The dynamic simulation is carried out by using Benedict amp; Kelly model and time-varying friction coefficients obtained in Figure 2.8 under different micro-states of tooth surfaces.
1. Time-domain signal characteristics of dynamic displacement
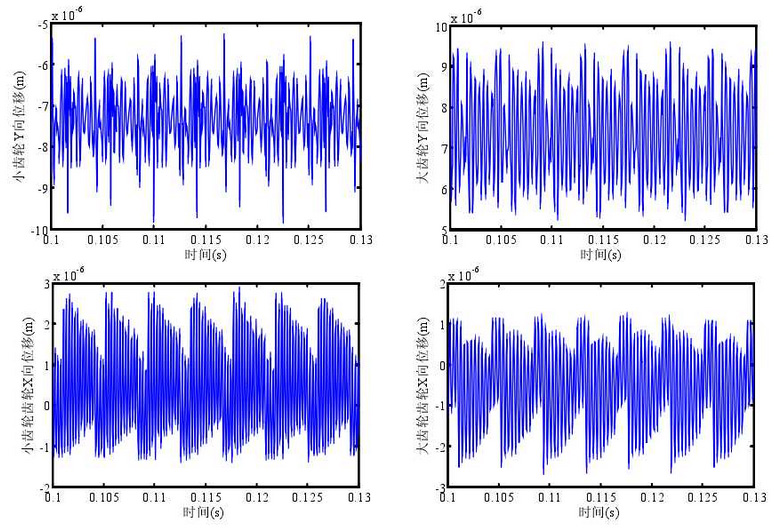
Figure 1 shows the time-domain signal (Savg=0.523) of the displacement response of the active and passive gears in the X and Y directions.Fig.) N K (force rodent) N K (visible engagement line direction (Y direction) displacement amplitude is greater than friction direction (X direction), there is obvious periodic impact on both signals.
2. Dynamic engagement force and friction force
As shown in Figure 2, the time domain signal of dynamic force between two gears is extracted from the signal of two meshing cycles in steady state, which is also convenient for analysis. The transverse coordinate is also convenient for analysis in dimensionless time (t/tD), the transverse coordinate is also convenient for analysis in dimensionless time (t/tD), and the transverse coordinate is expressed in dimensionless time (t/tD).The periodicity of dynamic meshing force fluctuation can be seen from the diagram. There is obvious meshing impact at single and double teeth alternating meshing point B, D and E, up to 3.6kN, while the average meshing force is about 2.6kN, which is the main excitation source of gear vibration.Comparing the three different tooth surfaces, with the increase of roughness, the meshing amplitude tends to decrease gradually. For example, when Savg=0.991, the maximum meshing force is 3kN and the average meshing force is 2.2kN.
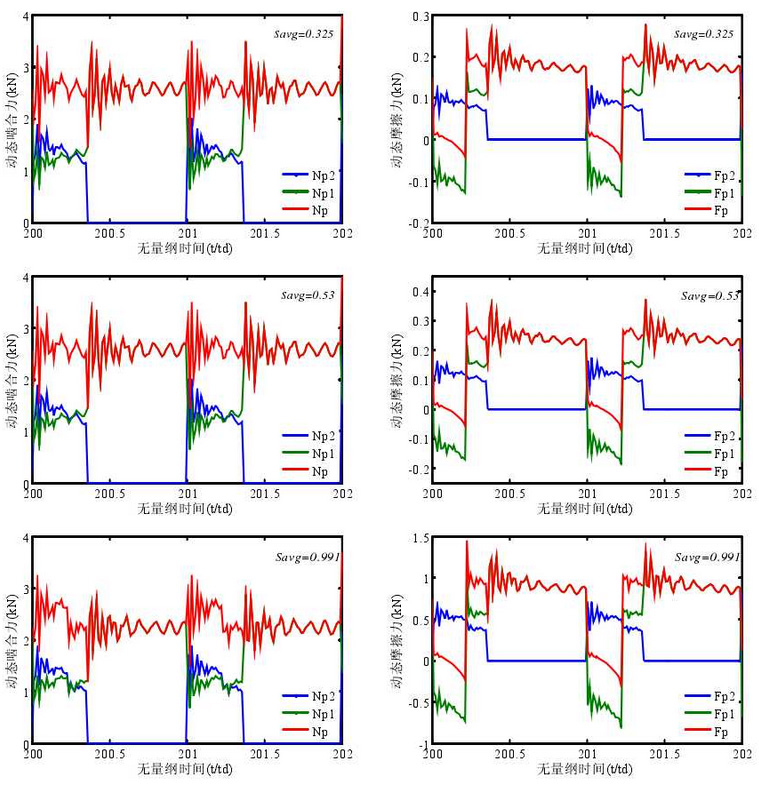
Figure 2 shows that there is obvious periodic change in the dynamic friction force on the tooth surface. In the AC segment, the two teeth have opposite directions and the total friction force cancels each other, while the direction of the friction force on the gear tooth 1 changes at joint C and the total friction force) N K (friction impact occurs when the axial Y of the bearing force increases sharply).At points B and E, the abrupt change in the meshing force causes fluctuations in the friction force.On the whole, the friction force on the tooth surface increases with the increase of the roughness of the tooth surface, because the variation of the friction coefficient is non-linear, and the sudden change of the friction coefficient at point C also aggravates the impact caused by the friction force when the gear meshes through the joint.
3. Dynamic bearing force
Bearing force is the dynamic force formed by the meshing force of the gear transferred to the bearing via the gear-shaft, which ultimately excites the vibration of the box.Figure 3 shows the time-frequency signal of bearing force of pinion in Y-direction, i.e. engagement line direction. It can be seen that the impact excitation of pinion is obvious when the gear is in rodent at time T D and rodent at time T D. However, from the time-domain signal, the change of bearing force amplitude is not obvious, while the frequency-domain signal shows that when the tooth surface roughness increases, the amplitude of low-frequency component increases and the high-frequency component decreases slightly.
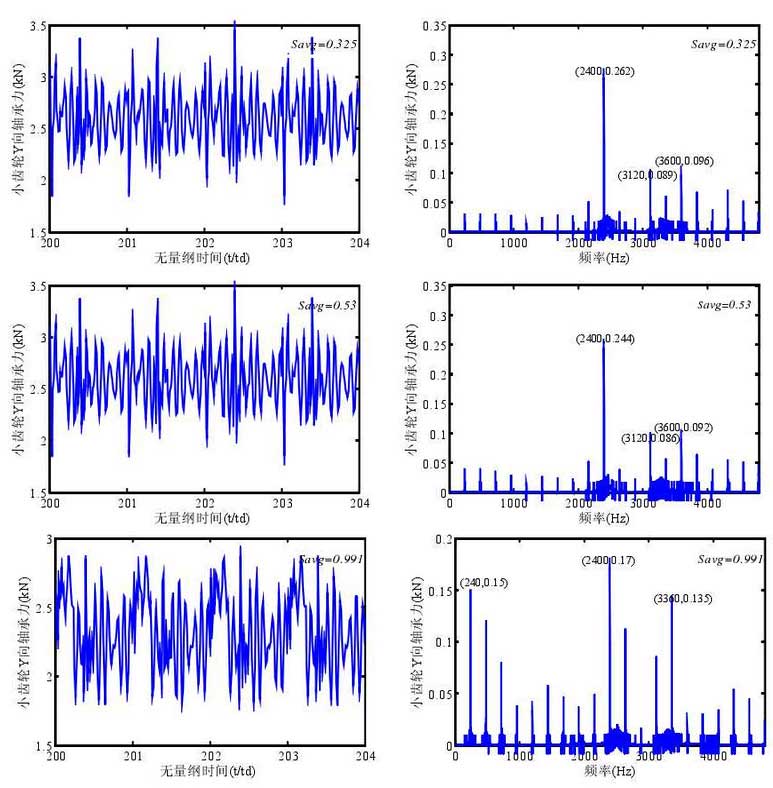
Figure 4 shows the bearing force in the direction of pinion friction force. The time-domain signal shows that the bearing force at the joint forms impact vibration due to the change of friction force and gradually decreases under the action of bearing damping, while the bearing force increases with the increase of tooth surface roughness.In frequency domain, the first three order amplitude of low frequency is larger.It is found that the natural frequency of translation motion is 8517Hz, because the bearing stiffness in both directions is the same, the natural frequencies are shown in Fig. 3 and Fig. 4.
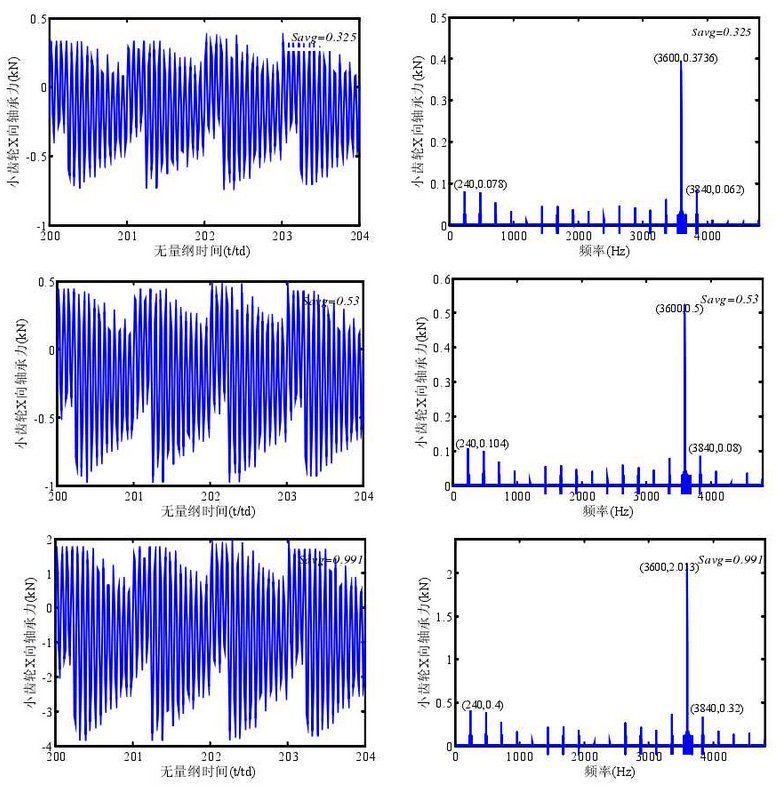
4. Dynamic Transmission Error (DTE)
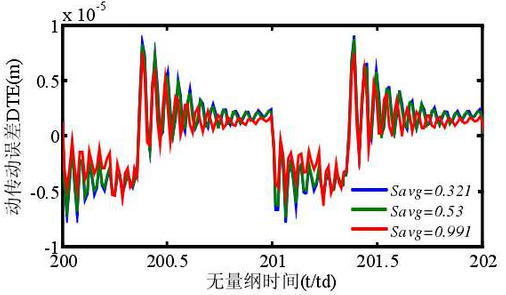
Fig. 5 compares the time-domain signals of dynamic transmission errors with different roughness. It is found that the amplitudes of DTE fluctuate between -7~9um and the impact of tooth surface is obvious. When there is gap between actual teeth, tooth detachment and slapping will occur.Comparing the error magnitude of three cases, it is found that the error decreases with the increase of roughness, especially the magnitude of the first two orders decreases significantly, while the higher order changes little, as shown in Figure 6.
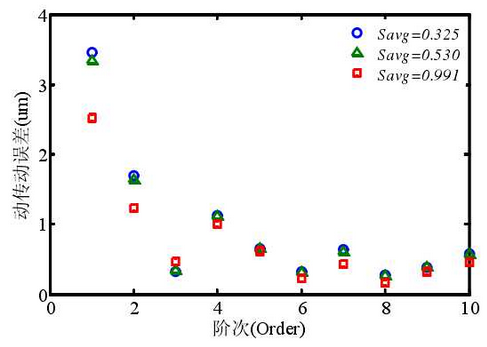
On the one hand, the results indicate that the increase of tooth surface roughness increases the friction force on the tooth surface. When the friction moment is opposite to the driving moment, the friction force restrains the vibration of the gear in the direction of meshing line to a certain extent and thus reduces the generation of dynamic error.In the example of this study, the influence of friction force is more obvious because the period of friction action takes up a longer part of the whole meshing process (about 4/5) for the need of experimental design; on the other hand, the increase of roughness causes the variation of error e(t), which has no obvious influence on dynamic error.It can be seen that the dynamic signal of meshing line direction is not sensitive to the Micro-changes of tooth surface.