Designing and manufacturing hypoid gears requires careful consideration of various factors to ensure their optimal performance and reliability. Here are some key design and manufacturing considerations for hypoid gears:
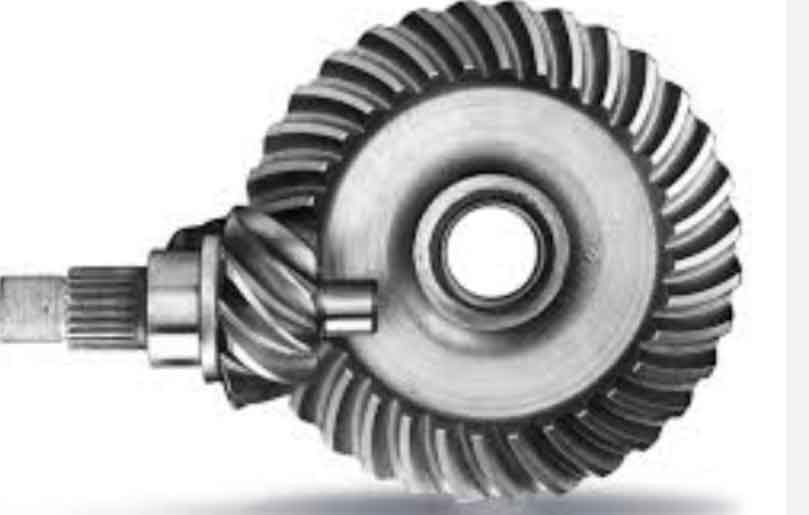
1. Gear Geometry and Tooth Profile:
Hypoid gears have a complex tooth profile that combines elements of helical and spiral bevel gears. The gear geometry should be designed to ensure smooth meshing and proper tooth contact, minimizing friction and wear. Computer-aided design (CAD) software and advanced simulation tools can be used to optimize the tooth profile and gear geometry.
2. Offset and Shaft Angle:
The offset distance and shaft angle between the pinion and gear are critical design parameters in hypoid gears. Properly determining the offset and shaft angle ensures the correct generation of the tooth surfaces and prevents interference during gear meshing.
3. Load Distribution and Torque Capacity:
Hypoid gears are often used in applications with high torque requirements. Designing the gears to distribute the load evenly across the teeth is essential for maximizing the gear’s torque capacity and minimizing stress concentrations.
4. Material Selection:
Choosing the right material for hypoid gears is crucial for ensuring strength, durability, and resistance to wear. Common materials include alloy steels, heat-treated steels, and specialty materials like carburizing and nitriding steels. The material selection should consider the specific application requirements and environmental factors.
5. Heat Treatment and Surface Finish:
Hypoid gears often undergo heat treatment processes, such as carburizing or case hardening, to achieve the desired hardness and wear resistance. Additionally, a high-quality surface finish is essential to reduce friction and improve gear performance.
6. Gear Cutting and Machining Techniques:
Hypoid gears are typically manufactured using specialized gear cutting processes, such as face milling, face hobbing, or face grinding. These processes require precise machinery and skilled operators to achieve the required accuracy and quality of the gear teeth.
7. Quality Control and Inspection:
Rigorous quality control measures should be in place throughout the manufacturing process to ensure that the finished hypoid gears meet the required specifications and performance standards. Non-destructive testing and inspection techniques, such as coordinate measuring machines (CMM), are commonly used to verify gear accuracy.
8. Lubrication and Maintenance:
Proper lubrication is essential for reducing friction and wear in hypoid gears. Lubricant selection should consider the operating conditions and the gear material. Regular maintenance and inspection help to identify potential issues early and ensure the gears’ long-term reliability.
9. Noise and Vibration Analysis:
Hypoid gears can generate noise and vibration during operation. Conducting noise and vibration analysis during the design phase can help identify potential sources of noise and develop measures to mitigate it.
By carefully considering these design and manufacturing factors, engineers can produce high-quality hypoid gears that meet the demands of various applications and deliver efficient and reliable power transmission.