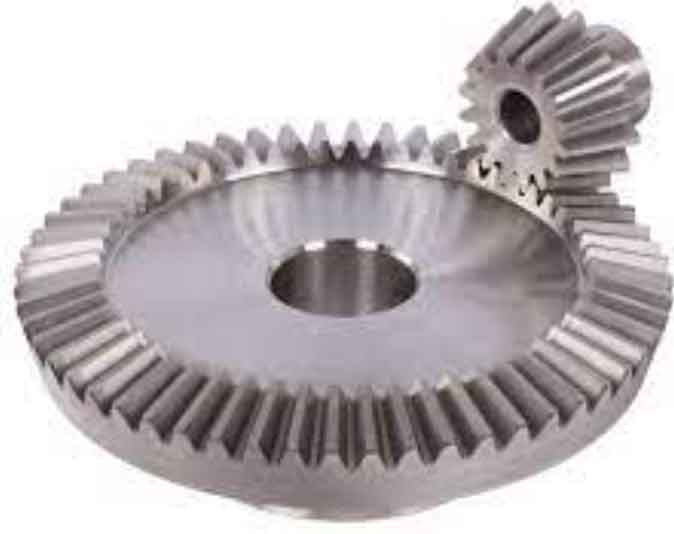
The Bevel gears are used for transmissions between intersecting axes. Generally, the single-stage transmission ratio can be up to 6, the maximum could reach 8 or above. Corresponding transmission efficiency could be up to 0.94~0.98.
As designing, manufacturing and installing works of straight bevel gears and helical ones are more simple, added loud noises made by the 2 kinds bevel gears, they’re commonly adopted in low speed transmission units (<5m/s). The transmission power of bevel gears can reach 370Kw, and the peripheral speed can be around 5m/s. Helical bevel gears have stable transmissions but have high gear loading capacities. Therefore, bevel gears are commonly applied in the conditions of high speed and heavy load in accordance with their special characteristics. In addition, bevel gears occupy an important position in auto industry.
Bevel gears are a type of gears with conical-shaped teeth, and they are commonly used to transmit power and motion between intersecting shafts. Here are some more particular knowledge and key aspects of bevel gears:
1. Types of Bevel Gears:
- Straight Bevel Gears: Straight bevel gears have straight teeth and are used in applications where the shafts intersect at 90 degrees. They are the most common type of bevel gears.
- Spiral Bevel Gears: Spiral bevel gears have helical teeth that form a spiral pattern around the gear cone. They offer smoother and quieter operation compared to straight bevel gears and are suitable for high-speed and high-load applications.
- Zerol Bevel Gears: Zerol bevel gears have curved teeth similar to spiral bevel gears but with a slightly different tooth profile. They are known for low noise operation and are used in applications where quietness is crucial.
- Hypoid Gears: Hypoid gears are a special type of bevel gears with an offset center distance between the shafts. They allow non-intersecting, but non-parallel shafts to transmit power.
2. Tooth Contact Patterns:
- The tooth contact pattern is essential for ensuring proper load distribution and avoiding uneven wear. It is crucial to achieve a well-centered tooth contact pattern for efficient and reliable gear operation.
- Proper tooth contact is achieved through precise gear manufacturing and careful alignment during assembly.
3. Applications:
- Bevel gears find applications in various industries, including automotive, aerospace, industrial machinery, marine, and robotics.
- In automotive, they are used in differentials, steering systems, and transmissions.
- In aerospace, they are used in aircraft engines and helicopter rotor assemblies.
- In industrial machinery, they are used in gearboxes, power tools, and printing presses.
- In marine applications, they are used in propulsion systems.
4. Efficiency and Load Capacity:
- Bevel gears generally have lower efficiency compared to parallel-axis gears like spur and helical gears due to additional sliding motion at the tooth contact.
- Spiral bevel gears offer higher efficiency compared to straight bevel gears due to their helical teeth, which minimize sliding friction.
5. Lubrication:
- Proper lubrication is essential for bevel gears to reduce friction, wear, and heat generation during operation.
- Splash lubrication or forced lubrication systems are commonly used to ensure adequate lubrication for bevel gears.
6. Mounting and Assembly:
- Proper alignment and precision in mounting and assembly are crucial for the smooth operation and longevity of bevel gears.
Bevel gears are versatile and robust components used in various mechanical systems, and their design and selection depend on specific application requirements, loads, speeds, and environmental conditions. Precise manufacturing, proper lubrication, and maintenance are key factors for ensuring reliable performance and longevity of bevel gears in different applications.