modulation signal bispectrum + SVM and modulation signal bispectrum + BP were compared. Among them, SVM uses RBF kernel function with parameters selected as follows: kernel function parameter δ=3, penalty factor C=4, and BP neural network hidden layer node number is 32, and node activation function is ReLU. The latest test set classification confusion matrix is shown in Figure 8, where 0, 1, and 2 represent normal gears, slightly damaged gears, and moderately damaged gears, respectively. The diagonal line in the figure shows the specific prediction results of each type of signal. The recognition results and model training time are shown in Table 3. From Table 3, it can be seen that the average recognition accuracy of modulation signal bispectrum + CNN is 99.91%, while the average recognition accuracy of other two intelligent fault recognition methods are lower than this method; Similarly, sampling modulation signal bispectrum as model input sample, the training time of this method is 97s, which is far superior to other two intelligent fault recognition methods and greatly improves the efficiency of fault identification. When dealing with multi-classification problems, SVM has a more complex model due to the construction of the classifier, which leads to slower training speed. Moreover, SVM’s classifier only trains on samples with the same label, resulting in slower training and testing classification speed of SVM. Using modulation signal bispectrum as sample input,The features extracted by SVM are more accurate, resulting in a higher average recognition accuracy. However, the shallow structure of the BP neural network limits its ability to handle nonlinear problems, making it difficult to recognize some image features, which limits its ability to recognize fault information. The convolutional neural network is a deep structure with strong nonlinear processing capabilities. The weight sharing mechanism in the convolutional layer of the convolutional neural network reduces the number of trainable parameters in the network, improving training efficiency and resulting in a higher average recognition accuracy of the model.
Conclusion of the report
1) The convolutional network model and modulation signal bispectrum sample construction method that are constructed combine automatic feature learning with fault classification, which can compensate for the lack of human knowledge and improve the accuracy of fault classification.It overcomes the shortcoming of traditional fault identification methods that require manual feature extraction and simplifies the diagnostic process.
2) Compared with vibration signals, the modulation signal bispectrum has a higher average recognition accuracy when used as an input sample.Compared with traditional intelligent fault recognition methods, the proposed recognition method has advantages in both average recognition accuracy and model training time.Advantages.