Loaded transmission error is an important indicator for evaluating the dynamic meshing performance of gears. The smaller the fluctuation amplitude of the loaded transmission error, the better the dynamic meshing performance of the gear pair. With the increase in gear speed, the requirements for the fluctuation amplitude of the loaded transmission error become higher and higher.
Although there have been many studies on gear loaded transmission error in recent years, the analysis of internal spur gears is relatively insufficient. Internal meshing transmission is generally used in planetary transmissions, usually in the form of short tooth height. Therefore, this article mainly discusses the modification methods of internal short tooth spur gears.
Modeling of Internal Short Tooth Spur Gears:
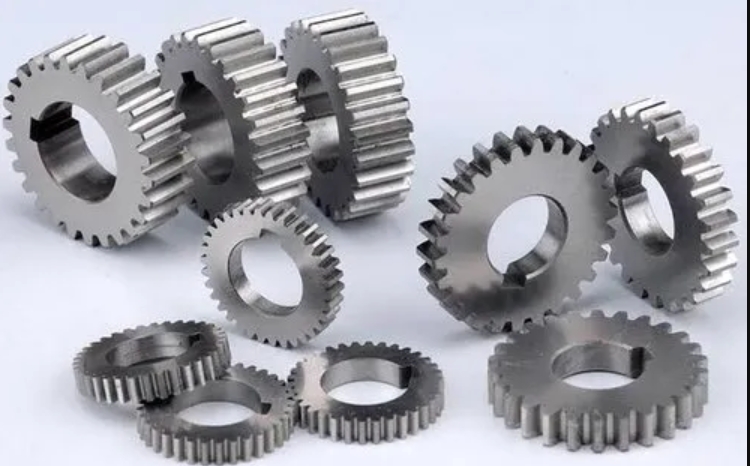
- Gear modeling is carried out in the Romax software. The type of gear set is defined as spur gears, and the gears are defined using parameters such as pressure angle, module, modification coefficient, tooth width, addendum coefficient, and dedendum coefficient.
- The parameters of the internal gear pair studied in this article are shown in Table 1. For the internal gear pair, the pinion is solid, and the rim thickness of the gear needs to be considered. The formula for calculating the rim thickness of the gear is δ0 = (2.5 – 4)m, where m ≥ 8. Here, the rim thickness is taken as 16 mm.
Modification Methods for Spur Gears:
- Tooth Profile Modification:
- The tooth profile modification parameters include the modification amounts and lengths at the tooth top and root. To facilitate the modification processing, the tooth profile modification diagram is represented along the tooth height direction, as shown in Figure 1.
- The tooth top modification and tooth root modification can take the form of a parabola or a straight line. In Figure 1, y1 is the maximum modification amount at the tooth top, y2 is the modification length in the tooth height direction at the tooth top, y3 is the maximum modification amount at the tooth root, and y4 is the modification length in the tooth height direction at the tooth root.
- Considering the convenience of processing, only the pinion is modified, and the gear is not modified.
- To analyze the influence of the tooth profile modification parameters on the loaded transmission error, the range of the modification parameters needs to be determined first. The maximum modification amounts at the tooth top and root are respectively taken as five values: 0.010 mm, 0.015 mm, 0.020 mm, 0.025 mm, and 0.030 mm.
- Helix Modification:
- The helix modification of the pinion includes end slope and drum-shaped modification. This article compares and analyzes these two modification methods, as shown in Figure 2.
- In Figure 2, y5 is the maximum helix modification amount. In Figure 2(a), y6 is the modification length of the helix slope. The modification curve of the slope is a straight line, and the drum-shaped modification is a parabola.
- For the slope modification, the maximum modification amount is generally 13 – 35 μm, and the modification length is 0.25b, where b is the tooth width. For the drum-shaped modification, for high-precision and high-reliability gears, the drum-shaped modification amount is 10 – 25 μm, plus the manufacturing error of 5 μm.
- Similarly, to analyze the influence of the helix modification amount on the loaded transmission error, the maximum helix modification amount y5 is respectively taken as five values: 0.010 mm, 0.015 mm, 0.020 mm, 0.025 mm, and 0.030 mm.
- When analyzing the influence of the tooth profile modification parameters, the helix modification adopts the drum-shaped modification, and the modification parameters are fixed. When analyzing the influence of the helix modification parameters, the helix modification adopts the comparison and analysis of the end slope and drum-shaped modification.
Analysis of Modification for Internal Spur Gear Pairs:
- Influence of Tooth Profile Modification Parameters on Loaded Transmission Error:
- To compare and analyze the influence of tooth surface modification on the loaded transmission error, the loaded transmission error of the unmodified standard tooth surface is first simulated using the Romax software, as shown in Figure 3. The fluctuation amplitude of the loaded transmission error is 6.69 μm.
- To analyze the influence of each tooth profile modification parameter on the loaded transmission error, the helix adopts the drum-shaped modification, and the drum-shaped modification amount y5 is kept at 0.020 mm. The tooth profile modification parameters are as follows:
- The maximum modification amount at the tooth top changes, and other modification parameters remain unchanged, y2 = 1.0Ld mm, y3 = 0.020 mm, y4 = 1.0Lg mm.
- The maximum modification amount at the tooth root changes, and other modification parameters remain unchanged, y1 = 0.020 mm, y2 = 1.0Ld, y4 = 1.0Lg mm.
- In the above modification parameter analysis, the modification lengths at the tooth top and root are taken as the length of the double tooth meshing area, where Ld represents the tooth top modification length, and Lg represents the tooth root modification length.
- The analysis result of the first case is shown in Figure 4. With the increase in the maximum modification amount at the tooth top, the fluctuation amplitude of the loaded transmission error first decreases and then increases. The best effect can be achieved by optimizing the maximum modification amount at the tooth top.
- The analysis result of the second case is shown in Figure 5. For the parabolic modification, with the increase in the maximum modification amount at the tooth root, the fluctuation amplitude of the loaded transmission error decreases. However, for the linear modification, the fluctuation amplitude of the loaded transmission error first decreases and then increases.
- Influence of Helix Modification Parameters on Loaded Transmission Error:
- As mentioned earlier, when analyzing the influence of the helix modification parameters, the helix modification adopts the comparison and analysis of the end slope and drum-shaped modification. The maximum helix modification amount changes, and other modification parameters remain unchanged, y1 = 0.020 mm, y2 = 1.0Ld, y3 = 0.020 mm, y4 = 1.0Lg, y6 = 0.25b.
- The analysis result is shown in Figure 6. With the increase in the maximum helix modification amount, the fluctuation amplitude of the loaded transmission error increases, which is caused by the decrease in the tooth stiffness with the increase in the modification amount. In addition, the drum-shaped modification is better than the end slope.
- By comparing Figure 6, it can be seen that reasonable modification can effectively reduce the fluctuation amplitude of the loaded transmission error.
Optimization Design of Modification Parameters:
- To obtain a better modification effect, this article studies the optimization design method of the modification parameters for the parabolic tooth profile modification and the drum-shaped helix modification, so as to minimize the fluctuation amplitude of the loaded transmission error.
- The Loaded Tooth Contact Analysis (LTCA) method is used to obtain the loaded transmission error represented by the rotation angle. The same way of only modifying the pinion and not modifying the gear is adopted, and only the modification parameters of the pinion are optimized. To achieve better optimization results, the maximum modification amount of the tooth profile, the modification length, and the maximum helix modification amount are optimized.
- The Particle Swarm Optimization (PSO) algorithm is used. PSO is a kind of random optimization technique based on swarm intelligence. Compared with the genetic algorithm, both are based on iterative search of the population, but the PSO algorithm does not have crossover and mutation operators and searches for the optimal solution through the collaboration of individuals. It utilizes the idea of information sharing in biological populations. The PSO algorithm is easy to implement and is more suitable for engineering applications.
- The modification optimization parameters are y1, y2, y3, y4, and y5, and the particle is defined as Y = [y1 y2 y3 y4 y5]. The objective function f is the fluctuation amplitude of the loaded transmission error, which is calculated using LTCA.
- The particle swarm optimization algorithm consists of five steps:
- Randomly initialize the particles in the particle swarm.
- Calculate the fitness (objective function value) of each particle.
- Calculate the best position experienced by the particle.
- Evolve the particles.
- Determine the end condition (whether it has evolved to the preset number of generations, otherwise return and continue).
- The optimization process is shown in Figure 7.
Comparison of Modification Effects:
- The optimization results are: y1 = 28.392 μm, y2 = 2.139588 mm, y3 = 28.91 μm, y4 = 1.672763 mm, y5 = 13.516 μm.
- The recommended modification design method and the optimized modification design method of Romax are adopted. To compare and analyze, the modification optimization results of this article, the modification recommended by Romax, and the modification optimized by Romax are uniformly simulated and analyzed in the Romax software platform.
- The recommended modification method of Romax is the one-way linear tooth profile modification method, and the helix is not modified without considering the installation error. The modification parameters are y1 = 16.08 μm, y2 = 1.28 mm, y3 = 16.08 μm, and y4 = 1.08 mm. The modification effect is shown in Figure 8, and the fluctuation amplitude of the loaded transmission error is 6.45 μm.
- In the optimized modification method of Romax, both the tooth profile and the helix adopt the parabolic modification. Romax uses the genetic algorithm in the optimized modification. Under the same optimization parameters as this article, the optimized modification result of Romax is y1 = 16.98 μm, y2 = 2.475512 mm, y3 = 21.76 μm, y4 = 2.0247985 mm, and y5 = 10.03 μm. The modification effect is shown in Figure 9, and the fluctuation amplitude of the loaded transmission error is 3.10 μm. Of course, the optimization effect is related to the optimization parameters.
- The optimization modification effect of this article is shown in Figure 10. Both the tooth profile and the helix adopt the parabolic modification, and the fluctuation amplitude of the loaded transmission error is 2.86 μm. The comparison of the modification effects is shown in Table 2. It can be seen from Table 2 that the optimization modification design effect of this article is better than the modification recommended by Romax and the modification optimized by Romax.
Conclusions:
- The influences of the modification amounts at the tooth top and root on the fluctuation amplitude of the loaded transmission error are nonlinear. Due to the different tooth profile modification methods (linear and parabolic modifications), the influences of the maximum modification amounts at the tooth top and root on the fluctuation amplitude of the loaded transmission error are different.
- The helix modification also has an influence on the fluctuation amplitude of the loaded transmission error of the internal gear pair, and the drum-shaped modification effect is better than the end slope modification.
- Through comparative analysis, it is known that reasonable modification can effectively reduce the fluctuation amplitude of the loaded transmission error.
- The optimization design method of the modification parameters proposed in this article can effectively reduce the loaded transmission error.
The research results of this article provide a basis for the modification design of internal short tooth spur gears with high transmission performance.