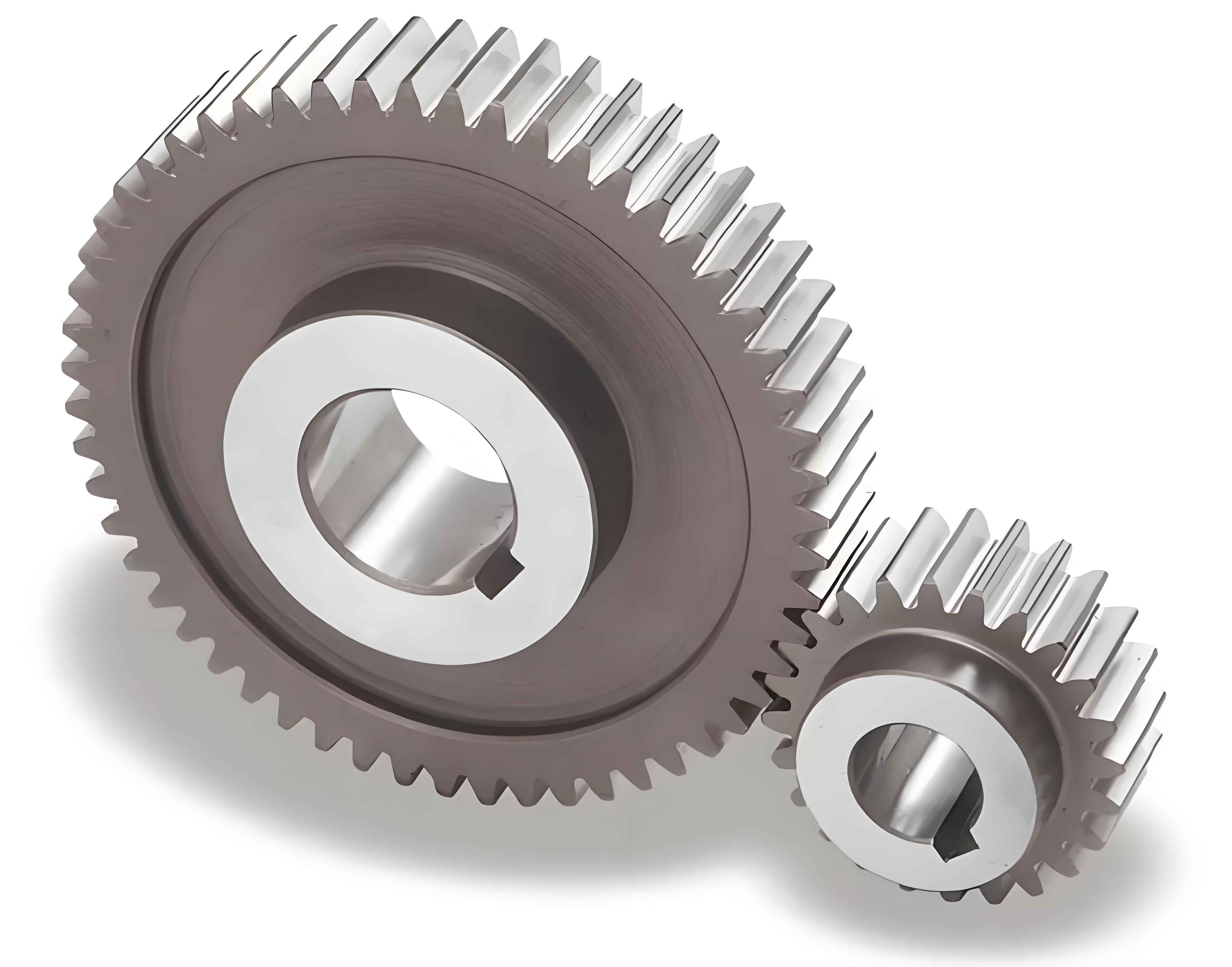
Spur gear is critical components in heavy machinery, providing efficient power transmission and torque conversion. Advances in material science have led to significant improvements in the performance, durability, and efficiency of spur gear. This article explores the latest material science breakthroughs that are transforming spur gear applications in heavy machinery.
Introduction
Spur gear is widely used in heavy machinery due to their simplicity, reliability, and ability to handle high torque loads. However, the harsh operating conditions of heavy machinery, including high loads, variable speeds, and abrasive environments, pose significant challenges to the longevity and performance of spur gear. Material science breakthroughs are addressing these challenges by enhancing the properties of gear materials and introducing innovative coatings and treatments.
Advanced Materials for Spur Gear
1. High-Strength Steels
High-strength steels are traditional materials for spur gear. Recent advancements in metallurgical processes have led to the development of ultra-high-strength steels with improved hardness and fatigue resistance. These materials offer superior performance in heavy-duty applications, reducing the risk of gear failure and extending the operational life of machinery.
2. Composite Materials
Composite materials, combining metals with ceramics or polymers, provide an excellent balance of strength, weight, and durability. The use of composite materials in spur gear can reduce weight and inertia, leading to increased efficiency and reduced wear. Innovations in composite manufacturing techniques, such as additive manufacturing, enable the production of complex gear geometries with optimized material properties.
3. Nano-Structured Materials
Nano-structured materials have unique mechanical properties due to their fine-grained microstructure. These materials exhibit exceptional hardness, wear resistance, and toughness. The application of nano-structured materials in spur gear can significantly enhance their performance, especially in high-load and high-speed conditions. Advances in nano-material synthesis and processing are making these materials more accessible for industrial applications.
Innovative Coatings and Surface Treatments
1. Diamond-Like Carbon (DLC) Coatings
Diamond-like carbon (DLC) coatings are known for their extreme hardness and low friction properties. These coatings can be applied to spur gear surfaces to reduce wear, improve efficiency, and increase resistance to abrasive environments. Recent developments in DLC coating technology have improved adhesion and uniformity, making them more effective for heavy machinery applications.
2. Surface Hardening Techniques
Surface hardening techniques, such as carburizing, nitriding, and induction hardening, enhance the surface properties of spur gear without compromising the toughness of the core material. These treatments create a hard, wear-resistant surface layer that improves gear life and performance. Advances in these techniques, including precision control and process optimization, have led to better consistency and effectiveness in industrial applications.
3. Ceramic Coatings
Ceramic coatings offer excellent thermal stability, wear resistance, and corrosion resistance. The application of ceramic coatings on spur gear can protect them from harsh operating conditions and extend their service life. Innovations in ceramic coating technologies, such as plasma spraying and chemical vapor deposition, allow for precise and uniform application, ensuring optimal protection and performance.
Case Studies and Applications
Case Study 1: Mining Equipment
In the mining industry, spur gear is subjected to extreme loads and abrasive conditions. The adoption of high-strength steels and advanced surface treatments has led to significant improvements in spur gear durability and performance. For example, the use of carburized and nitrided gear in mining equipment has resulted in a 50% increase in operational life and a reduction in maintenance costs.
Case Study 2: Construction Machinery
Construction machinery, such as excavators and bulldozers, rely on spur gear for efficient power transmission. Composite materials and DLC coatings have been successfully implemented in these applications, leading to lighter gear with enhanced wear resistance. This has improved fuel efficiency and reduced downtime due to spur gear failure.
Table: Comparison of Advanced Materials and Coatings for Spur Gear
Material/Coating | Key Properties | Applications | Benefits |
---|---|---|---|
High-Strength Steels | High hardness, fatigue resistance | Heavy-duty gears, mining equipment | Increased durability, reduced failure risk |
Composite Materials | Lightweight, high strength, wear resistance | Construction machinery, automotive gears | Improved efficiency, reduced weight |
Nano-Structured Materials | Exceptional hardness, toughness | High-speed, high-load gears | Enhanced performance, extended service life |
DLC Coatings | Extreme hardness, low friction | Abrasive environments, high-precision gears | Reduced wear, improved efficiency |
Surface Hardening | Hard wear-resistant surface, tough core | General heavy machinery, industrial gears | Improved life span, better performance |
Ceramic Coatings | Thermal stability, corrosion resistance | Harsh environments, chemical processing | Protection from harsh conditions, longevity |
Conclusion
Material science breakthroughs are revolutionizing spur gear applications in heavy machinery. The development of advanced materials, innovative coatings, and surface treatments is enhancing the performance, durability, and efficiency of spur gear. These advancements are not only improving the reliability of heavy machinery but also reducing maintenance costs and downtime, leading to increased productivity and profitability.
By leveraging these material science innovations, industries can achieve better performance and longer life spans for their spur gear, ultimately driving progress and efficiency in heavy machinery applications.