Hypoid gear is integral components in various high-performance applications, including automotive differentials, aerospace systems, and industrial machinery. The fatigue life of these gears, which determines their durability and reliability, is significantly influenced by the surface treatments applied during manufacturing. This article examines the various surface treatments used on hypoid gear and their impact on fatigue life, providing a comprehensive understanding of how these treatments enhance gear performance.
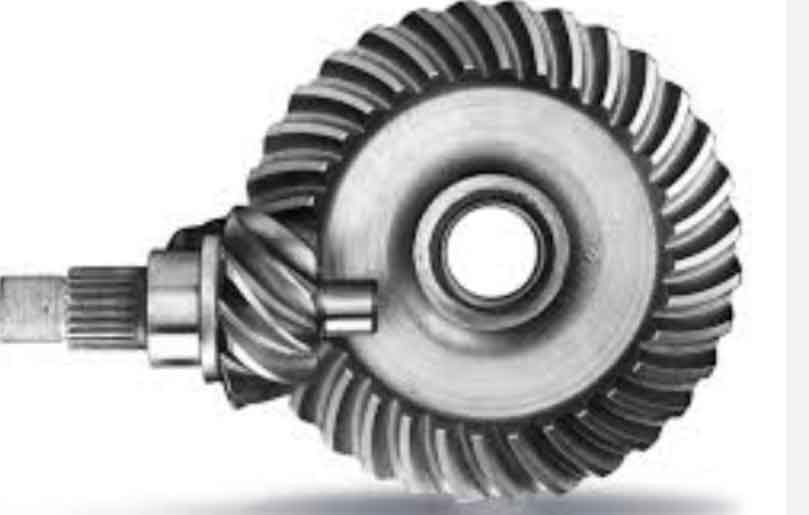
Introduction
The fatigue life of hypoid gear is a critical parameter that affects their operational longevity and maintenance requirements. Surface treatments are employed to enhance the surface properties of hypoid gear, such as hardness, wear resistance, and corrosion resistance, thereby extending their fatigue life. Understanding the effects of different surface treatments is essential for optimizing gear performance and ensuring reliability under demanding conditions.
Types of Surface Treatments
- Carburizing:
- Carburizing is a heat treatment process that introduces carbon into the surface layer of hypoid gear.
- It increases surface hardness and wear resistance, improving hypoid gear’s ability to withstand fatigue.
- Nitriding:
- Nitriding involves diffusing nitrogen into hypoid gear surface at a low temperature.
- This process creates a hard, wear-resistant surface without the need for quenching, reducing distortion.
- Induction Hardening:
- Induction hardening uses electromagnetic induction to heat hypoid gear surface, followed by rapid cooling.
- It provides localized hardening, enhancing surface hardness and fatigue resistance.
- Shot Peening:
- Shot peening bombards hypoid gear surface with small spherical media, inducing compressive residual stresses.
- This treatment improves fatigue resistance by reducing the likelihood of crack initiation and propagation.
- Coating Treatments:
- Coatings such as diamond-like carbon (DLC) and tungsten carbide (WC) are applied to hypoid gear surfaces to reduce friction and wear.
- These coatings also enhance surface hardness and corrosion resistance, contributing to extended fatigue life.
Comparative Analysis of Surface Treatments
Surface Treatment | Advantages | Disadvantages |
---|---|---|
Carburizing | Increased surface hardness, improved wear resistance | Potential distortion, long process time |
Nitriding | Enhanced wear resistance, minimal distortion | Limited to certain steel alloys |
Induction Hardening | Localized hardening, improved fatigue resistance | Requires precise control, limited depth |
Shot Peening | Induces compressive stresses, reduces crack initiation | Surface roughness increase, process control required |
Coating Treatments | Reduced friction, enhanced hardness and corrosion resistance | Additional cost, potential coating failure under extreme conditions |
Impact of Surface Treatments on Fatigue Life
1. Carburizing
Carburizing significantly enhances the fatigue life of hypoid gear by increasing surface hardness and wear resistance. The carbon-enriched surface layer can withstand higher cyclic stresses, reducing the risk of surface fatigue failures. However, the process may introduce residual stresses and distortion, which must be carefully controlled.
2. Nitriding
Nitriding produces a hard, wear-resistant surface with minimal distortion, making it ideal for precision gears. The nitrogen-enriched surface layer improves fatigue resistance by reducing surface wear and enhancing load-bearing capacity. This process is particularly effective for hypoid gear that require high surface hardness without compromising core toughness.
3. Induction Hardening
Induction hardening provides localized surface hardening, improving fatigue resistance by creating a hard, wear-resistant surface layer. The rapid cooling involved in this process induces beneficial compressive residual stresses, which help prevent crack initiation and propagation. However, precise control of the heating and cooling process is essential to avoid surface defects.
4. Shot Peening
Shot peening enhances fatigue life by inducing compressive residual stresses on hypoid gear surface. These stresses counteract the tensile stresses experienced during operation, reducing the likelihood of crack formation. Shot peening also improves resistance to surface fatigue and stress corrosion cracking, making it an effective treatment for hypoid gear subjected to high cyclic loads.
5. Coating Treatments
Advanced coatings such as DLC and WC reduce friction and wear, extending the fatigue life of hypoid gear. These coatings provide a hard, low-friction surface that minimizes wear and heat generation during operation. Additionally, coatings enhance corrosion resistance, protecting hypoid gear from environmental degradation and further extending their service life.
Factors Affecting the Efficacy of Surface Treatments
- Material Composition: The effectiveness of surface treatments depends on hypoid gear material’s composition and microstructure.
- Process Parameters: Precise control of process parameters, such as temperature, time, and cooling rate, is crucial for achieving optimal results.
- Surface Preparation: Proper surface preparation before treatment ensures uniform and effective application of the treatment.
- Operational Conditions: The operating environment, including load, speed, and temperature, influences the performance of treated surfaces.
Future Directions in Surface Treatments
- Hybrid Treatments:
- Combining multiple surface treatments, such as carburizing followed by shot peening, can provide synergistic benefits, enhancing fatigue life beyond what is achievable with a single treatment.
- Nano-Coatings:
- The development of nano-coatings with superior hardness and low friction properties is an emerging area of research.
- These coatings offer significant potential for improving fatigue life and wear resistance.
- Smart Coatings:
- Smart coatings that can adapt to changing operational conditions are being explored.
- These coatings can alter their properties in response to load, temperature, and other factors, optimizing performance in real-time.
Conclusion
Surface treatments play a crucial role in enhancing the fatigue life of hypoid gear. By improving surface hardness, wear resistance, and inducing beneficial residual stresses, these treatments significantly extend the operational lifespan of hypoid gear. The ongoing advancements in surface treatment technologies, including hybrid treatments, nano-coatings, and smart coatings, promise further improvements in gear performance and reliability. As the demands on hypoid gear continue to increase, the importance of advanced surface treatments in ensuring their durability and efficiency cannot be overstated.