This article focuses on the dynamics analysis of spiral bevel gears, considering out-of-mesh engagement in both steady-state and variable speed transient conditions. In the steady state, the vibration displacement, velocity, and dynamic meshing force show periodic fluctuations, with vibration shocks at the start and end of the meshing cycle. In the variable speed transient state, simulations of the uniform speed change process of the driving wheel reveal larger amplitude and dynamic meshing force fluctuations. The research provides valuable insights for understanding and optimizing the performance of bevel gear transmissions.
1. Introduction
Spiral bevel gears are widely used in various fields such as automobiles, helicopters, and construction machinery due to their large overlap coefficient, ability to change the direction of torque transmission, high load-carrying capacity, and smooth operation with low noise. In the field of bevel gear dynamics analysis, many scholars have made significant progress in establishing models and understanding the factors affecting gear performance. However, some aspects such as the impact of out-of-mesh engagement caused by installation errors and tooth deformation on time-varying meshing stiffness, and the detailed analysis of system responses in variable speed conditions, have not been thoroughly investigated. This study aims to address these gaps by establishing a variable speed model of spiral bevel gears considering out-of-mesh engagement and analyzing the system’s vibration responses under different loads and speeds.
2. Out-of-Mesh Engagement Caused by Tooth Load Deformation
When a gear pair rotates without load, the teeth do not deform, and the meshing line length remains constant, resulting in a theoretical transmission ratio. However, when the gears are loaded, the teeth deform, leading to early entry into meshing and delayed exit from meshing, which is known as out-of-mesh or extended meshing. This phenomenon increases the actual contact ratio of the gear pair. The meshing interval can be divided into three parts for calculating the elastic deformation: before entering the theoretical meshing line (early meshing), within the theoretical meshing area, and after exiting the theoretical meshing area (late meshing). The elastic deformation in each region is calculated based on the position of the teeth on the actual meshing line.
3. Dynamics of Spiral Bevel Gear Pairs
A concentrated parameter method is used to establish an eight-degree-of-freedom torsional vibration model of spiral bevel gears. The model considers the transverse, axial, and torsional vibrations along the XYZ axes. The normal force and the forces and moments in each coordinate direction of the meshing gear are expressed in terms of time-varying meshing stiffness and meshing damping. The differential equations of the model are derived, and they can be represented in matrix form. By introducing state variables, the equations are transformed into a 16-degree-of-freedom first-order differential equation system.
4. Examples
4.1 Steady-State Condition
Taking a pair of spiral bevel gears in a helicopter’s first-stage reducer as an example, with specific gear parameters, the dynamic responses of the system in the steady state are analyzed. By setting appropriate initial values and using software functions, the time-varying displacements, velocities, dynamic transmission errors, and dynamic meshing forces in the coordinate directions are obtained. The results show that there are larger vibration shocks at the start and end of the meshing cycle. The axial vibration displacement in the z direction is the largest, and the vibration displacements and velocities on the driving and driven wheels show a high degree of consistency in the changing trend. In the frequency domain, the main amplitude of the dynamic meshing force is at the meshing frequency and its multiples, with the maximum amplitude at 5 times the meshing frequency. The dynamic load coefficient of the gear pair also shows a characteristic curve that rises rapidly with the increase of discrete rotational speed and then fluctuates.
4.2 Variable Speed Transient Condition
In the variable speed transient condition, with a constant load on the driven wheel, the angular velocity of the driving wheel increases uniformly from 0 to 5000 r/min. By taking appropriate initial values and simulating the calculation of the dynamic meshing force, it is found that compared with the steady state, the amplitude of the dynamic meshing force in the meshing process of the spiral bevel gear pair shows significant fluctuations, but there is no disengagement phenomenon.
5. Tables for Summary
Condition | Vibration Characteristics | Meshing Force Characteristics |
---|---|---|
Steady State | Periodic fluctuations, larger shocks at start and end of meshing cycle | Main amplitude at meshing frequency and multiples, maximum at 5 times meshing frequency |
Variable Speed Transient | Larger amplitude fluctuations compared to steady state | Significant fluctuations in amplitude |
6. Conclusion
This study establishes a variable speed transmission dynamics model of spiral bevel gears considering out-of-mesh engagement and analyzes the system’s dynamic responses in steady-state and transient conditions. In the steady state, the vibration displacement and dynamic meshing force show periodic fluctuations, and in the variable speed transient state, the model is verified to be applicable to the speed change process, and the system speed change causes larger amplitude and dynamic meshing force fluctuations. The research findings contribute to a better understanding of the behavior of spiral bevel gears and can be used for optimizing their design and performance in practical applications.
7. Images for Illustration
In Figure 1, we can observe the normal plane meshing line when the gears are unloaded. This provides a clear visual understanding of the theoretical meshing state before any deformation occurs. It shows the positions of the theoretical meshing points A and B, which are crucial for understanding the subsequent changes in meshing due to load.
Figure 2 depicts the normal plane meshing line after the gears are loaded. Here, we can clearly see the phenomenon of out-of-mesh engagement. Due to the deformation of the teeth, the actual meshing region extends beyond the theoretical one. The early entry of some teeth into meshing and the delayed exit of others are evident, which directly affects the meshing stiffness and dynamic behavior of the gear pair.
For the vibration analysis, we can have a series of graphs. For example, a graph showing the vibration displacement in different directions over time can help us understand how the gears vibrate during operation. The x-axis could represent time, and the y-axis could represent the displacement in a particular direction (such as x, y, or z direction). We would expect to see periodic fluctuations in the displacement, with larger peaks and troughs corresponding to the start and end of the meshing cycle as observed in the actual results.
Another important image could be the frequency domain analysis of the dynamic meshing force. This graph would show the amplitudes of the dynamic meshing force at different frequencies. We would see a prominent peak at the meshing frequency (1916Hz) and its multiples, with the highest peak at 5 times the meshing frequency. This visual representation helps in understanding the frequency components that dominate the dynamic meshing force and how they vary with different operating conditions.
In the case of the variable speed transient condition, an image of the angular velocity of the driving wheel as a function of time would be useful. It would show a steadily increasing curve from 0 to 5000 r/min, demonstrating the uniform speed change process. Alongside this, a graph of the dynamic meshing force during this variable speed process would show the significant fluctuations in amplitude compared to the steady-state condition. This would emphasize the impact of speed changes on the dynamic behavior of the gear pair.
8. Expanding on the Introduction
Spiral bevel gears play a crucial role in many mechanical systems. Their unique geometric and mechanical properties make them suitable for applications where high torque transmission and smooth operation are required. In the automotive industry, they are used in the differential gears to distribute power between the wheels while allowing for different rotational speeds during cornering. In helicopters, they are an essential part of the transmission system, transmitting power from the engine to the rotor blades. In construction machinery, they are used in various drive systems to handle heavy loads.
The study of bevel gear dynamics has evolved over the years. Initially, researchers focused on establishing basic models that considered simple factors such as gear geometry and material properties. As the understanding of gear behavior improved, more complex factors such as tooth flexibility, meshing stiffness variation, and the presence of clearances were incorporated into the models. However, there are still challenges in accurately predicting the behavior of bevel gears under all operating conditions.
One of the main challenges is the accurate representation of out-of-mesh engagement. This phenomenon is not only affected by the load on the gears but also by factors such as manufacturing tolerances, installation errors, and thermal expansion. These factors can cause variations in the tooth contact patterns and meshing stiffness, which in turn affect the vibration and noise characteristics of the gear pair. Another challenge is the analysis of the system’s response in variable speed conditions. In real-world applications, gears often operate at different speeds, and the dynamic behavior during speed changes can have a significant impact on the overall performance and reliability of the system.
9. Detailed Explanation of Out-of-Mesh Engagement
When a gear pair is in operation, the teeth are subjected to various forces. Under load, the teeth deform, and this deformation can be divided into different components depending on the location of the tooth on the meshing line. In the region before entering the theoretical meshing line (early meshing), the deformation is caused by the approaching of the teeth towards each other before the expected meshing point. This early contact can lead to an increase in the contact force and a change in the meshing stiffness.
Within the theoretical meshing area, the deformation is influenced by the normal load and the relative motion between the teeth. The meshing stiffness in this region also varies depending on the position of the teeth and the load distribution. After exiting the theoretical meshing area (late meshing), the teeth continue to deform as they separate from each other. This late deformation can cause additional vibrations and affect the overall dynamic behavior of the gear pair.
To accurately calculate the elastic deformation in each region, we need to consider the geometry of the gears, the material properties, and the load conditions. The meshing line length, the angle of the teeth, and the radius of the base circle all play a role in determining the deformation. For example, a larger meshing line length may result in a greater potential for deformation, especially if the teeth are subjected to high loads. The material properties such as the modulus of elasticity and the Poisson’s ratio affect the ability of the teeth to deform under load. A stiffer material will have less deformation for the same load compared to a more flexible material.
10. In-depth Analysis of Spiral Bevel Gear Pairs Dynamics
The eight-degree-of-freedom torsional vibration model of spiral bevel gears provides a comprehensive framework for analyzing the dynamic behavior of the gear pair. The model takes into account the transverse, axial, and torsional vibrations along the XYZ axes. These different types of vibrations interact with each other and are affected by factors such as the meshing stiffness, meshing damping, and the external loads.
The transverse vibrations occur in the direction perpendicular to the gear axis. They can be caused by unbalanced forces, misalignments, or the dynamic meshing forces. The axial vibrations occur along the axis of the gear and are often related to the thrust forces generated during meshing. The torsional vibrations involve the rotation of the gears around their axes and are affected by the torque transmitted and the torsional stiffness of the system.
The normal force acting on the meshing gear is a key factor in determining the dynamic behavior. It is related to the meshing stiffness and the deformation of the teeth. The meshing stiffness, which is time-varying, depends on the position of the teeth on the meshing line and the load conditions. As the teeth move along the meshing line, the meshing stiffness changes, leading to variations in the dynamic meshing force. The meshing damping also plays an important role in dissipating energy and reducing vibrations. A higher damping value can help to stabilize the system and reduce the amplitude of vibrations.
The differential equations of the model describe the relationship between the accelerations, velocities, and displacements of the gear system. These equations are derived based on the principles of mechanics and take into account the forces and moments acting on the gears. By representing the equations in matrix form, we can use numerical methods to solve for the unknown variables and analyze the dynamic behavior of the system. The transformation into a 16-degree-of-freedom first-order differential equation system allows for more accurate and detailed analysis.
11. Further Discussion on Examples
11.1 Steady-State Condition – Vibration Displacement
In the steady-state condition, the vibration displacement of the gear pair shows interesting characteristics. The periodic fluctuations in displacement are related to the meshing cycle of the gears. As the teeth engage and disengage, the forces acting on the gears change, leading to vibrations. The larger vibration shocks at the start and end of the meshing cycle can be attributed to the sudden changes in the contact force and meshing stiffness. At these points, the teeth are either just starting to engage or are about to disengage, and the transition between different meshing states causes a significant impact on the vibration.
The z-direction axial vibration displacement being the largest can be explained by the thrust forces generated during meshing. These thrust forces are more pronounced in the z-direction, especially for spiral bevel gears where the tooth geometry and meshing angles can lead to a significant component of the force in this direction. The consistency in the vibration displacements and velocities on the driving and driven wheels indicates that the gears are operating in a coupled manner. The forces and deformations on one gear are transmitted to the other gear, resulting in a similar dynamic behavior.
11.2 Steady-State Condition – Dynamic Meshing Force
In the frequency domain analysis of the dynamic meshing force, the presence of peaks at the meshing frequency and its multiples is a significant finding. The meshing frequency is determined by the rotational speed of the gears and the number of teeth. The fact that the main amplitude is concentrated at these frequencies suggests that the dynamic meshing force is strongly influenced by the meshing process itself. The maximum amplitude at 5 times the meshing frequency may be due to a combination of factors such as the resonance effects within the gear system, the interaction between different frequency components, and the specific geometry and loading conditions of the gears.
The dynamic load coefficient curve provides additional insights into the behavior of the gear pair under different rotational speeds. The rapid rise in the curve with increasing rotational speed indicates that the dynamic forces acting on the gears increase significantly. This is because as the speed increases, the frequency of meshing also increases, leading to higher dynamic forces. The subsequent fluctuations in the curve may be due to the complex interaction between different factors such as the variation in meshing stiffness, the presence of clearances, and the damping effects.
11.3 Variable Speed Transient Condition – Angular Velocity and Dynamic Meshing Force
In the variable speed transient condition, the steadily increasing angular velocity of the driving wheel from 0 to 5000 r/min is a key feature. This uniform speed change process is an important aspect of the model’s verification. It shows that the model can accurately represent the speed change behavior of the gears. The significant fluctuations in the dynamic meshing force amplitude during this process are due to the changing meshing conditions. As the speed changes, the meshing frequency, meshing stiffness, and the forces acting on the gears all change, leading to fluctuations in the dynamic meshing force. The absence of a disengagement phenomenon indicates that the model is able to maintain the integrity of the meshing process during speed changes, which is crucial for the reliable operation of the gear pair.
12. Tables for More Detailed Summary
Condition | Vibration Displacement Characteristics | Meshing Force Frequency Characteristics | Dynamic Load Coefficient Characteristics |
---|---|---|---|
Steady State | Periodic fluctuations, larger shocks at start and end of meshing cycle, z-direction axial vibration displacement largest | Main amplitude at meshing frequency and multiples, maximum at 5 times meshing frequency | Rapid rise with increasing rotational speed, then fluctuations |
Variable Speed Transient | Larger amplitude fluctuations compared to steady state | Significant fluctuations in amplitude during speed change | N/A (not applicable as focus is on amplitude fluctuations of meshing force) |
Gear Component | Transverse Vibration Influencing Factors | Axial Vibration Influencing Factors | Torsional Vibration Influencing Factors |
---|---|---|---|
Spiral Bevel Gear Pair | Unbalanced forces, misalignments, dynamic meshing forces | Thrust forces generated during meshing | Torque transmitted, torsional stiffness of system |
13. Conclusion and Future Perspectives
This study has made significant contributions to the understanding of spiral bevel gear dynamics, particularly considering out-of-mesh engagement in variable speed conditions. The established model and the analysis of different operating conditions have provided valuable insights into the vibration and meshing force characteristics of the gear pair.
In the future, further research could focus on improving the accuracy of the model. This could involve incorporating more detailed models of tooth deformation, considering the effects of thermal expansion and contraction, and improving the representation of manufacturing tolerances. Additionally, experimental validation of the model could be carried out to verify the accuracy of the predicted results. This would involve conducting tests on actual gear pairs under different operating conditions and comparing the measured data with the predicted values from the model.
Another area of future research could be the optimization of gear design based on the dynamic analysis. By understanding the factors that affect the dynamic behavior of the gears, designers could make more informed decisions about gear geometry, material selection, and operating conditions. This could lead to the development of more efficient and reliable gear systems for various applications.
Overall, the study of spiral bevel gear dynamics is an ongoing area of research with significant potential for improving the performance and reliability of mechanical systems that rely on these gears.
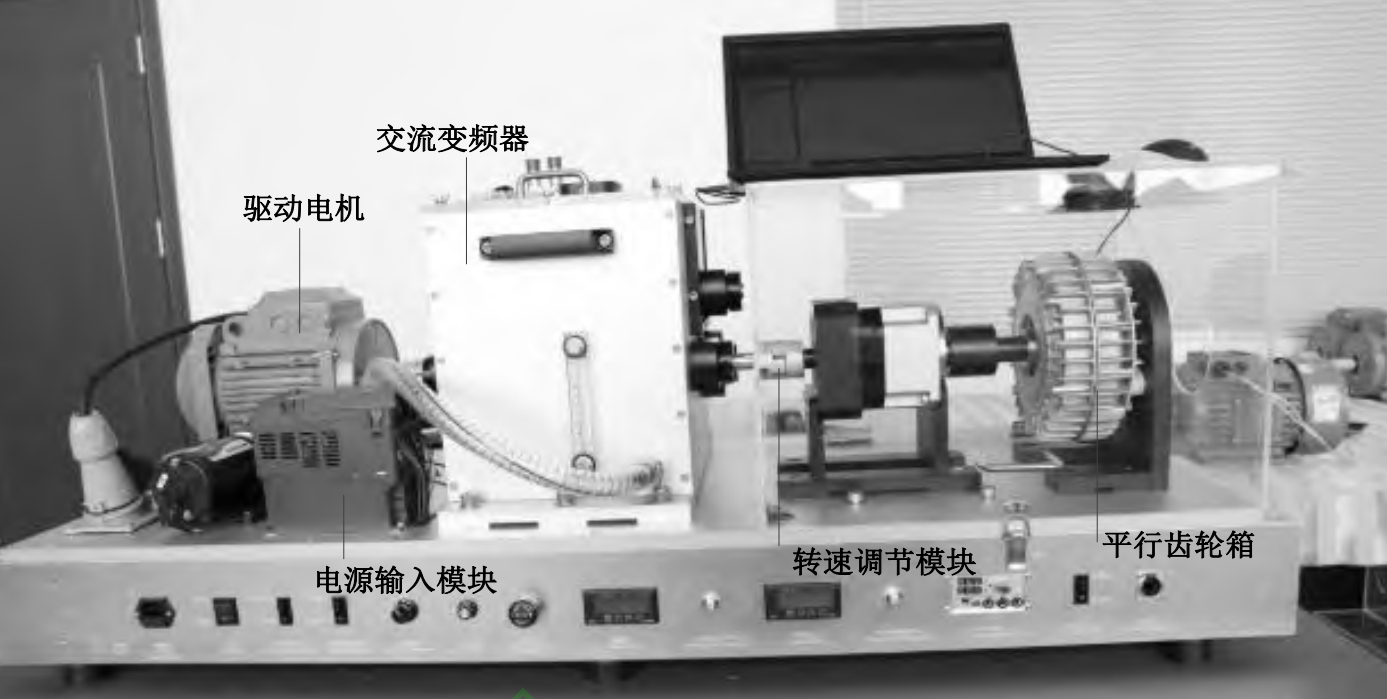