Because the bearing and gear of the gear transmission mechanism will produce a lot of heat in the process of high-speed operation, this chapter mainly determines the size of the friction heat source and the boundary conditions of the bearing, so as to get the change rule of the bearing temperature with the increase of speed. Because the inner ring of the bearing is in direct contact with the shoulder, the temperature of the shoulder is greatly affected by the friction of the bearing, so the temperature of the shoulder is mainly affected by the temperature rise of the bearing. The gear shaft is in direct contact with the inner ring of the bearing, so the temperature of the outer surface where the gear shaft is in contact with the inner ring is also relatively high. The heat generated by the friction between the bearing and the gear in the gear transmission mechanism changes with the change of the speed of the gear wheel axle. Therefore, it is necessary to study the change law of the temperature field and the thermal stress field of the gear assembly at different speeds.
The rolling bearing consists of four parts: cage, rolling element, outer ring and inner ring. The inner ring is assembled with the journal, while the outer ring is assembled with the bearing seat. The inner ring rotates with the journal while the outer ring remains stationary. The influencing factors of bearing working temperature are: load on bearing, rotation speed of gear shaft, friction moment produced by bearing, type of lubricant used, lubricant viscosity and ambient temperature, etc. The change of bearing temperature is mainly affected by two factors: the heat generated by the friction of the system itself and the heat exchange capacity between the system and the environment. The heat of the system mainly comes from friction, including the rolling friction between the roller and the inner raceway, the rolling friction between the outer raceway, the sliding friction between the roller and the cage, the viscous friction, etc. In the process of bearing operation, most of the energy loss is converted into heat energy, which makes the temperature of bearing rise. The higher the temperature of the bearing, the greater the temperature difference between the bearing and the surrounding environment, and the heat transferred to the surrounding environment through heat exchange. Finally, the bearing will reach a heat balance state, that is, the friction heat generated by the system is equal to the heat lost to the environment.
The heat source in the bearing mainly comes from the friction heat generated by friction loss and rolling resistance. The main influencing factors of friction torque are: elastic lag of material, geometry of contact surface, deformation of contact surface and viscosity of lubricating oil.
Determination of boundary conditions: under the condition of neglecting radiation, the heat generated by bearing friction is mainly dissipated by conduction and convection. Since the bearing is located in the reduction gearbox, the gear is lubricated by immersion, and the lubricating oil will splash on the bearing, so it will have a cooling effect on the bearing. The forced convection heat transfer between the lubricating oil and the inner and outer raceways of the bearing is generally determined by experience, which is related to Prandtl number, viscosity of liquid or gas, heat transfer coefficient of gas or liquid and rotating speed.
In order to study the temperature of the bearing and the gear, the precise modeling method is adopted, the characteristics of the gear and the bearing are preserved, and the simplified model is used in the study of the whole system, which not only reduces the calculation time, but also makes the model simulation calculation easier to converge. In order to simplify the model, the following assumptions are made: ① when the gear is running at high speed, all the teeth on the gear shaft are considered as a continuous whole. ② The influence of the chamfering of the gear shaft and the profile of the gear on the temperature distribution of the whole system is ignored. ③ Neglecting the bearing groove and other characteristics, the influence of removing the gasket on the heat conduction of the system is ignored. On the basis of the above three assumptions, the gear assembly is properly simplified.
The thermal characteristic parameters of the above gear components are loaded into the established finite element simulation model of gear components, and the thermal solid coupling simulation analysis of the complex gear components is carried out through the thermal solid coupling function set in the finite element software. As shown in the figure, the temperature field distribution of gear assembly is illustrated with a typical speed of 4000R / min.
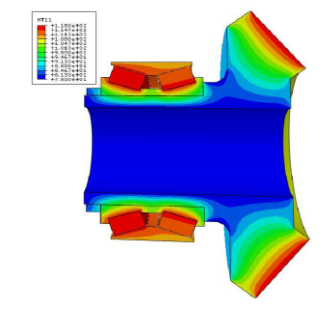
At different speeds, the heat generated by friction between bearing and gear is different, so the temperature field distribution and thermal stress field distribution of gear shaft at different speeds are studied, because the change of speed leads to the change of stress and temperature of gear shaft shoulder. The curve of the temperature T of the gear shaft shoulder with the speed is shown in the figure: when the speed is 2000r / min, the maximum temperature of the gear shaft shoulder is 87.66 ℃; when the speed is 4000R / min, the maximum temperature of the gear shaft shoulder is 93.65 ℃.
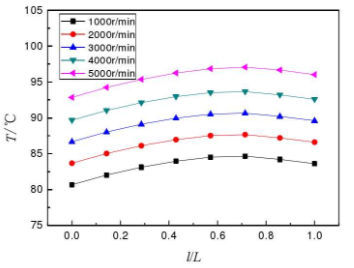
It can be seen from the figure that the temperature of gear shaft shoulder is higher and higher with the increase of rotating speed. When the speed is low, the temperature distribution curve of the gear shaft shoulder is relatively flat, while the slope of the temperature change curve becomes larger and larger at high speed. The results show that the temperature of the gear shoulder changes faster and faster with the increase of rotating speed. When the rotational speed of the gear shaft is fixed, the temperature of the shoulder decreases with the increase of the relative height and the decreasing amplitude is small. Because the gear shoulder and the bearing inner ring are closely connected, the temperature of the shoulder is more affected by the bearing, that is, the temperature of the gear shoulder gradually decreases from the bottom of the shoulder to the top of the shoulder. The temperature at the top of the gear shoulder is the lowest due to the cooling effect of the lubricating oil. In addition, the splashing of lubricating oil on the surface of gear assembly will also cool the gear shaft.
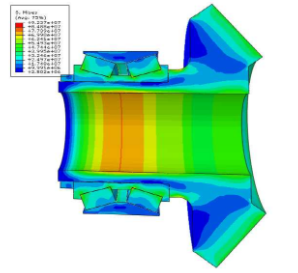
As shown in the figure, the distribution of the thermal stress field of the gear assembly at the speed of 4000R / min. It can be seen from the figure that the maximum stress is concentrated on the inner wall of the gear shaft, because this area is the location with the maximum temperature difference of the gear assembly. The gear shaft and the inner ring of the bearing are assembled with interference, and the gear assembly is heated and expanded, resulting in more serious extrusion between the gear shaft and the inner ring of the bearing.
The curve of the thermal stress σ t of the gear shoulder with the height of the shoulder is shown in the figure: the thermal stress of the gear shoulder increases with the height of the shoulder. In the range of 0 to 0.6 relative shoulder height, the thermal stress of shoulder increases slowly with the increase of rotating speed, while in the range of 0.6 to 1 relative shoulder height, the thermal stress of shoulder increases rapidly. With the increase of rotational speed, the slope of the curve of thermal stress changes more and more, which shows that the higher the rotational speed of gear shaft, the faster the change rate of thermal stress of gear shoulder.
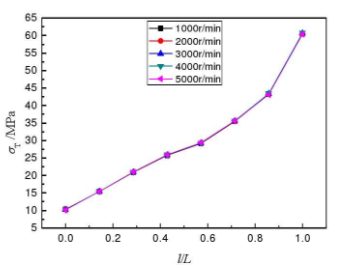
It can be seen from the figure that when the rotational speed of the gear shaft is fixed, the thermal stress of the gear shaft shoulder increases gradually from the bottom to the top of the shaft shoulder: when the rotational speed is 1000r / min, the thermal stress of the gear shaft shoulder increases from 10.41mpa at the bottom of the shaft shoulder to 60.40mpa at the top of the shaft shoulder. At the same shoulder height, the thermal stress of the shoulder increases with the increase of the rotating speed, but the increasing degree is not obvious: when the rotating speed is 2000r / min, the thermal stress of the top of the shoulder is 60.51mpa; when the rotating speed is 5000r / min, the thermal stress of the top of the shoulder is 60.87mpa. It can be seen that the influence of rotating speed on the change of thermal stress of shaft shoulder is not obvious.
According to the principle of thermal expansion and cold contraction, the gear shoulder is deformed due to the heat absorbed from the bearing and gear. The distribution of the thermal strain field of the gear assembly at the speed of 4000R / min is shown in the figure.
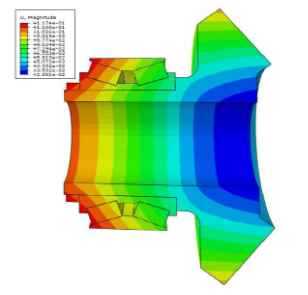
The curve of the thermal deformation of the gear shoulder τ st with the speed is shown in the figure respectively.
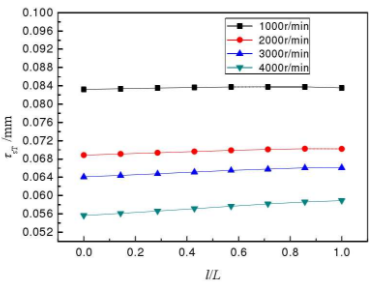
It can be seen from the figure that when the rotating speed is 1000r / min, the thermal deformation of the gear shoulder gradually increases from 0.0832mm to 0.0835mm; when the rotating speed is 3000r / min, the thermal deformation of the gear shoulder gradually increases from 0.0641mm to 0.0661mm, and the maximum deformation is at the highest position of the gear shoulder. Therefore, the thermal deformation of the gear shoulder increases slowly with the increase of the relative height of the shoulder.
Due to the constant contact between the shoulder and the bearing, the shoulder and the inner ring of the bearing will press against each other due to expansion after being heated and deformed in the working process, which will produce relatively large thermal stress. After stopping, the expansion will disappear, the shoulder and the inner ring will cooperate back to the initial state, and the thermal stress will disappear, and the long-term work will produce thermal fatigue.