1. Introduction
Beveloid gears are a unique type of gears that have found significant applications in various mechanical systems. They possess distinct geometric features that set them apart from traditional gears such as spur gears and bevel gears. Understanding the nature and capabilities of beveloid gears is crucial for engineers and designers in the field of mechanical engineering.
2. Geometry of Beveloid Gears
2.1 Definition and Basic Structure
A beveloid gear is a type of gear with a conical or frustum – like shape. Its teeth are designed in a specific pattern that allows for smooth meshing with other gears. Unlike regular bevel gears, beveloid gears have a more complex tooth profile that can be adjusted to meet different design requirements. The pitch surface of a beveloid gear is not a perfect cone but has a more general curved shape.
2.2 Tooth Profile and Parameters
The tooth profile of a beveloid gear is characterized by several parameters. These include the pressure angle, module, number of teeth, and helix angle. The pressure angle determines the force transmission characteristics between the meshing teeth. The module relates to the size of the gear teeth, and the number of teeth affects the gear ratio. The helix angle, if present, influences the axial thrust during gear operation. A comparison of these parameters with those of other common gears is shown in the following table:
Gear Type | Pressure Angle Range | Module Range | Number of Teeth Range | Helix Angle Option |
---|---|---|---|---|
Beveloid Gear | [α1 – α2] (varies depending on design) | m1 – m2 (application – specific) | z1 – z2 (depending on gear ratio needs) | Can have non – zero values for helical beveloid gears |
Spur Gear | Fixed standard values (e.g., 20°) | Standard series | Varies widely for different applications | Usually 0° |
Bevel Gear | Standard pressure angles similar to spur gears for some types | Specific to bevel gear design | Limited by cone geometry | Can be 0° for straight bevel gears, non – zero for spiral bevel gears |
3. Advantages of Beveloid Gears
3.1 High Load – Carrying Capacity
Beveloid gears are designed to handle high loads effectively. The unique tooth geometry distributes the load more evenly across the tooth surface compared to some other gear types. This results in reduced stress concentrations, which in turn allows the gears to withstand greater forces without premature failure. For example, in heavy – duty industrial machinery where large torque transmission is required, beveloid gears can provide reliable operation under high load conditions.
3.2 Smooth and Quiet Operation
The tooth profile of beveloid gears is optimized for smooth meshing. The gradual engagement and disengagement of the teeth reduce vibration and noise during operation. This makes them ideal for applications where noise reduction is crucial, such as in automotive transmissions or household appliances. The following table shows a comparison of noise levels between beveloid gears and other gears in a typical operating environment:
Gear Type | Noise Level (dB) at Rated Load |
---|---|
Beveloid Gear | [L1 – L2] (lower compared to some) |
Spur Gear | Higher than beveloid gear due to impact during meshing |
Helical Gear | Similar to beveloid gear in some cases but may have different frequency characteristics |
3.3 Versatility in Gear Ratio Adjustment
Beveloid gears offer great flexibility in achieving different gear ratios. By modifying the tooth parameters and the shape of the pitch surface, designers can obtain a wide range of gear ratios to suit specific application requirements. This is particularly useful in complex mechanical systems where multiple speed settings are needed, such as in machine tools or robotic actuators.
3.4 Compact Design
Due to their unique geometry, beveloid gears can often achieve the same gear ratio as larger traditional gears in a more compact space. This space – saving feature is highly valued in applications where size and weight constraints are important, such as in aerospace and portable equipment. For instance, in a small unmanned aerial vehicle’s power transmission system, beveloid gears can be used to transmit power efficiently within the limited space available.
4. Applications of Beveloid Gears
4.1 Automotive Industry
In the automotive sector, beveloid gears are used in various components. They are commonly found in differential systems, where they help distribute torque between the wheels. The ability to handle high loads and provide smooth operation is essential in this application. Additionally, beveloid gears are also used in some automatic transmission designs to achieve precise gear ratios for different driving conditions. The following table summarizes their applications in the automotive industry:
Automotive Component | Function of Beveloid Gears |
---|---|
Differential | Torque distribution between wheels, enabling smooth turning |
Automatic Transmission | Gear ratio adjustment for different speeds and driving modes |
4.2 Industrial Machinery
Beveloid gears play a significant role in industrial machinery. In conveyor systems, they are used to transfer power between different shafts to drive the conveyor belts. In heavy – duty milling machines, beveloid gears are employed to transmit the high torque required for cutting operations. They can also be found in printing presses, where precise speed and torque control are necessary for accurate printing.
Industrial Machinery Type | Role of Beveloid Gears |
---|---|
Conveyor System | Power transmission between shafts to drive the conveyor belt |
Milling Machine | High – torque transmission for cutting operations |
Printing Press | Precise speed and torque control for accurate printing |
4.3 Robotics
In the field of robotics, beveloid gears are used in joint actuators. Their compact design and ability to provide variable gear ratios make them suitable for robotic applications where space is limited and different motion speeds are required. For example, in the joints of an industrial robot arm, beveloid gears can help achieve the desired range of motion and force transmission.
Robotics Application | Function of Beveloid Gears |
---|---|
Robot Joint Actuators | Provide variable gear ratios for different motion speeds and force transmission in a compact space |
4.4 Aerospace Applications
In aerospace, beveloid gears are used in various systems. They can be found in aircraft landing gear mechanisms, where they need to handle high loads during landing and take – off. In some small satellite attitude control systems, beveloid gears are used to transfer power between different components in a limited space environment.
Aerospace Application | Role of Beveloid Gears |
---|---|
Landing Gear Mechanism | High – load handling during landing and take – off |
Satellite Attitude Control System | Power transfer in a limited space environment |
5. Manufacturing and Production of Beveloid Gears
5.1 Manufacturing Processes
The manufacturing of beveloid gears involves several advanced machining processes. These include gear hobbing, shaping, and grinding. Gear hobbing is a common method for rough cutting the teeth of beveloid gears. Shaping is used to refine the tooth profile, and grinding is often employed for achieving high – precision surface finish. Specialized cutting tools and machine tools are required for these processes. The choice of manufacturing process depends on factors such as the required accuracy, production volume, and cost.
5.2 Quality Control and Inspection
Quality control is of utmost importance in the production of beveloid gears. Inspection techniques such as coordinate measuring machines (CMMs) are used to measure the dimensions and geometric accuracy of the gears. Tooth profile errors, pitch errors, and run – out are some of the parameters that are carefully monitored. Any deviation from the specified tolerances can lead to poor performance or premature failure of the gears.
6. Design Considerations for Beveloid Gears
6.1 Load Analysis
When designing beveloid gears, a detailed load analysis is necessary. This includes determining the maximum torque, radial and axial loads that the gears will experience during operation. Based on this analysis, the appropriate gear material, tooth geometry, and size can be selected to ensure reliable performance under the expected load conditions.
6.2 Lubrication
Proper lubrication is essential for the smooth operation of beveloid gears. The lubricant not only reduces friction between the meshing teeth but also helps in dissipating heat generated during operation. The choice of lubricant depends on factors such as the operating speed, load, and temperature conditions. In some high – speed applications, special high – performance lubricants may be required.
6.3 Gearbox Design
When beveloid gears are used in a gearbox, the overall design of the gearbox needs to be carefully considered. This includes factors such as the layout of the gears, shaft alignment, and bearing selection. The gearbox should be designed to minimize vibration and noise and ensure efficient power transmission.
7. Future Trends and Developments
7.1 Advanced Materials
The use of advanced materials in beveloid gears is an area of ongoing research. New materials with higher strength – to – weight ratios, better wear resistance, and improved thermal properties are being developed. These materials will enable beveloid gears to operate under more extreme conditions and further enhance their performance.
7.2 Computational Design and Simulation
With the development of computational techniques, more accurate design and simulation of beveloid gears are possible. Finite element analysis (FEA) and computational fluid dynamics (CFD) can be used to analyze the stress distribution, heat transfer, and lubrication behavior of beveloid gears. This will lead to more optimized designs and reduced development time.
7.3 Miniaturization and Integration
In the future, there will be a trend towards miniaturization and integration of beveloid gears in micro – mechanical systems. This will require further innovation in manufacturing processes and design techniques to meet the challenges of working at smaller scales.
In conclusion, beveloid gears are a remarkable type of gears with numerous advantages and wide – ranging applications. Their unique geometry, high load – carrying capacity, smooth operation, and versatility make them an important component in various mechanical systems. With continuous research and development in materials, manufacturing, and design, beveloid gears are expected to play an even more significant role in the future of mechanical engineering.
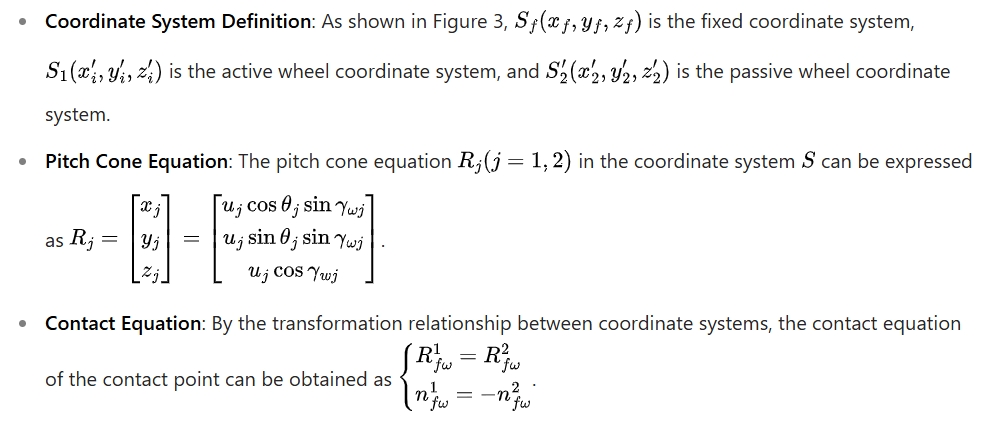