Introduction
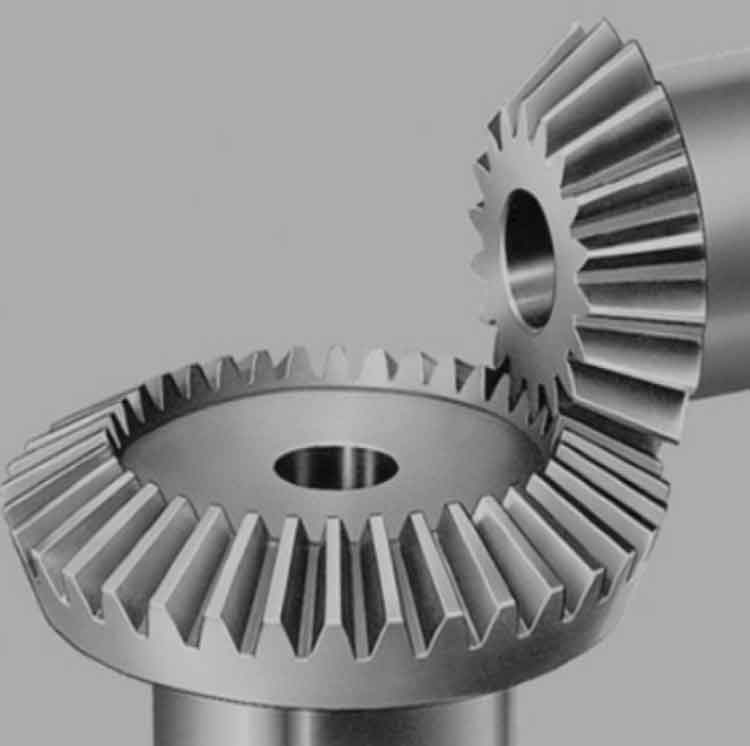
Machining large straight bevel gears presents a unique set of challenges due to their size, complexity, and the precision required. These gears are essential components in heavy machinery, power transmission systems, and various industrial applications. This article explores the primary challenges encountered in the machining of large straight bevel gears and offers practical solutions to address these issues.
Importance of Large Straight Bevel Gears
Large straight bevel gears are critical for several reasons:
- Power Transmission:
- They enable efficient power transmission between intersecting shafts.
- Load Capacity:
- Capable of handling high loads due to their robust design.
- Versatility:
- Used in a wide range of industrial applications, from heavy machinery to automotive and aerospace sectors.
Key Challenges in Machining Large Straight Bevel Gears
- Material Selection and Handling:
- Choosing the right material that balances strength, wear resistance, and machinability.
- Handling large, heavy workpieces during the machining process.
- Precision and Accuracy:
- Achieving the required geometric tolerances and surface finish.
- Maintaining accuracy throughout the machining process to ensure proper gear meshing and performance.
- Tool Wear and Management:
- High rates of tool wear due to the hardness and toughness of straight bevel gear materials.
- Efficient management and replacement of cutting tools to maintain quality and productivity.
- Thermal Distortion:
- Managing heat generation during machining to prevent thermal distortion and maintain dimensional accuracy.
- Surface Finish and Quality:
- Achieving the desired surface finish to ensure smooth operation and minimize wear.
- Preventing surface defects such as scratches, burrs, and pitting.
- Time and Cost Efficiency:
- Balancing machining time with cost-efficiency while maintaining high-quality standards.
- Reducing downtime and optimizing production schedules.
Solutions to Machining Challenges
1. Material Selection and Handling
Solution:
- Material Selection:
- Opt for high-quality, machinable materials like alloy steels, which offer a balance between hardness and machinability.
- Handling:
- Use advanced material handling systems such as overhead cranes, robotic arms, and automated guided vehicles (AGVs) to safely and efficiently move large workpieces.
2. Precision and Accuracy
Solution:
- Advanced CNC Machines:
- Utilize state-of-the-art CNC machines with high precision capabilities to achieve tight tolerances.
- Inspection and Measurement:
- Implement rigorous inspection processes using coordinate measuring machines (CMMs) and laser scanners to ensure accuracy at each stage of machining.
3. Tool Wear and Management
Solution:
- High-Quality Cutting Tools:
- Use high-quality, wear-resistant cutting tools made from carbide or ceramic materials to extend tool life.
- Tool Monitoring Systems:
- Employ tool monitoring systems that detect wear and predict tool life, allowing for timely replacements and reducing unexpected downtime.
4. Thermal Distortion
Solution:
- Coolant Systems:
- Implement advanced coolant systems to effectively manage heat and reduce thermal distortion.
- Machining Strategies:
- Use strategies such as intermittent cutting and optimized cutting speeds to minimize heat generation.
5. Surface Finish and Quality
Solution:
- Finishing Operations:
- Perform finishing operations such as grinding, honing, and polishing to achieve the desired surface finish.
- Quality Control:
- Implement strict quality control measures to inspect and rectify surface defects promptly.
6. Time and Cost Efficiency
Solution:
- Process Optimization:
- Optimize machining processes through simulation and modeling to reduce cycle times and improve efficiency.
- Lean Manufacturing:
- Adopt lean manufacturing principles to eliminate waste, streamline production, and enhance cost efficiency.
Comparative Analysis of Solutions
Table 1: Comparative Analysis of Solutions
Challenge | Solution | Advantages | Disadvantages |
---|---|---|---|
Material Handling | Advanced Handling Systems | Safe, efficient movement of large workpieces | High initial investment |
Precision | Advanced CNC Machines | High accuracy and tight tolerances | Requires skilled operators |
Tool Wear | High-Quality Cutting Tools | Extended tool life, reduced downtime | Higher cost of cutting tools |
Thermal Distortion | Advanced Coolant Systems | Reduced thermal distortion, improved dimensional accuracy | Increased operational complexity |
Surface Finish | Finishing Operations | Enhanced surface quality and performance | Additional processing time and cost |
Time Efficiency | Process Optimization | Reduced cycle times, improved productivity | Requires advanced planning and analysis |
Implementation Strategies
- Training and Development:
- Invest in training programs for operators and technicians to ensure they are skilled in using advanced machinery and handling large components.
- Research and Development:
- Continuously invest in R&D to develop new machining techniques and materials that can improve performance and efficiency.
- Collaboration with Suppliers:
- Work closely with suppliers to ensure a consistent supply of high-quality materials and cutting tools.
- Maintenance and Upkeep:
- Establish a robust maintenance program to keep machinery in optimal condition, minimizing downtime and extending equipment life.
Conclusion
Machining large straight bevel gears involves addressing several significant challenges, from material selection and precision to tool wear and thermal distortion. By implementing advanced technologies, optimizing processes, and investing in skilled labor, manufacturers can overcome these challenges and produce high-quality bevel gears efficiently. Continuous improvement and adaptation to new technologies will further enhance the machining of large straight bevel gears, ensuring their reliability and performance in various industrial applications.