1. Introduction
1.1 Research Background and Significance
Spiral bevel gears play a crucial role in mechanical transmission, known for their smooth operation, high load-bearing capacity, and efficient power transfer. They are widely used in various industries such as automotive, aerospace, and mining. However, the traditional machining methods, like milling, have several drawbacks, including low material utilization and damage to the metal flow lines, which affect the gear’s performance and lifespan. The emergence of plastic forming techniques, especially gear rolling, offers a promising alternative with higher material efficiency and better mechanical properties. But the current spiral bevel gear rolling process still faces challenges like tooth misalignment and surface defects, which hinder its further development. This research focuses on addressing these issues by proposing a novel rolling process and investigating the metal flow line evolution, aiming to enhance the gear’s quality and performance.
1.2 Current Research Status of Gear Rolling Technology
Gear rolling technology has seen significant advancements over the years. In the automotive industry, efforts have been made to improve the manufacturing process of planetary gears. For instance, the use of die forging has reduced material waste and production time. Shanghai Automotive Gear Factory and Shanghai Institute of Mechanical Manufacturing Technology have developed new precision forging processes for spiral bevel gears, increasing material utilization. Researchers like Du Zhongyou have optimized forging molds and processes to minimize material waste and energy consumption. Qingdao University of Technology has designed new molds to overcome issues in forging straight cylindrical gears.
In terms of research on gear rolling mechanisms, scholars have explored various factors. Domblesky used finite element simulation to study thread rolling, analyzing the influence of process parameters on material flow. Seizo investigated the effect of gear rotation speed on tooth profile error in rack and pinion rolling. Jun Li and others analyzed the factors causing “rabbit ear” defects in gear rolling and proposed solutions. Dongcheng Li proposed a multi-pass rolling method to suppress “rabbit ear” defects, and Khodaee explored the effect of changing the rotation direction of the die on defect suppression.
Despite these efforts, the research on spiral bevel gear rolling, especially in aspects like the relationship between feed and pitch and motion compensation, remains insufficient. There is a need for further studies to optimize the process and improve the gear quality.
1.3 Research Status of Metal Flow Lines in Plastic Forming
Metal flow lines in plastic forming significantly impact the mechanical properties of products. In the case of spiral bevel gears, the distribution and integrity of metal flow lines are crucial for their performance. Previous studies have shown that reasonable metal flow line distribution can enhance the gear’s strength and durability. For example, in the research on ring rolling by Luo Xingen and Meng Wen, the changes in microstructure and mechanical properties after deformation were analyzed, highlighting the importance of metal flow lines.
However, in the study of spiral bevel gear rolling, most research has focused on the influence of process parameters on metal flow lines without delving into the underlying causes of their evolution. There is a lack of in-depth understanding of how different factors during the rolling process affect the formation and transformation of metal flow lines, which is an area that requires further exploration.
1.4 Research Objectives and Contents
This research aims to address the problems in the current spiral bevel gear rolling process, especially tooth misalignment and surface defects. The main objectives include proposing a new rolling process to ensure correct tooth division and pitch matching, optimizing process parameters to improve gear quality, and investigating the evolution law of metal flow lines to enhance the mechanical properties of the gears.
The specific research contents are as follows:
- Analyze the causes of tooth misalignment in the spiral bevel gear rolling process and propose a new rolling process theory to ensure correct tooth division and pitch matching at any time during rolling.
- Verify the feasibility of the new rolling process through numerical simulation and comparison with the traditional single-die rolling process.
- Use the single-factor method to study the influence of process parameters on the forming quality of spiral bevel gears, establish an evaluation index for “rabbit ear” defects, and optimize relevant parameters.
- Analyze the evolution law of metal flow lines during the rolling process, explore the relationship between metal flow lines and forming forces, and reveal the causes of tooth surface folding.
2. Theoretical Analysis of Spiral Bevel Gear Rolling Process
2.1 Introduction
Gear rolling, as an advanced plastic forming technology, has the potential to improve the manufacturing quality of spiral bevel gears. However, the existing rolling process faces challenges such as tooth misalignment and surface defects. This chapter focuses on analyzing the root causes of these problems based on the kinematic relationship between the die and the forming wheel and the theory of metal plastic deformation. By observing the motion state during tooth misalignment, we aim to provide a theoretical foundation for a new rolling process.
2.2 Optimization Concept of the Rolling Structure in the New Spiral Bevel Gear Rolling Process
In the rolling process of spiral bevel gears, the traditional single-die rolling often leads to tooth misalignment and surface folding due to the inconsistent pitch between the die and the forming wheel. To address this issue, a new process concept is proposed.
Taking gear rack rolling as an example, to ensure correct tooth division and pitch matching, the rack’s tooth height and pitch need to be gradually adjusted during rolling. This can be achieved by using segmented dies that are advanced to a specified position and then perform rolling without feed. After each rolling stage, the die is advanced again for the next rolling cycle.
In the case of spiral bevel gear rolling, ensuring that the initial rolling positions of consecutive turns coincide can prevent the reconstructed of the formed tooth profile and effectively avoid tooth misalignment and surface folding. By comparing the traditional rolling structure with the proposed new structure, it is evident that the new concept has the potential to significantly improve the rolling quality.
2.3 Finite Element Modeling of Spiral Bevel Gears
The machining of spiral bevel gears on milling machines involves a complex process where the摇台机构 simulates an imaginary gear, and the cutter head on the摇台 acts as a gear tooth. The cutting process is similar to the meshing of spiral bevel gears, with the cutter head’s tangent plane and the machined gear surface being conjugate tooth profiles. The常用的产形轮 include平面产形轮 and锥形产形轮, with different cutter head axis orientations and face cone angles.
The mathematical model of the spiral bevel gear cutter, the gear cutting principle, the calculation of tooth points, the reverse conjugation principle, and the establishment of the three-dimensional model have been detailed in previous studies. In this research, these established models and principles are utilized as the basis for further analysis.
2.4 Determination of the Initial Radius of the Spiral Bevel Gear Blank Based on the Equal Chord Length Method with an Imaginary Wheel
2.4.1 Determination of the Initial Radius of Cylindrical Gears
In gear rolling, the diameter of the gear blank significantly affects the tooth division and profile formation quality. The equal chord length method is proposed to determine the blank diameter, which is beneficial for correct tooth division.
Taking a straight cylindrical gear with a tooth number ratio of 9/39 as an example, the basic parameters are shown in Table 2-1. By using the equal chord length formula, the initial diameter of the blank can be calculated. Different methods, such as changing the module and the tooth number, are explored to determine the optimal blank radius. The results are summarized in Table 2-2, showing that the method of fixing the module and changing the tooth number results in the largest volume increase.
Gear Basic Parameters | Numerical Value |
---|---|
Z1 | 9 |
Z2 | 39 |
m (mm) | 1 |
α (°) | 20 |
ha* | 1 |
C* | 0.25 |
Method | Standard Equal Chord Method | Fixed Tooth Number and Changed Module | Fixed Module and Changed Tooth Number |
---|---|---|---|
Blank Radius (mm) | 4.731 | 4.760 | 5.244 |
Unit Volume Surplus (%) | 0.00 | 0.63 | 10.85 |
2.4.2 Influence of Node Displacement on Tooth Number Change
For spiral bevel gears, determining the initial blank radius is more complex compared to cylindrical gears. The traditional equal volume method has limitations, such as difficulties in calculating material loss during rolling. Based on the principle of using the intersection point as the node, as in cylindrical gear rolling, the initial blank diameter of the spiral bevel gear is determined.
During the rolling process, the position of the node changes, which affects the tooth number ratio. As the die cone of the spiral bevel gear contacts the forming wheel, the original node shifts, resulting in a change in the tooth number ratio. The range of tooth number changes for the large and small gears is determined based on geometric calculations.
2.4.3 Initial Radius of the Blank Based on the Imaginary Wheel
Based on the contact point as the node and the change law of the gear tooth number ratio, the initial diameter of the blank is calculated using the equal arc length principle. Considering different tooth number ratios for the imaginary wheel, such as 10/38 and 11/38, the corresponding blank diameters are determined.
The results in Table 2-3 show that the equal arc length method provides a more accurate blank diameter. However, considering factors such as material loss and defect compensation, the method based on the imaginary wheel with a certain volume surplus is more suitable for meeting the requirements of the rolling process.
Method | Equal Arc Length Method | Imaginary Wheel 10/38 | Imaginary Wheel 11/38 |
---|---|---|---|
Blank Large End Radius (mm) | 25.74 | 25.88 | 31.64 |
Unit Volume Surplus (%) | 0 | 0.55 | 22.92 |
2.5 Root Causes and Uniformity Conditions of Rolling Tooth Division Errors
2.5.1 Correctness of Tooth Division in Variable Rolling Ratio Rolling of Straight Cylindrical Gears
The correctness of tooth division in the initial stage of gear rolling is crucial for the subsequent forming process. For straight cylindrical gears with a tooth number ratio of 9/39, the initial diameter of the blank calculated by the equal chord length method is used.
The rolling process requires that after the blank rotates one circle, the tenth tooth of the die aligns with the first formed tooth profile of the blank. By using the equal arc length principle and calculating the rotation angle of the die, it is determined that the equal chord length method can meet the correct tooth division conditions, although there may be a small allowable error.
2.5.2 Root Causes of Tooth Division Errors in Spiral Bevel Gear Rolling
Unlike cylindrical gears, spiral bevel gears face challenges in ensuring correct tooth division. The main reasons are that the blank radius determined by methods like the equal volume method or the imaginary wheel method is larger than the pitch circle radius, and the pitch of the forming wheel changes during rolling while the die pitch remains fixed.
As shown in Figure 2-12, the pitch of the blank decreases during rolling. In the traditional single-die rolling process, although the final tooth number can be correct, tooth misalignment occurs during rolling, leading to surface folding and affecting the final tooth surface quality.
2.5.3 Uniformity Conditions of Tooth Division in Spiral Bevel Gear Rolling
To achieve uniform tooth division, the arc lengths of the die and the blank must match during rotation. The conditions for correct tooth division are given by the formulas 2-19 and 2-20, where the radii and angles of the die and the blank at the current rolling position are related to the tooth numbers.
The blank radius is determined based on the imaginary wheel method, and the feed amount during rolling is crucial. If the feed is too large or too small, it will lead to arc length mismatches and tooth misalignment. Additionally, controlling the tooth height of the die can help limit the tooth misalignment angle within an acceptable range.
2.6 Design Method of the Die Wheel Based on Variable Rolling Ratio
2.6.1 Relationship between the Rotational Speeds of the Die Wheel and the Blank Based on Equal Pitch
To ensure accurate tooth division, the pitch of the die wheel needs to match that of the blank during rolling. Since the pitch of the blank changes, the die wheel can be designed with a variable pitch or its rotational speed can be adjusted to adapt to the blank’s pitch change.
One approach is to use multiple sets of dies with different tooth numbers. By adjusting the die tooth number according to the blank’s pitch change, the arc lengths can be matched. The rotational speed of the die wheel is calculated based on the formula 2-26, where the rotational speeds of the blank and the die are related to their pitch circle radii.
2.6.2 Design of the Die Wheel
The design of the die wheel involves several aspects. Firstly, a unified blank with 39 teeth is used, and only the tooth number is changed during rolling to simplify the design and control variables. Secondly, the tooth number and height of the die wheel are designed based on the principle of ensuring correct tooth division and improving die life. The tooth height is distributed in an arithmetic progression based on the pitch cone line.
To reduce material flow resistance and provide space for material movement, the tooth top of the die wheel is rounded, and the tooth side clearance is enlarged. Additionally, the large end of the die wheel is extended to accommodate material flow and facilitate die replacement.
2.7 Summary
This chapter proposes a new rolling process theory for spiral bevel gears, including the optimization of the rolling structure, the determination of the blank initial diameter, the analysis of tooth division error causes, and the design of the die wheel. These theoretical foundations provide a basis for further research on the feasibility and optimization of the new rolling process.
3. Feasibility Study of the Optimization of the Spiral Bevel Gear Rolling Process
3.1 Research on the Rolling Forming Process with Actively and Continuously Variable Tooth Numbers of the Die Wheel
3.1.1 Finite Element Parameter Settings for the Rolling Forming Process
To simulate the new rolling process, finite element models are established with specific parameter settings. The blank is heated to 900°C using medium-frequency induction heating, and the local deformation depth is set to 9mm. To reduce computational effort, only half of the gear tooth volume is meshed, initially divided into 100,000 elements. The die wheel and drive shaft are set as rigid bodies, with the friction coefficient between the die and the blank set to 0.1 and that between the blank and the drive shaft set to 0.8. The environmental temperature is set to 20°C, and heat transfer is disabled to focus on deformation analysis. The rotational speed of the forming wheel is set to 30r/min, and the rotational speed of the die wheel is calculated according to the formula ω₂ = (z₁/z₂)ω₁, where z₁ and z₂ are the tooth numbers of the forming wheel and the die wheel, respectively, and ω₁ and ω₂ are their rotational speeds.
3.1.2 Simulation of the Rolling Forming Process
The new rolling process involves multiple steps with variable die tooth numbers. In the first step, a die wheel with 33 teeth is used, with an initial feed of 2.06mm at a speed of 0.5mm/s. After reaching the specified depth, the die wheel rotates at 8.182r/min for two circles. The simulation results show that there is no tooth misalignment, indicating the correctness of the feed and rotational speed calculations.
In the subsequent steps, the die wheel is changed as the feed depth increases. For example, in the second step with a total feed depth of 3.24mm, a die wheel with 34 teeth is used. The simulation shows that the tooth surface bulge phenomenon is not significant, but a “spur” – like defect appears on the active side of a certain tooth due to insufficient material filling in the space between the die and the forming wheel.
As the process continues, different die wheels are used at different feed depths. In the final step, after the feed depth reaches 8.4mm and the die wheel with 39 teeth is used, the tooth surface folding defect is observed, mainly concentrated on the active side. However, after the reverse and forward rotations in the finishing stage, the tooth surface becomes smoother, and the flower key of the forming wheel has no significant deformation.
The torque, circumferential force, axial force, and material loss at the end of the forming wheel are analyzed and compared with those of the single-die rolling process. The results show that the new rolling process significantly reduces the tooth surface folding defect (by about 98%), torque (by about 75%), axial force (by about 75%), and the end volume loss of the forming wheel (by about 5.13%). The circumferential force is also lower than that of the single-die rolling process, although it still exists due to the continuous forming of the tooth profile. The radial load is larger in the new process due to the 先进给 and then rolling mechanism, but overall, the new process shows better performance.
3.2 Single-Die Spiral Bevel Gear Rolling Forming Process
3.2.1 Finite Element Parameter Settings for the Rolling Forming Process
Similar to the previous process, the single-die rolling process also involves heating the blank to 900°C with a local deformation depth of 9mm. The blank volume is meshed with 100,000 elements, and the die and drive shaft are set as rigid bodies. The friction coefficients are set to 0.2 between the die and the blank and 0.8 between the blank and the drive shaft. The environmental temperature is 20°C, and heat transfer is disabled. The rotational speed of the small wheel is 30r/min, and the die wheel rotates at 6.923r/min with a feed speed of 0.2mm/s.
3.2.2 Simulation of the Rolling Forming Process
In the single-die rolling process, the tooth surface folding defect is more severe compared to the new process. The initial stage shows significant tooth surface reconstruction due to tooth misalignment, which persists even as the die and forming wheel pitches gradually match in the middle stage. Although the tooth surface becomes smoother after the forward and reverse rotations in the final stage, the cumulative tooth misalignment error in the early stage affects the overall tooth surface quality.
The tooth surface folding is mainly concentrated on the active side and moves towards the tooth tip. This is because the single-die rolling process cannot effectively control the pitch matching, resulting in material accumulation and surface reconstruction.
3.3 Comparative Analysis of the Two Rolling Forming Processes
Based on the simulation results of the two rolling processes, a comprehensive comparison is conducted in terms of tooth surface quality, folding defects, torque, and loads.
The final tooth surface quality of the new process is significantly better than that of the single-die process. The tooth surface of the new process is smoother, with almost no visible tooth surface folding defects, while the single-die process shows obvious folding and unevenness.
In terms of torque, the new process has a much lower torque, which is less than a quarter of that of the single-die process and shows periodic fluctuations. This is because the new process separates the feeding and rolling stages, and torque is only generated during rolling.
The circumferential force of the new process is also lower than that of the single-die process, although it still exists due to the continuous forming of the tooth profile. The axial force of the new process is significantly smaller, about 75% less than that of the single-die process, which helps reduce material loss at the end of the gear.
The volume loss at the end of the forming wheel is also compared. The new process results in a 5.13% larger volume than the single-die process, indicating better material utilization.
Overall, the new rolling process with actively and continuously variable tooth numbers shows clear advantages over the single-die rolling process, providing a more feasible and efficient solution for spiral bevel gear manufacturing.
3.4 Summary
This chapter validates the feasibility of the proposed new rolling process through detailed simulations and comparisons. The results demonstrate that the new process effectively reduces tooth surface defects, improves gear quality, and shows better mechanical performance. These findings lay the foundation for further optimization and application of the spiral bevel gear rolling process.
4. Numerical Simulation Study on the Forming Law of Spiral Bevel Gear Rolling
4.1 Introduction
Gear rolling forming is a complex plastic forming process, and the quality of the formed gears is affected by various factors. Previous studies have focused on different aspects of gear rolling, but there is still a lack of in-depth understanding of the influence of process parameters on the forming quality. This chapter aims to optimize the process parameters of the spiral bevel gear rolling process proposed in the previous chapter and investigate their influence on the forming quality. By using the single-variable control method and numerical simulation, the optimal process parameter combination is explored to improve the gear quality.
4.2 Establishment of the Initial Standard for the Tool Wheel
Based on the feasibility study of the variable rolling ratio in Chapter 3, this chapter further investigates the “rabbit ear” defect by establishing a unified standard for the die wheel blank. The die wheel blank is designed with a 39-tooth profile, and the pitch cone angle of the large gear is used for all die wheels. The large end of the die wheel is extended to avoid material overflow and ensure the smooth progress of the rolling process.
By simulating the rolling process with different extensions of the die wheel large end (8mm, 10mm, and 12mm), the relationship between the die wheel extension and the tooth surface folding defect is analyzed. The results show that when the large end is extended by 8mm, the tooth surface folding defect is effectively suppressed. Therefore, an 8mm extension is considered for the subsequent simulations.
4.3 Determination of the Evaluation Index
The “rabbit ear” defect significantly affects the forming quality of spiral bevel gears. To quantitatively evaluate this defect, an evaluation index is established. The index is based on the ratio of the height of the “rabbit ear” to the effective tooth height at the midpoint of the gear during rolling. By measuring the radii of the actual tooth top and the effective tooth top, the proportion of the “rabbit ear” defect in the actual tooth height can be calculated, providing a basis for evaluating and optimizing the rolling process.
4.4 Influence Law of the Gear Rolling Process on Tooth Forming
4.4.1 Tooth Groove Deepening
To address the issue of premature contact between the tooth root of the die wheel and the tooth top of the forming wheel, which leads to material flow and forming defects, the tooth groove of the die wheel is deepened. Simulations are conducted with different groove depths (2mm, 3mm, and 4mm), while keeping other parameters constant (feed speed of 0.5mm/s, forming wheel rotational speed of 30r/min, and fillet radius of 0.5mm).
The simulation results show that as the tooth groove depth increases, the proportion of the “rabbit ear” defect on the active side of the forming wheel tooth profile increases. This is because the deeper groove can accommodate more material flow, preventing premature contact between the die and the forming wheel and reducing material loss at the ends. When the groove depth is 2mm, the “rabbit ear” proportion is the smallest, so a 2mm groove depth is selected as the optimal parameter.
4.4.2 Fillet Radius of the Die Wheel Tooth Top
The fillet radius of the die wheel tooth top is varied (0.1mm, 0.3mm, 0.5mm, and 0.7mm) to study its influence on the “rabbit ear” defect. With other parameters unchanged (tooth groove depth of 2mm, feed speed of 0.5mm/s, and forming wheel rotational speed of 30r/min), the simulations are carried out.
The results indicate that the change in the fillet radius has an irregular impact on the “rabbit ear” proportion. Although the overall trend shows some stability, the differences between different radii are relatively small. This suggests that the sensitivity of the tooth profile forming to the fillet radius change is relatively low, and the influence on the “rabbit ear” defect is not as significant as other factors.
4.4.3 Friction Factor
The friction factor between the die wheel and the forming wheel is another important parameter. Simulations are performed with different friction factors (0.1, 0.2, and 0.3), while keeping the tooth groove depth at 2mm, feed speed at 0.5mm/s, and forming wheel rotational speed at 30r/min.
The results show that as the friction factor increases, the proportion of the “rabbit ear” defect decreases. This is because the friction force restricts the material flow on both sides of the forming wheel, preventing it from moving towards the tooth top and effectively suppressing the formation of the “rabbit ear” defect.
4.4.4 Forming Temperature
The forming temperature directly affects the material flow during the rolling process. Simulations are conducted at different temperatures (900°C, 950°C, and 1000°C), with a friction factor of 0.2 and other parameters unchanged.
The results indicate that as the temperature increases, the material flow becomes more uniform, and the “rabbit ear” defect is effectively suppressed. The difference between the actual tooth height and the effective tooth height decreases with increasing temperature, suggesting that maintaining a constant high forming temperature can improve the gear quality by reducing the “rabbit ear” defect.
4.4.5 Rotational Speed of the Forming Wheel
The rotational speed of the forming wheel affects the material deformation rate and the forming force. Simulations are carried out with different rotational speeds (30r/min, 40r/min, and 50r/min), a friction factor of 0.2, a temperature of 900°C, and a feed amount of half the total.
The results show that as the rotational speed increases, the proportion of the “rabbit ear” defect also increases. This is because the higher rotational speed leads to a greater instantaneous deformation of the material, which causes more material to be squeezed to the sides of the tooth profile and forms a sharper “rabbit ear” due to the difference in material flow speed between the center and the sides.
4.4.6 Feed Amount at Different Stages
To simplify the calculation process while ensuring correct tooth division, a feed tolerance method is proposed. Three different feed methods are compared: precise calculation at each stage, an initial bite of 2.4mm followed by 1.1mm increments, and an initial bite of 3mm followed by 1mm increments. The total feed depth is 9mm, and other rolling conditions remain unchanged.
The simulation results show that the feed amount at different stages has a certain influence on the “rabbit ear” defect. The differences between the first two feed methods are relatively small, while the third method shows a larger difference. This is because the feed amount in the early stage affects the material distribution and flow, which in turn influences the formation of the “rabbit ear” defect.
4.5 Summary
This chapter systematically investigates the influence of various process parameters on the forming quality of spiral bevel gears. By using the single-variable control method and numerical simulation, the optimal parameter values for each factor are obtained. These findings provide a theoretical basis for further optimizing the rolling process and improving the quality of spiral bevel gears.
5. Study on the Evolution Law of Metal Flow Lines in Spiral Bevel Gear Rolling
5.1 Introduction
The distribution of metal flow lines in spiral bevel gears is closely related to their mechanical properties. In the previous chapters, the rolling process and parameter optimization were studied, but the evolution law of metal flow lines and its relationship with the forming process and gear quality have not been fully explored. This chapter focuses on analyzing the evolution of metal flow lines during the rolling process of spiral bevel gears, aiming to understand how different factors affect the distribution and morphology of metal flow lines and to provide a theoretical basis for further improving the mechanical properties of the gears.
5.2 Characteristics of the Evolution Law of Metal Flow Lines
The 不合理 distribution of metal flow lines after rolling can lead to substandard 组织 and mechanical properties of the gears, affecting their service life. By using simulation software, the metal flow lines of the forming wheels in two rolling processes, namely the die wheel actively and continuously variable tooth number rolling forming and the single-die fixed tooth number continuous feed rolling forming, are analyzed.
In the new rolling process, the metal flow lines are mainly densely distributed at the tooth root, which is beneficial for improving the bending fatigue strength of the gear. The flow lines on the tooth side are also relatively dense and consistent, indicating correct tooth division. However, a “rabbit ear” – like distribution is observed at the tooth top, which is mainly due to the fixed rotation direction during rolling. In contrast, the single-die rolling process results in 紊乱 and interrupted metal flow lines, with significant differences between different tooth profiles. Metal flow lines are piled up at the tooth root, and even fractures occur, indicating poor quality of the formed gears.
5.3 Study on the Whole Process Evolution Law of Metal Flow Lines
Based on the optimized die structure and process parameters obtained in the previous chapter, numerical simulations are further conducted to analyze the evolution law of metal flow lines. The models and simulation results are shown in Figures 5 – 3 and 5 – 4.
In the initial stage of rolling (Figure 5 – 5), the metal flow lines form the initial shape of the tooth profile under the action of extrusion. The flow lines on both sides of the tooth are denser due to the extrusion force, and the bottom layer near the tooth root is also relatively dense. In the second stage (Figure 5 – 6), the metal flow lines on the active side of the tooth root change due to the extrusion, while those on the 从动侧 form a concave shape. In the third stage (Figure 5 – 7), the density of the metal flow lines at the tooth root increases, and the flow lines in the groove shift along the spiral line. The correct tooth division in this process ensures the continuity and controllability of the metal flow line evolution.
In the fourth stage (Figure 5 – 8), the metal flow lines at the tooth root become denser, and no obvious “rabbit ear” defect is observed. The correct control of the tooth division and the consistent extrusion position contribute to the dense and orderly distribution of the metal flow lines. In the fifth stage (Figure 5 – 9), the distribution of the metal flow lines at the normal direction of the midpoint is reasonable, with dense flow lines at the tooth profile and root, which can improve the contact fatigue strength and bending fatigue strength of the gear.
In the final stage (Figure 5 – 10), the “rabbit ear” defect appears on the active side of the tooth top, but the overall metal flow lines are relatively dense and orderly. The final forming process eliminates the “rabbit ear” defect, and the metal flow lines are distributed in layers, with the highest density at the tooth root, which is beneficial for improving the gear strength.
5.4 Influence of Forces on the Change of Metal Flow Lines during Rolling
5.4.1 Influence of Circumferential Force
The circumferential force is an important factor affecting the metal flow lines during rolling. It mainly increases the density of the metal flow lines at the tooth profile and improves the tooth surface quality. By analyzing the force formula and the change of the circumferential force during rolling (Figure 5 – 13), it is found that the circumferential force increases with the feed depth.
The change of the circumferential force is related to the increase in the tooth number of the die wheel and the complexity of the gear structure. The increase in the tooth number leads to an increase in the force, and the instantaneous mismatch of the pitch circle during the rolling process also causes fluctuations in the circumferential force. The denser metal flow lines on the active side of the tooth root are mainly due to the action of the circumferential force, and the curvature of the flow lines gradually increases with the feed depth.
5.4.2 Influence of Axial Force
The axial force affects the position of the gear blank and may cause material overflow and changes in the metal flow lines. By observing the changes in the gear blank and metal flow lines under the action of the axial force (Figure 5 – 15), it is found that the axial force causes material to move towards the ends of the gear, resulting in a decrease in the filling height of the tooth profile and an “arch” – like shape.
The calculation formula of the axial force shows that it is related to the circumferential force and other parameters. The change of the axial force during rolling is periodic, and it gradually decreases with the increase in the contact area between the die wheel and the forming wheel. The different directions of the axial force at different positions of the gear tooth surface cause the metal flow lines to move in different directions.
5.4.3 Influence of Radial Force
The radial force in the spiral bevel gear rolling process cannot be ignored. It is divided into the progressive radial force during extrusion and the instantaneous radial force during rolling. The calculation formula of the radial force is given, and the change of the radial force during rolling is analyzed (Figure 5 – 17).
The radial force shows a periodic change, and it increases with the feed depth due to the increase in the contact area. The instantaneous radial force during rolling is caused by the extrusion process, and the correct tooth division in the rolling process can avoid defects such as metal flow line folding and fracture. The radial force causes the metal flow lines near the tooth profile to bend and be densely distributed, especially at the junction of the tooth root and the profile.
5.5 Tooth Surface Folding during Rolling
Tooth surface folding is a serious defect that affects the quality of the gear. By using simulation settings (Figure 5 – 19), the formation process of tooth surface folding is analyzed.
It is found that tooth surface folding occurs after the formation of “spurs” during rolling. The folding position is above the “spurs” and tends to move towards the tooth top. This is because the material is affected by the friction force and has an upward movement trend. The presence of tooth surface folding indicates that the material has undergone secondary folding, which may reconstruct the formed tooth profile and affect the gear quality.
5.6 Summary
This chapter analyzes the evolution law of metal flow lines during the rolling process of spiral bevel gears and the influence of forces on the metal flow lines. The results show that the distribution and change of metal flow lines are closely related to the rolling process and the forces acting on the gears. Understanding these relationships can help optimize the rolling process and improve the mechanical properties of the gears.
6. Conclusions and Prospects
6.1 Conclusions
- Analysis of Tooth Surface Folding and Proposal of a New Rolling Process: The root cause of tooth misalignment in the previous gear rolling process is analyzed, and a new rolling process is proposed to ensure uniform tooth division. The mathematical model for controlling the rotational speed and feed amount during rolling is established, and the initial radius of the forming wheel is determined based on the variable tooth number and numerical control module method. The effectiveness of the tooth division control strategy is verified by numerical simulation.
- Feasibility Verification of the New Rolling Process: The new rolling process is verified to be feasible through numerical simulation. The tooth surface folding defect is significantly reduced (by about 98%), the torque is reduced (by about 75%), and the end volume loss of the forming wheel is reduced (by about 5.13%). The superiority of the new process is demonstrated by comparing it with the traditional single-die rolling process.
- Optimization of Process Parameters in Multi-Die Rolling: The relationship between the feed amount and the tooth number of the die wheel in multi-die rolling is established, and the die wheel is extended to ensure smooth rolling. An evaluation index for the “rabbit ear” defect is established, and single-factor optimization is conducted on parameters such as tooth groove depth, die wheel tooth top fillet radius, friction factor, forming temperature, rotational speed, and feed amount. The optimal process parameter values are obtained.
- Study on the Evolution Law of Metal Flow Lines: The evolution law of metal flow lines during the rolling process is investigated, and the relationship between the metal flow lines and the forming forces is established. It is found that the change of metal flow lines is mainly related to the forces during rolling, and the essence of tooth surface folding is the overlap of metal flow lines, that is, the secondary reconstruction of the tooth surface.
6.2 Prospects
- Further Optimization of the New Rolling Process: Although the new rolling process shows good results in reducing tooth surface folding, there is still room for improvement. The volume establishment of the forming wheel blank needs to be further optimized, the design details of the die wheel need to be refined, and the accurate position of the node during rolling needs to be further determined to form a more complete theoretical system.
- Expansion of Process Parameter Research: In this study, only six process parameters are optimized using the single-factor method. Future research can expand to other parameters and use orthogonal experiments and response surface methods to find the optimal combination of process parameters. This will help further reveal the material flow mechanism and the spatial distribution law of metal flow lines during rolling and achieve better control of the forming quality.
- Experimental Verification: Due to limitations in experimental conditions, the proposed new rolling process has not been experimentally verified. Future work can focus on building experimental setups and using appropriate manufacturing methods to produce die wheels for experimental validation. This will provide more practical support for the application of the new rolling process.
- Improvement of Simulation Efficiency: The gear rolling simulation requires high-quality meshing, and the existing meshing methods may lead to low time efficiency due to mesh reconstruction during the simulation. The emerging meshless method shows potential in improving simulation accuracy and efficiency and can be explored in future research to overcome the limitations of traditional finite element methods.
In summary, this research has made significant progress in optimizing the spiral bevel gear rolling process and understanding the evolution law of metal flow lines. Future work will focus on further improving the process, expanding parameter research, conducting experimental verification, and improving simulation methods to promote the application and development of spiral bevel gear rolling technology.
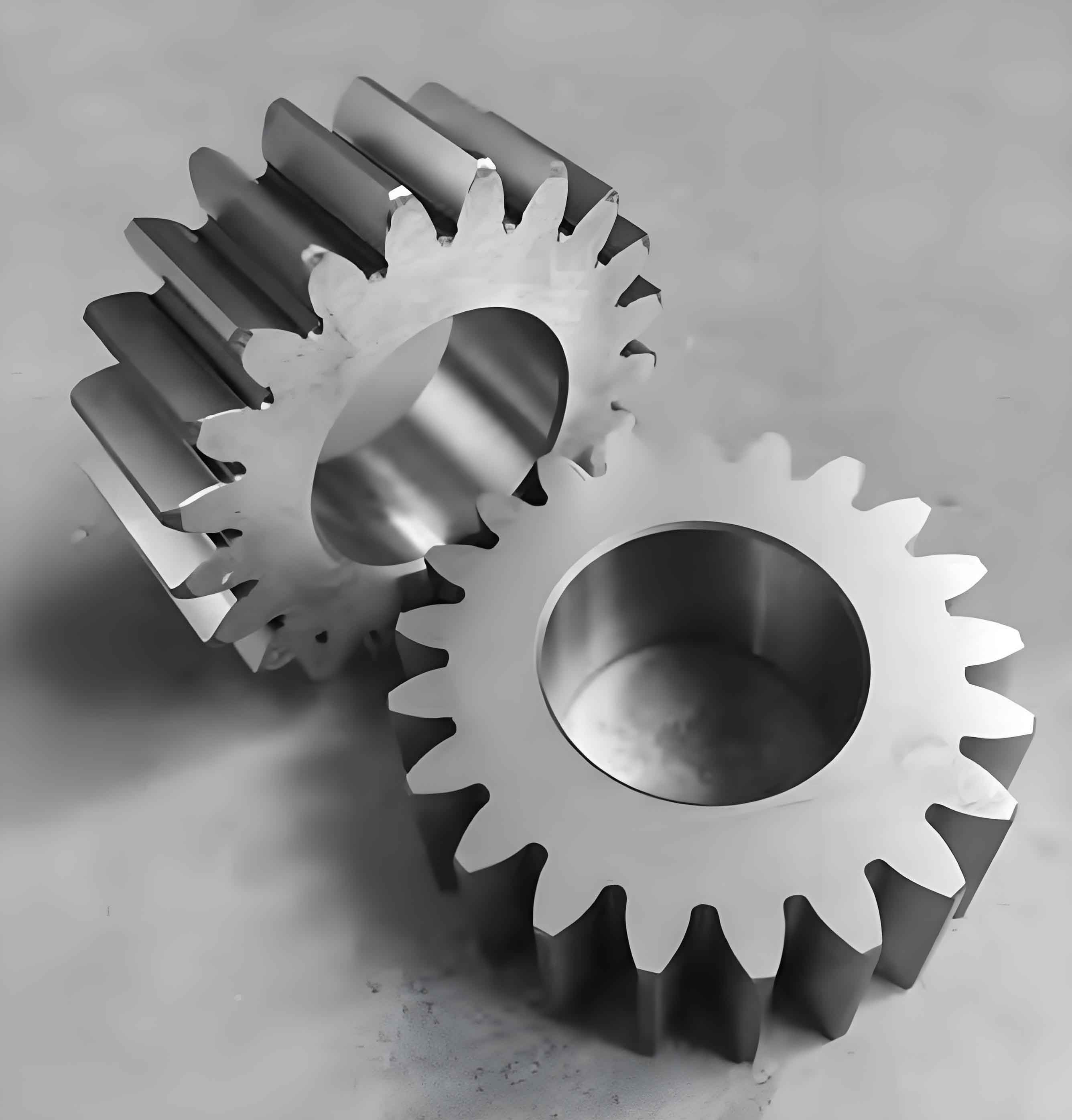