Abstract
The efficient and precise modeling of gear contact under the influence of elasticity and errors is crucial for studying the transmission accuracy characteristics of gears. This paper proposes a semi-analytical contact model for cylindrical gears that accounts for elastic errors. Taking involute cylindrical gears as an example, an error tooth surface equation is established by combining the tooth surface equation with tooth profile errors. Subsequently, a semi-analytical contact model is developed by integrating analytical methods with finite element analysis (FEA), and the deformation coordination equation and force balance equation are derived. Finite element models are constructed for the complete and local gear geometries, and the transmission accuracy is calculated by extracting the compliance matrix of the contact tooth surfaces. The influence of profile errors and elastic deformations on the transmission accuracy of helical gears is analyzed using the semi-analytical model, and the results are compared with those from FEA, verifying the model’s efficiency and accuracy. This research provides theoretical guidance for the engineering application of cylindrical gears.
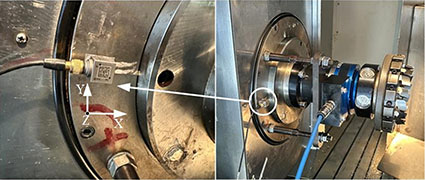
1. Introduction
Transmission error, which significantly affects the transmission accuracy and dynamic characteristics of gears, is a crucial parameter to consider in the design and analysis of gear systems. Accurate modeling and analysis of transmission errors are essential for enhancing the performance of gear transmissions. Various modeling approaches, including analytical, finite element, and semi-analytical methods, have been developed to address this challenge.
Analytical methods offer high computational efficiency but may lack precision in capturing gear structural elasticity. On the other hand, finite element methods provide high accuracy but require significant computational resources and time. To balance efficiency and accuracy, semi-analytical methods have emerged as a promising alternative.
This paper focuses on developing a semi-analytical contact model for cylindrical gears that incorporates elastic errors. The model aims to improve the understanding of the influence of elastic deformations and profile errors on transmission accuracy.
2. Literature Review
2.1 Modeling Methods for Transmission Error
Finite Element Analysis (FEA): FEA is a popular method for analyzing gear transmission errors due to its ability to capture complex geometries and material behaviors. Korta et al. [1] studied the static transmission error of lightweight gears using FEA. However, FEA is computationally intensive, requiring significant time and resources for detailed models.
Analytical Methods: Analytical methods, such as those employed by Zou et al. [7], offer fast computation times but may overlook structural elasticity, limiting their accuracy.
Semi-Analytical Methods: To bridge the gap between efficiency and accuracy, semi-analytical methods have gained attention. Dong et al. [13] developed a semi-analytical model for face gear systems, demonstrating improved computational efficiency while maintaining accuracy.
2.2 Factors Affecting Transmission Error
Multiple factors, including material properties, tooth profile errors, and loads, impact transmission error. Korta et al. [1] investigated the influence of material properties, while Zou et al. [7] focused on gear eccentricity. However, few studies have comprehensively considered the effect of elastic errors on transmission accuracy.
3. Error Tooth Surface Model for Involute Cylindrical Gears
3.1 Basic Tooth Surface Equation
The tooth surface of an involute cylindrical gear is generated by a curve that is stretched uniformly along a helical path. The parametric equation of the involute helical surface can be expressed as:
begincasesx=rbsin(θ+uk)−rbukcos(θ+uk)y=rbcos(θ+uk)+rbuksin(θ+uk)z=pθendcases
where rb is the base circle radius, θ is the rotation angle, p is the helix parameter, and uk is the involute occurrence angle.
3.2 Error Tooth Surface Equation
Tooth profile errors are incorporated into the tooth surface model by discretizing the tooth profile and calculating the deviation from the ideal profile. The tooth profile error Δf at a point K on the profile can be expressed as:
Deltaf=fsin[2π(re−r0r−r0)]
where f is the maximum tooth profile error, r0 is the distance from the first discrete point to the gear center, re is the distance from the end point of the profile to the gear center, and r is the distance from an arbitrary discrete point K to the gear center.
The new coordinates of the discrete points on the error tooth surface, denoted as K′(xk′,yk′), are calculated by offsetting the original points along their normal directions:
begincasesxk′=xk+Δfcosϕkyk′=yk+Δfsinϕkendcases
where ϕk is the angle between the normal direction at point K and the x-axis.
4. Semi-Analytical Contact Model Considering Elastic Errors
4.1 Deformation Coordination Equation
During gear meshing, contact can be modeled as the interaction of elastic bodies. The deformation coordination equation at contact point i can be expressed as:
Qi=ϵi+σi−Ui
where Qi is the final gap between contact point i and its counterpart, ϵi is the initial contact gap due to errors, Ui is the displacement caused by rigid body motion with six degrees of freedom, and σi is the elastic deformation at contact point i.
Elastic deformation σi comprises contact deformation σhi and bending-shear deformations σb1 and σb2 of the driving and driven gears, respectively:
sigmai=σhi+σb1+σb2
Local deformation at the contact point can be calculated using Hertzian contact theory:
ui=πliE2Fi(lnBi2wi+0.148)
where ui is the local deformation, Fi is the normal force at contact point i, li is the contact line length, E is the equivalent elastic modulus, wi is the gear thickness at the contact point, and Bi is the half-width of the contact region.
4.2 Force Balance Equation
The force balance equations for the driving and driven gears are derived to solve for the contact forces. For the driving gear, the force balance equation can be written as:
mathbfT1=G1TF12+K1Φ1
where T1 is the external load vector, F12 is the contact force vector from the driven gear, K1 is the support stiffness matrix of the driving gear, and Φ1 is the rigid displacement vector of the driving gear. A similar equation can be derived for the driven gear.
4.3 Compliance Matrix Extraction
The complete compliance matrix λw of the gear system is obtained by combining the bending-shear compliance matrices λb1 and λb2 of the driving and driven gears, respectively, with the contact compliance matrix λh:
lambdaw=λb1+λb2+λh
The elastic deformation vector σ is then calculated as:
sigma=λwF
where F is the normal force vector at the contact points.
5. Case Study and Results
5.1 Model Validation
To validate the semi-analytical model, a case study was conducted using the parameters of a helical gear pair (Table 1). The transmission errors calculated using the semi-analytical model were compared with those obtained from FEA. The results showed good agreement, with a maximum relative error of 5.8% and a minimum relative error of 3.2% (Figure 5). Notably, the semi-analytical model was 79.57 times faster than FEA.
Table 1. Basic Parameters of the Helical Gear Pair
Parameter | Value |
---|---|
Number of teeth (z) | 36 |
Module (m) | 3 mm |
Pressure angle (α) | 20° |
Face width (B) | 30 mm |
Helix angle (β) | 15° |
Addendum coefficient | 1 |
Dedendum coefficient | 1.25 |
Elastic modulus (E) | 206 GPa |
Poisson’s ratio (μ) | 0.3 |
5.2 Influence of Tooth Profile Errors
The effect of tooth profile errors on transmission accuracy was investigated using the semi-analytical model. With a 4-grade tooth profile error, the transmission error increased significantly compared to the case without errors (Figure 6). The transmission accuracy degraded from 1.133 × 10-5 rad.
5.3 Influence of Loads
The transmission error was analyzed under different loads (100, 200, 300, and 400 N·m). As the load increased, the transmission error also increased, indicating that loads significantly impact transmission accuracy (Figure 7).
5.4 Influence of Tooth Profile Error Grades
The influence of different tooth profile error grades (none, 4-grade, and 5-grade) on transmission accuracy was studied under a load of 100 N·m. The transmission error increased with the error grade, with the 5-grade error causing the largest variation in transmission accuracy (Figure 8).
6. Conclusions
This paper presented a semi-analytical contact model for cylindrical gears considering elastic errors. By combining analytical and finite element methods, the model efficiently calculates transmission errors while maintaining high accuracy. The model was validated against FEA results, demonstrating a 79.57 times improvement in computational efficiency. The influence of tooth profile errors and loads on transmission accuracy was investigated, providing valuable insights for engineering applications of cylindrical gears.