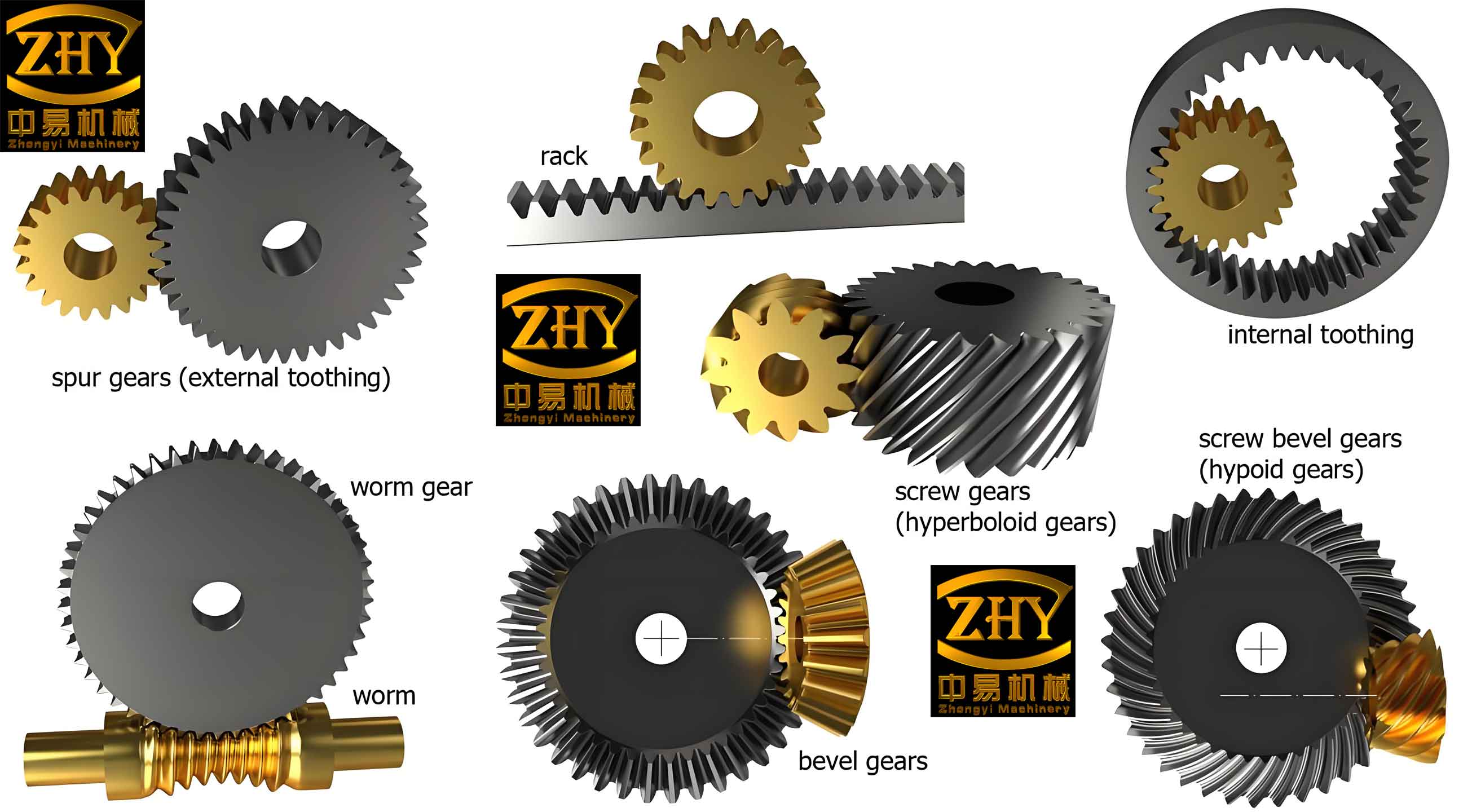
The manufacturing of gears is a critical process in various industries, including automotive, aerospace, and heavy machinery. The choice of material significantly impacts the performance, durability, and efficiency of gears. Nodular cast iron, also known as ductile iron, has gained prominence in gear manufacturing due to its unique combination of strength, ductility, and wear resistance. This article presents a comparative study of nodular cast iron and other ferrous alloys commonly used in gear manufacturing, highlighting their respective advantages, limitations, and applications.
Introduction
Gears are essential components that transmit power and motion between machine parts. The materials used for gear manufacturing must exhibit high strength, wear resistance, fatigue resistance, and machinability. Ferrous alloys, including nodular cast iron, carbon steel, and alloy steel, are widely used in gear manufacturing. This comparative study examines the properties, performance, and applications of these materials in gear manufacturing.
Properties of Nodular Cast Iron
Nodular cast iron is characterized by its spherical graphite nodules, which impart enhanced mechanical properties compared to traditional cast iron. The key properties of nodular cast iron relevant to gear manufacturing include:
- High Tensile Strength: Provides resistance to breaking under tensile loads.
- Excellent Ductility: Allows the material to deform without breaking, improving shock absorption.
- Good Wear Resistance: Reduces surface wear in high-contact applications.
- Superior Fatigue Resistance: Enhances the lifespan of gears under cyclic loading.
Table 1: Key Properties of Nodular Cast Iron
Property | Value |
---|---|
Tensile Strength | 600 – 900 MPa |
Yield Strength | 350 – 600 MPa |
Elongation | 10 – 18% |
Hardness | 150 – 300 HB |
Fatigue Strength | High (similar to steels) |
Comparison with Other Ferrous Alloys
1. Carbon Steel
Carbon steel is a popular material for gear manufacturing due to its high strength and hardness. It is available in various grades, each offering different properties based on carbon content.
Advantages:
- High strength and hardness
- Good wear resistance
- Cost-effective
Limitations:
- Lower ductility compared to nodular cast iron
- Requires heat treatment to achieve desired properties
Applications:
- Automotive gears
- Industrial machinery
Table 2: Properties of Common Carbon Steels Used in Gear Manufacturing
Grade | Tensile Strength (MPa) | Yield Strength (MPa) | Hardness (HB) |
---|---|---|---|
AISI 1045 | 570 – 700 | 300 – 450 | 170 – 210 |
AISI 1050 | 640 – 770 | 350 – 500 | 200 – 230 |
AISI 1060 | 690 – 840 | 400 – 600 | 210 – 250 |
2. Alloy Steel
Alloy steels contain additional alloying elements such as chromium, molybdenum, and nickel, which enhance their mechanical properties and corrosion resistance.
Advantages:
- High strength and toughness
- Improved wear and corrosion resistance
- Excellent fatigue resistance
Limitations:
- Higher cost compared to carbon steel
- More complex heat treatment processes
Applications:
- High-performance automotive gears
- Aerospace components
- Heavy-duty industrial gears
Table 3: Properties of Common Alloy Steels Used in Gear Manufacturing
Grade | Tensile Strength (MPa) | Yield Strength (MPa) | Hardness (HB) |
---|---|---|---|
AISI 4140 | 850 – 1000 | 650 – 850 | 200 – 260 |
AISI 4340 | 930 – 1080 | 720 – 960 | 240 – 300 |
AISI 8620 | 620 – 880 | 350 – 650 | 140 – 200 |
3. Comparison of Performance
Strength and Hardness: Alloy steels generally offer higher tensile and yield strengths compared to nodular cast iron and carbon steel. This makes them suitable for high-stress applications.
Ductility and Toughness: Nodular cast iron excels in ductility and toughness due to its graphite nodules, making it ideal for applications requiring impact resistance and shock absorption.
Wear and Fatigue Resistance: While alloy steels provide excellent wear and fatigue resistance, nodular cast iron also performs well in these aspects, especially when properly heat-treated.
Cost and Machinability: Nodular cast iron is cost-effective and easier to machine than many alloy steels, offering a good balance between performance and manufacturing efficiency.
Table 4: Comparative Performance of Ferrous Alloys in Gear Manufacturing
Property | Nodular Cast Iron | Carbon Steel | Alloy Steel |
---|---|---|---|
Tensile Strength | Moderate | High | Very High |
Ductility | High | Moderate | Moderate |
Wear Resistance | High | High | Very High |
Fatigue Resistance | High | Moderate | Very High |
Cost | Moderate | Low | High |
Machinability | Good | Moderate | Moderate to Poor |
Case Studies and Applications
Case Study 1: Automotive Gears
In the automotive industry, gears must withstand high loads, frequent cycling, and varying environmental conditions. Nodular cast iron gears offer a balance of strength, wear resistance, and cost-effectiveness, making them suitable for transmission and differential gears.
Case Study 2: Heavy Machinery
Heavy machinery gears require exceptional toughness and durability to handle harsh operating conditions. Alloy steels, with their superior strength and fatigue resistance, are often chosen for these applications. However, nodular cast iron is also used in some cases where cost and machinability are prioritized.
Conclusion
The choice of material in gear manufacturing depends on various factors, including mechanical properties, cost, and specific application requirements. Nodular cast iron offers a unique combination of high strength, ductility, wear resistance, and cost-effectiveness, making it a viable alternative to traditional ferrous alloys such as carbon and alloy steels. By understanding the comparative advantages and limitations of these materials, manufacturers can make informed decisions to optimize gear performance and longevity.