In this experiment, the tooth surface pitting only occurs on one tooth surface of the driven gear, and the tooth surface pitting mainly concentrates near the pitch line of the tooth surface. The experimental tooth surface pitting fault is shown in Fig. 1.
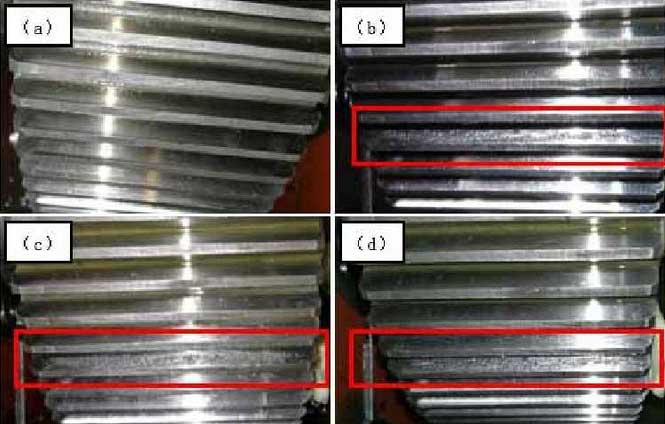
In order to facilitate the following analysis and expression, healthy gear system is represented by healthy gear system, and three gear systems with different degrees of pitting-1, pitting-2 and pitting-3 are respectively used to represent three kinds of gear systems with different tooth surface pitting faults. In this paper, the above four gear systems with different gear states are tested. In Adobe Photoshop software, the tooth surface pitting photos are processed to identify the tooth surface pitting fault area. The gear pitting fault degree is defined by the proportion of the pitting fault area to the total tooth surface area. The percentage of pitting-1, pitting-2 and pitting-3 to the total tooth surface area is 4.32%, 12.12% and 20.47%, respectively.
According to the experiment of micro pitting, four kinds of gear models are established in this paper: healthy gear and three kinds of pitting fault gear. The three kinds of gear pitting fault in the simulation study are corresponding to the gear pitting fault in the experimental study and keep basically the same. The experimental research of gear micro pitting fault will be described in Chapter 5. This chapter mainly studies the gear pitting fault through simulation and modeling. In this paper, the main simulation model.
For four kinds of gear models with different gear states: in the healthy gear system, all tooth surfaces of the driving and driven gears are kept smooth and intact; in the three kinds of gear systems with different degrees of pitting corrosion, the pitting fault only occurs on one tooth surface of the driven gear, the other teeth of the driven gear are kept smooth and intact, and the driving gear is also intact. The location and size of pitting on the tooth surface of driven gear can be expressed by three variables: (μ,,), where is the distance from the center of pitting to the tooth root; is the radius of circular pitting; is the depth of pitting.. For convenience of expression, healthy gear system is represented by healthy gear system, and pitting-1, pitting-2 and pitting-3 are respectively used for three kinds of gear systems with pitting failure. In addition, the proportion of pitting area is defined as the ratio of pitting fault area to meshing surface area of driven gear.

The early pitting corrosion of gear is a kind of fatigue phenomenon of tooth surface in the initial stage of gear operation. The initial pitting corrosion usually occurs in the root part near the pitch line. Therefore, in the modeling of pitting corrosion, it is assumed that all the centers of pitting are distributed on the pitch line of driven gear tooth surface, and the model for simulating pitting fault is shown in Fig. 2. After rough calculation, the surface area of meshing tooth surface of driven gear is about 574 mm. For pitting-1, there are 8 circular pitting corrosion occurred on one meshing tooth surface of driven gear, and the pitting fault area is about 4.38% of the meshing surface area of driven gear. Therefore, the failure degree of pitting corrosion is set to keep basically the same as that in the experiment. Therefore, for pitting-2 and pitting-3, the number of pitting-2 and pitting-3 are 10 and 17 respectively, and the pitting-2 and pitting-3 areas account for 12.31% and 20.93% respectively.