Introduction
Parametric modeling of bevel gears is a method of quickly establishing gear models with the help of computer-aided design. Spur bevel gears and helical bevel gears both belong to the category of bevel gears. The parameterized modeling process of both gear blanks has similarities, but the distribution of teeth on the gear blanks is different. The teeth of spur bevel gears are distributed vertically along the gear blank, while the teeth of helical bevel gears are distributed in a certain arc along the gear blank. It is this arced distribution that enables helical bevel gears to have more meshing teeth, a more stable force, and a higher load-bearing capacity than spur bevel gears with the same number of teeth and modulus in engineering machinery. Due to the numerous parameters and complex structure of helical bevel gears, modeling is difficult. Many scholars at home and abroad have conducted extensive research on the establishment of helical bevel gear models. The involute equation of bevel gears is not easily achieved directly in SolidWorks software. By establishing the involute equation in MATLAB software first, the obtained involute discrete points are imported into SolidWorks software. Based on CATIA software, a parametric modeling method for helical bevel gears was studied, and some parameters of the gear were optimized. By using the secondary development tool Protoolkit in PTC software to program, a three-dimensional parametric modeling method for logarithmic helical bevel gears was realized. Based on the derivation of the spherical involute theory, using CATIA as a secondary development platform, a parametric design interactive interface for logarithmic helical bevel gears was realized. By entering original parameters, calculated parameters were obtained. Taking high-teeth helical bevel gears as the research object, a parametric equation for constant-teeth helical bevel gears was derived. Using UG/Open GRIP as a secondary development tool, a three-dimensional solid model of constant-teeth helical bevel gears was realized. Based on the SWEEP method of spherical involute tooth surface modeling, an arc-tooth bevel gear model was created by using SWEEP to form the end surface profile curve. The conjugate meshing mechanism of line contact on the meshing surface was studied, and the key parameters of the arc-tooth bevel gear tooth profile were calculated using spatial geometric principles. Then, CATIA software was used to establish a three-dimensional solid model of the arc-tooth bevel gear. A practical industrial ESI-like geometric design and manufacturing method for helical bevel gears with variable surface details was proposed, and its model was 3D printed. Wang Yongxu et al. [9] based on the theory of spherical involute formation, used MATLAB to obtain discrete point data on the tooth surface, and realized the modeling of helical bevel gears in UG. It can be seen that different three-dimensional modeling software can be used to model helical bevel gears, but most literature describes the specific steps in the modeling process less and is not very operable.This article provides an in-depth analysis of the important steps in the modeling process. First, a straight bevel gear is modeled. On this basis, a helical bevel gear is modeled by rotating the involute group of the large and small ends around the axis of the gear blank. The theoretical basis is the geometric relationship between the original parameters and calculated parameters of the bevel gear, as well as the involute equations of the large and small ends. The research idea is to given the basic parameters of the bevel gear and use MATLAB R2022a software to derive the calculated parameters of the bevel gear by writing a program. In Creo Parametric 9.0 software, the specific parameterized modeling of the bevel gear is implemented, and the designed model is realized through 3D printing. The advantage of parameterized modeling of bevel gears is that by changing the basic parameters, corresponding bevel gear models can be obtained.
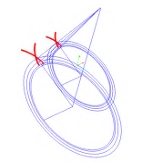
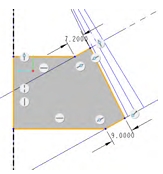
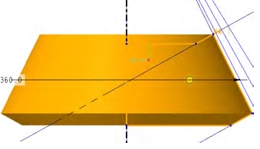
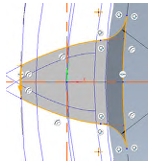
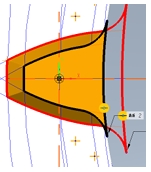
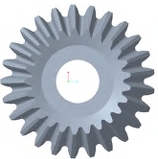
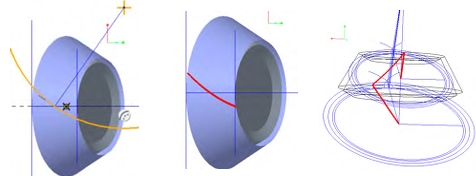
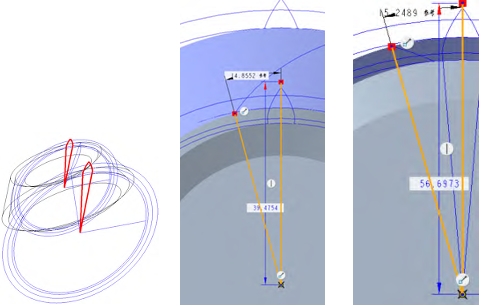
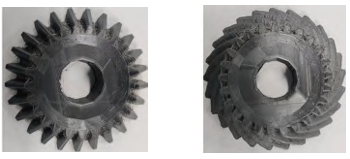
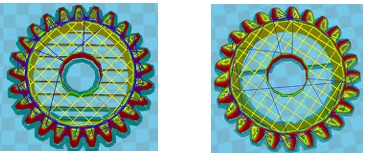
Epilogue
By using MATLAB software to write programs to derive the calculation parameters of bevel gears, the workload of manual calculations is greatly reduced, making the derivation of formulas faster and more accurate. The parameterized modeling of spur bevel gears and helical bevel gears is similar, with the difference being the construction of the final tooth profile. Through research and analysis of the important steps in the modeling process of bevel gears, the parameterized method is used to model bevel gears, which greatly reduces the difficulty of modeling. Since only changing the basic parameters can obtain a corresponding new model, this method is fast, efficient, and accurate, providing a new idea for modeling bevel gears. Combined with 3D printing technology, compared to traditional CNC machine tool processing, it can obtain model objects faster, saving a lot of manpower and financial resources, which has important practical significance.