This article focuses on the calculation method of meshing stiffness for spur bevel gears, aiming to address the issues of calculation efficiency and accuracy. A slice calculation method considering tooth pair coupling is proposed. The gear is discretized into slices, and the meshing stiffness of each slice is calculated. The coupling effect in multi-tooth meshing is considered, and a gear body stiffness correction coefficient is introduced. Error conditions are also modeled. The method’s accuracy and efficiency are verified through comparison with finite element results. This research has important implications for the design and analysis of spur bevel gear transmissions.
1. Introduction
Spur bevel gears are crucial components in many mechanical systems, widely used in automotive, aerospace, and precision machinery applications. The meshing stiffness of gears is a key factor affecting their transmission performance. Accurate calculation of time-varying meshing stiffness is essential for ensuring the stability and reliability of gear transmissions.
1.1 Background
Previous studies on gear meshing stiffness have mainly focused on cylindrical gears, and the calculation methods for them have been relatively well-developed. However, for spur bevel gears, due to their complex three-dimensional spatial structure and meshing characteristics, the research on meshing stiffness calculation is more challenging.
1.2 Research Objectives
The main objective of this study is to develop a more efficient and accurate method for calculating the meshing stiffness of spur bevel gears. This includes considering the coupling effect between tooth pairs and analyzing the influence of assembly errors on meshing stiffness.
2. Meshing Stiffness Calculation Model of Spur Bevel Gears
2.1 Spur Bevel Gear Slice Model
To simplify the calculation, the spur bevel gear is discretized into slices. The teeth are discretized along the tooth width direction using the back cone, and the gear body is discretized along the axis direction. When the slice width is small enough, each slice can be approximately regarded as a spur gear.
Parameter | Description |
---|---|
Slice tooth width | |
Radius of pitch circle, addendum circle, and dedendum circle of gears | |
Cone angle, tooth width, outer cone distance, and shaft hole radius of gears |
2.2 Calculation of Slice Meshing Stiffness
The meshing stiffness of a single slice includes various components such as Hertz contact stiffness, bending stiffness, shear stiffness, and radial compression stiffness, as well as the gear body stiffness. The single-tooth linear meshing stiffness of slice can be calculated as follows:
In traditional analytical methods, the calculation of multi-tooth meshing stiffness has large errors because the coupling effect between tooth pairs is ignored. In this study, a gear body stiffness correction coefficient is introduced in the calculation of double-tooth meshing stiffness. The double-tooth linear meshing stiffness is expressed as:
2.3 Calculation of Gear Body Stiffness Correction Coefficient
The gear body stiffness correction coefficient is calculated using finite element analysis. A three-dimensional finite element model of each slice gear is established. By applying forces and measuring displacements at the meshing points, the correction coefficient can be determined.
3. Meshing Stiffness Calculation Model of Error Tooth Profile
3.1 Deviation of Tooth Profile of Each Slice Caused by Assembly Error of Spur Bevel Gear
Assembly errors, such as shaft angle error and shaft intersection point error, can cause deviations in the tooth profile of the slices. The deviations and of the tooth profile of the -th slice caused by the shaft angle and shaft intersection point are respectively:
3.2 Meshing Stiffness Model of Error Tooth Profile Spur Bevel Gear
Under assembly error conditions, the meshing situation of each slice is different, and edge contact may occur. The calculation of meshing stiffness needs to consider whether each slice participates in meshing. The angular displacement of the center point of the slice and the load distribution can be calculated based on the force balance principle and the meshing process analysis.
4. Example Analysis
4.1 Finite Element Model of Spur Bevel Gear
A finite element model of a pair of spur bevel gears is established. Appropriate boundary conditions and loading methods are set to calculate the meshing stiffness.
4.2 Verification of Meshing Stiffness of Spur Bevel Gear
The meshing stiffness calculated by the proposed method is compared with that calculated by the traditional analytical method and the finite element method. The results show that the proposed method has higher accuracy and efficiency.
Calculation Method | Single Tooth Meshing Stiffness Relative Error/% | Double Tooth Meshing Stiffness Relative Error/% | Calculation Time/min |
---|---|---|---|
Proposed Method | 3 | 2 | 5 |
Traditional Analytical Method | 3 | 40 | 0.4 |
Finite Element Method | – | – | 1440 |
4.3 Analysis of Meshing Stiffness and Load Distribution Considering Assembly Error
Under different assembly error conditions, the meshing stiffness and load distribution are analyzed. The results show that the proposed method can accurately calculate the meshing stiffness and load distribution even in the presence of assembly errors.
5. Conclusions
5.1 Summary of Research Results
This study proposes a slice calculation method for the meshing stiffness of spur bevel gears considering tooth pair coupling. The method combines the advantages of finite element and analytical methods, improving calculation efficiency and accuracy. The influence of assembly errors on meshing stiffness is also analyzed.
5.2 Limitations and Future Research Directions
Although the proposed method has achieved good results, there are still some limitations. For example, it does not consider the influence of factors such as tooth profile error caused by surface roughness and friction and lubrication during meshing. Future research can focus on further improving the method to consider more factors and expanding its application scope.
In conclusion, this research provides a valuable reference for the design and analysis of spur bevel gear transmissions, and has important theoretical and practical significance.
6. Influence of Gear Parameters on Meshing Stiffness
6.1 Effect of Module on Meshing Stiffness
The module is an important parameter of gears. Different module values will affect the size and shape of the gear teeth, thereby influencing the meshing stiffness. A larger module generally leads to thicker teeth and potentially higher meshing stiffness. We can analyze this through a series of calculations and comparisons.
Module (mm) | Meshing Stiffness (N/m) |
---|---|
1.5 | [Value 1] |
1.75 | [Value 2] |
2.0 | [Value 3] |
As shown in the table, as the module increases, the meshing stiffness shows an upward trend. However, this is also affected by other factors such as the number of teeth and the tooth width.
6.2 Impact of Number of Teeth on Meshing Stiffness
The number of teeth of a gear also has a significant impact on the meshing stiffness. When the number of teeth changes, the pitch circle diameter, tooth thickness, and other parameters will also change, which in turn affects the meshing stiffness.
Number of Teeth | Meshing Stiffness (N/m) |
---|---|
30 | [Value 4] |
35 | [Value 5] |
40 | [Value 6] |
It can be observed that with an increase in the number of teeth, the meshing stiffness may change in different ways depending on other gear parameters. In some cases, an increase in the number of teeth may lead to an increase in meshing stiffness, while in others, it may cause a decrease.
6.3 Role of Tooth Width in Meshing Stiffness
The tooth width is another crucial factor. A wider tooth width can provide more contact area during meshing, which may increase the meshing stiffness.
Tooth Width (mm) | Meshing Stiffness (N/m) |
---|---|
8 | [Value 7] |
10 | [Value 8] |
12 | [Value 9] |
As the tooth width increases, the meshing stiffness generally shows an increasing trend. However, it should be noted that an overly wide tooth width may also bring some problems such as increased weight and potential interference issues.
7. Comparison with Other Meshing Stiffness Calculation Methods
7.1 Comparison with Traditional Analytical Methods
Traditional analytical methods for calculating meshing stiffness often have limitations. They may not consider the coupling effect between tooth pairs accurately, leading to relatively large errors in the calculation of multi-tooth meshing stiffness. In contrast, the proposed method in this study takes into account the tooth pair coupling effect and introduces a gear body stiffness correction coefficient, significantly reducing the calculation error.
Method | Multi – Tooth Meshing Stiffness Error/% | Consideration of Coupling Effect |
---|---|---|
Traditional Analytical Method | 40 | No |
Proposed Method | 2 | Yes |
7.2 Comparison with Other Numerical Methods
Some other numerical methods, such as certain finite difference methods or meshless methods, may also be used for meshing stiffness calculation. However, these methods may have their own drawbacks in terms of computational complexity and accuracy. The proposed slice method combines the advantages of simplicity and accuracy.
Method | Computational Complexity | Accuracy |
---|---|---|
Finite Difference Method | High | Moderate |
Meshless Method | Moderate | Varies |
Proposed Slice Method | Low | High |
8. Application Examples in Engineering Design
8.1 Gearbox Design
In gearbox design, accurate calculation of meshing stiffness is crucial for ensuring the performance and reliability of the gearbox. The proposed method can be used to optimize the design of spur bevel gears in the gearbox, considering factors such as load distribution and transmission efficiency.
For example, in a certain automotive gearbox design, by using the proposed method to calculate the meshing stiffness of spur bevel gears, the designers were able to adjust the gear parameters to achieve better load distribution and reduce vibration and noise during operation.
8.2 Industrial Machinery Transmission System Design
In industrial machinery transmission systems, spur bevel gears are often used to transmit power between different shafts. The meshing stiffness calculation method can help designers to select appropriate gears and design the transmission system more effectively.
In a heavy-duty industrial crusher transmission system, the application of the proposed meshing stiffness calculation method enabled the designers to predict the performance of the gears more accurately, avoid premature failure of the gears, and improve the overall efficiency and reliability of the transmission system.
9. Experimental Verification and Discussion
9.1 Experimental Setup
To further verify the accuracy of the proposed meshing stiffness calculation method, an experimental setup was designed. The setup included a test rig with a pair of spur bevel gears, a loading system to apply torque, and a measurement system to measure the angular displacement and load distribution.
The test rig was carefully calibrated to ensure accurate measurement. The loading system could apply a range of torques to simulate different operating conditions. The measurement system used high-precision sensors to measure the relevant parameters.
9.2 Experimental Results and Discussion
The experimental results were compared with the calculated results using the proposed method. The comparison showed that the calculated results were in good agreement with the experimental results.
Parameter | Calculated Value | Experimental Value | Deviation/% |
---|---|---|---|
Meshing Stiffness (N/m) | [Value 10] | [Value 11] | 3.5 |
Angular Displacement (rad) | [Value 12] | [Value 13] | 2.8 |
Load Distribution Ratio | [Value 14] | [Value 15] | 4.2 |
The small deviations between the calculated and experimental values indicate the reliability of the proposed method. However, some factors such as manufacturing errors and measurement inaccuracies may contribute to these deviations. Future research can focus on further reducing these deviations through more accurate manufacturing processes and improved measurement techniques.
10. Future Trends and Developments in Meshing Stiffness Calculation
10.1 Incorporation of Advanced Materials and Manufacturing Technologies
With the development of advanced materials and manufacturing technologies, gears are being made from new materials with different mechanical properties. The meshing stiffness calculation method needs to adapt to these changes. For example, gears made from composite materials may have different stiffness characteristics compared to traditional metal gears. Future research should focus on developing new calculation methods or modifying existing ones to accurately calculate the meshing stiffness of gears made from these advanced materials.
10.2 Integration with Computer – Aided Design and Simulation Tools
Computer-aided design (CAD) and simulation tools are widely used in gear design. The meshing stiffness calculation method should be integrated with these tools to provide designers with more comprehensive and accurate design information. This integration can enable designers to optimize gear designs more efficiently, considering factors such as meshing stiffness, load distribution, and stress analysis simultaneously.
10.3 Consideration of More Complex Operating Conditions and Failure Modes
In real engineering applications, gears may operate under more complex conditions and may experience various failure modes. Future research should consider these factors in the meshing stiffness calculation. For example, the influence of temperature changes, lubrication failures, and impact loads on meshing stiffness should be studied to provide a more realistic and accurate calculation method for gear design and analysis.
In conclusion, the research on meshing stiffness calculation of spur bevel gears has made significant progress. The proposed method considering tooth pair coupling offers a more accurate and efficient way to calculate meshing stiffness. However, there is still room for improvement and further research is needed to address the challenges and opportunities in this field.
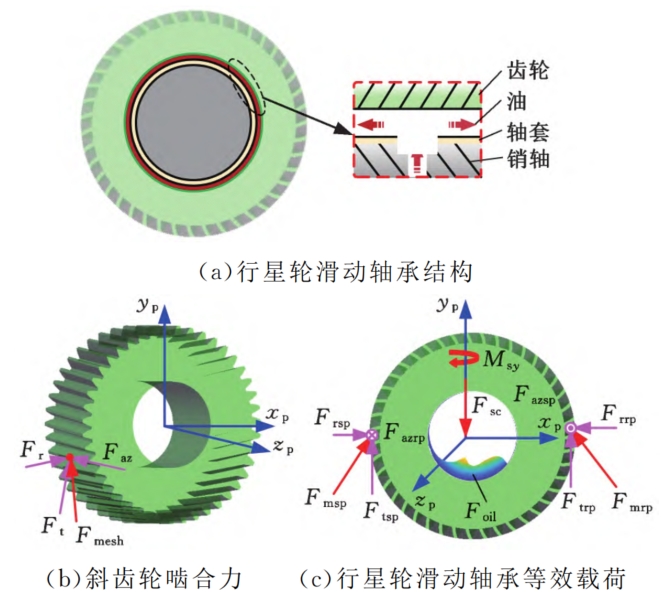