In order to verify the correctness of digital closed-loop manufacturing technology for end face spiral bevel gear coupling, grinding experiments were carried out on h650g CNC spiral bevel gear grinding machine, which can not only grind spiral bevel gear, but also have the function of grinding end face spiral gear coupling.
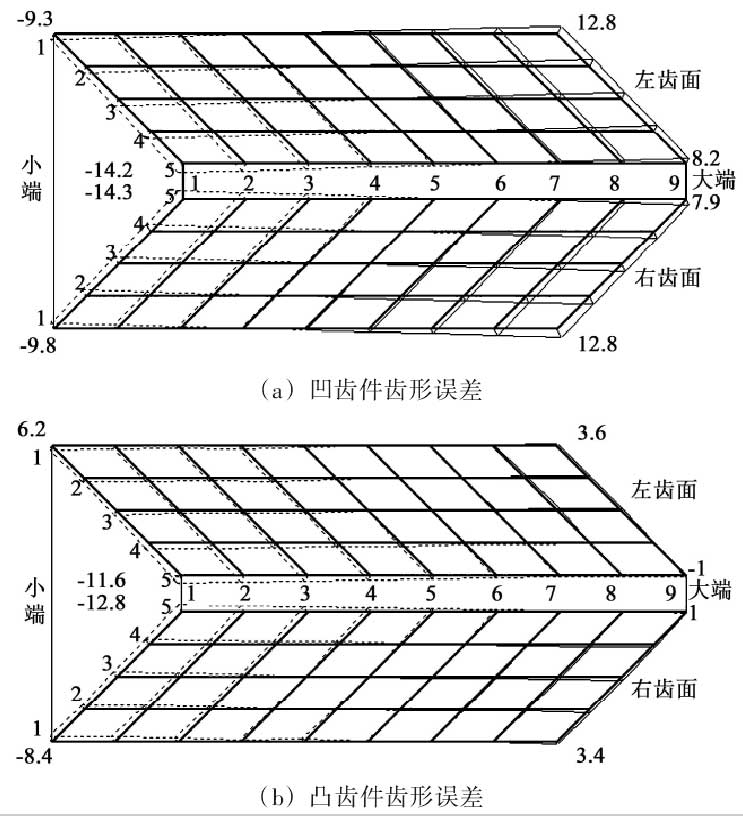
After grinding the concave and convex teeth of the end face spiral gear coupling, the tooth profile error is detected on the domestic l65g high precision gear measuring center. The test results are shown in Fig. 1. In Figure 1, the black solid line represents the theoretical tooth surface, and the thin solid line and thin dotted line represent the actual tooth surface. At the same time, the error value of tooth profile is listed at four corner points of tooth surface. When the value is “+”, it means that the actual tooth surface is lower than the theoretical tooth surface; when the value is “+”, it means that the actual tooth surface is higher than the theoretical tooth surface, and the unit of error difference shown is μ M. As shown in Fig. 1, the maximum profile error of concave tooth is 14.3 μ m, and that of convex tooth is 12.8 μ M.
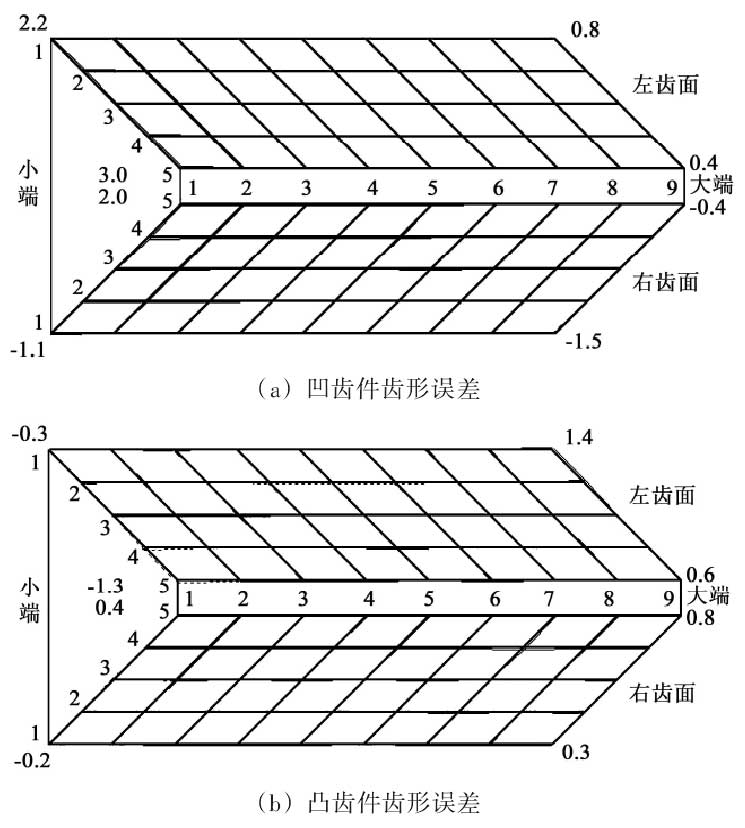
Using the method of tooth profile error correction established in this paper, the adjustment parameters of machine tool and the change of grinding wheel parameters are calculated. According to the modified machine tool adjustment parameters and grinding wheel parameters, the experimental workpiece is grinded again and the tooth profile error of the workpiece is measured. The measurement results are shown in Fig. 2. The maximum tooth profile error of concave teeth is 3 μ m, and that of convex teeth is 1.4 μ m, which fully meets the accuracy requirements of actual production. The contact area of the workpiece after tooth profile error correction is detected by using colorant. Blue and reddish brown colorants are applied on the concave and convex parts respectively, and then the concave and convex parts are meshed and slightly knocked along the circumference to make the colorants fully contact. Finally, the concave and convex parts are separated.
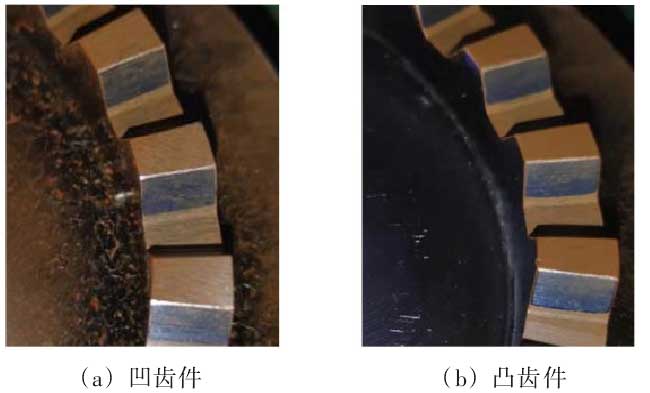
The coloring style is shown in Figure 3. The colored surface is rectangular and colored along the whole length of the tooth. There are no defects on the colored surface, and all teeth have the same color style. According to the design and inspection standard of aeroengine circular arc end teeth, the coloring style of the tooth surface contact area of the test workpiece is completely qualified.