1. Introduction
Beveloid gears with crossed axes are widely used in various fields such as all-wheel-drive vehicles, marine gearboxes, and industrial robots due to their compact structure, high transmission efficiency, and low cost. They have broad market application prospects. In recent years, numerous studies have been conducted on beveloid gears by scholars at home and abroad. For example, Cao et al. proposed a numerical calculation method for contact pressure and load distribution of crossed-axis beveloid gears and verified its feasibility through examples. Sun et al. analyzed the influence of pitting defects of different sizes and positions and obtained a numerical calculation method for irregular thickening of tooth profile meshing stiffness. Liu et al. proposed a geometric design method for face-milling hypoid beveloid gears with small crossed angles and a meshing characteristic control method considering the smooth transition of the tooth root. Zhu et al. established a beveloid gear model by inclined shaping and proposed two methods for calculating the tooth thickness error of spur beveloid gears. Song et al. studied the dynamic response of beveloid gears in marine gearboxes with cross-shaped helical gears. Ni et al. described a method for calculating the influence of geometric design parameters and gear profile shift on the contact ellipse of crossed-axis beveloid gear pairs and explored the influence of tool modification on the machining of beveloid gears. Ye et al. proposed a new worm drive with adjustable backlash and obtained its design criteria and experimental results. Liu et al. analyzed the contact characteristics of beveloid gears with concave and convex modifications. Ni et al. analyzed the influence of four different machining path curves on the contact characteristics of crossed-axis nonlinear profile-shifted beveloid gears. Zhou et al. studied the meshing characteristics of involute cylindrical and beveloid gears with small crossed angles under different modification methods and amounts. Zhu et al. studied the sensitivity of the contact path and transmission error of beveloid gear pairs with small shaft angles to angular errors. Deng et al. studied the meshing characteristics of beveloid gears in RV reducers and provided a theoretical basis for improving the load-carrying capacity of RV reducers. Zou et al. realized the electronic control of the backlash of beveloid gear pairs through experiments. Li et al. proposed a grinding method for beveloid gears with tapered worm grinding wheels and verified the superiority of the process.
In this paper, a parabolic rack cutter is introduced into the beveloid gear transmission, and the tooth surface equation of the beveloid gear machined by the parabolic cutter is derived. The influence of the parabolic modification coefficient on the contact path of the gear pair under different geometric design parameters is studied by the tooth contact analysis method. The influence of the parabolic modification on the tooth surface contact force, transmission error, tooth root stress, and meshing mark of the gear pair with different FPD angles is studied, and the superiority of the parabolic rack cutter in machining beveloid gears is verified.
2. Mathematical Model of Beveloid Gear Machined by Parabolic Cutter
2.1 Coordinate System Establishment
The machining of beveloid gears by a parabolic cutter involves multiple coordinate systems. As shown in Figure 1, , , and are coordinate systems fixed on the rack cutter. and are the midpoint and width of the cutter pitch plane tooth groove, respectively. is the parabolic modification coefficient, is the tooth surface parameter of the rack cutter ( for the two beveloid gears), and is the circular pitch. Figure 2 shows the machining coordinate system of the rack cutter for machining the beveloid gear, including , , for the rack cutter coordinate system, as the auxiliary coordinate system, and as the moving coordinate system of the gear blank with the gear blank rotation angle .
2.2 Tooth Surface Equation Derivation
Based on the hobbing machining theory, the tooth surface equation of the beveloid gear machined by the parabolic cutter is derived. The traditional rack cutter tooth profile is usually a straight line, and in this paper, the straight line segment is replaced by a parabola to achieve the parabolic modification of the rack cutter. As shown in Figure 1, for any point on the parabola in the coordinate system, its coordinate can be expressed as . Through coordinate transformation from to and then to , the tooth surface equation of the parabolic segment in the pitch plane coordinate system can be obtained as . Therefore, the tooth surface equation of the beveloid gear machined by the parabolic cutter in the coordinate system is ().
3. Tooth Contact Analysis
3.1 Contact Equation and Analysis Model
Based on the spatial gear meshing principle, when two gears are in mesh, their contact surfaces are always in a tangent state. Therefore, analyzing the contact path of the gear teeth can well simulate the actual contact situation of the gear teeth. By the TCA method, the contact equation is . Through the derivation of the tooth surface mathematical model of the parabolic modified beveloid gear, the TCA analysis model of the crossed-axis beveloid gear transmission is established, as shown in Figure 3. In the model, is the center distance between the two axes, is the shaft angle, #\## is the working pitch circle radius, is the tangent contact point, and are the distances from the working pitch plane of the beveloid gear to the coordinate system, and are the moving coordinate systems fixed on the gears for tooth contact analysis, and are the reference coordinate systems, and and are the auxiliary coordinate systems.
3.2 Influence of Parabolic Modification on Contact Path
Two sets of typical geometric design parameters of the crossed-axis beveloid gear pair are designed, as shown in Table 1. In the two sets of geometric parameters, the pitch cone angle and helix angle of the gear are changed, respectively, so that the FPD angle changes accordingly. By performing contact analysis and load analysis on the two examples, the influence law of the parabolic cutter on the TCA of the crossed-axis beveloid gear can be clearly obtained.
Parameter | Example 1 | Example 2 | ||
---|---|---|---|---|
Pinion | Gear | Pinion | Gear | |
Normal module/mm | ||||
Normal pressure angle/(°) | 20 | |||
Number of teeth | 29 | 45 | 29 | 45 |
Pitch cone angle/(°) | 3.0 | 0.8 | 2.0 | 1.0 |
Helix angle/(°) | 25 | -10.57 | 23 | -8.40 |
(RH) | (LH) | (RH) | (LH) | |
Center distance/mm | 229 | |||
Shaft angle/(°) | ||||
Profile shift coefficient of pitch end face | 0.17 | 0.2181 | 0.15 | 0.2054 |
Tooth width/mm | 50 | 60 | 50 | 60 |
FPD angle/(°) | 2.2811 | 2.9976 |
Taking the second example in Table 1 (FPD is 2.9976°), the influence of the contact path length and position under different modification coefficients is explored. As shown in Figure 4, the left figure is the contact path diagram of the pinion, and the right figure is the tooth surface contact path diagram of the gear. It can be observed that as the tool modification coefficient increases, the angle between the contact path and the axial direction gradually decreases, but the contact path length significantly increases. It can be seen that the parabolic modification can effectively increase the contact path length of the crossed-axis beveloid gear pair, reduce the relative sliding speed between the gear pairs, reduce the wear between the gears, and improve the service life of the gears. As shown in Figure 5, the change of the contact ellipse of the gear under different modification coefficients is shown. The blue ellipse is the contact area of the gear pair, the red circle is a certain number of points selected on the contact path, and the black outer frame represents the tooth profile. It can be seen from the figure that as the modification coefficient increases, the contact ellipse area continuously increases, and the contact path length also increases, which is consistent with the above conclusion.
4. Loaded Contact Analysis
4.1 LTCA Analysis Model
To further explore the influence law of the parabolic tool modification coefficient on the contact characteristics of the crossed-axis beveloid gear under different geometric design parameters, a three-dimensional model of the crossed-axis beveloid gear is established and imported into the finite element analysis software ABAQUS for LTCA analysis. The meshing analysis model of the crossed-axis beveloid gear pair is shown in Figure 6. The pinion is modified positively, and the gear is modified negatively, and a load of 400N·m is applied to calculate the tooth surface contact force, transmission error, meshing mark, and tooth root stress. The results are compared with the data before modification.
4.2 Influence of Parabolic Modification on Contact Characteristics
- Tooth Surface Contact Force: As shown in Figure 7, the change of the tooth surface contact force of the pinion during meshing is shown. The blue solid line represents the change of the tooth surface contact force before modification, and the red dashed line represents the change of the tooth surface contact force after modification. The square and circle represent Example 1 and Example 2 in Table 1, respectively. It can be observed that compared with the data before modification, the maximum value of the tooth surface contact force after modification is significantly reduced, indicating that the parabolic tool modification effectively reduces the maximum contact force of the tooth surface. Moreover, after modification, the maximum value of the tooth surface contact force in Example 1 is smaller than that in Example 2, indicating that the smaller the FPD angle, the more obvious the reduction of the maximum value of the tooth surface contact force.
- Transmission Error: As shown in Figure 8, the transmission error curves of the beveloid gear pair before and after parabolic modification in the two examples are shown. It can be seen that after the tool is modified by a parabola, the transmission error of the machined crossed-axis beveloid gear pair is reduced, and the transmission error of the gear pair is significantly reduced with the decrease of the FPD angle.
- Tooth Root Stress: As shown in Figure 9, the influence of the parabolic modification of the tool on the tooth root stress of the large and small gears along the tooth width direction in the two examples is shown. It can be seen that compared with before modification, the tooth root stresses of the large and small gears after modification are both reduced, indicating that the parabolic tool modification can effectively reduce the tooth root stress of the large and small gears, improve the transmission efficiency, and increase the service life of the gears. Before and after modification, the maximum value of the tooth root stress in Example 2 is greater than that in Example 1, and this rule is more obvious before modification than after modification, indicating that the larger the FPD angle, the greater the tooth root stress of the gear.
- Meshing Mark: To further verify the correctness of the above results, the meshing mark diagrams of the gear before and after modification in the two examples are extracted. As shown in Figure 10, (a) and (b) are the tooth surface meshing marks of the gear with an FPD angle of 2.2811° before and after parabolic modification, respectively, and (c) and (d) are the tooth surface meshing marks of the gear with an FPD angle of 2.9976° before and after modification, respectively. It can be found that the meshing marks before and after modification under different parameters do not change much, indicating that the parabolic tool modification has little influence on the surface contact stress of the gear. However, in Example 2, the change of the meshing mark after modification is more obvious than that in Example 1, indicating that under different FPD angles, the parabolic tool modification has different degrees of reduction in the tooth surface contact stress. The larger the FPD angle, the more obvious the reduction. Moreover, in the two examples, the meshing mark area of Example 1 is larger and the color is lighter, indicating that the smaller the FPD angle, the smaller the tooth surface bearing capacity, the larger the meshing contact area of the gear pair, and the better the meshing effect.
5. Conclusion
- The parabolic rack cutter is introduced into the crossed-axis beveloid gear transmission. Under different design parameters, the parabolic cutter can effectively increase the contact path length and the contact ellipse area of the crossed-axis beveloid gear pair.
- The parabolic tool modification can effectively reduce the maximum value of the tooth surface contact force and the tooth root stress of the gear, improve the transmission efficiency, and increase the service life of the gear.
- After the tool is modified by a parabola, the maximum value of the tooth surface contact force of the crossed-axis beveloid gear decreases more obviously with the decrease of the FPD angle, the transmission error is significantly reduced, and the smaller the FPD angle, the smaller the tooth surface bearing capacity and the tooth root stress, the larger the meshing contact area of the gear pair, and the better the meshing effect.
The research in this paper provides a new idea for the modification method of beveloid gear transmission and has certain theoretical and practical significance for the design and optimization of beveloid gear transmission. Future research can further explore the influence of other factors on the contact characteristics of beveloid gears and improve the performance of beveloid gear transmission.
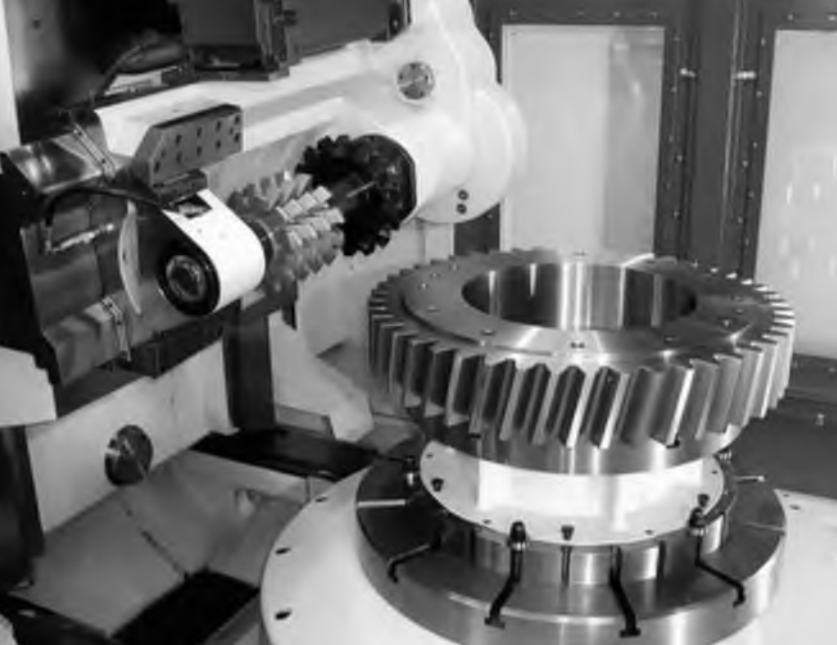