Introduction
Gear Shafts are critical components in both aerospace and electric vehicle (EV) applications. They play a vital role in transmitting power, ensuring smooth operation, and enhancing the overall efficiency of mechanical systems. The performance requirements for Gear Shafts in these industries are stringent due to the demanding operational environments. This article delves into the specific applications of Gear Shafts in aerospace and electric vehicles, highlighting the materials used, design considerations, and the unique challenges faced.
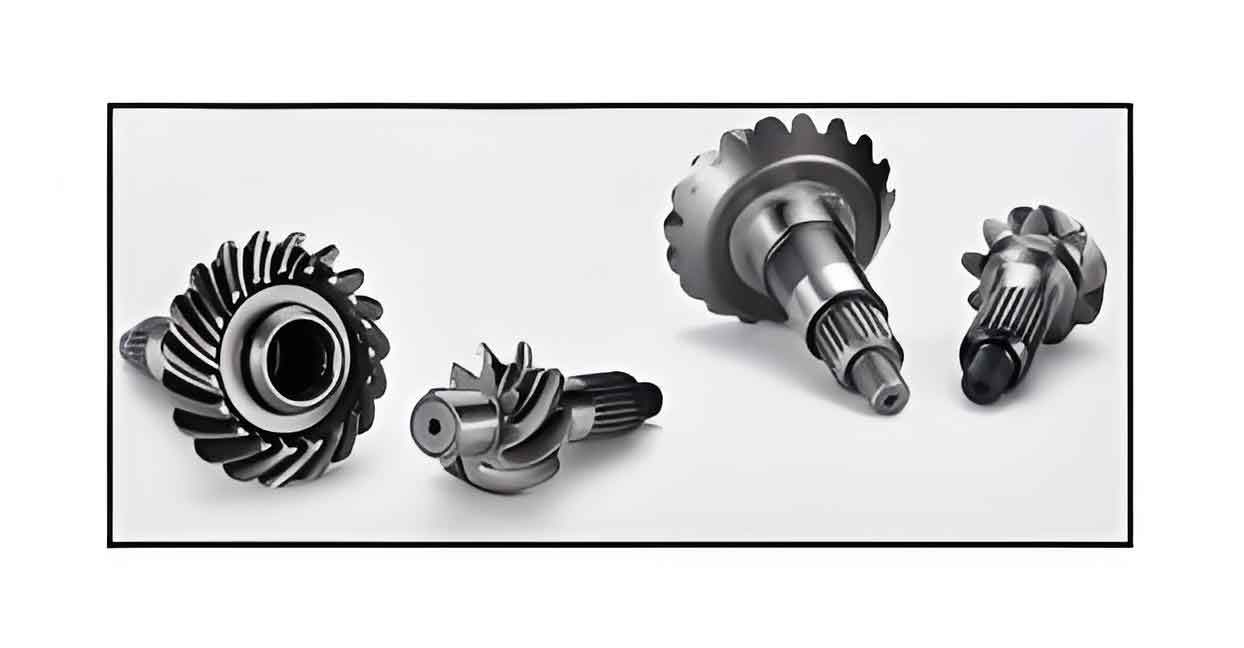
Importance of Gear Shafts in Aerospace and Electric Vehicles
- Power Transmission: Gear Shafts are essential for transmitting mechanical power from one component to another.
- Efficiency: Properly designed and manufactured Gear Shafts ensure the efficient operation of mechanical systems.
- Reliability: High-performance Gear Shafts contribute to the reliability and longevity of aerospace and electric vehicle (EV) systems.
- Safety: In aerospace, reliable Gear Shafts are critical for ensuring the safety of flights, while in electric vehicle (EV), they are essential for safe and efficient vehicle operation.
Gear Shafts in Aerospace Applications
Key Requirements for Aerospace Gear Shafts
- High Strength-to-Weight Ratio: Aerospace applications demand materials that offer high strength while being lightweight.
- Corrosion Resistance: Gear Shafts must withstand harsh environmental conditions, including exposure to varying temperatures and corrosive elements.
- Fatigue Resistance: Aerospace Gear Shafts are subjected to cyclic loading and must exhibit high fatigue resistance.
- Precision: High precision in manufacturing is crucial to ensure smooth and reliable operation.
Common Materials Used
Titanium Alloys:
- High strength-to-weight ratio.
- Excellent corrosion resistance.
- High fatigue resistance.
- Expensive and challenging to machine.
Nickel Alloys:
- High strength and toughness.
- Excellent high-temperature performance.
- Good corrosion resistance.
- Used in high-stress and high-temperature environments.
High-Strength Steels:
- High tensile strength.
- Good machinability.
- Cost-effective compared to titanium and nickel alloys.
- Requires protective coatings for corrosion resistance.
Design Considerations
- Weight Optimization: Reducing the weight of Gear Shafts without compromising strength is a primary focus.
- Surface Treatments: Applying coatings or treatments to enhance wear and corrosion resistance.
- Precision Manufacturing: Ensuring tight tolerances and high precision during manufacturing to meet aerospace standards.
Gear Shafts in Electric Vehicle Applications
Key Requirements for Electric Vehicle (EV) Gear Shafts
- Efficiency: Gear Shafts must contribute to the overall efficiency of the electric drivetrain.
- Durability: Long-lasting performance to match the lifecycle of electric vehicles.
- Noise and Vibration: Minimizing noise and vibration for a smooth and quiet ride.
- Weight Reduction: Lightweight materials to improve vehicle range and efficiency.
Common Materials Used
Aluminum Alloys:
- Lightweight.
- Good machinability.
- Adequate strength for certain applications.
- Lower wear resistance compared to steels.
High-Strength Steels:
- High tensile strength and durability.
- Good wear resistance.
- Heavier than aluminum alloys.
Composites:
- Extremely lightweight.
- High strength-to-weight ratio.
- Complex manufacturing processes.
- Costly.
Design Considerations
- Thermal Management: Efficient heat dissipation to prevent overheating.
- Lubrication: Adequate lubrication to reduce friction and wear.
- Noise Reduction: Design modifications to minimize gear noise and ensure a quiet ride.
Comparative Analysis of Gear Shaft Materials
Property | Titanium Alloys | Nickel Alloys | High-Strength Steels | Aluminum Alloys | Composites |
---|---|---|---|---|---|
Strength-to-Weight Ratio | Excellent | Good | Moderate | Good | Excellent |
Corrosion Resistance | Excellent | Excellent | Moderate | Moderate | Excellent |
Fatigue Resistance | High | High | High | Moderate | High |
Machinability | Challenging | Challenging | Good | Excellent | Complex |
Cost | High | High | Moderate | Low | High |
Unique Challenges in Aerospace and Electric Vehicle (EV) Applications
Aerospace Challenges
- Extreme Conditions: Gear Shafts must perform reliably under extreme temperatures and pressure variations.
- Weight Constraints: Every component must be optimized for minimal weight to improve aircraft efficiency.
- Regulatory Compliance: Aerospace components must adhere to strict regulatory standards and undergo rigorous testing.
Electric Vehicle (EV) Challenges
- Range Optimization: Reducing the weight of Gear Shafts contributes to the overall range of the vehicle.
- Integration with Electric Drivetrains: Gear Shafts must be compatible with the unique requirements of electric drivetrains.
- Noise and Vibration Control: Ensuring smooth and quiet operation is essential for consumer satisfaction.
Conclusion
The selection of materials and design of Gear Shafts are critical factors that influence the performance, efficiency, and reliability of aerospace and electric vehicle systems. Aerospace applications prioritize high strength-to-weight ratios, corrosion resistance, and fatigue resistance, while electric vehicle (EV) applications focus on efficiency, durability, and noise reduction. By understanding the specific requirements and challenges of each application, engineers can make informed decisions to optimize the performance and longevity of Gear Shafts in these advanced technological fields.
4o