The main structural design parameters of circular arc gear include pressure angle, tooth width, tooth radius, modulus, etc. Since there are relevant standards for gear modulus and pressure angle, this paper mainly discusses the influence of design parameters, tooth width and tooth line radius on gear profile characteristics.
When the parallel linkage mechanism is used to process cylindrical gear with circular arc tooth line, the variation curve of tooth thickness at different tooth width is shown in Fig. 1 when m = 4, z = 31, and tooth radius is 100 mm and 400 mm respectively.
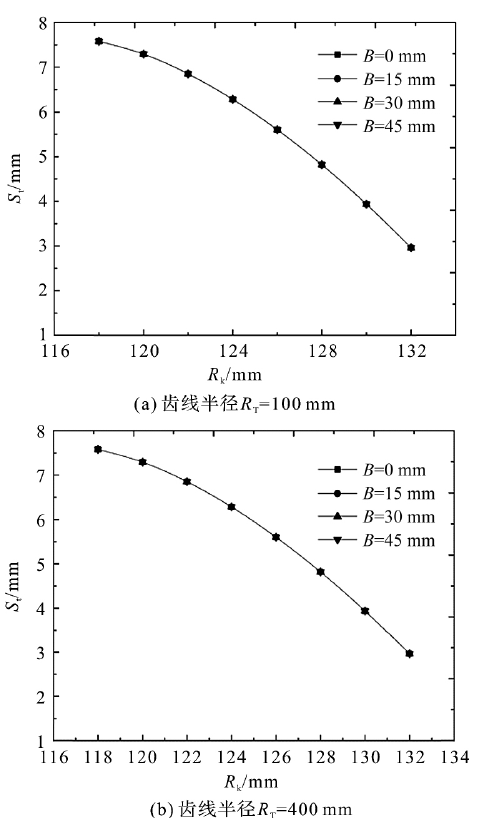
When the rotary cutter head is used to mill the cylindrical gear with circular tooth profile, when m = 4, z = 31, and the tooth radius is 100 mm and 400 mm respectively, the variation curve of tooth thickness at different tooth width is shown in Fig. 2.
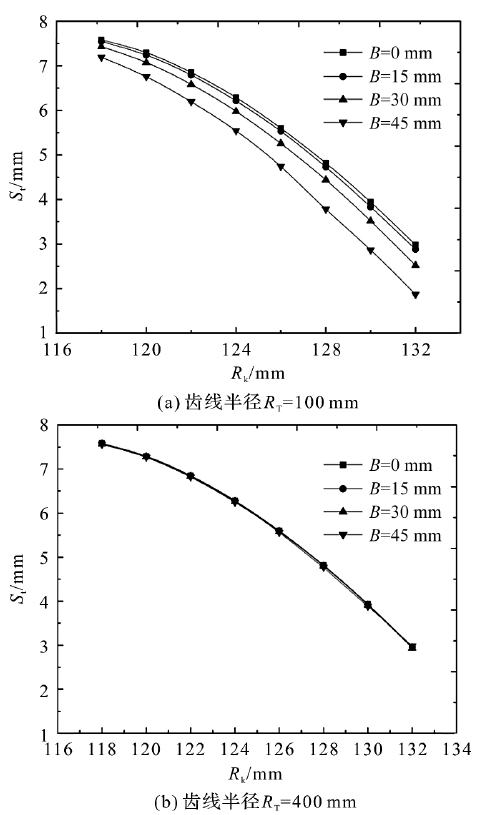
In figure (1, 2), B = 15 mm indicates that the distance between the measured section of tooth profile and the section in gear is 15 mm, and so on.
It can be seen from figures (1,2)
The results show that: (1) the tooth thickness of cylindrical gear with circular tooth profile processed by parallel linkage mechanism has no change at different tooth radius and tooth width, which is consistent with the principle of gear forming. The reason is that the tooth profile of each section of the gear is involute, and the tooth thickness remains unchanged;
(2) for the cylindrical gear with circular tooth profile milled by rotating cutter head, the tooth thickness decreases with the distance between the measured section and the middle section of the gear, especially when the tooth line radius is small, the change of tooth thickness is large. The reason is that the gear profile in the middle section is an involute profile, and the profile of other sections is a hyperbolic envelope.
In order to accurately and clearly compare and analyze the difference characteristics of the gear profile obtained by the two machining methods, the author defines the tooth thickness of gear machined by parallel connecting rod minus the tooth thickness of gear machined by rotating cutter head as the tooth thickness deviation E. on this basis, the influence of tooth line radius and tooth width on the tooth thickness deviation is analyzed respectively.