Introduction
Helical gears are fundamental components in a wide range of applications, from electric vehicles to industrial machinery. Ensuring their durability and efficiency is paramount, particularly in high-stress environments. Innovative coatings and surface treatments play a crucial role in enhancing the performance and longevity of helical gears. This article explores various advanced coatings and surface treatments applied to helical gears, highlighting their benefits, applications, and impact on gear performance.
Understanding Helical Gears
Helical gears are cylindrical gears with teeth cut at an angle to the axis of rotation. This design allows for smoother and quieter operation compared to spur gears due to the gradual engagement of the teeth.
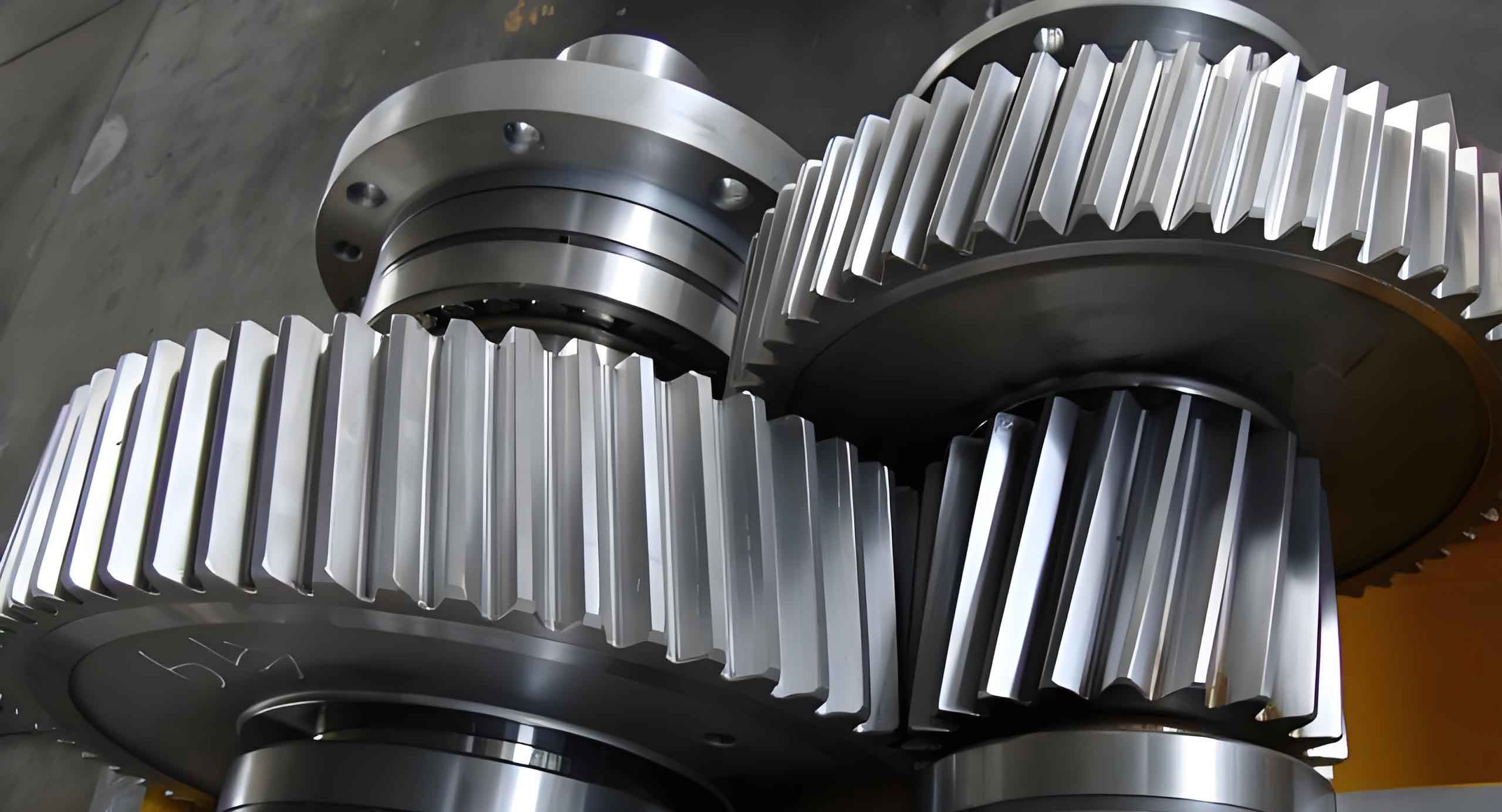
Key Features of Helical Gears:
- Angled Teeth: Typically cut at angles between 15° and 30°.
- Smooth Operation: Reduced noise and vibration due to gradual tooth engagement.
- Load Distribution: Even distribution of load across the teeth.
- High Load Capacity: Increased contact area allows for handling higher loads.
Importance of Coatings and Surface Treatments
Coatings and surface treatments are essential for improving the performance and lifespan of helical gears. They provide additional protection against wear, corrosion, and fatigue, and can enhance the gear’s mechanical properties.
Objectives of Coatings and Surface Treatments:
- Reduce Wear: Minimize material loss due to friction and contact stresses.
- Enhance Corrosion Resistance: Protect gears from environmental degradation.
- Improve Fatigue Life: Increase the gear’s resistance to cyclic loading.
- Reduce Friction: Enhance efficiency by lowering the coefficient of friction.
Innovative Coatings for Helical Gears
Several advanced coatings have been developed to address the specific challenges faced by helical gears in various applications. These coatings are applied to the gear surfaces to provide enhanced protection and performance.
Common Coatings for Helical Gears:
- Diamond-Like Carbon (DLC) Coatings:
- Benefits: Extremely hard, low friction, excellent wear resistance.
- Applications: High-performance automotive gears, aerospace components.
- Chromium Nitride (CrN) Coatings:
- Benefits: High hardness, good corrosion resistance, wear resistance.
- Applications: Industrial machinery, heavy-duty equipment.
- Tungsten Carbide (WC) Coatings:
- Benefits: High hardness, excellent wear resistance, moderate friction.
- Applications: Cutting tools, mining equipment, industrial gears.
- Molybdenum Disulfide (MoS2) Coatings:
- Benefits: Low friction, good wear resistance, effective in high vacuum environments.
- Applications: Aerospace gears, precision instruments.
Table: Comparison of Innovative Coatings for Helical Gears
Coating Type | Key Benefits | Typical Applications |
---|---|---|
Diamond-Like Carbon (DLC) | Extremely hard, low friction, wear resistance | High-performance automotive gears, aerospace components |
Chromium Nitride (CrN) | High hardness, corrosion resistance, wear resistance | Industrial machinery, heavy-duty equipment |
Tungsten Carbide (WC) | High hardness, wear resistance, moderate friction | Cutting tools, mining equipment, industrial gears |
Molybdenum Disulfide (MoS2) | Low friction, wear resistance, effective in high vacuum | Aerospace gears, precision instruments |
Advanced Surface Treatments for Helical Gears
In addition to coatings, advanced surface treatments are employed to enhance the properties of helical gears. These treatments modify the surface characteristics of the gear material, providing various performance benefits.
Common Surface Treatments for Helical Gears:
- Carburizing:
- Process: Introducing carbon into the surface layer of the gear material.
- Benefits: Increased surface hardness, wear resistance, and fatigue strength.
- Applications: Automotive gears, heavy-duty industrial machinery.
- Nitriding:
- Process: Adding nitrogen to the surface layer of the gear material.
- Benefits: High surface hardness, excellent wear and corrosion resistance.
- Applications: Aerospace components, precision gears.
- Induction Hardening:
- Process: Rapidly heating the gear surface using electromagnetic induction, followed by quenching.
- Benefits: Enhanced surface hardness, improved wear resistance.
- Applications: Large industrial gears, automotive components.
- Shot Peening:
- Process: Bombarding the gear surface with small spherical media.
- Benefits: Improved fatigue strength, reduced stress concentrations.
- Applications: Aerospace gears, high-stress industrial components.
Table: Comparison of Advanced Surface Treatments for Helical Gears
Surface Treatment | Key Benefits | Typical Applications |
---|---|---|
Carburizing | Increased surface hardness, wear resistance, fatigue strength | Automotive gears, heavy-duty industrial machinery |
Nitriding | High surface hardness, wear and corrosion resistance | Aerospace components, precision gears |
Induction Hardening | Enhanced surface hardness, improved wear resistance | Large industrial gears, automotive components |
Shot Peening | Improved fatigue strength, reduced stress concentrations | Aerospace gears, high-stress industrial components |
Impact of Coatings and Surface Treatments on Helical Gear Performance
The application of innovative coatings and surface treatments significantly enhances the performance and durability of helical gears. These enhancements are critical in high-stress applications where reliability and longevity are paramount.
Performance Benefits:
- Wear Resistance: Coatings and surface treatments provide a hard, wear-resistant surface that reduces material loss and extends gear life.
- Corrosion Resistance: Protective layers prevent corrosion, ensuring gears remain functional in harsh environments.
- Fatigue Life: Treatments such as shot peening and nitriding improve the fatigue strength of gears, allowing them to withstand cyclic stresses.
- Friction Reduction: Low-friction coatings like DLC and MoS2 improve gear efficiency by reducing energy losses due to friction.
List: Benefits of Innovative Coatings and Surface Treatments
- Enhanced Wear Resistance: Extends the operational life of helical gears.
- Improved Corrosion Resistance: Protects gears from environmental degradation.
- Increased Fatigue Strength: Allows gears to endure high cyclic loads.
- Reduced Friction: Enhances efficiency and reduces energy consumption.
- Better Performance in Harsh Environments: Ensures reliability in demanding applications.
Applications in Various Industries
Helical gears with advanced coatings and surface treatments are used in a wide range of industries, each benefiting from the enhanced performance and durability.
Industry-Specific Applications:
- Automotive Industry:
- Electric Vehicles: Improved efficiency and reliability of transmission systems.
- High-Performance Vehicles: Enhanced wear resistance and fatigue strength for gears under high loads and speeds.
- Aerospace Industry:
- Aircraft Components: High-strength, wear-resistant gears for flight control systems and engine components.
- Space Exploration: Gears with low-friction coatings for use in high-vacuum environments.
- Industrial Machinery:
- Heavy-Duty Equipment: Durable gears capable of withstanding high loads and harsh conditions.
- Precision Machinery: High-accuracy gears with excellent wear and fatigue properties.
- Renewable Energy:
- Wind Turbines: Reliable gears with corrosion-resistant coatings for long-term use in offshore environments.
- Solar Tracking Systems: Efficient, low-friction gears for precise positioning.
Table: Industry-Specific Applications of Coated and Treated Helical Gears
Industry | Specific Applications | Benefits of Coatings and Treatments |
---|---|---|
Automotive | Electric vehicles, high-performance vehicles | Improved efficiency, reliability, wear resistance |
Aerospace | Aircraft components, space exploration | High strength, wear resistance, low friction |
Industrial Machinery | Heavy-duty equipment, precision machinery | Durability, load handling, accuracy |
Renewable Energy | Wind turbines, solar tracking systems | Corrosion resistance, efficiency, reliability |
Conclusion
Innovative coatings and surface treatments are essential for enhancing the performance and durability of helical gears in various high-stress applications. By improving wear resistance, corrosion resistance, fatigue strength, and reducing friction, these treatments ensure that helical gears can meet the demanding requirements of modern technology. As industries continue to evolve and push the boundaries of performance, the role of advanced coatings and surface treatments in gear manufacturing will become increasingly important, driving further advancements in the efficiency and reliability of helical gears.