Introduction
Hypoid gear is crucial component in many automotive and industrial applications due to their ability to transfer power between non-intersecting shafts at right angles. The unique geometry of hypoid gear, which combines elements of spiral bevel and helical gear, allows for smooth and quiet operation. However, this complexity also makes hypoid gear susceptible to wear and failure if not properly designed and maintained. Finite Element Analysis (FEA) has become an invaluable tool in predicting wear and failure in hypoid gear, enabling engineers to optimize their designs for durability and performance.
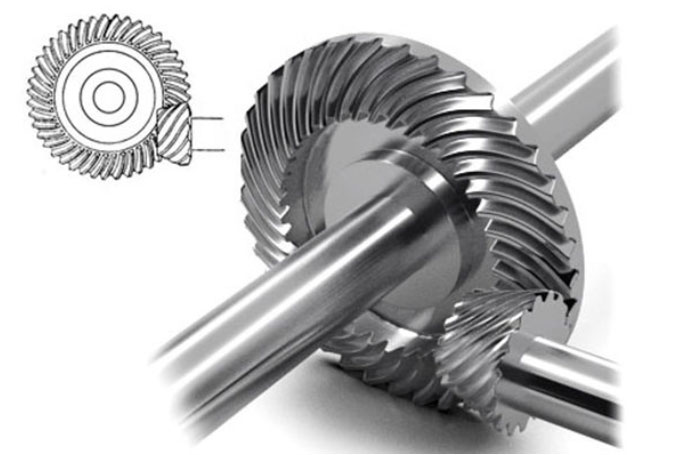
Understanding Hypoid Gear
Hypoid gear differ from standard bevel gear by having an offset between the axes of the pinion and the gear. This offset creates a sliding action along the teeth, which can increase the load-carrying capacity but also introduces more complex stress patterns. To ensure the reliability of hypoid gear, it is essential to understand and predict the wear mechanisms and potential failure modes that can occur during operation.
Finite Element Analysis in Gear Development
Finite Element Analysis (FEA) is a computational technique used to predict how a product reacts to real-world forces, vibration, heat, fluid flow, and other physical effects. FEA subdivides a large problem into smaller, simpler parts called finite elements. This process involves the creation of a mesh, which is a network of points that represent the geometry of hypoid gear. By applying the material properties and boundary conditions, engineers can simulate and analyze the stresses and strains on the gear teeth.
Key Steps in FEA of Hypoid Gear
- Geometry Modeling: Creating an accurate 3D model of the hypoid gear set.
- Mesh Generation: Dividing the model into finite elements to facilitate analysis.
- Material Properties: Assigning material characteristics such as elasticity, density, and thermal conductivity.
- Boundary Conditions: Defining how the gear is constrained and the loads applied.
- Simulation: Running the FEA to predict stress distribution, deformation, and potential wear areas.
- Result Interpretation: Analyzing the output data to identify critical stress points and areas prone to wear or failure.
Benefits of Using FEA
- Improved Accuracy: Provides detailed insight into the stress distribution and potential failure points.
- Cost Efficiency: Reduces the need for extensive physical testing by allowing virtual simulations.
- Enhanced Durability: Helps in designing gear with optimized tooth profiles and material selection for better wear resistance.
- Failure Prediction: Identifies potential failure modes, allowing for proactive design adjustments.
Predicting Wear and Failure
Predicting wear and failure in hypoid gear involves understanding the contact mechanics and material behavior under operational loads. Wear prediction models can be integrated into the FEA to simulate how material loss occurs over time. This involves:
- Contact Analysis: Evaluating the contact pressure and sliding velocities between hypoid gear teeth.
- Material Fatigue: Assessing the cyclic loading effects and the potential for fatigue cracks.
- Thermal Effects: Considering the impact of temperature variations on material properties and lubrication.
Case Study: Application of FEA in Hypoid Gear Development
A practical example of FEA application in hypoid gear development involved a set of gear used in an automotive differential. By applying FEA, engineers were able to identify high-stress regions on the gear teeth, which corresponded to areas with increased wear rates observed in real-world testing. The FEA results prompted design modifications, including changes to the tooth geometry and material selection, which significantly improved the gear’s lifespan and performance.
Conclusion
Finite Element Analysis has revolutionized the development of hypoid gear by providing a detailed understanding of stress distribution and wear mechanisms. By leveraging FEA, engineers can design more durable and reliable gears, ultimately enhancing the performance of the systems they power. As technology advances, the integration of FEA with other predictive maintenance tools will continue to improve the longevity and efficiency of hypoid gears.
Table: Summary of FEA Benefits in Hypoid Gear Development
Benefit | Description |
---|---|
Improved Accuracy | Provides detailed stress distribution and failure point identification. |
Cost Efficiency | Reduces physical testing requirements through virtual simulations. |
Enhanced Durability | Optimizes gear design for better wear resistance and performance. |
Failure Prediction | Identifies potential failure modes, allowing for proactive design adjustments. |
Contact Analysis | Evaluates contact pressure and sliding velocities for wear prediction. |
Material Fatigue | Assesses cyclic loading effects and potential for fatigue cracks. |
Thermal Effects | Considers temperature variations’ impact on material properties and lubrication. |
By utilizing FEA, the development process of hypoid gear can be significantly improved, leading to more efficient and longer-lasting components in various applications.