1. Introduction
1.1 Background and Significance
With the rapid development of national defense, robotics, and aerospace technology, precision machine tools are advancing towards high speed, high efficiency, and high precision. The cycloid gear forming grinding machine is one of the core equipments for realizing the localization of industrial robot cycloid pinwheel precision reducers in China. The column, as a key basic component and guiding element of the machine tool, directly affects the grinding accuracy. Optimizing the stiffness, anti-vibration, and stability of precision machine tools, and realizing the lightweight and optimal layout of components are current technical challenges faced by precision machine tools.
1.2 Research Status at Home and Abroad
Many scholars at home and abroad have studied the structures of machine tool columns and beds using methods such as finite element analysis and topology optimization. However, most of them use a single optimization design method and do not comprehensively optimize using multiple methods.
1.3 Research Objectives and Contents
This article aims to propose a multistage multi-objective optimization design method combining topology optimization, structural bionics, and size optimization for the cycloid wheel forming grinding machine column, and verify its feasibility through performance simulation and comparison. The main research contents include the 3D modeling of the prototype cycloid wheel forming grinding machine, the static and dynamic analysis of the prototype column, and the three-stage comprehensive optimization design process.
2. Prototype Cycloid Wheel Forming Grinding Machine 3D Modeling
2.1 Introduction to Y7654A Cycloid Wheel Grinding Machine
The Y7654A cycloid wheel grinding machine is an early developed cycloid wheel grinding machine by Qinchuan Machine Tool Factory and is also a representative one in China. However, its processing accuracy is relatively low compared with foreign forming grinding machines at the same period, mainly due to the insufficient static and dynamic performance of the machine tool structure.
2.2 3D Modeling of Prototype Cycloid Wheel Forming Grinding Machine
A 3D model of the prototype cycloid wheel forming grinding machine is designed with reference to the Y7654A cycloid wheel grinding machine. The column is selected as the research object as its overall static and dynamic performance affects the machining accuracy of the cycloid wheel forming grinding machine.
2.3 Vibration System Analysis of Machine Tool Column
The machine tool column is regarded as a vibration system composed of mass, spring, and damping. The vibration differential equation is established, and the relationship between the natural frequency and the dynamic performance of the column is analyzed. It is found that increasing the maximum natural frequency can improve the dynamic performance of the machine tool column.
Parameter | Description | Relationship with Dynamic Performance |
---|---|---|
Mass | Affects the inertia of the vibration system | Larger mass may lead to lower natural frequency and poorer dynamic performance |
Spring constant | Determines the stiffness of the system | Higher can increase the natural frequency and improve dynamic performance |
Damping | Affects the attenuation of vibration | Appropriate damping can help stabilize the system |
3. Prototype Column Static and Dynamic Analysis
3.1 Prototype Column Finite Element Model
The cycloid wheel forming grinding machine column is drawn using 3D modeling software, and its structure is determined to be a cantilever beam structure. Based on the actual working conditions and loads, the prototype column is preliminarily designed, and the boundary conditions are set, including the application of uniform loads on the column guide surface and the top of the column, as well as the consideration of the column’s own gravity and fixed constraints at the bottom.
3.2 Prototype Column Static Analysis
The material of the machine tool column is set as gray cast iron, and after meshing, the finite element model is obtained. Through static analysis under the set boundary conditions, the maximum stress and deformation displacement of the prototype column are obtained, which are 0.56073 MPa and 0.0057636 mm, respectively.
Static Analysis Results | Value | Unit |
---|---|---|
Maximum Stress | 0.56073 | MPa |
Deformation Displacement | 0.0057636 | mm |
3.3 Prototype Column Modal Analysis
The modal analysis of the machine tool column is an important part of the machine tool structure analysis. The material properties and constraint conditions are the same as those in the static analysis. The first six-order vibration mode diagrams and natural frequencies of the machine tool column are obtained. The first-order natural frequency is 183.25 Hz.
Order | Natural Frequency (Hz) |
---|---|
1 | 183.25 |
2 | 189.39 |
3 | 471.44 |
4 | 805.78 |
5 | 812.46 |
6 | 887.89 |
4. Three-Stage Comprehensive Optimization Design Process
4.1 Column Main Body Topology Optimization
Topology optimization is used to improve the layout of the column main body structure by taking the structural compliance as the objective function and the material volume fraction as the constraint condition. After optimization, the overall iteration speed is fast, the lightweight effect is significant, and the structure has practicality.
Topology Optimization Results | Description |
---|---|
Iteration Speed | Converges quickly after 28 iterations with static compliance as the objective function |
Lightweight Effect | Column mass is greatly reduced |
Structure Practicality | Retained design areas with cell density above 0.4 have a large improvement in stiffness and are easy to manufacture |
4.2 Column Bionic Structure Optimization
Based on the similarity in structure, function, and load between the king lotus leaf veins and the banana petiole and the machine tool column, the internal rib plate structure of the column is optimized. The king lotus leaf veins have a cross-vein layout similar to the rib plate layout of the column, and both play a supporting role and bear similar loads. The banana petiole also has similarities in structure and function with the column.
4.3 Size Optimization Based on Response Surface Method
4.3.1 Parameterized Model Establishment
After topology optimization and structural bionic optimization, the internal structural dimensions of the bionic column are optimized. Eight size parameters are selected, and their initial values and variation ranges are determined. The parameterized model is established to prepare for subsequent optimization.
Size Parameter | Variable Description | Initial Value (mm) | Variation Range (mm) |
---|---|---|---|
DS_L | Thickness of the main vein rib plate imitating leaf veins | 10 | 9 – 11 |
DS_W | Length of the rear cavity of the column | 135 | 130 – 140 |
DS_P | Thickness of the secondary vein rib plate imitating leaf veins | 5 | 4 – 6 |
DS_R | Depth of the rear cavity of the column | 500 | 475 – 525 |
DS_Y | Thickness of the rib plate imitating the banana petiole | 8 | 7 – 9 |
DS_U | Thickness of the rib plate in the front cavity of the column | 10 | 9 – 11 |
DS_I | Depth of the front cavity of the column | 160 | 155 – 170 |
DS_T | Thickness of the diagonal rib in the column cavity | 5 | 4 – 6 |
4.3.2 Experimental Design
The central composite experimental design (CCD) is used to extract 81 groups of data theoretical points. The input parameters are the eight internal dimensions of the column, and the output parameters are the first-order natural frequency, mass, maximum stress, and deformation displacement of the column. The response values of the data theoretical points are obtained.
4.3.3 Column Optimization Based on MOGA Algorithm
Based on the response values of the data theoretical points obtained from the experimental design, a column optimization mathematical model is established with the column mass as the objective function and the first-order natural frequency and deformation displacement as the constraint functions. The genetic algorithm in ANSYS Workbench Design Experiment is used to solve the model, and three groups of optimal structural dimensions are obtained. The static and dynamic performance of the third group of dimensions with the smallest objective function under the same constraints is compared with that of the prototype column.
Column | Mass (kg) | Natural Frequency (Hz) | Deformation Displacement (mm) | Maximum Stress (MPa) |
---|---|---|---|---|
Prototype Column | 1254.5 | 183.25 | 0.0057636 | 0.56073 |
Bionic Column | 1023.7 | 184.09 | 0.0057327 | 0.42876 |
5. Conclusion
5.1 Summary of Optimization Results
A multistage multi-objective optimization method combining topology optimization, structural bionics, and size optimization is proposed for the cycloid wheel forming grinding machine column. This method breaks the æįž of existing design experience, provides a new design idea for the column structure, and realizes the lightweight and improvement of the static and dynamic performance of the column.
5.2 Significance and Application Prospect of Research Results
The research results have important guiding significance for the design and optimization of machine tool columns, and can provide a reference for improving the performance of precision machine tools. The proposed optimization method can also be extended to other mechanical structures to promote the development of mechanical design and manufacturing technology.
5.3 Future Research Directions
Future research can focus on further improving the optimization algorithm and model to achieve more accurate and efficient optimization results. In addition, the influence of different working conditions and materials on the performance of the machine tool column can be further studied to provide more comprehensive design guidance.
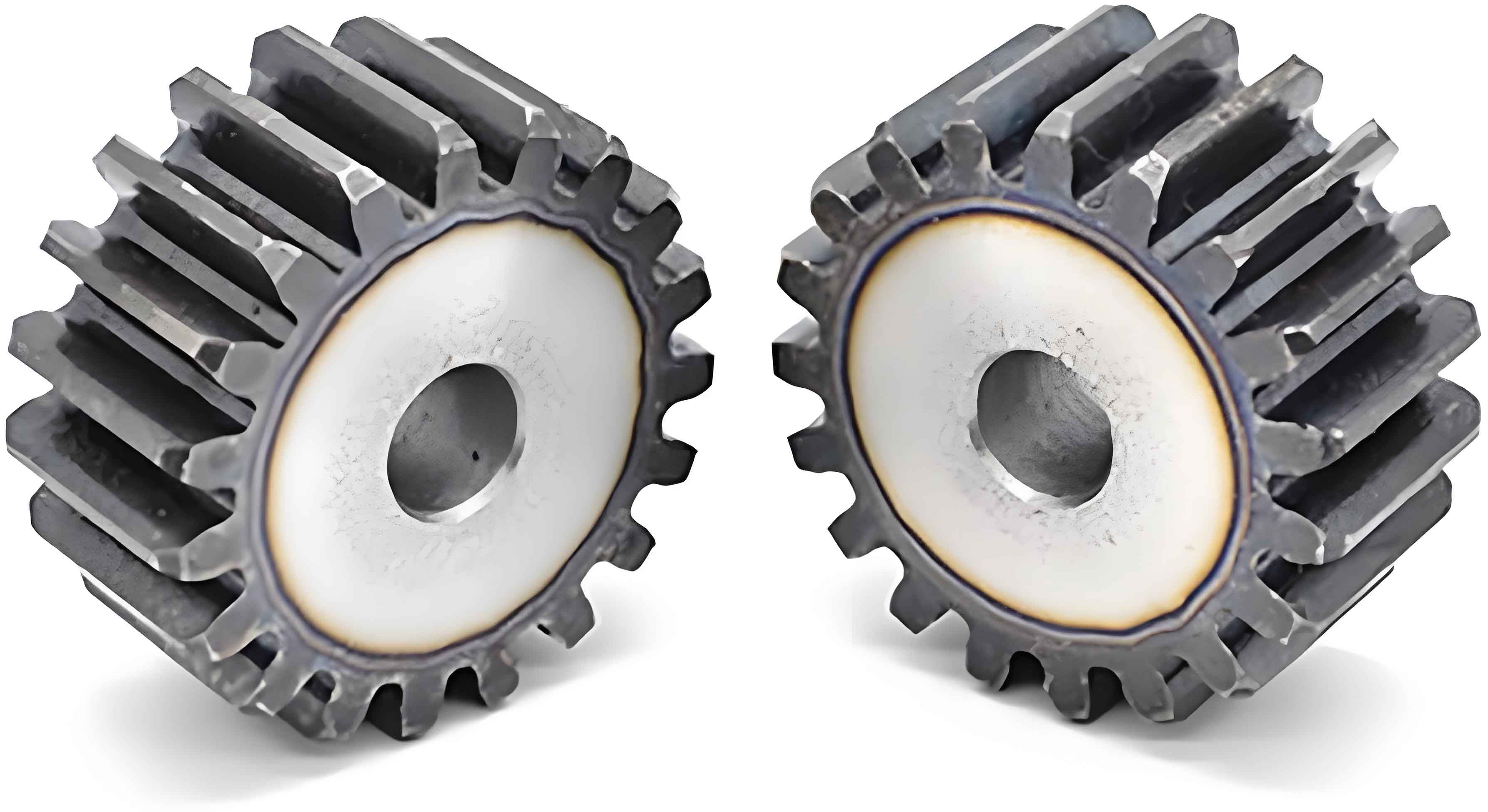