According to the characteristics of objective function and planetary gear design, constraints can be divided into flexible constraints and rigid constraints. According to the transmission power and speed, according to the design experience, the approximate range of gear modulus, the selection range of tooth width and the minimum number of teeth to ensure that the undercutting does not occur are estimated as flexible constraints. The adjoining condition, tooth surface contact strength condition and tooth root bending strength condition of planetary gear are rigid constraints.
Flexible constraints:
The maximum modulus is:

The minimum modulus is:

The conditions of no undercutting are as follows

The upper limit of tooth width is:

The lower limit of tooth width is:

Rigid constraint refers to the geometric relationship and strength condition of planetary gear transmission system in normal work and meshing, which usually needs to be derived. Rigid constraints:
The adjoining conditions of planetary gears are as follows:
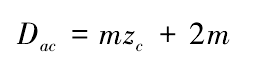
Where, DAC is the diameter of the top circle of planetary gear teeth. Substituting the geometric meshing relationship and related parameters, the expression of proximity condition can be obtained as follows:

The contact strength condition of tooth surface is as follows

The bending strength of tooth root is as follows:
