Introduction
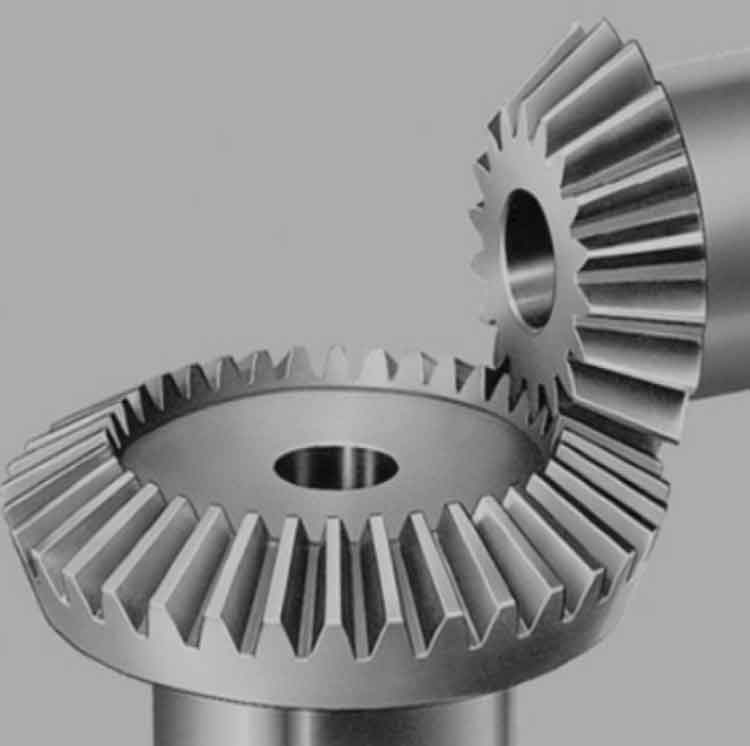
Straight bevel gear is integral components in numerous industrial applications, facilitating efficient power transmission between intersecting shafts. This article provides a comparative analysis of straight bevel gear performance across various industries, examining their advantages, limitations, and specific use cases.
Importance of Straight Bevel Gear
Straight bevel gear is characterized by their straight teeth, which are cut along the face of the bevel and intersect at an angle. These gears are essential due to their:
- Simplicity:
- Straightforward design and manufacturing process.
- Cost-Effectiveness:
- Lower production costs compared to more complex gear types.
- Versatility:
- Suitable for a wide range of industrial applications.
Key Performance Metrics
The performance of straight bevel gear can be evaluated based on several key metrics:
- Load Capacity:
- The maximum load straight bevel gear can handle without failure.
- Efficiency:
- The percentage of input power successfully transmitted to the output shaft.
- Durability:
- The gear’s ability to withstand wear and tear over time.
- Noise and Vibration:
- The level of noise and vibration generated during operation.
- Maintenance Requirements:
- The frequency and complexity of maintenance needed to keep straight bevel gear in optimal condition.
Comparative Analysis of Industrial Applications
1. Automotive Industry
In the automotive sector, straight bevel gear is commonly used in differential systems, allowing wheels to rotate at different speeds.
- Advantages:
- High load capacity
- Efficient power transmission
- Robust and durable
- Limitations:
- Moderate noise and vibration levels
- Requires precise alignment
Table 1: Performance Metrics in Automotive Applications
Metric | Performance |
---|---|
Load Capacity | High |
Efficiency | High |
Durability | Excellent |
Noise and Vibration | Moderate |
Maintenance | Regular lubrication and inspection needed |
2. Aerospace Industry
In aerospace applications, straight bevel gear is used in actuators and control systems, where precise movement is crucial.
- Advantages:
- High precision and reliability
- Lightweight design
- Good efficiency
- Limitations:
- Higher manufacturing costs
- Sensitive to alignment issues
Table 2: Performance Metrics in Aerospace Applications
Metric | Performance |
---|---|
Load Capacity | Moderate |
Efficiency | High |
Durability | High |
Noise and Vibration | Low |
Maintenance | Low, with high precision requirements |
3. Industrial Machinery
Straight bevel gear in industrial machinery are used in equipment such as conveyors, mixers, and pumps, where reliable power transmission is essential.
- Advantages:
- High load capacity
- Durable under harsh conditions
- Cost-effective
- Limitations:
- Can generate significant noise
- Requires regular maintenance
Table 3: Performance Metrics in Industrial Machinery Applications
Metric | Performance |
---|---|
Load Capacity | High |
Efficiency | Moderate to High |
Durability | Excellent |
Noise and Vibration | High |
Maintenance | Regular, often requiring lubrication |
4. Marine Industry
In the marine industry, straight bevel gear is used in propulsion systems and auxiliary equipment, where resistance to corrosion and reliability are critical.
- Advantages:
- High resistance to corrosion (with appropriate materials)
- Reliable performance under varying loads
- Good durability
- Limitations:
- Higher material costs for corrosion-resistant options
- Noise and vibration can be an issue
Table 4: Performance Metrics in Marine Applications
Metric | Performance |
---|---|
Load Capacity | High |
Efficiency | High |
Durability | Excellent with corrosion-resistant materials |
Noise and Vibration | Moderate |
Maintenance | Regular, with focus on corrosion prevention |
5. Robotics and Automation
In robotics and automation, straight bevel gear is used in joints and drive systems, where precision and responsiveness are key.
- Advantages:
- High precision and control
- Good efficiency
- Lightweight and compact
- Limitations:
- Sensitive to misalignment
- Higher production costs due to precision requirements
Table 5: Performance Metrics in Robotics and Automation
Metric | Performance |
---|---|
Load Capacity | Moderate |
Efficiency | High |
Durability | High |
Noise and Vibration | Low |
Maintenance | Low, with high precision requirements |
Material Considerations
The performance of straight bevel gear also heavily depends on the materials used. Common materials include:
- Carbon Steels
- Affordable, good mechanical properties.
- Suitable for general-purpose gears.
- Alloy Steels
- Enhanced strength, wear resistance.
- Ideal for high-performance applications.
- Stainless Steels
- Excellent corrosion resistance.
- Used in harsh environments like marine applications.
- Cast Iron
- Good vibration damping, machinability.
- Used in industrial machinery.
- Plastics and Composites
- Lightweight, low noise.
- Used in robotics and light-duty applications.
Table 6: Material Properties Comparison
Material | Strength | Wear Resistance | Corrosion Resistance | Cost |
---|---|---|---|---|
Carbon Steel | Moderate | Moderate | Low | Low |
Alloy Steel | High | High | Moderate | Medium |
Stainless Steel | Moderate | Moderate | High | High |
Cast Iron | Moderate | High | Low | Low |
Plastics/Composites | Low | Moderate | High | Low |
Challenges and Solutions
While straight bevel gear is highly versatile, they do present certain challenges:
- Alignment Issues
- Misalignment can lead to increased wear and noise.
- Solution: Precise manufacturing and installation processes.
- Noise and Vibration
- Straight teeth design inherently generates more noise compared to helical gears.
- Solution: Use of noise-damping materials and proper lubrication.
- Maintenance
- Regular maintenance is crucial to prevent wear and failure.
- Solution: Implementing regular inspection and lubrication schedules.
Future Trends
The future of straight bevel gear technology is likely to be influenced by several trends:
- Advanced Materials
- Development of new alloys and composites for enhanced performance.
- Additive Manufacturing
- Use of 3D printing for complex gear geometries and rapid prototyping.
- Digital Twins and IoT
- Integration of digital twins and IoT for real-time monitoring and predictive maintenance.
- Surface Treatments
- Advanced surface treatments to improve wear resistance and longevity.
Conclusion
Straight bevel gear play a critical role in various industrial applications due to their simplicity, cost-effectiveness, and versatility. This comparative analysis highlights the strengths and limitations of straight bevel gear in different sectors, emphasizing the importance of material selection and addressing common challenges. By understanding these factors, industries can optimize the performance and durability of straight bevel gear, ensuring efficient and reliable power transmission in their applications.