Abstract: This paper focuses on the performance analysis of the spiral bevel gear transmission system. It discusses the background, significance, and research status of the topic, and outlines the research ideas and main contents. The spiral bevel gear transmission is crucial in various fields due to its advantages, but the deformation during operation can affect the meshing state and performance of the gear pair. The lack of an efficient method for calculating the meshing dislocation of the spiral bevel gear transmission system is a problem. This paper aims to solve this problem by using the finite element method to analyze the performance of the transmission system, and proposes a static model analysis method based on solid finite elements to accurately and quickly calculate the meshing dislocation. The dynamic model of the transmission system considering the meshing stiffness is also constructed to study the vibration characteristics of the system. Finally, the test experiment verifies the correctness of the theoretical analysis method.
Keywords: Spiral bevel gear; Transmission system; Finite element; Meshing dislocation; Static analysis; Dynamic analysis
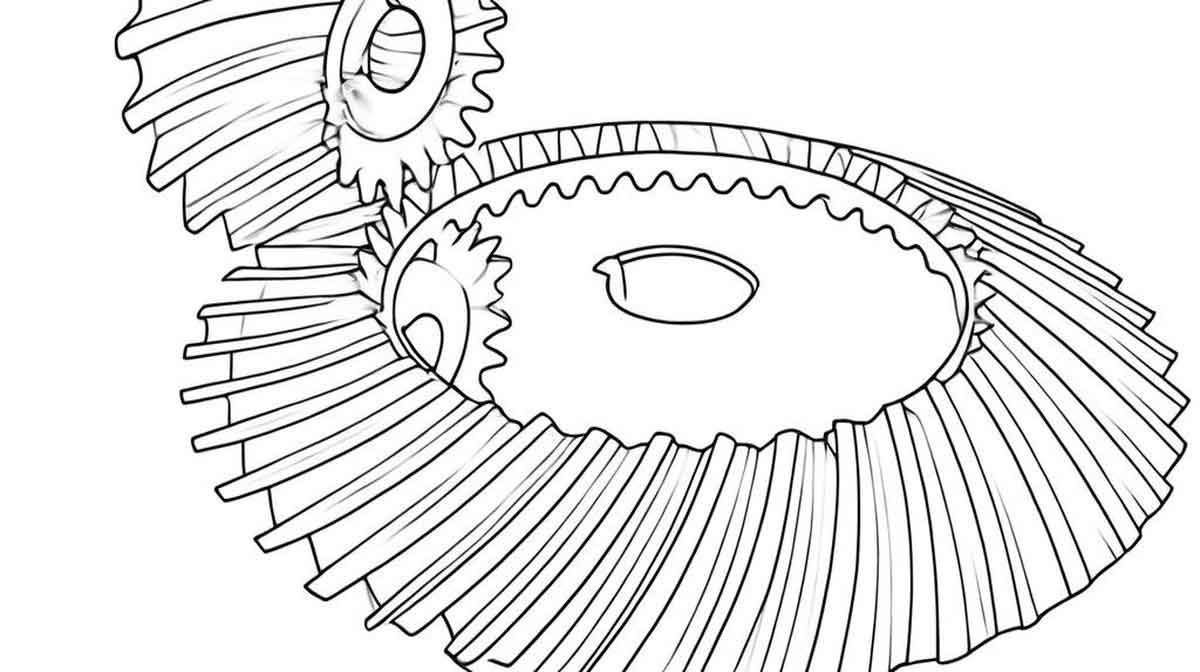
- Introduction
1.1 Background and Significance
Spiral bevel gears have been widely used in many fields such as aerospace, automotive, and shipbuilding due to their excellent performance, including high transmission efficiency, strong load-carrying capacity, and compact structure. However, the complex geometric structure and meshing characteristics of spiral bevel gears make them one of the most challenging designs in the gear transmission system. The failure of the gear transmission system can cause serious impacts on production, economic benefits, and even personal safety. Therefore, it is of great urgency and importance to deepen the research on the performance analysis of the spiral bevel gear transmission system, aiming to reduce equipment downtime, safety accidents, and economic losses caused by gear transmission system failures through in-depth theoretical analysis, fault prediction, and performance optimization.
During the actual operation of the transmission system, the meshing process between the gear pairs generates a meshing force, which is transmitted to the bearings through the transmission shaft, causing a certain degree of elastic deformation in the entire transmission system. When these forces continue to act on the transmission system, the originally accurate installation position of the gears will be shifted due to the force, that is, the original ideal meshing state changes under the load, which is defined as the meshing dislocation of the gear pair. According to the principle of meshing dislocation, the meshing dislocation can be calculated by the deformation of the tooth surface meshing point or the deformation of the transmission shaft. However, it is difficult to directly capture the precise meshing position by observing due to the complexity and uncertainty of the positioning of the tooth surface meshing point, so it is more suitable to calculate by the deformation of the transmission shaft. The finite element method is used to establish the static model of the spiral bevel gear transmission system, including the beam element model and the solid element model. The transmission system model constructed by the beam element has a fast calculation speed, but the deformation of the transmission shaft under load will cause a large error, which will affect the contact characteristics of the gears and thus the analysis of the transmission error and the loading mark. The transmission system model constructed by the solid element can improve the calculation accuracy, but the number of meshes is large, the division is difficult, and the calculation resources are very consumed, and the result of the gear’s loading contact characteristics will be more accurate. Currently, there is a lack of an efficient method with high calculation accuracy and efficiency for calculating the meshing dislocation of the spiral bevel gear transmission system model.
1.2 Research Status at Home and Abroad
1.2.1 Research Status of Meshing Dislocation of Spiral Bevel Gear Transmission System
In the process of power transmission, the internal deformation of the spiral bevel gear transmission system due to the load leads to the offset of the initial meshing position of the gear pair, which affects the stability, noise level, wear rate, and overall transmission efficiency of the gear pair. Therefore, quickly and accurately analyzing the meshing dislocation of the transmission system is very important for evaluating the loading meshing performance of the gear pair and optimizing the tooth surface design. Scholars at home and abroad have carried out relevant research on the analysis method of the meshing dislocation of the transmission system.
Litvin et al proposed a new analysis method for the tooth surface contact characteristics of spiral bevel gears considering the installation dislocation, aiming to study its influence on the transmission error and loading mark of spiral bevel gears. Qin Qiuxia et al obtained the meshing dislocation of the system by considering the influence of errors in the assembly process, manufacturing process, and loading process, and studied the meshing performance of the gear pair by adjusting the tooth surface. They verified the accuracy of the theoretical design method by using the gear fatigue test. Gu Jiangong et al proposed a contact analysis method for the split – flow transmission system of spiral bevel gears by considering the influence of edge contact and installation dislocation of the gear pair. Teik et al studied the influence of assembly errors on the meshing characteristics of hypoid gears by using the quasi – static analysis method. Tang Jinyuan et al derived the theoretical tooth surface equations of the large and small wheels of spiral bevel gears based on the gear meshing principle, and studied the influence of the installation errors of the gear pair on the tooth surface contact state. Cai Xiangwei et al studied the tooth surface redesign method by considering the influence of installation dislocation and established the trajectory function to calculate the installation dislocation by forming multiple dislocation installation methods between the tooth surfaces, and redesigned the tooth surface of the gear. Li et al constructed the finite element model of the bevel gear pair by considering the various errors in the assembly and processing processes, and studied the comprehensive influence on the meshing force, transmission error, and loading mark of the gear pair.
Lai Changfa et al obtained the meshing dislocation of the gear pair by using the Masta software to solve the deformation of the gear pair in the real working condition, and obtained the meshing characteristics of the gear pair by loading contact analysis, and verified the simulation results by the transmission test bench. Yang et al proposed an analysis method for the meshing performance of hypoid gear pairs, and used the Masta software to construct the transmission system model and extract the deformation of the transmission system to calculate the dislocation of the system, and studied the influence of the gear meshing performance under the independent dislocation and comprehensive dislocation. Yan Min et al used the Romax software to construct the transmission model, extracted the meshing dislocation of the main reduction gear, and studied the influence of different housing models on the meshing dislocation. Simon et al used the advanced tooth surface contact analysis method to study the influence of the position accuracy of the processing machine and the misalignment of the mating parts on the transmission error of the non – matching spiral bevel gears. Li Xuwei et al proposed an innovative finite element modeling method, considering the stiffness coupling characteristics and nonlinearity of the bearing, constructed the finite element model of the complete drive axle transmission system, solved the meshing dislocation of the system, and compared and analyzed by the support rigidity test of the drive axle. Gao Jie et al considered the support deformation of the housing, transmission shaft, and bearing under the load, superimposed the deformation to calculate the equivalent dislocation of the gear pair, constructed the tooth contact model considering the dislocation to obtain the contact mark. Qi Haoyu calculated the stiffness matrix of the shaft, bearing, and gear based on the Euler beam theory and deformation equation, superimposed them to obtain the coupling matrix of the system, and calculated the meshing dislocation by the force balance equation, and studied the contact analysis method of the gear pair. Zhou Yanzhu et al considered the influence of the deformation of the shaft and bearing on the meshing dislocation, constructed the gear transmission system model, and studied the influence of the meshing dislocation on the reliability of the system. He Changran et al studied the influence of the elastic deformation of the gear on the housing under the load, considered the stiffness matrix and mass matrix of the housing, and calculated the meshing dislocation it generated.
In summary, most of the existing methods for analyzing the meshing dislocation of the spiral bevel gear transmission system simplify the transmission shaft as the beam element model. However, this simplification ignores the assumption conditions derived from the Euler beam and Timoshenko beam theories. When the transmission shaft structure is complex, the deformation analysis result may have a large error, which will lead to the inaccurate calculation of the meshing dislocation of the gear transmission system. Or the solid full finite element model is constructed, which can obtain better calculation results, but it is extremely wasteful of resources. Or the meshing dislocation is obtained through experiments, which is more difficult to achieve. Therefore, there is an urgent need for a fast and accurate analysis method for the meshing dislocation of the spiral bevel gear transmission system to solve the existing problems.
1.2.2 Research Status of Dynamics Analysis of Spiral Bevel Gear Transmission System
The dynamics analysis can more accurately evaluate and improve the efficiency, load – carrying capacity, and service life of the gear transmission, and help design a transmission system with better performance and higher reliability. Scholars at home and abroad have carried out relevant research on the dynamics analysis method of the transmission system.
Li et al constructed a coupling model between the axial, lateral, and torsional vibration modes of the spiral bevel gear rotor – bearing system to study the vibration mechanism of the spiral bevel gear rotor system. Hua et al considered the influence of the bearing elasticity, used the finite element analysis method to construct the dynamic model of the bevel gear rotor – bearing, and studied its influence on the vibration characteristics of the entire transmission system. Yang et al considered the influence of the elastic housing structure, regarded the gear pair, bearing, and housing as dynamic substructures, and the pinion and gear models as nonlinear and time – varying meshing coupled rigid bodies, and proposed a method to predict the dynamic response of the hypoid gearbox under complex working conditions. Li et al considered the oil film force bearing support, used the numerical analysis theory method to study the nonlinear dynamics behavior of the bevel gear transmission system. Yavuz et al proposed a dynamics model including the finite element model of the transmission shaft and the meshing model of the gear pair, considering the meshing stiffness and tooth clearance nonlinearity, and studied the diverse nonlinear time – varying dynamics characteristics of the spiral bevel gear transmission system. Li et al constructed an 8 – degree – of – freedom nonlinear dynamics model of the spiral bevel gear pair, including the influences of transmission error, time – varying meshing stiffness, and asymmetric meshing stiffness, and used the numerical analysis method to study the vibration characteristics of the spiral bevel gear transmission system under the condition of asymmetric meshing stiffness. Hua et al based on the influence of the installation mode of the pinion, used the finite element analysis method to construct the dynamic model of the gear – bearing structure, and studied the influence of different design configurations on the dynamics characteristics of the spiral bevel gear. Shi et al considered the universal joint connection between the propeller shaft and the pinion shaft, proposed an improved dynamics model of the hypoid gear rotor system, and studied the dynamic response law of the hypoid gear under the conditions of shaft misalignment and unbalanced mass of the pinion. Zhu et al considered the laminated film coupling, tail rotor excitation, and the length of the oblique tail shaft in the middle and tail gearboxes of the helicopter, combined the finite element and lumped mass methods to establish the dynamics model, and studied the influence of these factors on the dynamic characteristics of the spiral bevel gear system. Cheng et al constructed a generalized three – dimensional dynamics model, considering the influence of the load transmission error as an important excitation source, and studied the coupled translational – rotational vibration response of the hypoid gear rotor system.
Liu Guanglei et al proposed a method to add a virtual support in the spiral bevel gear rotor system to ensure the meshing stability of the spiral bevel gear, and used the transfer matrix method to construct the vibration model of the spiral bevel gear – rotor system to analyze the dynamics characteristics of the system. Wang Lihua et al based on the lumped parameter method, considering the elastic deformation of the transmission shaft and bearing, constructed a multi – degree – of – freedom bending, torsion, axial, and wobble coupled vibration dynamics model of the spiral bevel gear. Wang Sanmin et al based on the elastic support, constructed the rotor – bearing dynamics model of the spiral bevel gear, and studied the nonlinear vibration characteristics of the system. Yu Lei et al constructed the longitudinal bending torsion coupled dynamics model of the bevel gear transmission rotor – bearing system, considering the influence of the external load on the stiffness and damping coefficients of the system, and the modal of the transmission system. Lin He et al considered the spiral bevel gear and planetary gear train in the helicopter, constructed the pure torsional vibration characteristics dynamics model, used the lumped parameter method to establish the dynamics equation including the tooth side clearance, and studied the dynamic load characteristics of the system under the conditions of time – varying meshing stiffness, tooth side clearance, and external load. Xie Zhiyu et al took the bilateral double – stage spiral bevel gear in the nutation reducer as the reference object, used the Adams to construct the dynamics analysis model of the reducer, and studied the dynamics characteristics of the reducer. Xiong Tao et al used the Adams software to construct the dynamics simulation model including the ball bearing and spiral bevel gear transmission, and used the variable speed as the excitation of the system to study the dynamic response of the system under this condition. Yao Tingqiang et al based on the contact dynamics conditions of the arc tooth bevel gear, proposed a new dynamics analysis method including the ball bearing and spiral bevel gear transmission, and studied the dynamic response characteristics of the system under the influence of the preload and load torque. Feng Zhiheng et al used the lumped parameter method to construct the nonlinear dynamics model of the spiral bevel gear system including the original motor, load, and gear pair, and solved the dynamic response of the system under the factors such as time – varying meshing stiffness, friction, and gyroscopic effect. Cheng Yong et al considered the influences of time – varying meshing stiffness, transmission error, and tooth side clearance, constructed the coupled dynamics model of the arc tooth bevel gear transmission system including 16 degrees of freedom of bending – torsion – axis, and solved the system response. Liao Ping et al used the finite element node method to construct the coupled dynamics model of the arc tooth bevel gear transmission system including the flexible shaft segment of bending – torsion – axis – swing, and studied the vibration characteristics of the transmission system under the load torque and contact trajectory. Zeng Hong et al used the Adams to construct the dynamics model of the arc tooth bevel gear transmission system, and solved the dynamics characteristic curves of the rotation speed, gear meshing force, and other parameters. Feng Gang et al constructed the 8 – degree – of – freedom dynamics model of the arc tooth bevel gear and rotor transmission system, and used the specific function in the Matlab software to solve the system vibration response with or without cracks. Yang Yanni et al constructed the dynamics contact analysis model of the hypoid gearbox transmission system, and solved the dynamic response of the system under the influences of meshing deformation, bending deformation of the transmission shaft, and bearing support stiffness.
In summary, the commonly used methods for the dynamics model of the spiral bevel gear transmission system are the transfer matrix method, the lumped mass method, and the finite element method, each of which has its advantages and limitations. However, scholars have less involvement in the way of combining the lumped parameter method and the finite element method to establish the dynamics model. The existing dynamics analysis methods can provide theoretical support and method reference for the hybrid modeling method.
1.2.3 Research Status of Gear Transmission System Test Bench
The gear transmission system test bench is a precise experimental facility, which mainly functions to conduct comprehensive, multi – level, accurate, and detailed performance tests and in – depth dynamic characteristic analysis on various gear transmission devices. Scholars at home and abroad attach great importance to the research of the gear transmission system test bench, and they have made a lot of fruitful work in improving the test accuracy and adaptability of the test bench, as well as in the test methods, data analysis, model establishment, and fault diagnosis technology.
Hargreaves et al explored the specific influence of different types and properties of lubricants on the transmission efficiency of the gear transmission system by building a mechanical test bench. Bader built a unique rocking box gear test bench to study the dynamics characteristics and performance parameters of the gear transmission system, in which two identical gearboxes are cleverly connected by a universal joint coupling, and one of the gearboxes is designed to rotate freely around a fixed axis to achieve torque loading. Mao et al used a mechanical closed test bench equipped with a precise lever loader to study the gear tooth surface wear performance of polymer materials under actual working conditions. Li et al used a mechanical closed test bench equipped with a rubber elastic coupling and a loader close to the test gearbox to effectively isolate the vibration influence of the external environment on the test box and ensure the vibration characteristics of the gear system under the change of tooth thickness. Schröder et al innovatively developed a new harmonic loading test bench, which cleverly uses the principle of harmonic gear transmission to achieve efficient loading by breaking through the traditional loading method. Through its unique flexible wheel and rigid wheel structure, it achieves a high transmission ratio and precise motion control.
Zhu Cailong designed a fatigue life test bench for the main reducer gear of the drive axle to study and verify the performance stability and life prediction of the drive axle main reducer gear under long – term and repeated loads. Xu Lei built a power – open test bench that can conduct detailed tests and analyses on multiple performance of the transmission system, including the internal mechanism and vibration signal manifestation of vibration and noise generation. Liu Kai et al designed an innovative test bench with a differential parallel coupling input and single output transmission structure to simulate and verify the performance of the vehicle power transmission system under various working conditions considering the diversity and complexity of the actual working environment of the vehicle. Cao Ke et al integrated a high – precision grating angle sensor by using the theory of dynamic gear transmission error and modern virtual instrument technology to build a comprehensive measurement test bench for the transmission error of the entire gearbox, which can accurately measure the single tooth meshing and the transmission error of the entire gearbox.
In summary, scholars have accumulated rich achievements and valuable experience in the theoretical research and technical development of the gear transmission test bench. By exploring the dynamics behavior of the gear transmission system under different working conditions, they have conducted comprehensive and detailed studies on the structure design, function realization, and performance test methods of the test bench. These profound research foundations provide detailed theoretical basis and technical support for the subsequent gear transmission test.
1.3 Research Ideas and Main Contents
This paper mainly takes the spiral bevel gear transmission system as the research object, constructs the solid finite element transmission shaft coupling analysis model to obtain the system deformation, and compares it with the other two finite element models to derive and calculate the meshing dislocation. According to the tooth surface equation of the spiral bevel gear, the theoretical model of the spiral bevel gear is constructed, and based on the meshing dislocation result, the multi-tooth meshing model is adjusted to study its transmission error and loading mark. By using the finite element method, the multi-tooth meshing stiffness is calculated, and based on a numerical control rolling inspection machine, the dynamic model of the spiral bevel gear transmission system considering the meshing stiffness is constructed to analyze the inherent characteristics of the transmission system and the vibration characteristics of the transmission system under the excitation of the multi-tooth meshing force. A test experiment is conducted on a numerical control rolling inspection machine, and the vibration characteristics curve is obtained by using an acceleration sensor, which is compared with the theoretical static and dynamic characteristic analysis results.
The main contents of this paper are as follows:
The first chapter mainly summarizes the source of the paper, the research background and significance, and expounds the research status of the meshing dislocation, dynamics analysis, and gear transmission test bench of the spiral bevel gear transmission system.
The second chapter mainly introduces the construction of the equivalent mechanical model of the key components in the spiral bevel gear transmission system, laying a solid foundation for the subsequent establishment of the static and dynamic analysis models of the spiral bevel gear transmission system.
The third chapter mainly introduces the construction of the solid finite element transmission shaft coupling analysis model to obtain the system deformation and calculate the meshing dislocation, constructs the theoretical spiral bevel gear model based on the tooth surface equation, and adjusts the posture of the model based on the meshing dislocation to complete the loading contact analysis. At the same time, the spiral bevel gear transmission system model based on the beam element and the full finite element model of the spiral bevel gear transmission system are constructed for comparative analysis.
The fourth chapter mainly calculates the multi-tooth meshing stiffness based on the multi-tooth meshing model considering the meshing dislocation. Based on a numerical control rolling inspection machine, the dynamic model of the spiral bevel gear transmission system considering the meshing stiffness is constructed, and the natural characteristics of the transmission system are solved by modal analysis, and the dynamic response of the transmission system is solved by the modal superposition method.
The fifth chapter mainly conducts the test experiment on a numerical control rolling inspection machine, and measures the vibration signal by using the acceleration sensor. The experimental results are compared with the theoretical results of the third and fourth chapters to verify the correctness of the static and dynamic analysis models.
The sixth chapter mainly summarizes the work of this paper on the performance analysis of the spiral bevel gear transmission system, and puts forward the prospects for the next step according to the shortcomings of the research.
In conclusion, this paper solves the problem of fast and accurate performance analysis of the spiral bevel gear transmission system, and verifies the feasibility and accuracy of the static and dynamic characteristic analysis method of the spiral bevel gear transmission system model by completing the test experiment on a numerical control rolling inspection machine. It provides some guidance for the adjustment design and theoretical analysis of the spiral bevel gear transmission system.