Helical gear is essential components in many mechanical systems, known for their smooth operation and ability to handle high loads. However, their performance and durability can be significantly enhanced through the application of advanced surface coatings. This article explores the various types of surface coatings available, their effects on helical gear durability and performance, and practical insights for engineers and manufacturers.
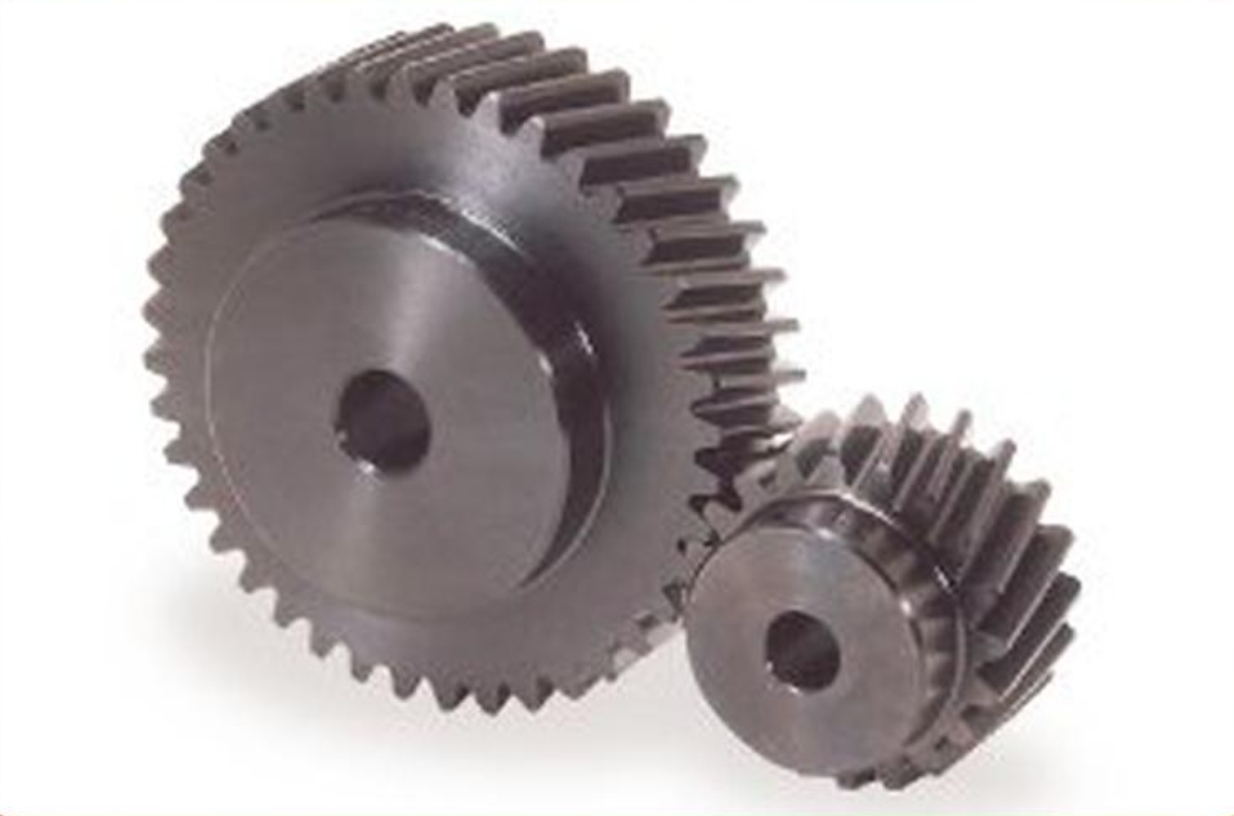
Introduction
Surface coatings have become a pivotal technology in extending the lifespan and enhancing the performance of mechanical components, including helical gear. These coatings provide additional protection against wear, corrosion, and fatigue, which are common issues faced in demanding operational environments. This article delves into the benefits of different surface coatings and their impact on the longevity and efficiency of helical gear.
Types of Surface Coatings
Hard Chrome Plating
Hard chrome plating is a widely used surface treatment that provides a hard, wear-resistant surface.
Coating Type | Benefits |
---|---|
Hard Chrome Plating | High hardness, excellent wear resistance, low friction |
Hard chrome plating is ideal for applications requiring high durability and low friction.
Nickel Plating
Nickel plating offers good corrosion resistance and moderate hardness, making it suitable for various industrial applications.
Coating Type | Benefits |
---|---|
Nickel Plating | Good corrosion resistance, moderate hardness |
Nickel plating is beneficial for environments with high humidity or chemical exposure.
Phosphating
Phosphating creates a thin, porous layer on helical gear surface that improves lubrication retention and corrosion resistance.
Coating Type | Benefits |
---|---|
Phosphating | Enhanced lubrication retention, improved corrosion resistance |
Phosphating is often used in conjunction with other coatings or treatments to enhance their effectiveness.
Titanium Nitride (TiN)
Titanium Nitride coatings are known for their extreme hardness and wear resistance, making them suitable for high-stress applications.
Coating Type | Benefits |
---|---|
Titanium Nitride (TiN) | Extreme hardness, excellent wear resistance, low coefficient of friction |
TiN coatings are ideal for high-load, high-speed applications where wear resistance is crucial.
Diamond-Like Carbon (DLC)
Diamond-Like Carbon coatings provide exceptional hardness and low friction, enhancing both durability and performance.
Coating Type | Benefits |
---|---|
Diamond-Like Carbon | Exceptional hardness, very low friction, excellent wear resistance |
DLC coatings are particularly effective in reducing friction and wear in high-performance gears.
Benefits of Surface Coatings
Enhanced Durability
Surface coatings significantly increase the hardness and wear resistance of helical gear, leading to longer operational life.
Benefit | Description |
---|---|
Increased Hardness | Provides a tough surface that resists wear |
Wear Resistance | Reduces material loss and extends gear life |
Enhanced durability ensures that helical gear can withstand harsh operating conditions without frequent maintenance or replacement.
Improved Performance
Coatings reduce friction and improve the efficiency of helical gear, resulting in smoother operation and lower energy consumption.
Benefit | Description |
---|---|
Reduced Friction | Less energy loss, higher operational efficiency |
Smoother Operation | Lower noise and vibration levels |
Improved performance translates to better reliability and cost savings over helical gear’s lifespan.
Corrosion Resistance
Surface coatings protect helical gear from corrosive environments, which can otherwise lead to rapid deterioration and failure.
Benefit | Description |
---|---|
Corrosion Protection | Prevents rust and degradation in harsh environments |
Extended Lifespan | Reduces the impact of environmental factors |
Corrosion resistance is crucial for helical gear operating in challenging conditions such as high humidity or exposure to chemicals.
Heat Resistance
Certain coatings provide thermal protection, allowing helical gear to operate at higher temperatures without losing their structural integrity.
Benefit | Description |
---|---|
Thermal Stability | Maintains gear strength and hardness at high temperatures |
Improved Reliability | Reduces risk of thermal damage |
Heat resistance is essential for applications involving high-speed operations or significant frictional heating.
Practical Insights for Engineers
Selection of Surface Coating
Choosing the right surface coating depends on the specific application requirements and operating conditions.
Consideration | Impact on Selection |
---|---|
Operating Environment | Temperature, humidity, chemical exposure |
Load and Speed | Determines the need for wear and heat resistance |
Maintenance Practices | Frequency and ease of maintenance |
Selecting the appropriate coating ensures optimal helical gear performance and longevity.
Application Techniques
The method of applying surface coatings can affect their effectiveness and durability.
Technique | Description |
---|---|
Electroplating | Suitable for metal coatings like chrome and nickel |
Physical Vapor Deposition (PVD) | Ideal for thin, hard coatings like TiN and DLC |
Choosing the right application technique ensures a uniform and durable coating layer.
Testing and Validation
Thorough testing and validation of coated helical gear is essential to ensure their performance meets the required standards.
Method | Benefits |
---|---|
Wear Testing | Evaluates resistance to abrasion and wear |
Corrosion Testing | Assesses protection against environmental factors |
Performance Testing | Measures efficiency, noise, and vibration |
Testing provides insights into the effectiveness of the coatings under real-world conditions.
Case Studies
- Automotive Industry: A major automotive manufacturer implemented DLC coatings on transmission gears, resulting in significant reductions in wear and friction, leading to improved fuel efficiency and longer transmission life.
- Aerospace Applications: An aerospace company used TiN coatings on helicopter gears to enhance wear resistance and reduce maintenance costs, ensuring reliable performance under high-stress conditions.
- Industrial Machinery: An industrial equipment manufacturer applied nickel plating to helical gear used in chemical processing plants, achieving excellent corrosion resistance and prolonged gear lifespan.
Conclusion
Surface coatings play a vital role in enhancing the durability and performance of helical gear. By providing additional protection against wear, corrosion, and heat, these coatings ensure that helical gear can operate efficiently and reliably under demanding conditions. Engineers and manufacturers must carefully select and apply the appropriate coatings to maximize the benefits and achieve optimal gear performance. Through thorough testing and validation, the effectiveness of these coatings can be ensured, leading to longer-lasting and more efficient gear systems.