Abstract:
This paper focuses on improving the meshing state of standard tooth face herringbone gear by adopting modification techniques. To reduce vibration and noise during transmission and enhance the stability of the transmission system, Monte Carlo method and genetic algorithm are employed for topology modification. The quadratic parabola is selected as the modification curve. Load analysis under five working conditions is conducted on the modified gears. The results demonstrate a significant reduction in transmission error peak-to-peak value and maximum contact stress, along with improved contact stress distribution. Notably, the genetic algorithm exhibits more pronounced modification effects.
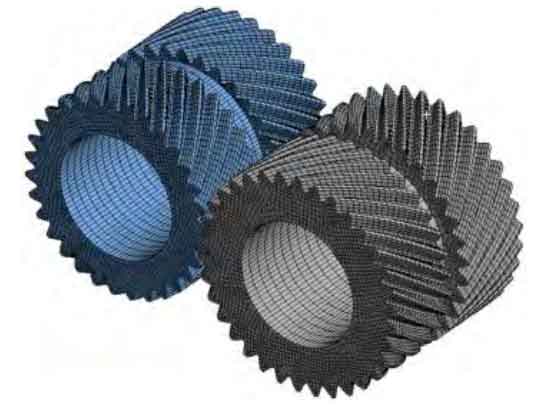
1. Introduction
Herringbone gear is widely utilized in aerospace, large ships, and other fields due to their advantages of high torque transmission capacity, compact structure, absence of additional axial force, and smooth operation. However, high torque and rotational speed lead to increased contact deformation of gear teeth, causing vibration and severe fatigue damage to the gear transmission system. Therefore, it is crucial to adopt reasonable methods for gear design and processing. Gear modification is a common measure to improve the meshing state of gear tooth surfaces. Proper modification can optimize the contact stress distribution on the tooth surface, reduce gear transmission error, and minimize vibration and noise, thereby mitigating fatigue damage to the gears.
2. Research Background and Methods
Previous studies on gear modification have primarily focused on spur gears, with relatively limited research on herringbone gear. The complex geometry of herringbone gear complicates the modification calculation process, resulting in low computational efficiency and poor applicability. In this study, based on ROMAX software, the gear transmission model is established, and Monte Carlo method and genetic algorithm are used for topology modification and load analysis to reduce vibration, noise, and improve the meshing state of the tooth surface.
Table 1: Basic Parameters of a Pair of Standard Herringbone Gear
Parameter | Unit | Pinion | Gear |
---|---|---|---|
Number of teeth | mm | 17 | 44 |
Normal module | mm | 6 | 6 |
Normal pressure angle | ° | 20 | 20 |
Helix angle | ° | 24.43 | -24.43 |
Helical direction | Left & right | Right & left | |
Effective tooth width (one side) | mm | 55 | 55 |
Table 2: Gear Drive System Working Conditions
Working Condition | Torque (N·m) |
---|---|
Condition 1 | 70 |
Condition 2 | 110 |
Condition 3 | 150 |
Condition 4 | 190 |
Condition 5 | 230 |
3. Tooth Surface Load Analysis
To facilitate processing, all modification results are applied to the pinion. The quadratic parabola is selected as the modification curve due to its good tolerance. Based on previous research on gear topology modification boundaries, the Monte Carlo method and genetic algorithm are used to obtain the topology modification results for the pinion, as shown in Figure 1. The modification results are superimposed on the standard tooth surface to obtain the transmission error curve, as shown in Figure 2. The transmission error peak-to-peak values and contact stress distributions are summarized in Tables 3 and 4, respectively, along with corresponding figures (Figures 3 to 8) illustrating the contact stress distributions under different working conditions.
Table 3: Change in the Amplitude of Transmission Error
Working Condition | Standard Tooth Surface (μm) | Monte Carlo Method (μm) | Reduction (%) | Genetic Algorithm (μm) | Reduction (%) |
---|---|---|---|---|---|
Condition 1 | 0.255 | 0.094 | 63.14 | 0.078 | 69.41 |
Condition 2 | 0.400 | 0.141 | 64.75 | 0.112 | 72.00 |
Condition 3 | 0.545 | 0.290 | 46.79 | 0.239 | 56.15 |
Condition 4 | 0.689 | 0.402 | 41.65 | 0.345 | 49.93 |
Condition 5 | 0.832 | 0.445 | 46.51 | 0.421 | 49.40 |
Table 4: Maximum Contact Stress Value (MPa)
Working Condition | Before Modification | Monte Carlo Method | Reduction (%) | Genetic Algorithm | Reduction (%) |
---|---|---|---|---|---|
Condition 1 | 339 | 345 | -1.74 | 320 | 5.94 |
Condition 2 | 428 | 410 | 4.39 | 382 | 12.04 |
Condition 3 | 502 | 459 | 9.37 | 434 | 15.67 |
Condition 4 | 567 | 500 | 13.40 | 479 | 18.37 |
Condition 5 | 626 | 537 | 16.57 | 520 | 20.38 |
4. Conclusion
(1) By comparing the transmission error and contact stress distribution of standard tooth surface gears and modified gears under set working conditions, it is demonstrated that gear modification reduces the peak-to-peak value of transmission error and the maximum contact stress, shifting it towards the middle of the tooth surface. This reduces stress concentration at the edges and improves the contact stress distribution.
(2) Under the same working conditions, the modification results obtained using the genetic algorithm are more effective in reducing the peak-to-peak value of transmission error and the maximum contact stress compared to the Monte Carlo method. Therefore, the genetic algorithm exhibits superior modification effects.
In summary, this study provides valuable insights into the topology modification of herringbone gear, offering a practical approach to enhance their performance and reliability in various applications.