Hypoid gear is essential components in various high-performance applications, such as automotive differentials, industrial machinery, and aerospace systems. Despite their advantages in handling high torque loads and providing smooth operation, hypoid gear can generate significant noise, which can negatively impact performance and user experience. This article explores effective noise reduction strategies for hypoid gear in high-performance applications, highlighting advanced techniques and technologies to minimize gear noise.
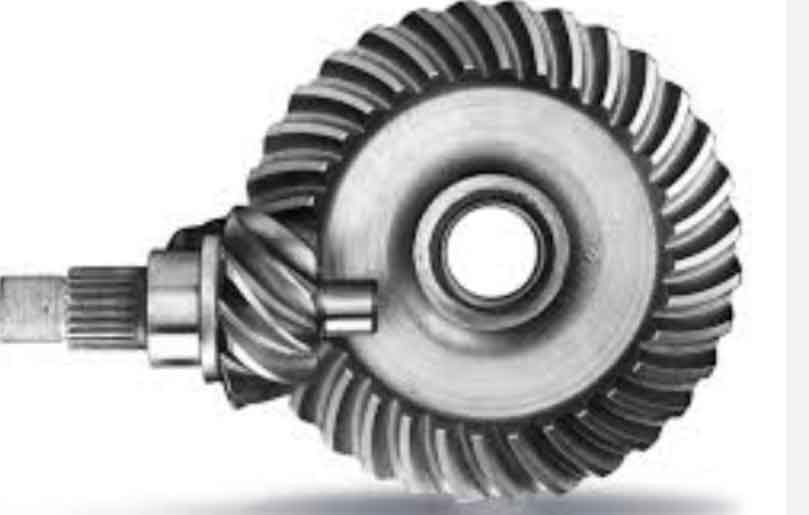
Introduction
Noise, vibration, and harshness (NVH) are critical factors in the design and operation of hypoid gear. High noise levels can lead to discomfort, reduced performance, and increased wear and tear on mechanical systems. Therefore, implementing noise reduction strategies is crucial for enhancing the performance and longevity of hypoid gear in high-performance applications.
Sources of Noise in Hypoid Gear
Understanding the sources of noise in hypoid gear is essential for developing effective noise reduction strategies. The primary sources of noise include:
- Gear Mesh Misalignment:
- Incorrect alignment of hypoid gear teeth during meshing can cause uneven load distribution and increased noise.
- Surface Roughness:
- Rough hypoid gear surfaces can lead to increased friction and noise during operation.
- Gear Geometry:
- Inaccurate gear geometry can result in improper contact between gear teeth, causing noise and vibrations.
- Manufacturing Defects:
- Defects such as burrs, nicks, and uneven surfaces can contribute to noise generation.
- Lubrication Issues:
- Inadequate or improper lubrication can increase friction and noise.
Noise Reduction Strategies
1. Precision Manufacturing and Gear Design
- High-Precision Machining:
- Utilizing advanced CNC machining techniques ensures tight tolerances and accurate hypoid gear geometries.
- High-precision machining reduces misalignment and surface roughness, leading to quieter operation.
- Optimized Gear Geometry:
- Designing gears with optimized tooth profiles can improve contact patterns and reduce noise.
- Computer-aided design (CAD) and finite element analysis (FEA) can be used to optimize hypoid gear geometry.
2. Surface Treatments
- Shot Peening:
- Shot peening induces compressive residual stresses on hypoid gear surface, reducing the likelihood of crack initiation and propagation.
- This treatment also smoothens surface irregularities, lowering noise levels.
- Coatings:
- Advanced coatings such as diamond-like carbon (DLC) and molybdenum disulfide (MoS2) reduce friction and wear.
- Coatings can improve surface finish and reduce noise generated by hypoid gear contact.
3. Lubrication Techniques
- High-Performance Lubricants:
- Using lubricants specifically designed for hypoid gear can reduce friction and noise.
- Synthetic lubricants and those with additives can enhance lubrication properties and minimize noise.
- Adaptive Lubrication Systems:
- Adaptive lubrication systems that adjust lubricant flow based on operating conditions can ensure optimal lubrication.
- These systems help maintain a consistent lubricant film, reducing noise and wear.
4. Gear Alignment and Assembly
- Precision Alignment:
- Ensuring precise alignment of hypoid gear during assembly can prevent misalignment and uneven load distribution.
- Using alignment tools and fixtures can enhance assembly accuracy.
- Proper Mounting Techniques:
- Proper mounting and fastening techniques can minimize vibrations and noise.
- Using vibration-damping materials and components can further reduce noise.
5. Advanced Materials
- High-Strength Alloys:
- Using high-strength, lightweight alloys can improve gear durability and reduce noise.
- These materials can withstand high loads and minimize deformation under stress.
- Composite Materials:
- Composite materials with high damping properties can absorb vibrations and reduce noise.
- These materials can be used in hypoid gear housings and mounts to enhance noise reduction.
Comparative Analysis of Noise Reduction Strategies
Strategy | Advantages | Disadvantages |
---|---|---|
Precision Manufacturing | High accuracy, reduced misalignment | High cost, requires advanced machinery |
Optimized Gear Geometry | Improved contact patterns, reduced noise | Complex design process, requires simulation |
Surface Treatments | Enhanced surface finish, reduced friction | Additional processing steps, cost |
High-Performance Lubricants | Reduced friction, improved gear lifespan | May require frequent replacement |
Adaptive Lubrication Systems | Consistent lubrication, reduced wear and noise | Complex system, higher initial cost |
Precision Alignment | Prevents misalignment, ensures even load distribution | Requires skilled labor, precise tools |
High-Strength Alloys | Improved durability, reduced deformation | Higher material cost |
Composite Materials | High damping properties, reduced vibrations | Limited load-bearing capacity |
Implementation of Noise Reduction Strategies
- Assess Gear Requirements:
- Evaluate the specific requirements of the application, including load, speed, and operating environment.
- Determine the primary sources of noise and select appropriate noise reduction strategies.
- Design Optimization:
- Utilize CAD and FEA to design optimized hypoid gear geometries.
- Conduct simulations to predict noise levels and identify potential improvements.
- Material Selection:
- Choose materials with high strength, low friction, and good damping properties.
- Consider advanced alloys and composite materials for specific components.
- Precision Manufacturing:
- Implement high-precision machining techniques to achieve tight tolerances and accurate geometries.
- Use advanced manufacturing processes to minimize surface roughness and defects.
- Surface Treatment Application:
- Apply surface treatments such as shot peening and coatings to enhance surface properties.
- Evaluate the effectiveness of different treatments through testing and analysis.
- Lubrication Management:
- Select high-performance lubricants suitable for hypoid gear.
- Implement adaptive lubrication systems for consistent and optimal lubrication.
- Assembly and Alignment:
- Ensure precise alignment and proper mounting during hypoid gear assembly.
- Use alignment tools and fixtures to enhance accuracy.
- Testing and Validation:
- Conduct comprehensive testing to validate the effectiveness of noise reduction strategies.
- Monitor gear performance under real-world operating conditions.
Future Trends in Noise Reduction for Hypoid Gear
1. Smart Gear Systems
- Embedded Sensors:
- Integrating sensors into hypoid gear can provide real-time data on temperature, stress, and noise levels.
- This data can be used to adjust operating parameters and reduce noise dynamically.
- Active Noise Control:
- Active noise control systems can counteract hypoid gear noise using anti-noise signals.
- These systems can adapt to changing operating conditions and minimize noise in real-time.
2. Advanced Manufacturing Technologies
- Additive Manufacturing:
- Additive manufacturing allows for the production of complex, optimized hypoid gear designs.
- This technology can create hypoid gear with built-in noise reduction features.
- Laser Surface Texturing:
- Laser surface texturing can create micro-scale patterns on hypoid gear surfaces to reduce friction and noise.
- This technique enhances lubrication retention and surface smoothness.
3. Eco-Friendly Lubricants
- Biodegradable Lubricants:
- Developing eco-friendly, biodegradable lubricants can reduce environmental impact.
- These lubricants must maintain high performance and noise reduction properties.
- Nano-Lubricants:
- Nano-lubricants containing nanoparticles can enhance lubrication efficiency and reduce noise.
- These lubricants offer improved wear resistance and thermal stability.
Conclusion
Noise reduction in hypoid gear is essential for enhancing the performance and user experience in high-performance applications. Implementing strategies such as precision manufacturing, optimized gear design, surface treatments, advanced lubrication techniques, and proper alignment can significantly reduce noise levels. As technology advances, the integration of smart systems, additive manufacturing, and eco-friendly lubricants will further enhance noise reduction capabilities. By adopting these advanced strategies, manufacturers can ensure the production of high-quality hypoid gear that meet the demanding requirements of modern high-performance applications.