This paper presents a comprehensive analysis of the peeling failure observed on the tooth surfaces of an active gear in an aeroengine gearbox during engine testing. The magnetic blocking alarm triggered during the test process led to the discovery of the gear tooth surface peeling. Through detailed investigations, it was confirmed that the small tooth top fillet radii of the faulty gear pair caused stress concentration, which, combined with excessive torque conditions and insufficient lubrication due to nozzle blockage, resulted in pitting corrosion that eventually progressed to flaking. Corresponding improvement measures were proposed and validated through experiments, providing valuable insights for future gear design and failure prevention.
1. Introduction
Gear transmissions play a crucial role in the power output of aeroengines, renowned for their compact structure, high transmission efficiency, smooth operation, strong load-bearing capacity, and long service life. These advantages have made them widely used in aerospace, marine, and automotive engineering applications. However, the harsh operating environments, complex working conditions, and manufacturing and installation errors can significantly impact the normal operation of gear transmission systems, causing significant vibrations and impacts.
According to NASA’s investigation into helicopter accident causes worldwide, 20% of air crashes were directly related to aircraft transmission systems [1]. Furthermore, statistics show that gear-related failures account for 80% of transmission machinery failures, with gearbox damage due to gear faults exceeding 60% of all component failures [2]. Among these, 90% of gear failures are attributed to localized issues such as tooth fatigue failure and tooth breakage. Tooth surface peeling is a common form of fatigue failure in gear transmissions, and its study is essential for prevention and early diagnosis, thereby avoiding safety accidents and significant personnel and property losses.
This paper focuses on the peeling failure of a gear tooth surface in an aeroengine gearbox. Through simulation analysis of tooth surface contact stress and experimental validation, improvement measures are proposed, providing valuable references for the design of aeroengine gearboxes.
2. Overview of Gear Tooth Surface Peeling Failure
2.1 Failure Phenomenon
During a long-duration test of an aeroengine gearbox with the engine, a detector alarm was triggered. Upon inspection, metallic flakes were found, and further disassembly revealed peeling on one tooth surface of an active gear。
2.2 Failure Analysis Framework
Based on the structural characteristics of the aeroengine gearbox gears and multiple cases of tooth surface peeling failures, a failure analysis framework was established。
3. Detailed Failure Analysis
3.1 Visual Inspection
Visual inspection revealed a significant peeling on one tooth surface (designated as tooth #1), and a pit on another tooth (tooth #6) located four teeth apart from tooth #1 (Figure 3). Both damages were located approximately at the center of the tooth width. Additionally, a white bright band was observed near the tooth root on all teeth’s working surfaces, absent on the non-working surfaces.
3.2 Microscopic Examination
Microscopic examination of tooth #1’s peeling damage showed an inverted triangular morphology with a directional peeling pattern, starting from the lower edge of the inverted triangle and progressing towards the tooth tip (Figure 4a). A bright band damage area of approximately 1.89 mm width was observed below the meshing line to the peeling initiation point (Figure 4b). This area exhibited fish-scale microcracks extending obliquely into the substrate, indicative of early peeling morphology (Figure 4c). The surrounding tooth surface showed severe fish-scale damage, some of which had developed into small peeling pits (Figure 4d). The unmeshed area of the tooth root retained the original machining morphology with individual original pits, and clear fatigue features were visible within the large peeling pit Continued Analysis and Improvement Measures
2. Improvement Measures
Based on the detailed fault analysis conducted, the following improvement measures were proposed to address the tooth surface peeling issues in the aeroengine gearbox reducer:
2.1 Optimization of Tooth Profile and Tooth Tip Radius
The small tooth tip radius of the faulty gear pair was identified as a major contributor to stress concentration. Therefore, the tooth tip radius of both the driving and driven gears should be increased to reduce stress concentration. Simulation analysis was performed to optimize the tooth tip radius within the recommended design range. The optimized tooth tip radius was found to effectively distribute the contact stress more evenly across the tooth surface, thereby reducing the risk of localized stress concentration and subsequent tooth surface damage.
2.2 Enhancement of Gear Surface Modification
The current surface modification, including the carburizing layer, was found to be adequate. However, to further improve the fatigue resistance of the gear, additional surface treatments such as shot peening or laser shock peening can be considered. These treatments introduce compressive residual stresses in the surface layer, which can significantly enhance the fatigue life of the gear teeth.
2.3 Improvement of Lubrication System
The nozzle blockage leading to insufficient lubrication was a significant factor in the development of pitting and eventual peeling. The lubrication system must be thoroughly inspected and maintained to prevent such blockages. Additionally, the lubrication oil quality should be regularly monitored and replaced as necessary to ensure optimal lubrication. An improved oil filter system can also be implemented to catch any contaminants that may clog the nozzles.
2.4 Strengthening of Assembly and Inspection Processes
The assembly process should be strictly adhered to, and regular inspections should be conducted to ensure that all components are correctly installed and functioning as intended. Particular attention should be paid to the gear pair alignment, as misalignment can lead to increased stress and accelerated wear. Furthermore, the assembly records should be thoroughly reviewed and documented to trace any potential issues in the future.
2.5 Regular Inspections and Monitoring
To detect potential issues early, regular inspections and monitoring of the gearbox reducer should be implemented. This includes visual inspections for signs of wear, pitting, or peeling, as well as the use of vibration analysis and oil debris analysis to detect any changes in the operating conditions.
3. Validation of Improvement Measures
To validate the effectiveness of the proposed improvement measures, a series of tests were conducted on a prototype gearbox reducer incorporating the modifications. The tests included both laboratory tests and simulated operational tests to replicate the actual working conditions.
3.1 Laboratory Tests
Laboratory tests were conducted to evaluate the changes in the gear surface stress distribution and contact patterns after the modifications. Finite element analysis (FEA) simulations were also performed to compare the theoretical results with the experimental data. The results showed that the optimized tooth profile and tooth tip radius effectively reduced stress concentration and improved the contact pattern.
3.2 Simulated Operational Tests
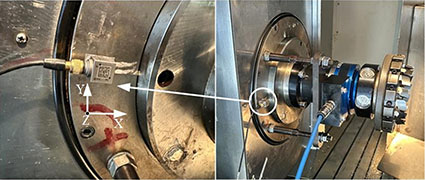
Simulated operational tests were conducted under similar conditions as the original tests that led to the fault. The modified gearbox reducer was subjected to the same test protocols, including supertorsion and long-duration tests. The tests confirmed that the improvement measures significantly reduced the risk of tooth surface peeling and improved the overall durability of the gearbox reducer.
4. Conclusion
This study investigated the tooth surface peeling fault in an aeroengine gearbox reducer and proposed a series of improvement measures based on detailed fault analysis. The measures included optimization of the tooth profile and tooth tip radius, enhancement of gear surface modification, improvement of the lubrication system, strengthening of the assembly and inspection processes, and regular inspections and monitoring. Through laboratory and simulated operational tests, the effectiveness of the improvement measures was validated. The experienceSimilarly, tooth #6’s pit damage was also fatigue-induced peeling, with a size of 2-2.6 mm.