Figure 1 shows the hardness change trend of the original sample without grinding of spiral bevel gear steel at different distances from the surface. It can be seen from the figure that the carburized layer depth of the workpiece selected in this test is about 1.0 ~ 1.2 mm, and the microhardness of the carburized layer is maintained at about 685 HV, with little change. This is because the good hardenability of 30CrMnTi leads to almost no residual austenite on the surface after quenching, so the hardness of carburized layer tends to be consistent. After 1.2 mm from the surface, the carbon content gradually decreases, so the microhardness decreases. When the hardness of the matrix reaches about 475 mm, the microstructure remains unchanged.
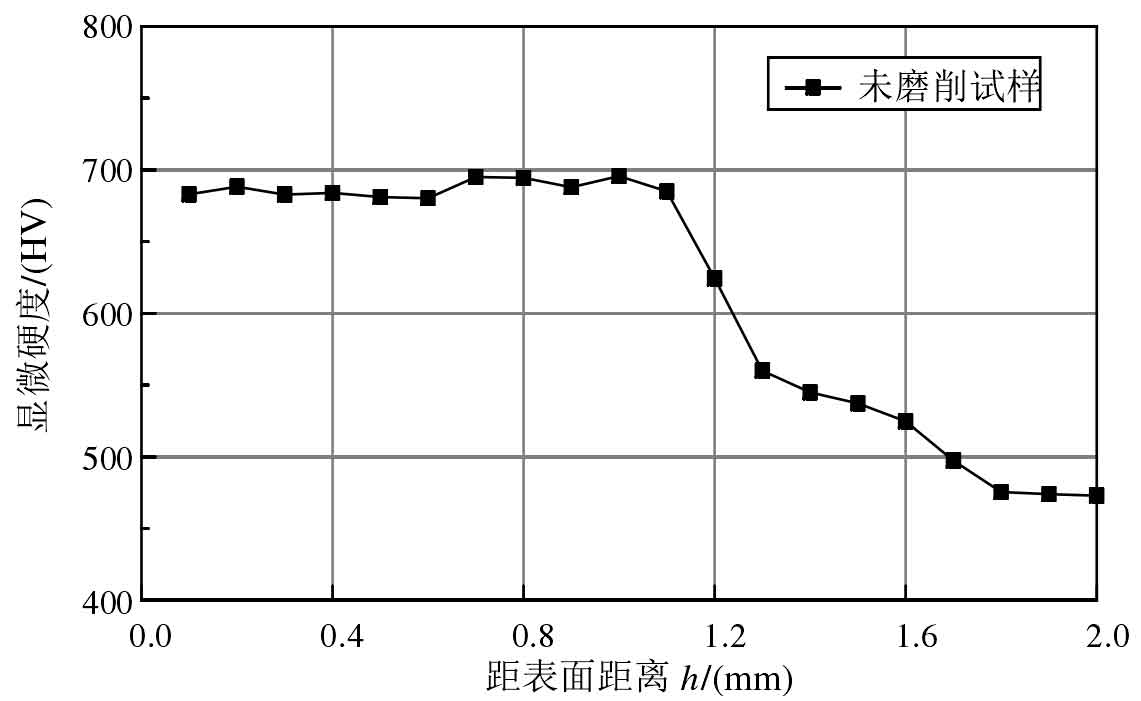
The influence of grinding parameters of spiral bevel gear steel on the depth of strengthening layer is discussed, so the change of microhardness after grinding of carburized layer (within 1 mm) is emphatically studied. The results are shown in Fig. 2.
It can be seen from Fig. 2 that the microhardness of the strengthening layer is improved to a certain extent after the grinding of spiral bevel gear steel, and the gradient hardness of the strengthening layer keeps the law of first increasing and then decreasing. The discussion shows that the martensite structure of the strengthening layer of spiral bevel gear steel after grinding is fine, and the hardness of this needle martensite is higher than that of the matrix plate martensite, so the hardness of the strengthening layer is improved. The gradient hardness first increases and then decreases because there is residual austenite near the grinding surface of spiral bevel gear steel, resulting in a slight decrease in the microhardness of the grinding surface of spiral bevel gear steel. With the increase of the distance to the surface, the content of residual austenite gradually decreases, so the microhardness reaches the maximum value.