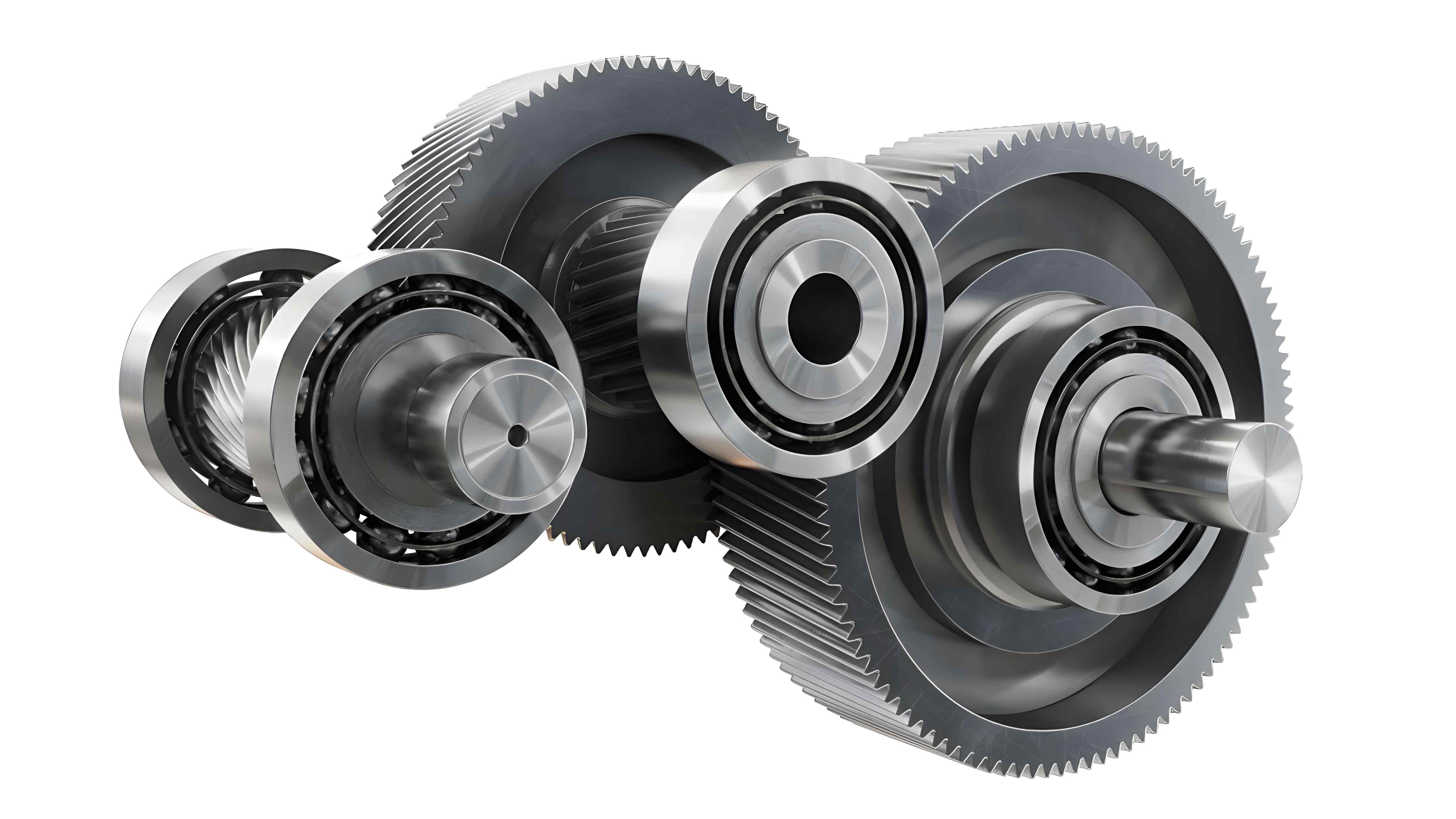
The transition to electric vehicles (EVs) has brought about significant advancements in automotive technology, including the use of helical gear in transmission systems. Helical gear offer several advantages over traditional spur gear, particularly in terms of performance and durability, making them an ideal choice for EVs. This article explores the key considerations for using helical gear in electric vehicles, focusing on their performance and durability.
Performance Considerations
1. Efficiency: Helical gear is known for their high efficiency, which is crucial in electric vehicles to maximize battery life and range. The angled teeth of helical gear engage more gradually than spur gear, resulting in smoother and quieter operation. This efficiency contributes to better overall vehicle performance and a more pleasant driving experience.
2. Noise Reduction: One of the significant advantages of helical gear is their ability to reduce noise and vibration. The gradual engagement of gear teeth minimizes the shock loads that can cause noise. This is particularly important in EVs, where the absence of an internal combustion engine makes gear noise more noticeable.
3. Load Capacity: Helical gear can handle higher loads compared to spur gear due to the larger contact area between the teeth. This increased load capacity is essential for the performance of EVs, which require reliable and durable transmission systems to handle the varying demands of driving conditions.
Durability Considerations
1. Wear Resistance: The helical gear design offers better wear resistance than spur gear. The angled teeth distribute the load more evenly across the gear face, reducing localized stress and wear. This is particularly beneficial in electric vehicles, where long-term durability is a key consideration.
2. Lubrication and Maintenance: Proper lubrication is critical for the durability of helical gear. The sliding action between the gear teeth requires effective lubrication to minimize friction and wear. Advances in lubricants and lubrication techniques have enhanced the durability of helical gear, making them more suitable for long-term use in EVs.
3. Material Selection: The materials used in the manufacturing of helical gear significantly impact their durability. Advanced materials such as high-strength steels and specialized coatings can improve the wear resistance and lifespan of helical gear. These materials help mitigate the effects of friction and reduce the need for frequent maintenance.
4. Heat Dissipation: Helical gear generate more heat due to their sliding action compared to spur gear. Effective heat dissipation mechanisms are necessary to prevent overheating and ensure the longevity of the gear system. Proper cooling systems and heat-resistant materials play a crucial role in maintaining the durability of helical gear in EVs.
Table: Comparison of Helical Gear and Spur Gear in Electric Vehicles
Feature | Helical Gear | Spur Gear |
---|---|---|
Efficiency | High | Moderate |
Noise Reduction | Excellent | Poor |
Load Capacity | High | Moderate |
Wear Resistance | High | Moderate |
Lubrication | Critical | Important |
Material Requirements | Advanced materials required | Standard materials suffice |
Heat Dissipation | More heat generated | Less heat generated |
Maintenance | Regular lubrication needed | Less frequent maintenance |
Conclusion
Helical gear offer several performance and durability advantages that make them well-suited for use in electric vehicles. Their high efficiency, noise reduction capabilities, and increased load capacity enhance the performance of EVs, while their superior wear resistance and material advancements ensure long-term durability. As electric vehicle technology continues to evolve, the use of helical gear in transmission systems will likely become even more prevalent, contributing to the overall efficiency and reliability of these vehicles.