Gear shaping is a machining process widely used for the precise manufacturing of gears. It involves the use of a gear shaping machine and a specialized cutting tool called a shaper cutter. Let’s delve into the essential aspects of gear shaping:
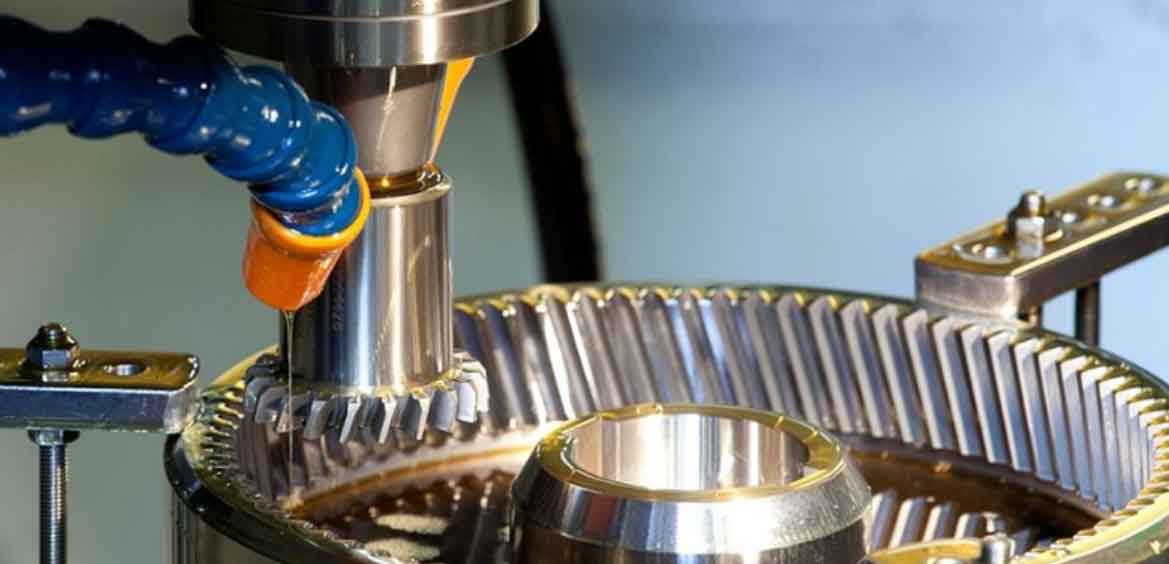
- Gear Shaping Process: The gear shaping process follows a principle of cutting gear teeth using a reciprocating motion. The shaper cutter, mounted on a reciprocating ram, gradually cuts the gear teeth as it moves across the workpiece. The workpiece rotates, and the cutter reciprocates to generate the desired gear tooth profile.
- Gear Shaping Machine: A gear shaping machine consists of several key components:
- Worktable: The workpiece is securely mounted on the worktable and rotates during the cutting process.
- Cutter Spindle: The shaper cutter is mounted on the cutter spindle, which provides the necessary rotational motion.
- Ram: The ram holds the cutter spindle and reciprocates to generate the gear teeth.
- Feed Mechanism: The feed mechanism controls the rate at which the cutter advances across the workpiece to cut the gear teeth.
- Drive Mechanism: The machine is powered by a drive mechanism that provides the necessary rotational and reciprocating motions.
- Gear Shaping Cutter: The shaper cutter is a specialized cutting tool with teeth that correspond to the desired gear tooth profile. The cutter has multiple cutting edges, and as it reciprocates across the workpiece, each edge engages with the workpiece to remove material and form the gear teeth. Shaper cutters are available in various configurations to produce different gear types, including spur gears, helical gears, and internal gears.
- Gear Shaping Advantages:
- Precision: Gear shaping is known for its ability to produce gears with excellent accuracy, precise tooth profiles, and tight dimensional tolerances.
- Versatility: Gear shaping machines can be used to manufacture a wide range of gear sizes and types, making them suitable for various applications.
- Efficiency: Gear shaping can be a more time-efficient process compared to some other gear manufacturing methods, especially for small and medium-sized batches.
- Complex Gear Profiles: Gear shaping machines can produce gears with complex tooth profiles, including helical gears and gears with custom profiles.
- Surface Finish: Gear shaping often provides a high-quality surface finish on the gear teeth, reducing the need for additional finishing operations.
- Factors Affecting Gear Shaping:
- Cutter Design: The choice of shaper cutter depends on the gear specifications, tooth profile requirements, and material being cut. Different cutter designs and materials can be used to optimize the cutting process.
- Machine Setup: Proper alignment and adjustment of the gear shaping machine are crucial for achieving accurate gear tooth generation and minimizing vibrations.
- Cutting Parameters: Cutting speed, feed rate, and depth of cut should be set based on the gear material, cutter design, and desired surface finish. These parameters need to be optimized to ensure efficient cutting and maximize tool life.
- Workpiece Holding: Securely clamping the workpiece during gear shaping is essential to prevent any movement or deflection that could affect gear accuracy.
Gear shaping is a versatile and precise gear manufacturing process that is commonly used in various industries. It offers the advantages of producing accurate gear teeth with tight tolerances, and it can handle a wide range of gear types and sizes. By leveraging the gear shaping process, manufacturers can achieve high-quality gears that meet the demands of their specific applications.