Using the improved LTCA method to calculate the time-varying meshing stiffness of gears is another high-efficiency and high-precision calculation method. Based on LTCA, this method can accurately obtain the tooth surface load distribution P and the load transmission error Z under the current contact position load P. According to the formula, the bearing transmission error Z is transformed into meshing deformation δ n:
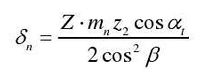
Where Mn is the normal modulus, the number of Z2 driven teeth, α t end pressure angle and β helix angle.
Then the meshing stiffness K (T) is:
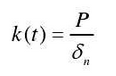
The bearing transmission error (LTE) of gear pair is mainly composed of geometric transmission error (TE), gear bending deformation and tooth surface contact deformation. The geometric transmission error Tooth Surface Design and the specific manufacturing and processing accuracy are determined. When the material, geometric parameters and meshing position of the gear pair are fixed, the bending deformation and contact deformation of the gear are determined by the load P on the tooth surface
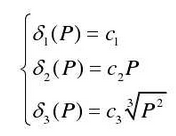
Where C1, C2 and C3 are coefficients to be calculated, δ 1, δ 2 and δ 3 represent te, gear bending deformation and contact deformation respectively.
A meshing period is divided into N parts. ZK (P) represents the load-bearing deformation of the K (k = 1,2, N + 1) meshing position under the nominal load P, which can be obtained by LTCA program.
In conclusion, the load-bearing deformation of the kth meshing position under the nominal load P can be obtained
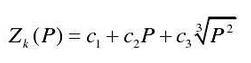
The load-bearing transmission errors of n different meshing positions under a fixed load are obtained by LTCA program, and the meshing stiffness of each meshing point is calculated by the method shown in the formula, and the time-varying meshing stiffness curve under the load is obtained after fitting.
By using the same method, the transmission error of a certain meshing position under three different loads is obtained, and the coefficients C1, C2 and C3 are determined by undetermined coefficient method, then the function expression of load and deformation at different meshing positions of the gear pair can be obtained, and then the meshing stiffness of the point under any load can be obtained. The time-varying meshing stiffness of the gear under any load can be obtained by calculating all the meshing positions in the whole meshing period.
Taking the reducer of an electric vehicle as an example, the load-bearing error of the gear pair is obtained by LTCA method, and the time-varying meshing stiffness curve of the high-speed gear pair under the input torque of 100N − m is obtained according to the above method.
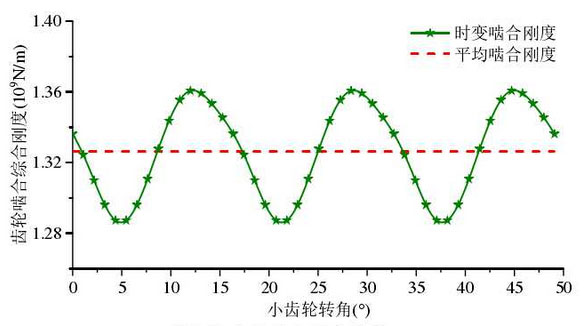