Introduction
The shield machine plays an increasingly important role in the construction of underground projects. As the core component of the shield machine, the operating status of the reducer directly affects the performance of the shield machine The performance and safety of the shield machine are affected by the wear state of the multi-stage planetary gears, which are one of the important components of the reducer. The detection of the wear state of the multi-stage planetary gears in the reducer of the shield machine is of great significance for ensuring the normal operation of the shield machine and improving the safety and efficiency of underground engineering construction. There are two traditional methods for detecting the wear state of planetary gears: one is to monitor the The first is the detection method of evaluating the operating status of equipment based on measuring the gear oil indicators of the wind turbine. The second is the detection method of gear meshing wear status based on improved spectral residuals. The above methods are time-consuming and difficult to achieve real-time detection. To solve the above problems, this paper proposes a multi-stage planetary gear wear status detection method for shield reducers, which can provide real-time detection of planetary gear wear status and improve the operational safety and efficiency of shield machines.
Wear state detection of multi-stage planetary gears in reducers
In planetary gears, the collection and processing of vibration signals are crucial, as these signals contain important information about the operating state of the equipment. However, these signals are often affected by environmental noise and electromagnetic interference inside the equipment, resulting in a large amount of noise in the signal. The presence of these noises affects the overall smoothness of the signal, further affecting the accuracy of wear state detection. Effective noise reduction measures are needed to process the collected vibration signals. Among them, translation invariant wavelet denoising method is a widely used noise reduction technique.
Segment the gear image meshing area
When the gear area is located at the edge of the grid area, applying a threshold method can result in incomplete segmentation of the grid area. The location of the gear area has an
The same height, and the wear areas of gears of different heights present different values in the image. This article uses a grid region segmentation method that combines region segmentation, region aggregation, and edge correction. Using the region segmentation method can avoid detecting low-intensity grid regions. The large region aggregation algorithm identifies candidate grid regions, which can be combined as a whole to obtain grid regions. Then, based on the topographical characteristics of the original grid region, the boundary of the original grid region is adjusted. It overcomes the incomplete division problem caused by pitting on the boundary of the original grid region, and obtains the final division result of the original grid region.
The grayscale features of the worn parts of each pinion gear are different, making it inappropriate to use global cutting techniques. After modifying the boundaries of the grid region, Usually includes some background regions with lower grayscale values, which have similar pitting grayscale features. Adaptive local threshold segmentation is used to obtain candidate regions, and false positive regions are removed from the candidate regions based on shape features.
The grayscale features of the worn parts of each pinion gear are different, making it inappropriate to use global cutting techniques. After modifying the boundaries of the grid region,Usually includes some background areas with lower gray values, which have similar pitting gray features. In order to reduce segmentation errors in the grid area, this segment is performed based on the classification results of the grid-like areas to obtain candidate regions for the grid area and determine whether the segmentation results of the upper and lower regions are correct. If the segmentation results are incorrect, they need to be improved. In similar gear types, different tooth surfaces have the same height. The height of the grid areas on different gear surfaces is basically consistent.
Detection result
The gear wear image is shown in the figure. The detection results of the method in this article are shown in the figure.
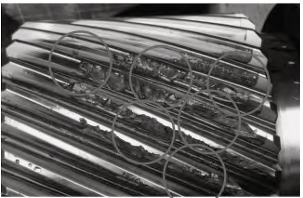
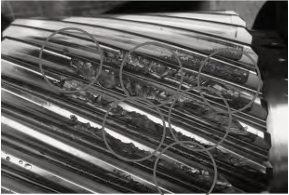
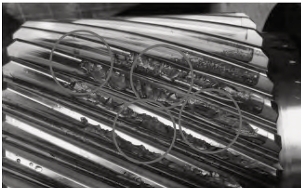
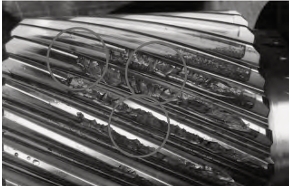
The results of detecting gear wear are the same as the original wear location of the gear, but the control group method and control group B method cannot detect all the locations of gear wear. Therefore, it can be concluded that the method in this article can accurately detect the state of gear wear, and the detection effect of gear wear state is good. Setting the number of iterations to 500, and comparing the control group method, control group method, and this method, we obtain the test results of different methods for detection accuracy, as shown in the figure.
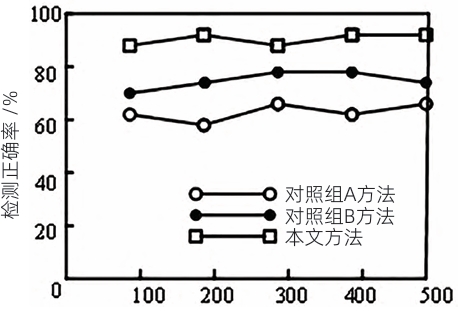
During the 500 iterations, the accuracy of gear wear state detection of the proposed method can reach about 90% on average, while the accuracy of gear meshing wear state detection of the control method is about 70% on average, both lower than the proposed method. Therefore, it can be concluded that the accuracy of gear wear state detection using the proposed method is higher than that of the control method.
Conclusion
The operating condition of the gear is directly related to the working quality of the shield machine reducer. In order to ensure its normal operation, it is necessary to design the multi-stage planetary gear reducer for the shield machine Regularly inspect the wear state of the wheel. Introduce the analysis method for the wear state of multi-stage planetary gears in the reducer of the shield machine. The application of this measurement method can greatly improve the accuracy of the measurement of the wear state of multi-stage planetary gears, far exceeding the control group method. Through comparative analysis, it is shown that there is good consistency between the results and the experimental data, with a small time deviation between the two. The vibration mode design is similar, jointly proving the effectiveness of basic research and experimental technology.