According to the structural characteristics of each component in the system, a multi degree of freedom equivalent dynamic model of the sealed rotor system is established by using the lumped parameter method to analyze the dynamic characteristics of the rotor system with seal.
According to the analysis, there are three degrees of freedom in the motion of the rotor, which are the translation degrees of freedom in the vertical and horizontal directions and the rotational degrees of freedom around its own rotation axis. Because the seal is fixed with the base, there are only two degrees of freedom, that is, the translation degrees of freedom in the vertical and horizontal directions. In this paper, considering that there are many factors affecting the system, the following assumptions are made for the sealing rotor system before establishing the dynamic model
(1) The axial displacement of the rotor and the seal can be ignored because of the device that limits the movement of the rotor and the seal in the axial direction, that is, the seal and the rotor only move or deform in the radial direction.
(2) Because of the coating on the surface of the rotor contacting with the seal, the friction between the two can be ignored. Therefore, the friction between the rotor and the seal will not be considered in the model.
(3) Because the radial displacement of the rotor causes the radial deformation of the finger tip beam, it can be assumed that the finger tip beam on the seal plate moves synchronously under the excitation of the rotor.
(4) In the system studied, the bearings supporting parts are deep groove ball bearings, so the influence of oil film force on the system is not considered.
(5) Because the seal is a multi-layer structure, and there will be relative motion between layers, but its impact on the overall system is very small, so the coupling effect of stiffness and damping is ignored.
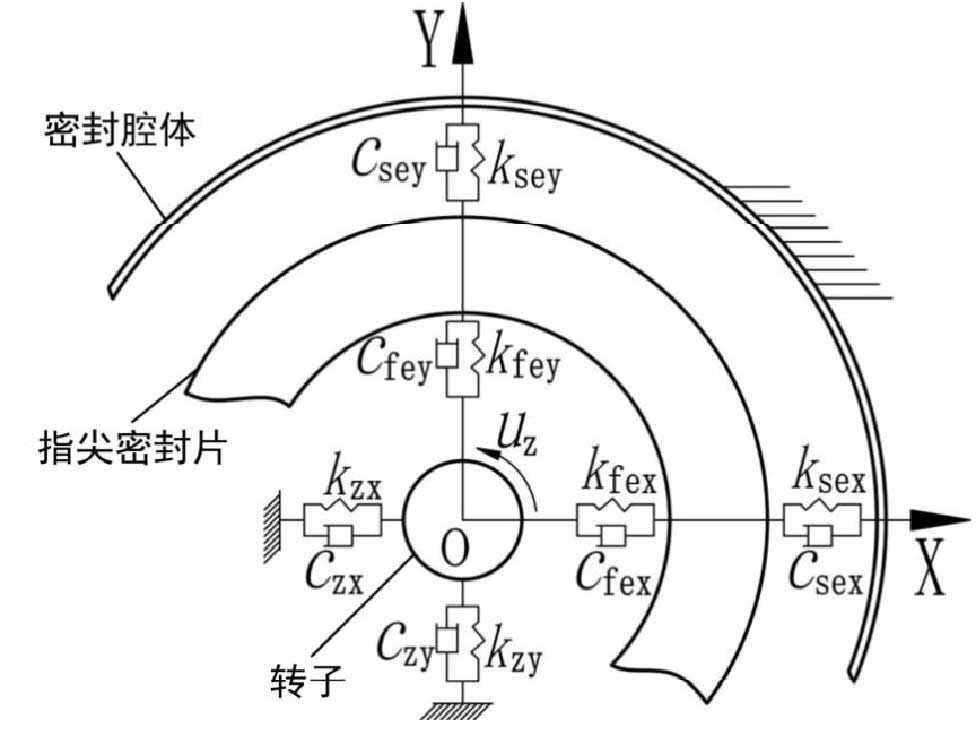
As shown in the figure is the dynamic model of the sealing rotor system established in this paper. Considering the different degrees of freedom of each component, and according to the relationship between the relative motions of each component, in order to facilitate the establishment of the dynamic model and the subsequent solution, the oxy absolute reference coordinate system is established, and the origin o is set up It is located at the center of rotation of the rotor, and this coordinate system is fixed. The motion of each component can be referenced by this coordinate system to establish dynamic equations and follow-up solutions. The selection of the coordinate system does not change the physical characteristics of the sealed rotor system, only affects the difficulty in the analysis process.