Abstract
This article focuses on optimizing the churning resistance of the hypoid gear in the rear axle of a vehicle. By establishing a three-dimensional numerical model of the rear axle based on the VOF two-phase flow model and the standard k – ε turbulence model, the churning power loss mechanism of the hypoid gear is analyzed. A method of removing the bolt structure and adding baffles on both sides of the gear is proposed. Through Fluent simulation and experimental verification, it is found that the simulation and experimental results are in good agreement, and the structural improvement can significantly reduce the churning resistance, with a maximum reduction of 35.9% at higher speeds.
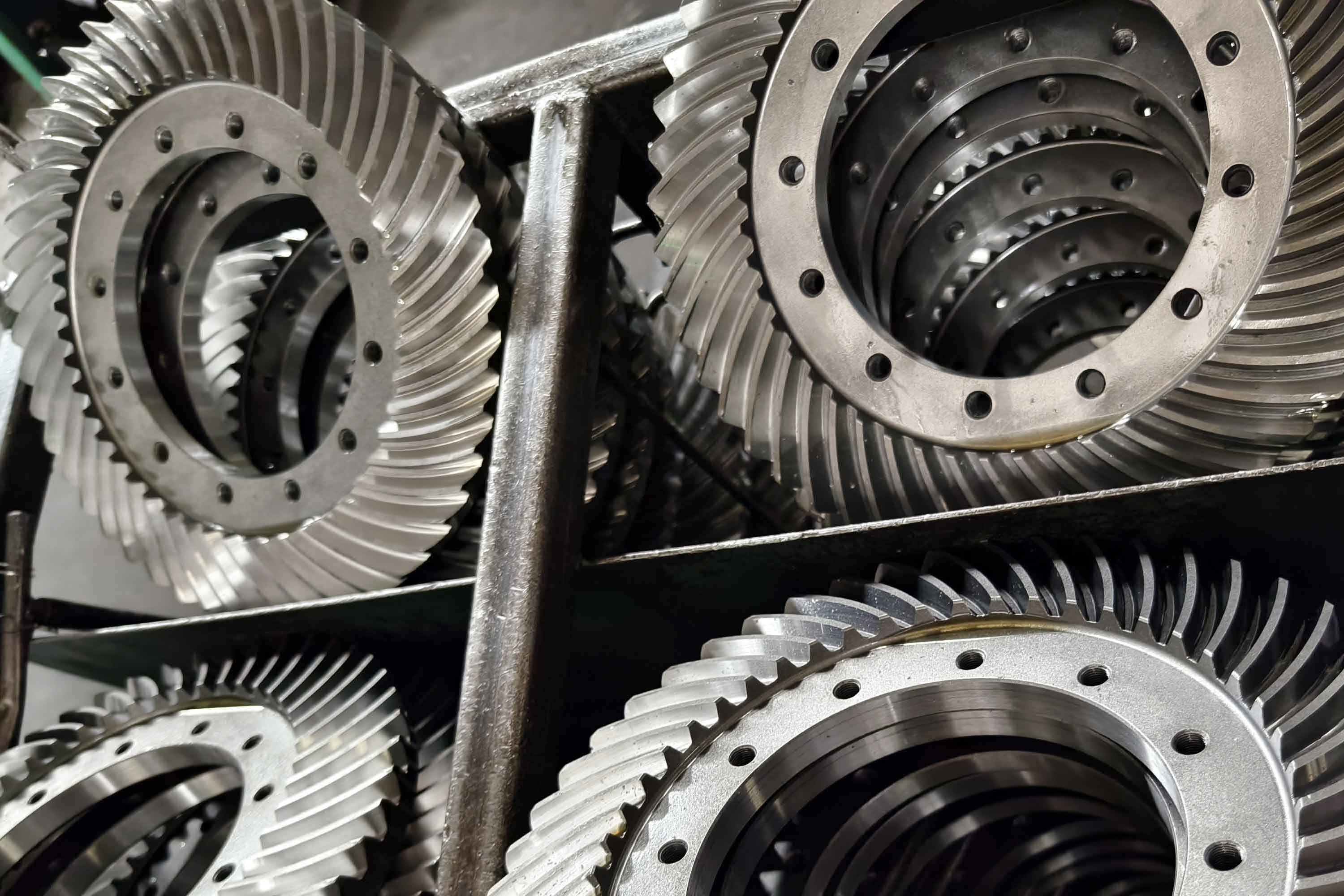
1. Introduction
The increase in global vehicle ownership has led to concerns about energy consumption and emissions. The rear axle of a rear-wheel-drive vehicle is a key component affecting transmission efficiency, and the churning resistance of the hypoid gear is a significant factor. Previous studies on gear churning losses have mainly focused on cylindrical gears, and this article aims to address the lack of research on the hypoid gears in the rear axle. The goal is to establish a model for the hypoid gear churning in the rear axle, improve the structure based on understanding the resistance mechanism, and provide a feasible method for reducing resistance through numerical and experimental verification.
2. Computational Fluid Dynamics Model Establishment
A simplified three-dimensional UG model of the rear axle is created, focusing on components related to lubricant flow. The model is imported into HYPERMESH for tetrahedral unstructured meshing. In Fluent, the gas-liquid two-phase flow model and the standard k – ε turbulence model are used for numerical calculations. The lubricant and air parameters, as well as the boundary conditions, are set according to the rear axle’s working state. The initial lubricant distribution is also defined.
Parameter | Value |
---|---|
Lubricant Temperature (C) | 50 |
Lubricant Density (kg/m³) | 839.8 |
Lubricant Dynamic Viscosity (kg/(m·s)) | 0.48 |
Air Temperature (C) | 50 |
Air Density (kg/m³) | 1.225 |
Air Dynamic Viscosity (kg/(m·s)) | 1.7894×10⁻⁵ |
Boundary Name | Boundary Type and Setting |
---|---|
Rear Axle Shell, Main Reducer Shell | Stationary Wall (Solid Wall, No Slip) |
Rear Axle Two Shaft Ends | Pressure Outlet (Vertical Pressure Outlet, Standard Atmospheric Pressure) |
Passive Gear, Differential Case, Bolt Assembly | Moving Wall (Rotational Motion Boundary) |
3. Churning Resistance Formation Mechanism Analysis and Structural Improvement
3.1 Hypoid Gear Churning Resistance Formation Mechanism Analysis
At 887 r/min, the churning resistance of the hypoid gear is analyzed. The gear teeth’s pressure and velocity fields show that the pressure difference between the front and back of the teeth creates resistance, and the increased fluid velocity dissipates power. The bolts also contribute to resistance due to high pressure and vortex formation.
3.2 Structural Improvement
The bolt structure is removed, and a laser welding alternative is proposed. Fixed baffles are added on both sides of the hypoid gear to reduce power loss. The baffle has a specific gap with the gear and a rectangular groove for lubricant circulation and heat dissipation.
3.3 Comparison Analysis
The churning resistance moments of the hypoid gear before and after improvement are calculated and compared. The flow field characteristics are also analyzed at 887 r/min. The results show reduced pressure and velocity after improvement.
Rotational Speed (r/min) | Calculated Value Before Improvement (N·m) | Calculated Value After Improvement (N·m) | Reduction Rate (%) | Simulation Value Before Improvement (N·m) | Simulation Value After Improvement (N·m) | Reduction Rate (%) | Experimental Value Before Improvement (N·m) | Experimental Value After Improvement (N·m) | Reduction Rate (%) |
---|---|---|---|---|---|---|---|---|---|
133 | 0.253 | 0.195 | 26.1 | 0.23 | 0.16 | 30.4 | – | – | – |
284 | 0.426 | 0.412 | 31.2 | 0.46 | 0.28 | 39.1 | – | – | – |
443 | 0.578 | 0.605 | 27.9 | 0.63 | 0.4 | 36.5 | – | – | – |
621 | 0.729 | 0.756 | 30.6 | 0.8 | 0.54 | 32.5 | – | – | – |
887 | 0.931 | 0.898 | 32.1 | 1.03 | 0.66 | 35.9 | – | – | – |
1065 | 1.055 | 1.064 | 32.5 | 1.18 | 0.78 | 33.9 | – | – | – |
Rotational Speed (r/min) | Maximum Dynamic Pressure Before Improvement (Pa) | Maximum Dynamic Pressure After Improvement (Pa) | Reduction Rate (%) | Maximum Velocity Before Improvement (m/s) | Maximum Velocity After Improvement (m/s) | Reduction Rate (%) |
---|---|---|---|---|---|---|
133 | 650 | 637 | 2 | 2.57 | 2.48 | 4 |
284 | 2293 | 1876 | 18 | 3.16 | 2.96 | 6 |
443 | 4512 | 3065 | 32 | 4.64 | 4.61 | 1 |
621 | 7055 | 4892 | 31 | 6.54 | 6.47 | 1 |
887 | 14805 | 6832 | 54 | 9.67 | 9.38 | 3 |
1065 | 23612 | 11236 | 52 | 11.2 | 10.7 | 4 |
4. Experimental Verification
Experiments are conducted on a “Drive Shaft – Rear Axle Test Bench” to measure the churning resistance moments of the hypoid gear before and after improvement at 50 C. The test bench setup and results are presented.
5. Results and Discussion
The churning loss of the hypoid gear increases with rotational speed due to enhanced fluid motion and increased centrifugal force. The CFD analysis and experimental results are consistent, validating the model. The improved structure significantly reduces the churning resistance moment, with the maximum reduction reaching 35.9% at higher speeds. The empirical formula has good agreement with the simulation results for the original structure but lower accuracy for the improved structure.
6. Conclusion
- The rear axle’s appurtenance, such as bolts, contribute significantly to the churning resistance of the hypoid gear, and this effect increases with rotational speed.
- Removing the bolt structure and adding baffles can reduce the maximum dynamic pressure and velocity of the hypoid gear, leading to a significant reduction in the churning resistance moment, with a maximum reduction of 35.9% at higher speeds.
- The empirical formula is effective in estimating the churning resistance moment of the original hypoid gear structure but has lower accuracy for the improved structure.