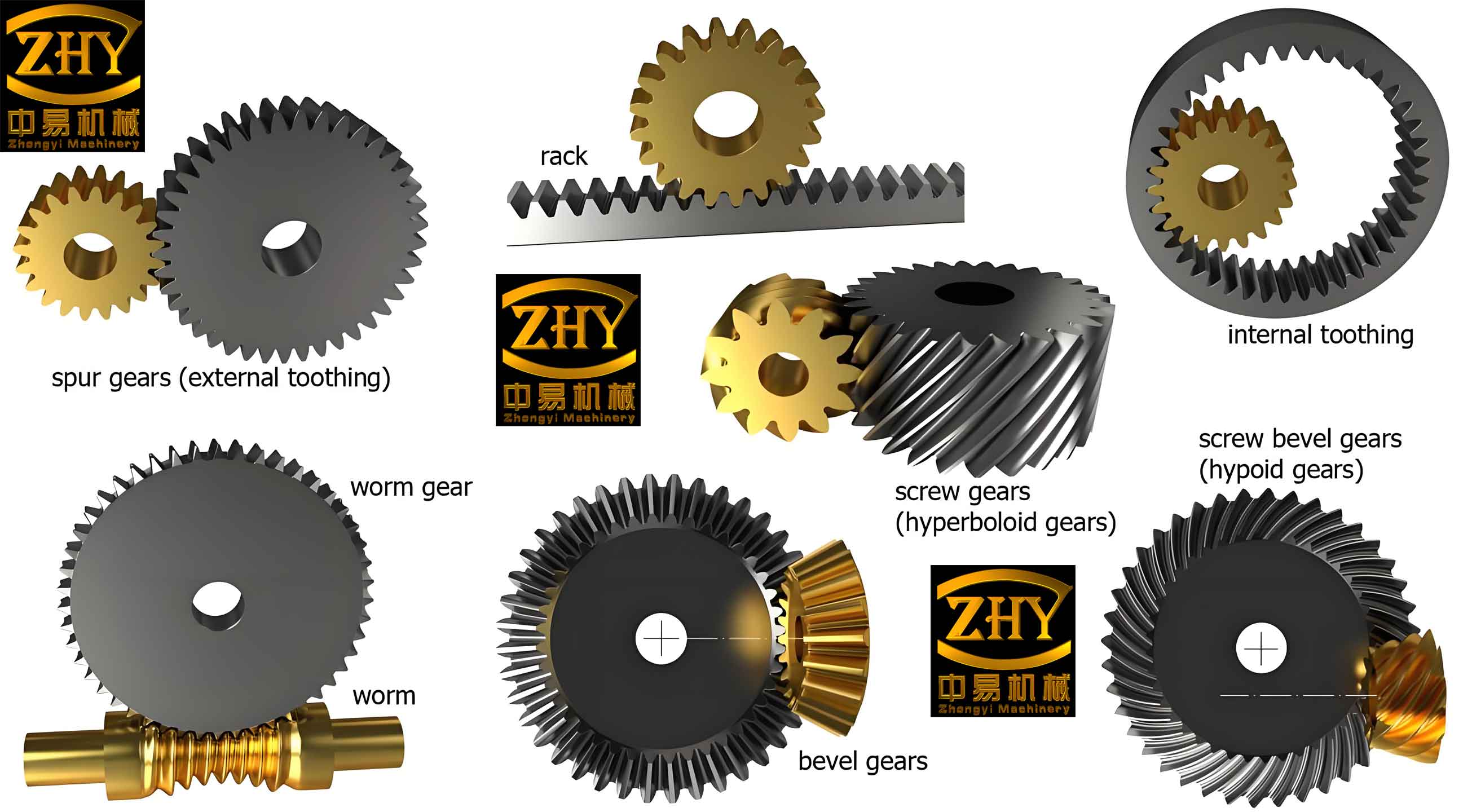
Introduction
Screw gear transmission systems are widely used in industrial applications due to their ability to transmit high torques smoothly and efficiently. However, energy efficiency in these systems is crucial for reducing operational costs and environmental impact. This article explores various strategies for improving the energy efficiency of screw gear transmission systems, focusing on design optimization, material selection, lubrication, and maintenance practices.
Importance of Energy Efficiency
Improving the energy efficiency of screw gear transmission systems offers several benefits, including reduced energy consumption, lower operational costs, and decreased greenhouse gas emissions. Efficient systems also tend to have longer lifespans and require less maintenance, further contributing to cost savings and sustainability.
Factors Influencing Energy Efficiency
Several factors influence the energy efficiency of screw gear transmission systems:
- Gear Geometry
- Material Properties
- Lubrication
- Operating Conditions
- Manufacturing Precision
Gear Geometry
The geometry of screw gear, including tooth profile, helix angle, and contact ratio, plays a significant role in determining the efficiency of power transmission. Optimized geometry reduces frictional losses and enhances load distribution.
Material Properties
High-quality materials with low friction coefficients and good wear resistance contribute to higher efficiency by reducing energy losses due to friction and wear.
Lubrication
Proper lubrication minimizes friction between gear teeth, reducing energy losses and wear. Advanced lubricants with additives can further enhance efficiency by reducing friction and improving load-carrying capacity.
Operating Conditions
Operating conditions, such as load, speed, and temperature, affect the efficiency of screw gear systems. Optimizing these conditions ensures minimal energy losses and consistent performance.
Manufacturing Precision
Precision manufacturing ensures accurate gear geometry and smooth surfaces, reducing friction and improving efficiency. Advanced techniques like CNC machining and additive manufacturing enable high precision and customization.
Strategies for Improving Energy Efficiency
Design Optimization
Optimizing the design of screw gear involves refining geometric parameters to minimize friction and improve load distribution. This can be achieved through analytical calculations, computer-aided design (CAD), and finite element analysis (FEA).
Key Design Parameters
- Tooth Profile: Optimizing the tooth profile to achieve smooth engagement and minimal friction.
- Helix Angle: Adjusting the helix angle to balance load distribution and reduce sliding friction.
- Contact Ratio: Increasing the contact ratio to distribute the load over more teeth, reducing stress and friction.
Table 1: Key Design Parameters for Energy Efficiency
Parameter | Optimization Strategy | Impact on Efficiency |
---|---|---|
Tooth Profile | Smooth engagement, minimal friction | Reduced energy losses |
Helix Angle | Balance load distribution, reduce sliding friction | Improved power transmission |
Contact Ratio | Distribute load over more teeth | Lower stress, reduced friction |
Material Selection
Selecting materials with low friction coefficients and high wear resistance enhances efficiency by reducing frictional losses. Advanced materials like alloy steels, ceramics, and composites offer superior performance in screw gear applications.
Benefits of Advanced Materials
- Alloy Steels: High strength and good wear resistance.
- Ceramics: Low friction coefficient and excellent wear resistance.
- Composites: Lightweight, high strength, and low friction.
Lubrication
Using high-performance lubricants with friction-reducing additives significantly improves energy efficiency. Ensuring proper lubrication regimes, such as oil bath, oil mist, or grease lubrication, reduces friction and wear.
Advanced Lubrication Techniques
- Synthetic Oils: Offer superior performance at high temperatures and loads.
- Solid Lubricants: Provide lubrication in extreme conditions where liquid lubricants fail.
- Nano-lubricants: Enhance load-carrying capacity and reduce friction at the nanoscale.
Table 2: Comparison of Lubrication Techniques
Lubrication Technique | Description | Efficiency Improvement |
---|---|---|
Synthetic Oils | High-performance oils with additives | Superior high-temperature performance |
Solid Lubricants | Lubrication in extreme conditions | Reduced friction and wear |
Nano-lubricants | Nanoparticle additives for enhanced lubrication | Higher load-carrying capacity, reduced friction |
Operating Conditions
Optimizing operating conditions such as load, speed, and temperature ensures efficient performance of screw gear systems. Maintaining optimal conditions prevents excessive wear and energy losses.
Optimal Operating Conditions
- Load: Ensuring that screw gear operate within their design load limits.
- Speed: Maintaining appropriate speed to minimize friction and wear.
- Temperature: Keeping operating temperatures within optimal ranges to prevent thermal degradation of materials and lubricants.
Maintenance Practices
Regular maintenance and condition monitoring are essential for sustaining the energy efficiency of screw gear systems. Predictive maintenance techniques, such as vibration analysis and oil analysis, help detect early signs of wear and prevent catastrophic failures.
Key Maintenance Practices
- Regular Inspections: Identifying wear and damage early.
- Condition Monitoring: Using sensors and analytical tools to monitor gear performance.
- Timely Lubrication: Ensuring proper lubrication levels and schedules.
Table 3: Maintenance Practices for Energy Efficiency
Practice | Description | Benefits |
---|---|---|
Regular Inspections | Early identification of wear and damage | Prevents catastrophic failures |
Condition Monitoring | Sensors and analytical tools for performance monitoring | Sustains efficient operation |
Timely Lubrication | Proper lubrication levels and schedules | Reduces friction and wear |
Case Study: Energy Efficiency Improvement in an Industrial Screw Gear System
Initial Assessment
An industrial screw gear system in a manufacturing plant was identified for energy efficiency improvement. The system exhibited high energy consumption and frequent maintenance issues due to wear and friction.
Analysis and Optimization
- Design Optimization: FEA was used to optimize the tooth profile and helix angle, resulting in reduced friction and improved load distribution.
- Material Upgrade: The screw gear were manufactured from a high-strength alloy steel with a low friction coefficient and good wear resistance.
- Advanced Lubrication: Synthetic oil with nano-additives was introduced to enhance lubrication and reduce friction.
- Operating Conditions: Load and speed were optimized to maintain efficient operation within design limits.
- Maintenance Practices: A condition monitoring system was installed to track gear performance and ensure timely maintenance.
Results
The optimized screw gear system demonstrated significant improvements:
- Energy Consumption: Reduced by 15%
- Maintenance Frequency: Decreased by 20%
- Operational Efficiency: Increased by 12%
- Gear Lifespan: Extended by 25%
Table 4: Comparison of Initial and Optimized Gear System Performance
Parameter | Initial System | Optimized System |
---|---|---|
Energy Consumption | High | Reduced by 15% |
Maintenance Frequency | Frequent | Decreased by 20% |
Operational Efficiency | Moderate | Increased by 12% |
Gear Lifespan | Standard | Extended by 25% |
Future Trends in Energy Efficiency
Smart Manufacturing Technologies
The integration of smart manufacturing technologies, such as the Internet of Things (IoT) and artificial intelligence (AI), allows for real-time monitoring and optimization of screw gear systems, enhancing energy efficiency.
Benefits of Smart Technologies
- Real-time Monitoring: Continuous tracking of performance and early detection of issues.
- Predictive Maintenance: AI-driven insights for timely maintenance actions.
- Adaptive Optimization: Dynamic adjustment of operating conditions for optimal efficiency.
Advanced Materials and Coatings
The development of new materials and coatings with superior wear resistance and low friction properties continues to drive improvements in screw gear efficiency.
Emerging Materials and Coatings
- Diamond-like Carbon (DLC) Coatings: Exceptional hardness and low friction.
- Graphene-based Lubricants: High thermal stability and excellent lubrication properties.
Table 5: Future Trends in Gear Efficiency
Trend | Description | Potential Benefits |
---|---|---|
Smart Manufacturing | IoT and AI for real-time monitoring and optimization | Enhanced energy efficiency, reduced downtime |
Advanced Materials | New materials with superior properties | Improved wear resistance, reduced friction |
Advanced Coatings | Innovative coatings for enhanced performance | Longer lifespan, higher efficiency |
Conclusion
Improving the energy efficiency of screw gear transmission systems is essential for reducing operational costs, minimizing environmental impact, and enhancing system performance. By focusing on design optimization, material selection, lubrication, and maintenance practices, significant efficiency gains can be achieved. Future advancements in smart manufacturing technologies and advanced materials will further drive improvements in screw gear efficiency, ensuring sustainable and cost-effective operation of industrial systems.